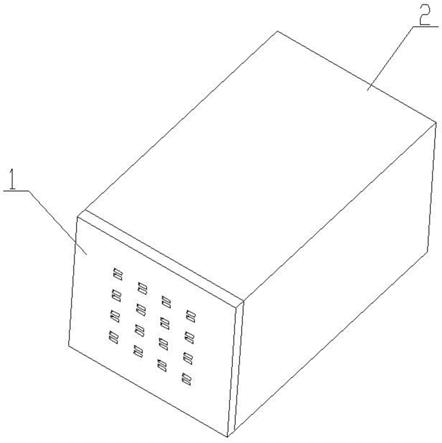
[0001]
本发明涉及材料焊接技术领域,具体涉及一种毫米波波导天线精密扩散焊接方法。
背景技术:[0002]
毫米波雷达具有高分辨、体积小等特点,是新一代雷达的发展方向。其中毫米波波导是毫米波雷达的关键结构,其波导腔是毫米波的传输通道。由于毫米波波长短,对波导腔的尺寸精度和粗糙度要求极高,否则会导致毫米波衰减严重,影响系统指标。目前毫米波波导腔尺寸精度要求
±
0.05mm,粗糙度不超过0.8um。
[0003]
常规波导主要焊接方式是真空钎焊,通过钎料熔化和凝固实现焊接,为了保证焊接面焊接饱满无缝隙,熔化的钎料会在焊接面边缘形成圆角,同时在焊缝附近的波导腔面上形成铺展。这两个特点对常规波导影响不大,但是对于毫米波波导,会造成损耗大等问题。同时钎焊焊缝强度低、振动可靠性差,因此在机载弹载环境使用时可靠性不足。因此需要提出新型焊接方法,保证毫米波波导尺寸精度的同时,保证焊接强度和可靠性。
[0004]
扩散焊方法是波导结构的焊接方法之一,通过被焊零件间的原子扩散实现焊接,因扩散焊不需要钎料,不存在圆角的钎料铺展问题,焊接完成的波导腔表面质量高、形状完整性好。但是现有的扩散焊方法均采用单一的焊接压应力实现较大的压缩变形,促进微观凸凹不平的两个零件焊接面不断变形,进而增加接触面积,保证整个焊接界面进行充分的原子扩散,保证焊接质量。采用现有的扩散焊方法焊接毫米波波导,一般高度方向变形3%~5%,因此不可避免的导致波导腔发生较大变形,约0.3mm~0.5mm,无法满足毫米波波导的高精度要求。
[0005]
鉴于上述缺陷,本发明创作者经过长时间的研究和实践终于获得了本发明。
技术实现要素:[0006]
为解决上述技术缺陷,本发明采用的技术方案在于,提供一种毫米波波导天线精密扩散焊接方法,毫米波波导天线采用铝合金材料,所述毫米波波导天线包括待焊接一体的两零件;
[0007]
所述毫米波波导天线精密扩散焊接方法,包括步骤:
[0008]
s1,清理所述零件表面,去除焊接面氧化膜;
[0009]
s2,完成所述零件装配并装入真空炉;
[0010]
s3,设置工艺参数,并进行焊接加工,所述焊接加工依次包括:升温阶段、均温阶段、高压应力破膜阶段、中压应力变形焊接阶段、低压应力焊接阶段、降温阶段。
[0011]
较佳的,所述步骤s3中,所述升温阶段中真空炉的真空度低于8
×
10-3
pa,升温速率为2℃/min~5℃/min,并在所述升温阶段将温度加热至铝合金焊接温度,所述升温阶段所述零件之间的压应力设为0.5mpa。
[0012]
较佳的,所述步骤s3中,所述均温阶段中所述真空度低于3
×
10-4
pa,并在所述高压
应力破膜阶段、所述中压应力变形焊接阶段、所述低压应力焊接阶段、所述降温阶段保持所述均温阶段中的真空度,所述均温阶段的所述压应力与所述升温阶段的压应力保持不变。
[0013]
较佳的,所述步骤s3中,所述高压应力破膜阶段的压应力2.5mpa~3.5mpa,保温30min。
[0014]
较佳的,所述步骤s3中,所述中压应力变形焊接阶段的压应力1.5mpa~2mpa,保温时间2~3小时。
[0015]
较佳的,所述步骤s3中,所述低压应力焊接阶段压应力0.5mpa~1.5mpa,保温时间2~3小时。
[0016]
较佳的,所述步骤s3中,所述降温阶段的压应力降至0.5mpa后,冷却至室温。
[0017]
较佳的,当材料为6063铝合金时所述铝合金焊接温度为540℃~550℃,当材料为3a21铝合金时所述铝合金焊接温度为550℃~560℃。
[0018]
较佳的,两所述零件的焊接面采用榫卯结构连接。
[0019]
较佳的,两所述零件分别设置有凹结构和凸结构,所述凸结构设置在所述凹结构内从而形成两所述零件连接的榫卯结构,所述凹结构内壁尺寸公差0~+0.01mm,所述凸结构外壁尺寸公差-0.01mm~0mm。
[0020]
与现有技术比较本发明的有益效果在于:1,本发明在铝合金扩散焊接的不同阶段设计不同的工艺参数,实现了铝合金波导天线扩散焊质量和结构变形两个结果的偶合优化,焊缝强度超过母材的75%,波导腔变形不超过0.05mm,实现了铝合金波导天线高精度扩散焊接;2,焊接过程采用三种水平的压力加载,分别实现了破除氧化膜、变形加速焊接、扩散焊接三个的目标,三种压力加载能够加速焊接过程,提高了焊接效率,减少了焊接时间;3,与现有真空钎焊波导天线相比,扩散焊波导天线在焊接面边缘不会存在钎料形成的圆角,焊缝附近的波导腔面上也不会形成钎料铺展,波导腔的粗糙度和尺寸一致性大幅提高,从而大幅提升了波导天线的电磁特性,进一步提升了毫米波雷达的威力。
附图说明
[0021]
图1为所述毫米波波导天线的结构立体图;
[0022]
图2为所述毫米波波导天线的结构剖视图;
[0023]
图3为所述毫米波波导天线精密扩散焊接方法的参数曲线图。
[0024]
图中数字表示:
[0025]
1-第一零件;2-第二零件。
具体实施方式
[0026]
以下结合附图,对本发明上述的和另外的技术特征和优点作更详细的说明。
[0027]
如图1和图2所示,图1为所述毫米波波导天线的结构立体图;图2为所述毫米波波导天线的结构剖视图;本发明所述毫米波波导天线精密扩散焊接方法,毫米波波导天线采用铝合金材料经精密数控加工而成,表面粗糙度小于0.4μm。所述毫米波波导天线包括待焊接一体的第一零件1和第二零件2,两所述零件的焊接面采用设计榫卯结构保证装配精度,具体的,两所述零件分别设置有凹结构和凸结构,所述凸结构设置在所述凹结构内从而形成两所述零件连接的榫卯结构,所述凹结构内壁尺寸公差0~+0.01mm,所述凸结构外壁尺
寸公差-0.01mm~0mm。
[0028]
本发明所述毫米波波导天线精密扩散焊接方法,包括步骤:
[0029]
s1,采用化学清洗的方法清理零件表面,去除焊接面氧化膜。
[0030]
s2,在6小时内完成零件装配并装入真空炉;
[0031]
s3,设置工艺参数,并进行焊接加工,所述焊接加工包括:
[0032]
第一阶段为升温阶段;第二阶段为均温阶段;第三阶段为高压应力破膜阶段;第四阶段为中压应力变形焊接阶段;第五阶段为低压应力焊接阶段;第六阶段,降温阶段。
[0033]
如图3所示,图3为所述毫米波波导天线精密扩散焊接方法的参数曲线图;所述步骤s3中,所述升温阶段中真空炉的真空度需低于8
×
10-3
pa,尽可能的减少焊接面新生成的氧化膜。升温速率为2℃/min~5℃/min,防止升温速率过大导致真空度下降超过8
×
10-3
pa。所述升温阶段温度加热至铝合金焊接温度。所述升温阶段零件压应力设为较小的初始压应力0.5mpa,保证多层两件的紧密接触。
[0034]
所述步骤s3中,所述均温阶段需保证真空度低于3
×
10-4
pa,并在后续各阶段保持该真空度,压应力与所述升温阶段的压应力保持不变。
[0035]
所述步骤s3中,所述高压应力破膜阶段的压应力2.5mpa~3.5mpa,通过高压应力使多层零件的接触界面发生微观塑性变形,从而破碎接触面氧化膜,并保证多层界面在微观尺度接完全接触。保温30min,避免时间过长导致零件整体发生较大变形;
[0036]
所述步骤s3中,所述中压应力变形焊接阶段压应力1.5mpa~2mpa,使多层零件焊接面产生蠕变变形,从而为界面扩散提供额外驱动力,提高扩散焊接效率,该阶段保温时间2~3小时。
[0037]
所述步骤s3中,所述低压应力焊接阶段压应力0.5mpa~1.5mpa,保温时间2~3小时,通过低压应力保证多层界面结合,在保温阶段实现界面元素的充分扩散,保证焊接质量。
[0038]
所述步骤s3中,所述降温阶段压应力降至0.5mpa后,关机炉冷至室温。
[0039]
所述铝合金焊接温度设置如下:当材料为6063铝合金时焊接温度为540℃~550℃,当材料为3a21铝合金时焊接温度为550℃~560℃。
[0040]
扩散焊是将被焊零件紧密贴合,在一定的温度和压应力下,使接触面之间的原子相互扩散形成连接的焊接方法。连接界面在扩散焊过程中的微观演化主要分为四个阶段,第一阶段为初始物理接触阶段,表面不平整,只有部分接触点接触。第二阶段为塑性变形阶段,在外加压应力的作用下,通过屈服和蠕变机理是使表面发生塑性变形,而且表面的接触面积逐渐增大,最终达到整个界面的可靠接触,界面未达到紧密接触区域形成界面空洞。第三阶段为元素扩散与反应阶段,接触面的原子间相互扩散,形成紧密结合,由于变形引起晶格畸变、位错、空位等缺陷,使界面能量显著增加,原子处于高度激活状态,有利于扩散。第四阶段为体扩散阶段,微孔逐渐消失,组织成分逐渐均匀化,最后达到晶粒穿过晶界界面生长,原始界面消失。
[0041]
传统的扩散焊主要单一追求焊接质量,因压应力在扩散焊前期能够促进界面贴合,后期通过变形为界面提供能量,促进扩散,因此扩散焊在焊接温度下采用较高的压应力且在焊接过程保持不变的工艺参数,能够简化焊接过程并获得高质量焊缝。
[0042]
铝合金结构扩散焊因表面氧化膜破碎要求而需要采用较高压应力,而铝合金高温
强度低,因此采用传统方法会导致较大的变形,因而不能用于高精度的毫米波波导焊接。实际焊接结果表明波导腔变形量约0.3~0.5mm,远远超过0.05mm的设计要求。
[0043]
对于铝合金扩散焊而言,其主要影响因素是扩散时间和焊接温度。压应力在扩散焊前期通过变性实现界面接触、破除氧化膜等,是必要阶段。后期通过变性提供额外的扩散焊驱动力,促进扩散是辅助阶段,因扩散焊时间较长,结构的变形量主要产生于该阶段。因此本发明在界面接触和破膜之后,降低并动态调控焊接过程施加压应力,通过延长扩散时间,既保证产品获得良好的焊接质量,又能尽可能的降低结构变形。
[0044]
实施例一
[0045]
在实施例中,所述毫米波波导天线采用3a21铝合金材料制造,波导天线各层零件采用铝合金材料经精密数控加工而成,表面粗糙度小于0.4μm。两层零件的焊接面设计榫卯结构保证装配精度,其中凹结构内壁尺寸公差0~+0.01mm,凸结构外壁尺寸公差-0.01mm~0mm。
[0046]
毫米波波导天线精密扩散焊接方法,步骤如下
[0047]
s1,采用化学清洗的方法清理零件表面,去除焊接面氧化膜。
[0048]
s2,在6小时内完成零件装配并装入真空炉。
[0049]
s3,设置工艺参数,由以下几个阶段组成。第一阶段为升温阶段;第二阶段为均温阶段;第三阶段为高压应力破膜阶段;第四阶段为中压应力变形焊接阶段;第五阶段为低压应力焊接阶段;第六阶段,降温阶段。
[0050]
升温阶段真空炉的真空度需低于8
×
10-3
pa,尽可能的减少焊接面新生成的氧化膜。升温速率为2℃/min~5℃/min,防止升温速率过大导致真空度下降超过8
×
10-3
pa。升温阶段温度加热至铝合金焊接温度550℃~560℃。升温阶段零件压应力设为较小的初始压应力0.5mpa,保证多层两件的紧密接触。
[0051]
均温阶段需保证真空度低于3
×
10-4
pa,并在后续各阶段保持该真空度,压应力与升温阶段压应力保持不变。
[0052]
高压应力破膜阶段的压应力2.5mpa~3.5mpa,通过高压应力使多层零件的接触界面发生微观塑性变形,从而破碎接触面氧化膜,并保证多层界面在微观尺度接完全接触。保温30min,避免时间过长导致零件整体发生较大变形;
[0053]
中压应力变形焊接阶段压应力1.5mpa~2mpa,使多层零件焊接面产生蠕变变形,从而为界面扩散提供额外驱动力,提高扩散焊接效率,该阶段保温时间2~3小时。
[0054]
低压应力焊接阶段压应力0.5mpa~1.5mpa,保温时间2~3小时,通过低压应力保证多层界面结合,在保温阶段实现界面元素的充分扩散,保证焊接质量。
[0055]
降温阶段压应力降至0.5mpa后,关机炉冷至室温。
[0056]
实施例二
[0057]
在实施例中,毫米波波导天线采用6063铝合金材料制造,波导天线各层零件采用铝合金材料经精密数控加工而成,表面粗糙度小于0.4μm。两层零件的焊接面设计榫卯结构保证装配精度,其中凹结构内壁尺寸公差0~+0.01mm,凸结构外壁尺寸公差-0.01mm~0mm。
[0058]
毫米波波导天线精密扩散焊接方法,步骤如下
[0059]
s1,采用化学清洗的方法清理零件表面,去除焊接面氧化膜。
[0060]
s2,在6小时内完成零件装配并装入真空炉。
[0061]
s3,设置工艺参数,由以下几个阶段组成。第一阶段为升温阶段;第二阶段为均温阶段;第三阶段为高压应力破膜阶段;第四阶段为中压应力变形焊接阶段;第五阶段为低压应力焊接阶段;第六阶段,降温阶段。
[0062]
升温阶段真空炉的真空度需低于8
×
10-3
pa,尽可能的减少焊接面新生成的氧化膜。升温速率为2℃/min~5℃/min,防止升温速率过大导致真空度下降超过8
×
10-3
pa。升温阶段温度加热至铝合金焊接温度540℃~550℃。升温阶段零件压应力设为较小的初始压应力0.5mpa,保证多层两件的紧密接触。
[0063]
均温阶段需保证真空度低于3
×
10-4
pa,并在后续各阶段保持该真空度,压应力与升温阶段压应力保持不变。
[0064]
高压应力破膜阶段的压应力2.5mpa~3.5mpa,通过高压应力使多层零件的接触界面发生微观塑性变形,从而破碎接触面氧化膜,并保证多层界面在微观尺度接完全接触。保温30min,避免时间过长导致零件整体发生较大变形;
[0065]
中压应力变形焊接阶段压应力1.5mpa~2mpa,使多层零件焊接面产生蠕变变形,从而为界面扩散提供额外驱动力,提高扩散焊接效率,该阶段保温时间2~3小时。
[0066]
低压应力焊接阶段压应力0.5mpa~1.5mpa,保温时间2~3小时,通过低压应力保证多层界面结合,在保温阶段实现界面元素的充分扩散,保证焊接质量。
[0067]
降温阶段压应力降至0.5mpa后,关机炉冷至室温。
[0068]
以上所述仅为本发明的较佳实施例,对本发明而言仅仅是说明性的,而非限制性的。本专业技术人员理解,在本发明权利要求所限定的精神和范围内可对其进行许多改变,修改,甚至等效,但都将落入本发明的保护范围内。