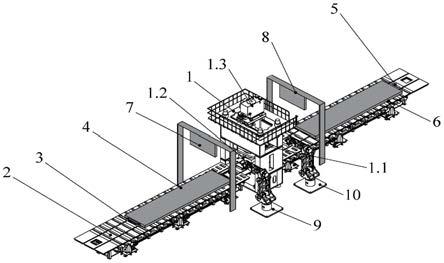
[0001]
本发明涉及宽厚板轧制技术领域,特别涉及一种实现宽厚板自动压力矫平的方法。
背景技术:[0002]
热轧宽厚板在轧后可能会出现板形质量问题,为了保证板材的平直,需要对板材进行矫直或矫正。一般来说厚度在40mm以下的板材可以通过辊式矫直机完成板材的矫直,而厚度在40mm以上的板材一般采用压力矫平机(简称压平机)进行压力矫平。
[0003]
目前,国际上的压平机生产主要以日本富士车辆株式会社、日本川崎重工株式会社、法国greucot loire、德国siempekamp等公司为主。我国针对矫平设备的设计开发始于20世纪60年代,虽然针对宽厚板矫平设备制成较晚,但发展迅速目前已经有50mn压平机。
[0004]
宽厚板压平机虽然经过几十年的发展取得了一些进步,但是非常遗憾的是宽厚板压平机目前仍处于手动工作模式,其工作过程是这样的:将需要矫平的板材用行车将其吊装到压平机机前辊道上,推送装置将推动板材向压平机方向移动,与此同时,操作人员确定需要压平的位置,当宽厚板运行到需要压平的位置后,停止前进,操作人员根据个人经验预设压平机压头行程或压平力以及两块垫板之间的位置,之后在宽厚板的上方和下方共放置三块垫板,然后,启动压下功能,压平机压头向下伸出,逐渐对宽厚板施压,达到指定位置后进行保压,达到保压时间后,操作人员操作对应按钮将压头返回;此时如果压头返程后,板材弹复变得平直,则完成了该位置压平工作,否则,继续按照当前的板凸度继续执行上面的过程。由以上过程说明可以看出,当前的压平机还处于手动工作模式,尚未实现自动化生产。
[0005]
在“智能制造”、“智慧工厂”的大背景下,压平机的手动生产大大制约了生产效率的提升,产品质量稳定性无法确保。为了提高生产效率和质量稳定性,实现板材自动压力矫平已迫在眉睫。经过分析,制约自动压力矫平的关键技术瓶颈之一是无法根据板凸度或原始曲率精准计算出压平机压头的行程或者压平力。
[0006]
因此,为了解决现有技术中的问题,需要一种根据板凸度或原始曲率精准计算出压平机压头的行程或者压平力,实现宽厚板自动压力矫平的方法。
技术实现要素:[0007]
本发明的目的在于提供一种实现宽厚板自动压力矫平的方法,所述方法包括如下步骤:
[0008]
(1)获取待压平板材的信息,包括弹性模量e、屈服强度σ
s
、金属板材宽度w和厚度h;
[0009]
(2)机前辊道后方的机前板材推送装置3推动待压平板材向压平机主机1方向移动;
[0010]
布置在压平机主机前的机前激光和视觉检测装置,获得待压平板材的原始曲率1/
r0、凹凸状态和弯曲段的纵向长度l0;
[0011]
(3)机前激光和视觉检测装置将所获得的待压平板材原始曲率1/r0、凹凸状态和弯曲段纵向长度l0的数据传送给压力矫平自动控制系统,
[0012]
当待压平板材弯曲段的区域中心到达压平机主机中心线时,机前板材推送装置停止动作;
[0013]
待压平板材停止运动,压平机主机上的压下油缸在压下油缸移动小车的拖动下开始移动,使得板材弯曲的中心点与安装在压下油缸下方的压头中心点重合;
[0014]
自动控制系统将根据待压平板材的凹凸状态和弯曲段纵向长度l0确定下垫板11和上垫板12的距离和位置;
[0015]
(4)建立压力矫平的数学模型:
[0016][0017]
其中,
[0018][0019][0020][0021][0022][0023][0024]
其中,m
e
为待压平板材的弹性弯矩的极限值,n
·
m,w为待压平板材的宽度,m;h为待压平板材厚度,m;σ
s
为待压平板材的屈服强度,pa;为待压平板材弹性弯曲曲率的极限值,1/m;曲率的极限值,1/m;为待压平板材的原始曲率,1/m;l为最外侧两块垫板的中心距,m;e为待压平板材的弹性模量,pa;i为待压平板材的惯性矩,m4,f为压平时所需的压平力,n。
[0025]
将压力矫平的数学模型(公式1)写入到自动控制系统软件程序中,将所获得的待压平板材4的弹性模量e、屈服强度σ
s
、金属板材宽度w、厚度h、原始曲率1/r0和最外侧两块垫
板的中心距l等参数的数值输入自动控制系统,控制系统计算得出压平所需的压平力f;
[0026]
(5)根据所获得的压平力f,自动控制系统按照所设定的压平力f控制安装在压平机主机上压下油缸下方的压头缓慢下压,达到设定值f后保压10s,随后压头复位,实现待压平板材的自动矫平;
[0027]
(6)待压平板材对应位置完成矫平工作后,机前板材推送装置继续推送待压平板材向前移动,待压平板材经过机后激光和图像检测装置,检测待压平板材在压平后的曲率是否满足要求,
[0028]
若满足要求则进行下一个弯曲区域的压平,否则,机前板材推送装置向后撤回,机后板材推送装置推动待压平板材沿反方向移动,当弯曲区域的中心与压平机主机中心线重合后,机后板材推送装置停止运动,随后复位,
[0029]
返回步骤(3)继续按照机后激光和图像检测装置所测得曲率进行二次压平。
[0030]
在一些较佳的实施例中,步骤(3)中,在待压平板材凹的一侧放置两块垫板,在凸的一侧放置一块垫板,三块垫板呈对称布置,同时当弯曲段的纵向长度l0≥1.5m时,最外侧两块垫板的距离l=1.5m;
[0031]
当弯曲段的长度l0<1.5m时,最外侧两块垫板的距离l=l0;自动控制系统将所计算得到的下垫板和上垫板的位置信息,发送给垫板机器人控制系统,机前垫板机器人和机后垫板机器人将按照所收到的位置信息放置下垫板和上垫板,放置完成后机前垫板机器人和机后垫板机器人复位。
[0032]
本发明提供的一种实现宽厚板自动压力矫平的方法,通过建立压力矫平模型,能够根据板凸度或原始曲率精准计算出压平机压平力,可以实现压力矫平的自动化生产,本发明的方法实施过程中不仅不会影响原产线布置,还可以实现自动生产,具有实施过程简单、自动化程度高的特点。
附图说明
[0033]
参考随附的附图,本发明更多的目的、功能和优点将通过本发明实施方式的如下描述得以阐明,其中:
[0034]
图1是本发明压平机工艺和设备布置图。
[0035]
图2是本发明压力矫平原理图。
具体实施方式
[0036]
通过参考示范性实施例,本发明的目的和功能以及用于实现这些目的和功能的方法将得以阐明。
[0037]
本发明提供了一种基于原始弯曲曲率和材料特征参数,以一次矫平为目标建立压力矫平力数学模型,并以压力矫平力数学模型为核心提供了一种实现宽厚板自动压力矫平的方法,包括如下步骤:
[0038]
(1)采用车间内的行车将待压平板材4放置在压平机主机1前面的机前辊道2上,同时获取待压平板材4的相关信息,包括弹性模量e、屈服强度σ
s
、金属板材宽度w和厚度h;
[0039]
(2)机前辊道2后方的机前板材推送装置3推动待压平板材4向压平机主机1方向移动,移动过程中布置在压平机主机1前的机前激光和视觉检测装置7获得待压平板材4的原
始曲率凹凸状态(用数字“0”表示凸,数字“1”表示凹)和弯曲段的纵向长度l0;
[0040]
(3)机前激光和视觉检测装置7将所获得的待压平板材4原始曲率凹凸状态和弯曲段纵向长度l0等数据传送给压力矫平自动控制系统,由自动控制系统控制设备的各个动作;当待压平板材4弯曲段的区域中心到达压平机主机1中心线时机前板材推送装置3停止动作,待压平板材4停止运动,压平机主机1上的压下油缸1.1在压下油缸移动小车1.3的拖动下开始移动,使得板材弯曲的中心点与安装在压下油缸1.1下方的压头1.2中心点重合。自动控制系统将根据待压平板材4的凹凸状态和弯曲段纵向长度l0确定下垫板11和上垫板12的距离和位置。
[0041]
具体来说:在待压平板材4凹的一侧放置两块垫板,在凸的一侧放置一块垫板,三块垫板呈对称布置,同时当弯曲段的纵向长度l0≥1.5m时,最外侧两块垫板的距离l=1.5m;当弯曲段的长度l0<1.5m时,最外侧两块垫板的距离l=l0。自动控制系统将所计算得到的下垫板11和上垫板12的位置信息,发送给垫板机器人控制系统,机前垫板机器人9和机后垫板机器人10将按照所收到的位置信息放置下垫板11和上垫板12,放置完成后机前垫板机器人9和机后垫板机器人10复位;
[0042]
(4)根据弹塑性力学理论结合压力矫平三点弯曲的特点,建立压力矫平的数学模型,如公式(1)所示:
[0043][0044]
公式(1)中,
[0045][0046][0047][0048][0049][0050][0051]
其中,m
e
为待压平板材的弹性弯矩的极限值,n
·
m,w为待压平板材的
宽度,m;h为待压平板材厚度,m;σ
s
为待压平板材的屈服强度,pa;为待压平板材弹性弯曲曲率的极限值,1/m;曲率的极限值,1/m;为待压平板材的原始曲率,1/m;l为最外侧两块垫板的中心距,m;e为待压平板材的弹性模量,pa;i为待压平板材的惯性矩,m4,f为压平时所需的压平力,n。
[0052]
将压力矫平的数学模型(公式1)写入到自动控制系统软件程序中,将所获得的待压平板材4的弹性模量e、屈服强度σ
s
、金属板材宽度w、厚度h、原始曲率和最外侧两块垫板的中心距l等参数的数值输入自动控制系统,控制系统计算得出压平所需的压平力f;
[0053]
(5)根据所获得的压平力f,自动控制系统将按照所设定的压平力f控制安装在压平机主机1上压下油缸1.1下方的压头1.2缓慢下压(速度在1mm/s~4mm/s之间),达到设定值f后,保压10s,保压完成后压头1.2复位,实现待压平板材4的自动矫平;
[0054]
(6)待压平板材4对应位置完成矫平工作后,机前板材推送装置3继续推送待压平板材4向前移动,待压平板材4经过机后激光和图像检测装置8,检测待压平板材4在压平后的曲率是否满足要求,满足要求,则进行下一个弯曲区域的压平。
[0055]
否则,机前板材推送装置3向后撤回,然后机后辊道6前方的机后板材推送装置5动作,推动待压平板材4沿反方向移动,当弯曲区域的中心与压平机主机1中心线重合后,机后板材推送装置5停止运动,返回步骤(3)继续按照机后激光和图像检测装置8所测得曲率进行二次压平。
[0056]
参见图1,传统的压力矫平线上在距离压平机主机1中心线前后大约3米处设置机前激光和视觉检测装置7和机后激光和视觉检测装置8,机前激光和视觉检测装置7和机后激光和视觉检测装置8安装在龙门架上;在压平机主机1的入口处和出口处分别安装机前垫板机器人9和机后垫板机器人10用于放置下垫板11和上垫板12;将机前垫板机器人9和机后垫板机器人10与压平机自动控制系统进行通讯,建立垫板位置和垫板放置完成等信号的数据通道;机前激光和视觉检测装置7和机后激光和视觉检测装置8的测量系统与压平机自动控制系统进行通讯,建立原始曲率、凹凸状态和弯曲段纵向长度等信号的数据通道;在压平机自动控制系统hmi上增设材料特征参数输入框,包括弹性模量、屈服强度、金属板材宽度和厚度,可以人为设定材料参数,也可以接收其他系统传递来的材料特征参数数据;同时增设压平力大小的输出框,用于显示模型计算出的压平力大小;将所建立的压力矫平的数学模型(公式1)写入压平机自动控制系统,实现以一次矫平为目标的压平力的计算。
[0057]
为了详细说明其实施方式,以具体实例进行说明,参见图1和图2,具体如下:
[0058]
(1)本实施例以q235板材压平为例,其材料特征参数如表1所示:
[0059]
表1材料特征参数表
[0060]
[0061]
(2)采用车间内的行车将待压平板材4放置在压平机主机1前面的机前辊道2上,同时获取待压平板材4的相关信息,弹性模量e=2
×
10
11
pa、屈服强度σ
s
=2.35
×
108pa、金属板材宽度w=3m、厚度h=0.09m。
[0062]
(3)机前辊道2后方的机前板材推送装置3推动待压平板材4向压平机主机1方向移动,同时经过机前激光和视觉检测装置7获得待压平板材4的原始曲率1/r0=0.00534861/m,该处板材呈凸型,弯曲段的纵向长度l0=1.2m。
[0063]
(4)机前激光和视觉检测装置7将所获得的待压平板材4原始曲率数字“0”和弯曲段的纵向长度l0传送给压力矫平自动控制系统。待压平板材4弯曲段的区域中心到达压平机主机1中心线时,机前板材推送装置3停止动作,待压平板材4停止运动,压平机主机1上的压下油缸1.1在压下油缸移动小车1.3的推动下开始移动,使得待压平板材4弯曲的中心点与安装在压下油缸1.1下方的压头1.2中心点重合。
[0064]
自动控制系统将根据待压平板材4的凸状态和弯曲段的纵向长度l0确定下垫板11和上垫板12的距离和位置,在待压平板材4的下方放两块垫板,上方放一块垫板,三块垫板呈对称布置,如图2所示;弯曲段的纵向长度l0<1.5m,最外侧两块垫板的中心距l=l0,自动控制系统将所得到的下垫板11和上垫板12的位置信息,发送给垫板机器人控制系统,机前垫板机器人9和机后垫板机器人10将按照所收到的位置信息放置下垫板11和上垫板12,放置完成后机前垫板机器人9和机后垫板机器人10复位。
[0065]
(5)将压力矫平的数学模型(公式1)写入到自动控制系统软件程序中,同时将所获得的待压平板材4的参数e,σ
s
,w,h,1/r0,l的数值输入自动控制系统,控制系统计算得出压平所需的压平力f,f=4029681n。
[0066]
(6)根据所获得的压平力f,自动控制系统将按照所设定的压平力f控制安装在压平机主机1上的压下油缸1.1下方的压头1.2缓慢下压,速度为2mm/s,达到设定值f后,保压10s,保压完成后将安装在压下油缸1.1下方的压头1.2复位,压头1.2通过压下油缸液压系统和压下油缸移动小车1.3进行复位,由此实现待压平板材4的自动矫平。
[0067]
(7)待压平板材4对应位置完成矫平工作后,机前板材推送装置3继续推送待压平板材4向前移动,待压平板材4经过机后激光和图像检测装置8,检测待压平板材4刚刚压平位置的曲率满足要求,然后进行下一个弯曲区域的压平。
[0068]
结合这里披露的本发明的说明和实践,本发明的其他实施例对于本领域技术人员都是易于想到和理解的。说明和实施例仅被认为是示例性的,本发明的真正范围和主旨均由权利要求所限定。