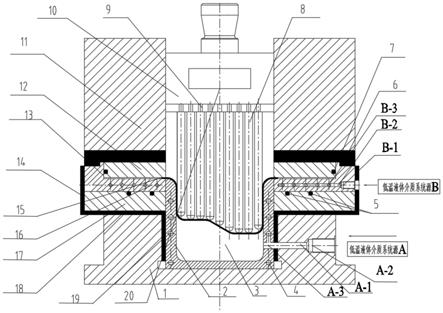
1.本发明涉及铝锂合金复杂薄壁结构件的特种成形制造工艺技术领域,具体地是指一种铝锂合金复杂结构件超低温柔性成形装置,薄壁是指结构件的壁厚不大于5mm,复杂结构件是指结构件的外形为空间曲面结构,该装置尤其适合成型铝锂合金薄壁复杂结构件。
背景技术:2.随着科技的进一步发展和社会的不断进步,结构轻量化对提高资源利用率,降低能耗和提高零部件的使用性能发挥着越来越重要的作用,已经成为当今制造业的发展趋势之一,而实现结构轻量化主要有材料和结构两种途径:材料途径是指采取铝合金、镁合金、钛合金等轻质材料代替钢铁等重型材料。因此,具有优良综合性能,可实现明显结构减重效果的铝锂合金成为关注的重点,而铝锂合金是一种以li为主要合金元素的新型铝合金,其特点是密度低,耐热性和抗腐蚀性优良。研究表明,在铝合金中加入1%的锂,可使合金密度降低3%,刚度提高6%。因此铝锂合金被认为是航空航天领域的理想结构材料。
3.铝锂合金的应用虽然有诸多优点,但是铝锂合金薄壁整体结构制造过程中主要存在以下几方面问题:
4.一是铝锂合金室温塑性较差,难以成形复杂形状构件;
5.二是铝锂合金断裂韧性差,采用传统的冲压、拉深等成形方法易出现微裂纹等缺陷;
6.三是回弹大,构件形状尺寸精度难以得到保证。
7.针对以上的问题,国内外对铝锂合金复杂结构件的成形通常采用热成形方法。热成形主要是利用铝锂合金材料在加热状态下的软化和蠕变性能,使其塑性提高,从而降低成形力和改善成形性,减少成形工序和零件的回弹。尽管可以通过提高成形温度来提高塑性和减小回弹,但造成成形后零件的强度降低,必须通过对成形零件热处理来进一步提高强度。然而成形后进行热处理时,加热或冷却过程中的受热不均将导致零件形状尺寸变化;因此必须设计一种新的成形工艺,来实现铝锂合金复杂结构件的精密成形,提高铝锂合金复杂结构件成形后的精度和性能,满足复杂结构件的工况需求。
8.国内外的学者研究表明,铝锂合金抗拉强度和屈服强度随着温度的降低而上升,延伸率基本保持不变甚至有所增长,具有良好的低温塑韧性,并且铝锂合金裂纹扩展速率随着温度的降低而降低,疲劳寿命与断裂韧性随着温度的降低而上升。
9.根据铝锂合金的这些特点,中国专利cn108326159a公布了一种大尺寸铝合金拼焊板类构件冷冻成形方法,用冷却剂使所述铝合金拼焊板冷却至超低温区间,使所述焊缝区的温度低于所述母材区的温度,采用模具成形出大尺寸铝合金整体曲面构件能够解决拼焊板焊缝区变形量大导致的开裂问题,适合于制造航空航天领域各种铝合金大尺寸整体薄壁曲面构件。但是,流体介质在成形过程中对模具产生较大的反作用力,反作用力随着液体压力和模具作用面积的增加而增加,导致设备吨位急剧增加此外,充液拉深依靠凸模型面控制最终零件的成形精度,因此对凸模加工精度要求较高。
10.多点成形采用一系列规则排列、离散的基本体代替整体模具,该方法的优点是基本体高度可调,可以实现不同形状复杂曲面的构型,因而可以减少模具加工费用,尤其适合异形曲面件的成形,但是,由于基本体群实质上是将整体模具型面用离散的小模具代替,并没有在根本上改变模具和板料的接触状态,板材在成形初期只与少数的基本体发生接触,由于接触点少、变形分布不均匀,极易发生局部应力集中,曲面件成形中常见的压痕、起皱、局部颈缩等缺陷不可避免。
技术实现要素:11.本发明解决的技术问题是:克服现有技术的不足,提供了一种铝锂合金薄壁结构件的超低温成形装置,铝锂合金复杂薄壁结构件室温成形难以成形复杂形状构件,断裂韧性差,室温成形易出现微裂纹等缺陷,成形回弹大,构件形状尺寸精度难以得到保证的难题。本发明的目的是结合多点成形和低温介质成形的技术优势,利用铝锂合金在超低温下增塑、增强的新现象,提供一种板材多点凸模充液拉深成形装置及方法,发明了一种铝锂合金薄壁结构件的超低温成形装置和成形制造方法,以解决铝锂合金复杂薄壁结构件室温成形难以成形复杂形状构件,断裂韧性差,室温成形易出现微裂纹等缺陷,成形回弹大,构件形状尺寸精度难以得到保证的难题。
12.本发明的技术解决方案是:
13.一种铝锂合金薄壁结构件的超低温柔性成形装置,该成形装置包括凹模座1、凹模套2、双层耐低温密封圈5、第一隔冷保温层6、超低温周向密封圈7、多点凸模头8、凸模本体10、第一压边圈11、第二压边内圈12、第二隔冷保温层14、低温成形凹模垫块a16、凹模座垫块b17、第三隔冷保温层18和第四隔冷保温层19;
14.凹模座1为整体圆柱形结构,中间留有圆柱形的内腔,即凹模座1为敞口带底的空心圆柱体;
15.凹模套2为敞口带底的空心圆柱体,即凹模套2带有空腔;
16.凹模套2的外径与凹模座1的内径相匹配,凹模套2放置在凹模座1的内腔中;凹模套2的外表面与凹模座1的内表面之间有第四隔冷保温层19;
17.凸模本体10为一顶端带有手柄的圆柱,凸模本体10的底端带有螺纹孔;
18.多点凸模头8包括多个钢柱,钢柱的一端带有外螺纹9,钢柱的另一端为半球型结构,钢柱带有外螺纹9的一端与凸模本体10的底端通过螺纹连接;
19.多点凸模头8位于凹模套2的空腔内;多个钢柱均布紧密排列;
20.多点凸模头8和凸模本体10组成成形凸模20;
21.第二压边内圈12为圆环结构;
22.第一隔冷保温层6为圆环结构;
23.第一压边圈11为圆环结构;
24.第二压边内圈12、第一隔冷保温层6、第一压边圈11从下到上依次套装在成形凸模20上,即首先将第二压边内圈12套装在成形凸模20上,然后将第一隔冷保温层6套装在成形凸模20上,最后将第一压边圈11套装在成形凸模20上;
25.凹模座垫块b17为圆环结构;
26.低温成形凹模垫块a16为圆环结构,低温成形凹模垫块a16固定连接在凹模座垫块
b17上面,且低温成形凹模垫块a16和凹模座垫块b17之间通过双层耐低温密封圈5进行密封,低温成形凹模垫块a16和凹模座垫块b17固定连接后一起套装在凹模座1上,凹模座垫块b17与凹模座1之间通过第三隔冷保温层18进行隔冷保温;
27.第二压边内圈12位于低温成形凹模垫块a16的上方;
28.超低温周向密封圈7套装在第二压边内圈12的外表面;
29.第二隔冷保温层14套装在低温成形凹模垫块a16和凹模座垫块b17的外表面,用于对低温成形凹模垫块a16和凹模座垫块b17进行隔冷保温;
30.多点凸模头8的外型面与待成形的铝锂合金薄壁结构件的内轮廓形状一致,多点凸模头8通过螺纹9调整多点凸模头8的高度,使多点凸模头8实现不同外轮廓形状的构型,同时可以根据待成形的铝锂合金板的零件的内轮廓形状进行单独的更换一根或者几根多点凸模头8;
31.成形凸模20与凹模套2之间的成形间隙,需要根据铝锂合金板的厚度来设定,成形凸模20与凹模套2的成形间隙优选为1.1t mm,t为铝锂合金板材厚度;成形凸模20设置与双动液压机的主缸连接的连接接口;
32.凹模套2与多点凸模头8围成的空腔作为高压低温充液室3,进行成形时,凹模套2的内腔与不同形状的多点凸模头8以及铝锂合金板15围成的空腔共同组成了不同形状的高压低温充液室3;
33.凹模座1的侧壁和凹模套2侧壁上开有通孔,该通孔作为低温液体介质系统源a与高压低温充液室3连通的通道;
34.凹模座1的侧边开有与低温液体介质系统源a相连接的充液接口a
‑
2及高压低温液体介质的进液通道a
‑
1,凹模套2侧壁上开有高压低温液体通道a
‑
3;
35.进液通道a
‑
1、液体通道a
‑
3与高压低温充液室3连通;
36.低温充液接口a
‑
2与低温液体介质系统源a连接的接头之间采用金属密封垫片和锥面复合式密封;
37.低温凹模成形垫块a16和凹模座垫块b17之间采用了锥面密封13和密封圈7密封的复合式密封方式;
38.凹模套2的尺寸为适应不同厚度的铝锂合金板和不同的成形的零件而略有差异,可根据不同厚度的铝锂合金板和不同形状的成形的零件进行调节和更换;
39.凹模套2侧壁上布满高压低温液体通道4,凹模套2的侧壁上也开有低温液体通道a
‑
3,低温液体通道a
‑
3与凹模座1开有的高压低温液体介质的进液通道a
‑
1相连通,低温液体介质系统源a输出的高压低温液体通过充液接口a
‑
2和高压低温液体介质的进液通道a
‑
1进入凹模套2的侧壁上开有的低温液体通道a
‑
3,然后进入高压低温充液室3和凹模套2侧壁上布满的高压低温液体通道4中。进入高压低温液体通道4中的高压低温液体可以用来降低和调整凹模套2的温度,从而控制铝锂合金板15的温度。
40.凹模套2使用时,先将第四隔冷保温层19放置在凹模座1中,然后再将凹模套2放置到凹模座1中;放置在凹模座1中的凹模套2的内腔与不同形状的多点凸模头8以及铝锂合金板15围成的空腔共同组成了不同形状的高压低温充液室3;
41.第一隔冷保温层6、第二隔冷保温层14、第三隔冷保温层18和第四隔冷保温层19均是将成形板材保持在深冷状态的主要结构。对于第一隔冷保温层6、第二隔冷保温层14、第
三隔冷保温层18和第四隔冷保温层19的隔冷保温设计,因保温材料无法承受液压机和模具的压力,因此需要将隔冷保温材料放置在抗压强度满足要求的装置中。装置采用中间填充隔冷保温材料,两边和四周采用钢板组成,使其抗压强度满足成形需要。保温材料选用珍珠岩混凝土,热导率为0.12~0.25w/(m
·
k),使用温度在
‑
273℃~200℃,抗压强度为1.5~8.5mpa。
42.第一压边圈11、第二压边内圈12、低温成形凹模垫块a16、凹模座垫块b17均为模块化设计,其尺寸根据不同厚度的铝锂合金板和不同形状的成形的零件来适配;凹模座垫块b17为圆环状结构,凹模座垫块b17的上表面与低温成形凹模垫块a16配合接触,两者相互配合的接触面开有双层密封沟槽,双层密封沟槽放置双层耐低温密封圈5进行密封,用于成形过程中高压低温液体介质的密封。双层耐低温密封圈5为可以采用镍、铟等金属材料制作的o形密封圈,具备超低温下的密封能力,优先采用铟软金属做成的密封圈。
43.低温成形凹模垫块a16为环状结构,并且侧面留有凸台,右侧边开有与独立低温液体介质系统源b相连接的充液接口b
‑
1及高压低温液体介质的进液通道b
‑
2,进液通道b
‑
2与低温液体介质通道b
‑
3连通,低温液体介质系统源b输出的高压低温液体通过充液接口b
‑
1和高压低温液体介质的进液通道b
‑
2进入低温成形凹模垫块a16的开有的低温液体介质通道b
‑
3,进入低温液体介质通道b
‑
3中的高压低温液体可以用来降低和调整低温成形凹模垫块a16的温度,从而控制铝锂合金板15的温度。低温充液接口b
‑
1与低温液体介质系统源b连接的接头之间采用金属密封垫片和锥面复合式密封。
44.第二压边内圈12为圆环状结构,侧面为密封面,开有密封沟槽,第二压边内圈12在侧面与低温成形凹模垫块a16侧面留有的凸台密封配合,密封沟槽之间使用的超低温周向密封圈7进行密封,超低温周向密封圈7为可以采用镍、铟等金属材料制作的o形密封圈,具备超低温下的密封能力,优先采用铟软金属做成的密封圈,同时第二压边内圈12和低温成形凹模垫块a16还采用了配合式的锥面密封13,实现了锥面密封。锥面密封加密封圈式的复合式密封共同用于成形过程中高压低温液体介质的密封。
45.铝锂合金板15是铝锂合金复杂薄壁结构件展开后的二维平面板材,第一压边圈11为整体式的压边圈,为圆环体状结构,设置在第一隔冷保温层6的正上方,上面设有与双动液压机的压边缸连接的接口;第一压边圈11和第二压边内圈12以及低温成形凹模垫块a16之间设置隔冷保温层6,用来防止超低温温度传递到第一压边圈11上。
46.使用时,首先将第三隔冷保温层18放置在凹模座1上,将凹模座垫块b17放置在第三隔冷保温层18上,然后将双层耐低温密封圈5放置到凹模座垫块b17开有的双层密封沟槽中,然后将低温成形凹模垫块a16放置到凹模座垫块b17上,然后再低温成形凹模垫块a16上放置铝锂合金板15,安装完成后将凹模座1放在液压机的下工作平台上,然后用压板将凹模座1固定在液压机的下工作平台上;
47.其次将超低温周向密封圈7用螺钉安装在第二压边内圈12上形成一组合体e,将第一隔冷保温层6放置在超低温周向密封圈7和第二压边内圈12形成的组合体e上,并用螺钉紧固,然后将该组合体e安装在第一压边圈11上,形成大组合体f,大组合体f通过与双动液压机的压边缸连接的接口直接安装到双动液压机的压边缸上,可以在压边缸的带动下控制铝锂合金板15成形过程中的压边力的大小;
48.最后,将不同形状的多点凸模头8通过多点凸模头8上的螺纹9直接连接在凸模本
体10上的螺纹孔中,然后组合成成形凸模20,将成形凸模20通过与双动液压机的主缸连接的接口直接连接到双动液压机的主缸上,可以在主缸的带动下沿着第一压边圈11、凹模套2形成的内腔上下移动;
49.本发明还提供了利用上述成形装置的铝锂合金复杂薄壁结构件的超低温成形制造方法,用于铝锂合金薄壁结构件的超低温成形,其成形过程主要包括如下步骤:
50.步骤一,读取铝锂合金薄壁结构件三维设计模型,根据该三维设计模型得到锂合金薄壁结构件的板料材料、曲面的曲率和板料的厚度,再根据得到的锂合金薄壁结构件的板料材料、曲面的曲率和板料的厚度通过有限元分析将薄壁复杂结构件三维设计模型展开为二维平面模型;
51.步骤二,对步骤一得到的二维平面模型进行修正,根据修正后的二维平面模型通过激光切割的方式切割铝锂合金薄壁结构件展开料,修正是指对二维平面模型预留工艺余量;
52.步骤三,对步骤二的激光切割完的展开料进行固溶处理,即将激光切割完成的展开料放在箱式电阻炉中进行退火处理,加热温度t=500~520℃,保温时间1~1.5h,如图4所示;
53.步骤四,将第三隔冷保温层18放置在凹模座1上,将凹模座垫块b17放置在第三隔冷保温层18上,然后将双层耐低温密封圈5放置到凹模座垫块b17开有的双层密封沟槽中,然后将低温成形凹模垫块a16放置到凹模座垫块b17上,然后再低温成形凹模垫块a16上放置铝锂合金板15;安装完成后将凹模座1放在液压机的下工作平台上,然后用压板将凹模座1固定在液压机的下工作平台上;
54.步骤五,将超低温周向密封圈7用螺钉安装在第二压边内圈12上形成一组合体e,将第一隔冷保温层6放置在超低温周向密封圈7和第二压边内圈12形成的组合体e上,并用螺钉紧固,然后将该组合体e安装在第一压边圈11上,形成大组合体f,大组合体f通过与双动液压机的压边缸连接的接口直接安装到双动液压机的压边缸上,液压缸可以通过控制液压力的大小,从而控制压边力的大小;
55.步骤六,利用高压转接接头将独立低温液体介质系统源a和凹模座1连接起来,跟独立低温液体介质系统源a形成封闭回路,从而形成高压低温液体介质充液室3;利用高压转接接头将独立低温液体介质系统源b和凹模座垫块b17连接起来,跟独立低温液体介质系统源b形成封闭回路;
56.步骤七,将步骤三制造完成的铝锂合金板15,放置在凹模座垫块b17上,压边时采用定间隙的方法,压边间隙通过旁边加半圆形垫环的形式实现,半圆形垫环厚度为(t+0.1t)mm,形状如图7所示,可以保证成形过程中,第二压边内圈12和低温成形凹模垫块a16间隙保持为1.1tmm不变;
57.步骤八,将不同形状的多点凸模头8通过多点凸模头8上的螺纹9直接连接在凸模本体10上的螺纹孔中,然后将成形凸模20通过与双动液压机的主缸连接的接口直接连接到双动液压机的主缸上;将多点凸模本体10连接到液压机的主缸上,液压机的主缸控制多点凸模本体10向下移动;
58.步骤九,利用压边缸控制第一隔冷保温层6、超低温周向密封圈7、第一压边圈11和第二压边内圈12共同形成的大组合体f向下移动使第二压边内圈12的下表面与铝锂合金板
15接触并施加压边力,压边力保持至f不变;
59.其中f=ap,a为压边圈下毛坯的投影面积(单位mm2),p为单位压边力(单位mpa),z为拉深系数的倒数,d为展开料的直径(单位mm),t为铝锂合金板材的厚度(单位mm),σ
b
为铝锂合金板材的抗拉强度(单位mpa)。
60.步骤十,独立低温液体介质系统源b按照如图5所示的初始液室压力曲线通过充液接口b
‑
1向低温成形凹模垫块a16充入高压低温液体介质,高压低温液体介质通过进液通道b
‑
2进入低温成形凹模垫块a16的开有的低温液体介质通道b
‑
3中,低温成形凹模垫块a16逐步填满低温液体介质,空气逐步被排出,使低温成形凹模垫块a16的温度逐渐降低,从而降低铝锂合金板15的温度;所述低温液体介质为一种超低温冷却介质,可以为液氮或液氦中的一种。
61.步骤十一,液压机的主缸控制多点凸模本体10向下移动,随之带动多点凸模头8向下移动,当多点凸模头8的下表面与铝锂合金板的上表面之间距离为(3~5)t mm时,独立低温液体介质系统源a按照如图6所示的初始液室压力曲线通过充液接口a
‑
2向凹模座1充入高压低温液体介质,高压低温液体介质通过进液通道a
‑
1进入凹模套2的开有的低温液体介质通道a
‑
3,从而进入高压低温充液室3中,此时,高压低温充液室3内逐步填满低温液体介质,空气逐步被排出,并使高压低温充液室3内部建立起(0.03σs~0.06σs)mpa的初始低温介质的液室压力;所述低温液体介质为一种超低温冷却介质,可以为液氮或液氦中的一种。
62.步骤十二,当高压低温充液室3内部建立起(0.03σs~0.06σs)mpa的初始液室压力后,液压机的主缸控制多点凸模本体10继续向下移动,随之带动多点凸模头8继续向下移动,下移过程中压边力保持不变,此时,继续通过充液孔接口a
‑
2继续按照如图6所示的液室压力曲线向高压低温充液室3充入低温液体介质,提高高压低温充液室3内部低温液体介质的压力至(0.3σs~0.6σs)mpa;
63.步骤十三,当高压低温充液室3内部建立起(0.3σs~0.6σs)mpa的液室压力,然后保温,测量模具温度降至
‑
100℃~
‑
196℃,此时,所述的铝锂合金板的温度达到
‑
100℃~
‑
196℃,液压机主缸控制多点凸模本体10继续下行,铝锂合金板料15逐渐流入,直至成形结束,成形出铝锂合金薄壁结构件;
64.步骤十四,多点低温充液成形结束后,卸载低温充液室3内的压力以及低温成形凹模垫块a16中的b
‑
3内的压力,液压机主缸带动多点凸模本体10回程,然后液压机压边缸带动第一隔冷保温层6、超低温周向密封圈7、第一压边圈11和第二压边内圈12共同形成的大组合体f上行,卸载压边力,使模具处于打开状态,取出成形完成的铝锂合金薄壁结构件。
65.本发明与现有技术相比的优点在于:
66.一、本发明利用铝锂合金在超低温下增塑、增强的特点,采用超低温柔性成形方法对铝锂合金板进行柔性成形,可以解决铝锂合金复杂薄壁结构件室温成形难以成形复杂形状构件,断裂韧性差,室温成形易出现微裂纹等缺陷,成形回弹大,构件形状尺寸精度难以得到保证的难题;
67.二、本发明利用多点凸模外轮廓构型可根据成形需要改变,而且无需额外加工模具的优势,可以实现复杂形状零件的柔性多步成形,并且极大的降低了模具的制造成本;
68.三、本发明方法制造的铝锂合金拼焊板类构件不会产生内部微观组织损伤,超低
温下成形对组织性能基本没有改变,成形后恢复原始组织状态;
69.四、本发明的柔性成形的过程中,铝锂合金板材在液体作用下产生的“摩擦保持效果”和“流体润滑效果”,可以进一步提高铝锂合金板材的成形极限,实现薄壁复杂构件的精密成形,另外铝锂合金板材和多点模具的工作表面形成冰冻润滑层,可降低铝锂合金板材流动的摩擦阻力,降低成形力,大幅降低成形装备吨位和造价
70.五、本发明还可以根据成形零件的复杂程度,在充液拉深步骤前增加预胀步骤,并根据成形需要设计预胀件的形状。
71.六、凹模套2为模块化设计,为组合式、可拆卸或更换式的结构,均为敞口带底的空心圆柱体,其尺寸为适应不同厚度的铝锂合金板和不同的成形的零件而略有差异,可根据不同厚度的铝锂合金板和不同形状的成形的零件进行调节和更换。
附图说明
72.图1为本发明的一种铝锂合金薄壁结构件的超低温柔性成形制造装置示意图;
73.图2为本发明的展开料的制备工艺流程;
74.图3为本发明的一种铝锂合金薄壁结构件的超低温柔性成形工艺流程;
75.图4为本发明的铝锂合金退火处理工艺曲线;
76.图5为本发明的初始液室压力加载曲线示意图;
77.图6为本发明液室压力加载曲线示意图。
78.图7为本发明半圆形垫环示意图。
具体实施方式
79.本发明针对现有技术的不足,提出了一种铝锂合金薄壁结构件的超低温成形装置和成形制造方法,铝锂合金复杂薄壁结构件室温成形难以成形复杂形状构件,断裂韧性差,室温成形易出现微裂纹等缺陷,成形回弹大,构件形状尺寸精度难以得到保证的难题。
80.本发明铝锂合金薄壁结构件的超低温成形装置和成形制造方法,涉及一种铝锂合金薄壁结构件的超低温成形装置,
81.整套装置采用组合式、可拆卸、快速更换式、模块化的结构,不同模块可根据不同厚度的铝锂合金板和不同的成形的零件进行调节和更换。
82.下面结合附图和实施例对本发明作进一步说明。
83.实施例
84.如图1
‑
图7所示,该成形装置包括凹模座1、凹模套2、双层耐低温密封圈5、第一隔冷保温层6、超低温周向密封圈7、多点凸模头8、凸模连接柱9、凸模本体10、第一压边圈11、第二压边内圈12、第二隔冷保温层14、铝锂合金板15、低温成形凹模垫块a16、凹模座垫块b17、第三隔冷保温层18、第四隔冷保温层19;
85.凹模套2为敞口带底的空心圆柱体,凹模套2的内腔与不同形状的多点凸模头8以及铝锂合金板15围成的空腔共同组成了不同形状的高压低温充液室3;
86.低温凹模成形垫块a16和凹模座垫块b17之间采用了锥面密封13和密封圈17密封的复合式密封方式;
87.凹模座1为整体圆柱形结构,中间留有圆柱形的内腔,用于放置不同结构形式的凹
模套2;凹模座1为敞口带底的空心圆柱体,侧边开有与低温液体介质系统源a相连接的充液接口a
‑
2及高压低温液体介质的进液通道a
‑
1,进液通道a
‑
1通过凹模套2侧壁上开的高压低温液体通道a
‑
3与凹模套2与多点凸模头8围成的空腔作为高压低温充液室3相连通,低温充液接口a
‑
2与低温液体介质系统源a连接的接头之间采用金属密封垫片和锥面复合式密封;
88.凹模套2为模块化设计,为组合式、可拆卸或更换式的结构,均为敞口带底的空心圆柱体,其尺寸为适应不同厚度的铝锂合金板和不同的成形的零件而略有差异,可根据不同厚度的铝锂合金板和不同形状的成形的零件进行调节和更换;
89.凹模套2侧壁上布满高压低温液体通道4,凹模套2的侧壁上也开有低温液体通道a
‑
3,低温液体通道a
‑
3与凹模座开有的高压低温液体介质的进液通道a
‑
1相连通,低温液体介质系统源a输出的高压低温液体通过充液接口a
‑
2和高压低温液体介质的进液通道a
‑
1进入凹模套2的侧壁上开有的低温液体通道a
‑
3,然后进入高压低温充液室3和凹模套2侧壁上布满的高压低温液体通道4中。进入高压低温液体通道4中的高压低温液体可以用来降低和调整凹模套2的温度,从而控制铝锂合金板15的温度。
90.凹模套2使用时,先将第四隔冷保温层19放置在凹模座1中,然后再将凹模套2放置到凹模座1中;放置在凹模座1中的凹模套2的内腔与不同形状的多点凸模头8以及铝锂合金板15围成的空腔共同组成了不同形状的高压低温充液室3;
91.第一隔冷保温层6、第二隔冷保温层14、第三隔冷保温层18和第四隔冷保温层19均是将成形板材保持在深冷状态的主要结构。对于第一隔冷保温层6、第二隔冷保温层14、第三隔冷保温层18和第四隔冷保温层19的隔冷保温设计,因保温材料无法承受液压机和模具的压力,因此需要将隔冷保温材料放置在抗压强度满足要求的装置中。装置采用中间填充隔冷保温材料,两边和四周采用钢板组成,使其抗压强度满足成形需要。保温材料选用珍珠岩混凝土,热导率为0.12~0.25w/(m
·
k),使用温度在
‑
273℃~200℃,抗压强度为1.5~8.5mpa。
92.第一压边圈11、第二压边内圈12、低温成形凹模垫块a16、凹模座垫块b17均为模块化设计,其尺寸根据不同厚度的铝锂合金板和不同形状的成形的零件来适配;凹模座垫块b17为圆环状结构,上表面与低温成形凹模垫块a16配合接触,两者相互配合的接触面开有双层密封沟槽,双层密封沟槽放置双层耐低温密封圈5进行密封,用于成形过程中高压低温液体介质的密封。双层耐低温密封圈5为可以采用镍、铟等金属材料制作的o形密封圈,具备超低温下的密封能力,优先采用铟软金属做成的密封圈。
93.低温成形凹模垫块a16为环状结构,并且侧面留有凸台,右侧边开有与独立低温液体介质系统源b相连接的充液接口b
‑
1及高压低温液体介质的进液通道b
‑
2,进液通道b
‑
2与低温液体介质通道b
‑
3连通,低温液体介质系统源b输出的高压低温液体通过充液接口b
‑
1和高压低温液体介质的进液通道b
‑
2进入低温成形凹模垫块a16的开有的低温液体介质通道b
‑
3,进入低温液体介质通道b
‑
3中的高压低温液体可以用来降低和调整低温成形凹模垫块a16的温度,从而控制铝锂合金板15的温度。低温充液接口b
‑
1与低温液体介质系统源b连接的接头之间采用金属密封垫片和锥面复合式密封。
94.第二压边内圈12为圆环状结构,侧面为密封面,开有密封沟槽,第二压边内圈12在侧面与低温成形凹模垫块a16侧面留有的凸台密封配合,密封沟槽之间使用的超低温周向密封圈7进行密封,超低温周向密封圈7为可以采用镍、铟等金属材料制作的o形密封圈,具
备超低温下的密封能力,优先采用铟软金属做成的密封圈,同时第二压边内圈12和低温成形凹模垫块a16还采用了配合式的锥面密封13,实现了锥面密封。锥面密封加密封圈式的复合式密封共同用于成形过程中高压低温液体介质的密封。
95.铝锂合金板15是铝锂合金复杂薄壁结构件展开后的二维平面板材,第一压边圈11为整体式的压边圈,为圆环体状结构,设置在第一隔冷保温层6的正上方,上面设有与双动液压机的压边缸连接的接口;第一压边圈11和第二压边内圈12以及低温成形凹模垫块a16之间设置隔冷保温层6,用来防止超低温温度传递到第一压边圈11上。
96.成形凸模20采用的多点凸模结构形式,多点凸模20主要由凸模本体10和多个不同高度的多点凸模头8组成,是由多点凸模头8通过多点凸模头8上的螺纹9直接连接在凸模本体10上的螺纹孔上。多个多点凸模头8均布紧密排列,沿竖向相互独立设置并构成凸模成形模块,多个多点凸模头8上表面构成与所需制造的薄壁复杂结构件内轮廓形状相同的凸模成形模块。
97.凸模本体10位于多个多点凸模头8的正上方,凸模本体10上与多个多点凸模头8相对应位置设有多个螺纹孔,螺纹孔的数量与多点凸模头8的数量相一致,多点凸模头8上端设有与凸模体10上的螺纹孔相对应的螺纹,多个多点凸模头8上端的螺纹与凸模体10的多个螺纹孔一一对应且分别穿入相应的螺纹孔内,并且采用螺纹连接9。
98.成形凸模20放置在第一压边圈11的中心,多点凸模的型面根据待成形的铝锂合金薄壁结构件的内腔形状来设计,多点凸模的外型面与待成形的铝锂合金薄壁结构件的内轮廓形状一致。多个多点凸模头8可以通过螺纹连接9调整多点凸模头8高度,使多点成形凸模8实现不同外轮廓形状的构型,同时可以根据待成形的铝锂合金板的零件的内轮廓形状进行单独的更换一根或者几根多点凸模头8。
99.成形凸模20与凹模套2之间的成形间隙,需要根据铝锂合金板的厚度来设定,成形凸模20与凹模套2的成形间隙优选为1.1t mm,t为铝锂合金板材厚度;成形凸模20设置与双动液压机的主缸连接的连接接口;
100.使用时,首先将第三隔冷保温层18放置在凹模座1上,将凹模座垫块b17放置在第三隔冷保温层18上,然后将双层耐低温密封圈5放置到凹模座垫块b17开有的双层密封沟槽中,然后将低温成形凹模垫块a16放置到凹模座垫块b17上,然后再低温成形凹模垫块a16上放置铝锂合金板15,安装完成后将凹模座1放在液压机的下工作平台上,然后用压板将凹模座1固定在液压机的下工作平台上;
101.其次将超低温周向密封圈7用螺钉安装在第二压边内圈12上形成一组合体e,将第一隔冷保温层6放置在超低温周向密封圈7和第二压边内圈12形成的组合体e上,并用螺钉紧固,然后将该组合体e安装在第一压边圈11上,形成大组合体f,大组合体f通过与双动液压机的压边缸连接的接口直接安装到双动液压机的压边缸上,可以在压边缸的带动下控制铝锂合金板15成形过程中的压边力的大小;
102.最后,将不同形状的多点凸模头8通过多点凸模头8上的螺纹9直接连接在凸模本体10上的螺纹孔中,然后组合成成形凸模20,将成形凸模20通过与双动液压机的主缸连接的接口直接连接到双动液压机的主缸上,可以在主缸的带动下沿着第一压边圈11、凹模套2形成的内腔上下移动;
103.本发明还提供了利用上述成形装置的铝锂合金复杂薄壁结构件的超低温成形制
造方法,用于铝锂合金薄壁结构件的超低温成形,其成形过程主要包括如下步骤:
104.步骤一、读取铝锂合金薄壁结构件三维设计模型,根据该三维设计模型得到锂合金薄壁结构件的板料材料、曲面的曲率和板料的厚度,再根据得到的锂合金薄壁结构件的板料材料、曲面的曲率和板料的厚度通过有限元分析将薄壁复杂结构件三维设计模型展开为二维平面模型;
105.步骤二、对步骤一得到的二维平面模型进行修正,根据修正后的二维平面模型通过激光切割的方式切割铝锂合金薄壁结构件展开料,修正是指对二维平面模型预留工艺余量;
106.步骤三、对步骤二的激光切割完的展开料进行固溶处理,即将激光切割完成的展开料放在箱式电阻炉中进行固溶处理,加热温度t=500~520℃,保温时间1~1.5h;
107.步骤四、首先将第三隔冷保温层18放置在凹模座1上,将凹模座垫块b17放置在第三隔冷保温层18上,然后将双层耐低温密封圈5放置到凹模座垫块b17开有的双层密封沟槽中,然后将低温成形凹模垫块a16放置到凹模座垫块b17上,然后再低温成形凹模垫块a16上放置铝锂合金板15;安装完成后将凹模座1放在液压机的下工作平台上,然后用压板将凹模座1固定在液压机的下工作平台上;
108.步骤五、其次将超低温周向密封圈7用螺钉安装在第二压边内圈12上形成一组合体e,将第一隔冷保温层6放置在超低温周向密封圈7和第二压边内圈12形成的组合体e上,并用螺钉紧固,然后将该组合体e安装在第一压边圈11上,形成大组合体f,大组合体f通过与双动液压机的压边缸连接的接口直接安装到双动液压机的压边缸上,液压缸可以通过控制液压力的大小,从而控制压边力的大小;
109.步骤六、利用高压转接接头将独立低温液体介质系统源a和凹模座1连接起来,跟独立低温液体介质系统源a形成封闭回路,从而形成高压低温液体介质充液室3;利用高压转接接头将独立低温液体介质系统源b和凹模座垫块b17连接起来,跟独立低温液体介质系统源b形成封闭回路;
110.步骤七、将步骤三制造完成的铝锂合金板15,放置在凹模座垫块b17上,压边时采用定间隙的方法,压边间隙通过旁边加半圆形垫环的形式实现,半圆形垫环厚度为(t+0.1t)mm,形状如图7所示,可以保证成形过程中,第二压边内圈12和低温成形凹模垫块a16间隙保持为1.1tmm不变;
111.步骤八、将不同形状的多点凸模头8通过多点凸模头8上的螺纹9直接连接在凸模本体10上的螺纹孔中,然后将成形凸模20通过与双动液压机的主缸连接的接口直接连接到双动液压机的主缸上;将多点凸模本体10连接到液压机的主缸上,液压机的主缸控制多点凸模本体10向下移动;
112.步骤九、利用压边缸控制第一隔冷保温层6、超低温周向密封圈7、第一压边圈11和第二压边内圈12共同形成的大组合体f向下移动使第二压边内圈12的下表面与铝锂合金板15接触并施加压边力,压边力保持至f不变;
113.其中f=ap,a为压边圈下毛坯的投影面积(单位mm2)p为单位压边力(单位mpa),z为拉深系数的倒数,d为展开料的直径(单位mm),t为铝锂合金板材的厚度(单位mm),σ
b
为铝锂合金板材的抗拉强度(单位mpa)。
114.步骤十、独立低温液体介质系统源b按照如图5所示的初始液室压力曲线通过充液接口b
‑
1向低温成形凹模垫块a16充入高压低温液体介质,高压低温液体介质通过进液通道b
‑
2进入低温成形凹模垫块a16的开有的低温液体介质通道b
‑
3中,低温成形凹模垫块a16逐步填满低温液体介质,空气逐步被排出,使低温成形凹模垫块a16的温度逐渐降低,从而降低铝锂合金板15的温度;所述低温液体介质为一种超低温冷却介质,可以为液氮或液氦中的一种。
115.步骤十一、液压机的主缸控制多点凸模本体10向下移动,随之带动多点凸模头8向下移动,当多点凸模头8的下表面与铝锂合金板的上表面之间距离为(3~5)t mm时,独立低温液体介质系统源a按照如图5所示的初始液室压力曲线通过充液接口a
‑
2向凹模座1充入高压低温液体介质,高压低温液体介质通过进液通道a
‑
1进入凹模套2的开有的低温液体介质通道a
‑
3,从而进入高压低温充液室3中,此时,高压低温充液室3内逐步填满低温液体介质,空气逐步被排出,并使高压低温充液室3内部建立起(0.03σs~0.06σs)mpa的初始低温介质的液室压力;所述低温液体介质为一种超低温冷却介质,可以为液氮或液氦中的一种。σs为铝锂合金板材的屈服强度;
116.步骤十二、当高压低温充液室3内部建立起(0.03σs~0.06σs)mpa的初始液室压力后,液压机的主缸控制多点凸模本体10继续向下移动,随之带动多点凸模头8继续向下移动,下移过程中压边力保持不变,此时,继续通过充液孔接口a
‑
2继续按照如图6所示的液室压力曲线向高压低温充液室3充入低温液体介质,提高高压低温充液室3内部低温液体介质的压力至(0.3σs~0.6σs)mpa;
117.步骤十三、当高压低温充液室3内部建立起(0.3σs~0.6σs)mpa的液室压力,然后保温,测量模具温度降至
‑
100℃~
‑
196℃,此时,所述的铝锂合金板的温度达到
‑
100℃~
‑
196℃,液压机主缸控制多点凸模本体10继续下行,铝锂合金板料15逐渐流入,直至成形结束,成形出铝锂合金薄壁结构件;
118.步骤十四、多点低温充液成形结束后,卸载低温充液室3内的压力以及低温成形凹模垫块a16中的b
‑
3内的压力,液压机主缸带动多点凸模本体10回程,然后液压机压边缸带动第一隔冷保温层6、超低温周向密封圈7、第一压边圈11和第二压边内圈12共同形成的大组合体f上行,卸载压边力,使模具处于打开状态,用工具取出成形完成的铝锂合金薄壁结构件。
119.本发明说明书中未作详细描述的内容属本领域技术人员的公知技术。