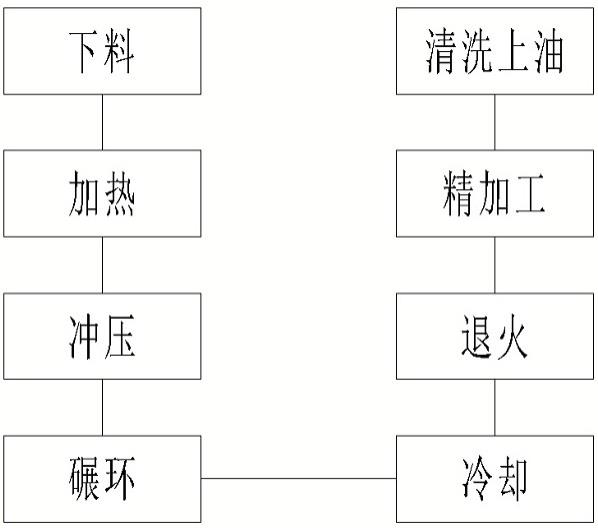
1.本发明涉及一种滚圈生产线及其生产工艺,属于轴承滚圈生产技术领域。
背景技术:2.轴承一般由内圈、外圈和滚子组成,滚圈的生产一般由锯切下料、加热、锻压、碾环、退火、精加工等工序组成,现有的滚圈生产中主要存在以下问题:1、圆钢头尾坯料在锯切时混入正常坯料中,在坯料加热时靠人工将头尾料挑选出,无法完全挑干净且影响坯料加热效率,由于圆钢头尾部分容易携带疏松、夹渣等铸造缺陷,在滚圈生产时,这些缺陷的存在会导致滚圈出现相应的质量问题;2、在锯切机床锯切圆钢时,锯切屑料需要人工清理,影响生产效率;3、在坯料碾成环形滚圈毛坯后,需要进行冷却,现有冷却设备的冷却效率低影响生产效率,且冷却均匀性不好,给滚圈的质量均匀性带来负面影响;4、滚圈毛坯退火时,由于滚圈规格不同,在人工装料时易造成料框过重或装料过高,进入退火炉后给退火炉造成不必要的损伤,引起设备故障;5、在退火炉料框吊装时,吊装设备复杂、昂贵,维护不方便。
技术实现要素:3.本发明的目的在于克服上述不足,提供一种圆钢锯切时自动挑出头尾料、锯切屑料自动收集、碾环后冷却效率高、冷却均匀、自动限制退火炉进料重量和装料高度、料框吊装装置结构简单的滚圈生产线及其生产工艺。
4.本发明的目的是这样实现的:一种滚圈生产线,包含依次序先后设置的自动锯切下料系统、加热炉、冲压机、碾环机、冷却炉、退火炉、精加工车床和自动清洗上油机;所述自动锯切下料系统包含安装在锯切机床上的头尾料自动分拣装置和屑料收集系统;所述头尾料自动分拣装置包含光电传感器、倾斜设置的坯料溜槽和分拣气缸;所述光电传感器安装在锯切位置的前后两侧,分别监测并反馈待切圆钢的头部和尾部信号;所述坯料溜槽设置在锯切位置的前下方,坯料溜槽位置高的一端底部设有定位销,定位销转动嵌置在锯切机床上的定位通孔内,坯料溜槽位置低的一端设有推杆,推杆活动嵌置在分拣气缸活动端端部的通孔内,分拣气缸的固定端固装在锯切机床上;所述屑料收集系统包含倾斜设置在锯切位置下方的屑料收集槽、屑料输送装置和底部设有滚轮的屑料收集车;所述屑料输送装置包含壳体、无轴螺旋输送叶片和安装在壳体端部的传动电机;所述壳体上设有屑料入口和屑料出口,所述屑料入口位于屑料收集槽出口的正下方,屑料出口位于屑料收集车的正上方,壳体底部设有切屑液出口,切屑液出口位置设有过滤网,切屑液出口通过管路与锯切机床的切削液储存槽相连通;所述无轴螺旋输送叶片架设在壳体内部,无轴螺旋输送叶片的旋转轴与传动电机通过变速箱传动连接;所述冷却炉包含左右两端分别设有主动链轮和从动链轮的炉架、套设在主动链轮
和从动链轮上的网带式输送带、设置在网带式输送带正上方的吸风罩、设置在网带式输送带下方的送风管、第一引风机、第二引风机和热电偶;所述吸风罩的顶部出风口设置在车间屋顶外;所述第一引风机安装在炉架右半部分的炉侧壁上,第一引风机出风口与送风管的进风口相连;所述第二引风机安装在炉架左半部分的吸风罩侧壁上;所述热电偶安装在吸风罩内;所述退火炉包含设置在退火炉入炉口辊道上的限高限重装置、架设在退火炉入炉口辊道旁的上料装置和滑动设置在入炉口辊道上的料框;所述限高限重装置包含竖向设置在退火炉入炉口辊道两侧的支撑杆、转动设置在两侧支撑杆上的横杆、固装在横杆中部的物料挡板、安装在横杆一端的信号触发板、设置在支撑杆上并靠近信号触发板的接近开关、设置在入炉口辊道轴两端轴承座底部的称重模块和声光报警装置;所述信号触发板通过定位螺栓旋转安装在横杆上;所述接近开关的信号触发点设在信号触发板的旋转轨迹上;所述接近开关和称重模块分别通过信号电缆与声光报警装置相连;所述上料装置包含安装有吊钩的上料架、和挂在吊钩上的吊装工装;所述吊装工装包含吊环、对称设置的两组悬臂、撑杆;所述吊环吊装在吊钩上,吊环的底部与悬臂的顶端铰接;所述悬臂下部固装有横档,悬臂的底端设有l形钩;所述撑杆的左端转动套装在左侧悬臂的横档上,设置在撑杆右端的限位挡块卡接在右侧悬臂的横档上;本发明一种滚圈生产线,所述坯料溜槽的出口下方对应设有并排放置的合格坯料框和头尾料框;本发明一种滚圈生产线,所述屑料输送装置的无轴螺旋输送叶片用链板式输送带代替,链板式输送带的主传动轮与传动电机通过变速箱传动连接;本发明一种滚圈生产线,所述第一引风机和第二引风机为轴流风机;所述主动链轮通过变速箱与电机传动连接;本发明一种滚圈生产线,所述物料挡板的下沿呈向入炉方向弯曲的曲面形状;本发明一种滚圈生产线,所述左侧悬臂的横档上设有限制撑杆沿横档滑动的限位圈;一种滚圈生产工艺,所述滚圈生产工艺是上述滚圈生产线实现的,其工艺步骤为:步骤一、下料:自动锯切下料系统将圆钢按设定的定尺长度进行锯切成坯料,锯切下来的坯料通过坯料溜槽滑落至合格坯料框;当光电传感器监测到锯切圆钢头部或尾部时,分拣气缸动作,推动坯料溜槽以定位销为中心发生转向,使坯料溜槽的出料口方向对准头尾料框,锯切下来的含圆钢头部或尾部的坯料进入头尾料框;锯切时产生的屑料由屑料收集系统进行收集,锯切屑料和切削液先进入屑料收集槽,然后从屑料入口进入屑料输送装置,无轴螺旋输送叶片将屑料输送至屑料出口后进入屑料收集车,切削液则经过滤网过滤后从壳体底部的切屑液出口回流至锯切机床的切削液储存槽实现循环使用;步骤二、加热:将锯切好的坯料送入加热炉加热;步骤三、冲压:将加热好的坯料送入冲压机锻压,然后在坯料心部位置冲出通孔而形成环形坯料;步骤四、碾环:碾环机将红热状态的环形坯料进一步碾压锻造成环形滚圈毛坯;步骤五、冷却:经碾环后的高温环形滚圈毛坯进入冷却炉冷却,热电偶监测到温度超出设定温度时,启动对应位置的第一引风机或第二引风机,第一引风机将冷风吹入送风
管,冷风从送风管出口吹出,透过网带式输送带流经环形滚圈毛坯,带走热量使环形滚圈毛坯降温后转变为热风,热风进入吸风罩后排出车间;第二风机将冷风直接吹至滚圈毛坯使之降温;热电偶监测到温度未超出设定值时,关闭对应位置的第一引风机或第二引风机,节约电能;步骤六、退火:将经冷却后的滚圈毛坯堆放入料框,人工抬起撑杆的右端并向上推,使两个悬臂分开,控制吊钩下降,使两个悬臂的l形钩位于料框上沿的下方,向右拉紧撑杆使l形钩夹紧并勾住料框上沿,压下撑杆右端,使撑杆右端的限位挡块卡住右侧悬臂的横档,使两个悬臂的l形钩保持夹紧状态不向外侧松脱;控制吊钩吊起料框并将之放置于退火炉入炉口辊道上,称重模块对料框料框重量进行检测,若超重则向声光报警装置反馈超重报警信号,将料框超重的滚圈毛坯取出并符合重量限制要求后,辊道将料框向后推进;在料框经过横杆时,物料挡板受到料框上沿或堆放位置高出料框上沿的滚圈毛坯推动而发生转动,滚圈毛坯的位置越高,则横杆转动的角度越大,横杆带动信号触发板转动,当信号触发板碰到接近开关的触发开关时,接近开关向声光报警装置反馈限高报警信号;当料框的滚圈毛坯同时满足限高限重要求后,辊道将料框送入退火炉退火;步骤七、精加工:经退火后的滚圈毛坯由机加工员工在精加工车床上按图纸要求进行车削、开孔等操作;步骤八、清洗上油:经精加工后的滚圈进入自动清洗上油机清洗并上油,上油后即进行包装入库。
5.与现有技术相比,本发明的有益效果是:本发明通过在锯切坯料时,将圆钢头尾坯料自动分开,确保头尾坯料不会混入滚圈后续生产,杜绝由此产生的滚圈质量问题,提高了坯料加热效率;将锯切屑料通过输送机构自动排出锯切机床,免去人工操作,提高生产效率;通过设置底部送风冷却方式,在滚圈毛坯高温段实现均匀快速冷却,在滚圈毛坯低温段通过侧向吹风冷却,简化设备结构,提高了冷却效率;在滚圈毛坯进入退火炉退火前设置限高限重装置,确保进入退火炉的料框内物料的重量和高度满足退火炉设计要求,避免损坏退火炉;吊装工装结构简单,操作方便,提高吊装效率,节约设备投入成本。
附图说明
6.图1为本发明一种滚圈生产工艺的工艺流程图。
7.图2为本发明一种滚圈生产线的自动锯切下料系统结构示意图。
8.图3为本发明一种滚圈生产线的自动锯切下料系统左视结构示意图。
9.图4为本发明一种滚圈生产线的冷却炉正视结构示意图。
10.图5为本发明一种滚圈生产线的冷却炉左视结构示意图。
11.图6为本发明一种滚圈生产线的冷却炉右视结构示意图。
12.图7为本发明一种滚圈生产线的退火炉结构示意图。
13.图8为本发明一种滚圈生产线的退火炉限高限重装置结构示意图。
14.图9为本发明一种滚圈生产线的退火炉上料装置结构示意图。
15.图10为本发明一种滚圈生产线的退火炉吊装工装结构示意图。
16.图11为本发明一种滚圈生产线的吊装工装l形钩吊装料框结构示意图。
17.其中:圆钢101、滚圈毛坯102;下料系统1、冷却炉2、退火炉3;自动分拣装置1.1、屑料收集系统1.2、合格坯料框1.3、头尾料框1.4;光电传感器1.1.1、坯料溜槽1.1.2、分拣气缸1.1.3、定位销1.1.4、定位通孔1.1.5、推杆1.1.6;屑料收集槽1.2.1、屑料输送装置1.2.2、屑料收集车1.2.3、壳体1.2.4、无轴螺旋输送叶片1.2.5、传动电机1.2.6、屑料入口1.2.7、、屑料出口1.2.8、切屑液出口1.2.9;炉架2.1、网带式输送带2.2、吸风罩2.3、送风管2.4、第一引风机2.5、第二引风机2.6、热电偶2.7、主动链轮2.8、从动链轮2.9;限高限重装置3.1、上料装置3.2、料框3.3;支撑杆3.1.1、横杆3.1.2、物料挡板3.1.3、信号触发板3.1.4、接近开关3.1.5、称重模块3.1.6、声光报警装置3.1.7、上料架3.2.1、吊钩3.2.2、吊装工装3.2.3、吊环3.2.4、悬臂3.2.5、撑杆3.2.6、横档3.2.7、l形钩3.2.8、限位挡块3.2.9、限位圈3.2.10。
具体实施方式
18.参见图1~11,本发明涉及的一种滚圈生产线,包含依次序先后设置的自动锯切下料系统1、加热炉、冲压机、碾环机、冷却炉2、退火炉3、精加工车床和自动清洗上油机;所述自动锯切下料系统1包含安装在锯切机床上的头尾料自动分拣装置1.1和屑料收集系统1.2;所述头尾料自动分拣装置1.1包含光电传感器1.1.1、倾斜设置的坯料溜槽1.1.2和分拣气缸1.1.3;所述光电传感器1.1.1安装在锯切位置的前后两侧,分别监测并反馈待切圆钢的头部和尾部信号;所述坯料溜槽1.1.2设置在锯切位置的前下方,坯料溜槽1.1.2位置高的一端底部设有定位销1.1.4,定位销1.1.4转动嵌置在锯切机床上的定位通孔1.1.5内,坯料溜槽1.1.2位置低的一端设有推杆1.1.6,推杆1.1.6活动嵌置在分拣气缸1.1.3活动端端部的通孔内,分拣气缸1.1.3的固定端固装在锯切机床上;所述屑料收集系统1.2包含倾斜设置在锯切位置下方的屑料收集槽1.2.1、屑料输送装置1.2.2和底部设有滚轮的屑料收集车1.2.3;所述屑料输送装置1.2.2包含壳体1.2.4、无轴螺旋输送叶片1.2.5和安装在壳体端部的传动电机1.2.6;所述壳体1.2.4上设有屑料入口1.2.7和屑料出口1.2.8,所述屑料入口1.2.7位于屑料收集槽1.2.1出口的正下方,屑料出口1.2.8位于屑料收集车1.2.3的正上方,壳体1.2.4底部设有切屑液出口1.2.9,切屑液出口1.2.9位置设有过滤网,切屑液出口1.2.9通过管路与锯切机床的切削液储存槽相连通;所述无轴螺旋输送叶片1.2.5架设在壳体1.2.4内部,无轴螺旋输送叶片1.2.5的旋转轴与传动电机1.2.6通过变速箱传动连接;所述冷却炉2包含左右两端分别设有主动链轮2.8和从动链轮2.9的炉架2.1、套设在主动链轮2.8和从动链轮2.9上的网带式输送带2.2、设置在网带式输送带2.2正上方的吸风罩2.3、设置在网带式输送带2.2下方的送风管2.4、第一引风机2.5、第二引风机2.6和热电偶2.7;所述吸风罩2.3的顶部出风口设置在车间屋顶外;所述第一引风机2.5安装在炉架2.1右半部分的炉侧壁上,第一引风机2.5出风口与送风管2.4的进风口相连;所述第二引风机2.6安装在炉架2.1左半部分的吸风罩2.3侧壁上;所述热电偶2.7安装在吸风罩2.3内;
所述退火炉3包含设置在退火炉3入炉口辊道上的限高限重装置3.1、架设在退火炉3入炉口辊道旁的上料装置3.2和滑动设置在入炉口辊道上的料框3.3;所述限高限重装置3.1包含竖向设置在退火炉3入炉口辊道两侧的支撑杆3.1.1、转动设置在两侧支撑杆3.1.1上的横杆3.1.2、固装在横杆3.1.2中部的物料挡板3.1.3、安装在横杆3.1.2一端的信号触发板3.1.4、设置在支撑杆3.1.1上并靠近信号触发板3.1.4的接近开关3.1.5、设置在入炉口辊道轴两端轴承座底部的称重模块3.1.6和声光报警装置3.1.7;所述信号触发板3.1.4通过定位螺栓3.1.8旋转安装在横杆3.1.2上;所述接近开关3.1.5的信号触发点设在信号触发板3.1.4的旋转轨迹上;所述接近开关3.1.5和称重模块3.1.6分别通过信号电缆与声光报警装置3.1.7相连;所述上料装置3.2包含安装有吊钩3.2.2的上料架3.2.1、和挂在吊钩3.2.2上的吊装工装3.2.3;所述吊装工装3.2.3包含吊环3.2.4、对称设置的两组悬臂3.2.5、撑杆3.2.6;所述吊环3.2.4吊装在吊钩3.2.2上,吊环3.2.4的底部与悬臂3.2.5的顶端铰接;所述悬臂3.2.5下部固装有横档3.2.7,悬臂3.2.5的底端设有l形钩3.2.8;所述撑杆3.2.6的左端转动套装在左侧悬臂3.2.5的横档3.2.7上,设置在撑杆3.2.6右端的限位挡块3.2.9卡接在右侧悬臂3.2.5的横档3.2.8上;进一步的,所述坯料溜槽1.1.2的出口下方对应设有并排放置的合格坯料框1.3和头尾料框1.4;进一步的,所述屑料输送装置1.2.2的无轴螺旋输送叶片1.2.5用链板式输送带代替,链板式输送带的主传动轮与传动电机1.2.6通过变速箱传动连接;进一步的,所述第一引风机2.5和第二引风机2.6为轴流风机;所述主动链轮2.8通过变速箱与电机传动连接;进一步的,所述物料挡板3.1.3的下沿呈向入炉方向弯曲的曲面形状;进一步的,所述左侧悬臂的横档3.2.8上设有限制撑杆3.2.7沿横档3.2.8滑动的限位圈3.2.10;一种滚圈生产工艺,所述滚圈生产工艺是上述滚圈生产线实现的,其工艺步骤为:步骤一、下料:自动锯切下料系统1将圆钢101按设定的定尺长度进行锯切成坯料,锯切下来的坯料通过坯料溜槽1.1.2滑落至合格坯料框1.3;当光电传感器1.1.1监测到锯切圆钢头部或尾部时,分拣气缸1.1.3动作,推动坯料溜槽1.1.2以定位销1.1.4为中心发生转向,使坯料溜槽1.1.2的出料口方向对准头尾料框1.4,锯切下来的含圆钢头部或尾部的坯料进入头尾料框1.4;锯切时产生的屑料由屑料收集系统1.2进行收集,锯切屑料和切削液先进入屑料收集槽1.2.1,然后从屑料入口1.2.7进入屑料输送装置1.2.2,无轴螺旋输送叶片1.2.5将屑料输送至屑料出口1.2.8后进入屑料收集车1.2.3,切削液则经过滤网过滤后从壳体1.2.4底部的切屑液出口1.2.9回流至锯切机床的切削液储存槽实现循环使用;步骤二、加热:将锯切好的坯料送入加热炉加热;步骤三、冲压:将加热好的坯料送入冲压机锻压,然后在坯料心部位置冲出通孔而形成环形坯料;步骤四、碾环:碾环机将红热状态的环形坯料进一步碾压锻造成环形滚圈毛坯102;步骤五、冷却:经碾环后的高温环形滚圈毛坯102进入冷却炉2冷却,热电偶2.7监测到温度超出设定温度时,启动对应位置的第一引风机2.5或第二引风机2.6,第一引风机
2.5将冷风吹入送风管2.4,冷风从送风管2.4出口吹出,透过网带式输送带2.2流经环形滚圈毛坯102,带走热量使环形滚圈毛坯102降温后转变为热风,热风进入吸风罩2.3后排出车间;第二风机2.6将冷风直接吹至滚圈毛坯102使之降温;热电偶2.7监测到温度未超出设定值时,关闭对应位置的第一引风机2.5或第二引风机2.6,节约电能;步骤六、退火:将经冷却后的滚圈毛坯102堆放入料框3.3,人工抬起撑杆3.2.6的右端并向上推,使两个悬臂3.2.5分开,控制吊钩3.2.2下降,使两个悬臂3.2.5的l形钩3.2.8位于料框3.3上沿的下方,向右拉紧撑杆3.2.6使l形钩3.2.8夹紧并勾住料框3.3上沿,压下撑杆3.2.6右端,使撑杆3.2.6右端的限位挡块3.2.9卡住右侧悬臂的横档3.2.7,使两个悬臂3.2.5的l形钩3.2.8保持夹紧状态不向外侧松脱;控制吊钩3.2.2吊起料框3.3并将之放置于退火炉3入炉口辊道上,称重模块3.1.6对料框3.3料框重量进行检测,若超重则向声光报警装置3.1.7反馈超重报警信号,将料框3.3超重的滚圈毛坯102取出并符合重量限制要求后,辊道将料框3.3向后推进;在料框3.3经过横杆3.1.2时,物料挡板3.1.3受到料框3.3上沿或堆放位置高出料框3.3上沿的滚圈毛坯102推动而发生转动,滚圈毛坯102的位置越高,则横杆3.1.2转动的角度越大,横杆3.1.2带动信号触发板3.1.4转动,当信号触发板3.1.4碰到接近开关3.1.5的触发开关时,接近开关3.1.5向声光报警装置3.1.7反馈限高报警信号;当料框3.3的滚圈毛坯102同时满足限高限重要求后,辊道将料框3.3送入退火炉3退火;步骤七、精加工:经退火后的滚圈毛坯102由机加工员工在精加工车床上按图纸要求进行车削、开孔等操作;步骤八、清洗上油:经精加工后的滚圈进入自动清洗上油机清洗并上油,上油后即进行包装入库。
19.另外:需要注意的是,上述具体实施方式仅为本专利的一个优化方案,本领域的技术人员根据上述构思所做的任何改动或改进,均在本专利的保护范围之内。