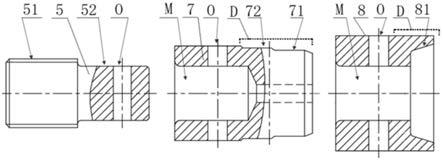
[0001]
本实用新型涉及管端成型机的辅助成型工模具结构改进技术,尤其是单工位端部成型机管端胀收口多工步加工模具组件。
背景技术:[0002]
管端成形机是在常态下对管件进行扩口、缩口及缩管的一种加工成形设备,它由集成的触控显示荧屏进行控制,适合管端复杂形状之加工。管端成形机被广泛用于管件接通、汽车油管、水管、空调管等连接部位的加工成形,是理想的管端成形加工设备。
[0003]
较为先进的的管端成形机具有三个工位,可自动换模,保证加工精度。手动自动任意选择,nc控制,中文显示,人机对话操作,并有自动计数功能。更换模具、缩管、扩口均可加工,同时配有倒角模,使加工倒角均可一次完成。使用不同的模具可实现对管件进行扩口、缩口、缩管、鼓包、墩筋,并可根据用户要求决定采用手动、点动或自动加工。其主要由油箱、车身、滑块、主油缸、限位油缸、压紧油缸、移位油缸、轴向定位油缸及轴向定位触铁等零件组成。通过在主油缸回路上设置管式节流阀,从而可以调节主油缸的工作速度;在压紧油缸回路上设置叠加式液控单向阀,可以保证模具夹紧过程中不松动;移位油缸、限位油缸、轴向定位油缸回路上均设置了叠加式双向节流阀,可调整上述油缸的双向运动速度。其中移位油缸和限位油缸配合使用转换工位,可使工位转换方便、精确,从而可以确保管件加工质量。
[0004]
通用的管端成型机即端部成型机通过水平油缸推动成型模对被夹紧模夹紧的钢管端部冷挤压成型。端部成型机有单工位和双工位两种。当管端的成型不能一次冷挤压实现时,就需要双工位或更多工位的端部成型机。
[0005]
现有单工位端部成型机实现多工步加工的方法有:
[0006]
1)按工步分批加工法:这方法采用钢管产品多次装夹,每装夹一次完成一个工步;2)按产品逐个成型法:钢管一次装夹,按工步依次更换成型模进行加工。
[0007]
如附图1所示,钢管1端部管端成型区12,需要两工位加工成型管端胀收口11,如附图2所示,现有的胀收口成型模具包括现有膨胀端口成型模41和现有膨胀收口成型模42,管端成型机上的推杆3端口上先后换装现有后端螺口结构的膨胀端口成型模41和现有膨胀收口成型模42,待加工的钢管1固定安装在夹模2中。
[0008]
现有技术以及模具缺陷在于:
[0009]
1)按工步采用分步加工法,钢管多次装夹,每装夹一次完成一个工步,加工精度差,钢管易变形,钢管表面压痕缺陷增加、加工效率低。
[0010]
2)按产品逐个成型法,钢管一次装夹,按工步依次更换成型模进行加工,成型模与推杆采用螺纹连接,且成型模较重,旋螺纹和搬动劳动强度大,更换时间长,加工效率低。
技术实现要素:[0011]
本实用新型的目的是提供单工位端部成型机管端胀收口多工步加工模具组件,利
用单工位端部成型机实现多工步端部成型加工。
[0012]
本实用新型的目的将通过以下技术措施来实现:包括芯轴、套筒胀管模和套筒收口模;芯轴、套筒胀管模和套筒收口模中轴线重合,芯轴后端有螺接端,芯轴前端有中心轴,套筒胀管模和套筒收口模后端中部轴向开内孔,中心轴与内孔间隙配合;套筒胀管模前段外壁有胀管区,套筒收口模前端面内凹有锥台槽形收口区,胀管区外径大于导向区的底部内径而小于导向区的口沿内径;中心轴与套筒胀管模和套筒收口模后端对应开有销孔,套筒胀管模或套筒收口模与芯轴通过销钉贯穿销孔连接定位。
[0013]
尤其是,销孔的中轴线不穿过销孔与芯轴、套筒胀管模和套筒收口模中轴线。销孔有一个至二个。
[0014]
尤其是,销孔的中轴线穿过销孔与芯轴、套筒胀管模和套筒收口模中轴线。
[0015]
尤其是,套筒胀管模前端环绕外壁边缘有锥台形导向区,导向区后段外径不大于胀管区外径。
[0016]
尤其是,在芯轴、套筒胀管模和套筒收口模中轴线方向上,收口区轴向深度小于胀管区轴向长度。
[0017]
尤其是,套筒胀管模前段中轴部开通孔并与套筒胀管模后段内孔连通。
[0018]
尤其是,套筒收口模后段内孔与收口区连通。
[0019]
尤其是,中心轴轴向长度不大于内孔轴向长度。
[0020]
本实用新型的优点和效果:在现有单工位的端部成型机上,采用产品逐个成型法,产品一次装夹、快速轻便更换成型模具,实现多工步加工,减少设备投入,提高加工效率和精度,减轻了操作工人的劳动强度。
附图说明
[0021]
图1为现有技术中钢管端部膨胀收口加工成型工序示意图。
[0022]
图2为本现有单工位端部成型机胀收口成型模具及加工示意图。
[0023]
图3为本实用新型实施例1中单工位端部成型模具及加工示意图。
[0024]
图4为本实用新型实施例1中单工位端部成型模具结构示意图。
[0025]
图5为本实用新型实施例1中单工位端部成型模具在推杆端安装结构示意图。
[0026]
图6为本实用新型实施例1中工作时芯轴和销钉旋转调整示意图。
[0027]
附图标记包括:
[0028]
1-钢管、11-管端胀收口、12-管端成型区、2-夹模、3-推杆、41-现有膨胀端口成型模、42-现有膨胀收口成型模、5-芯轴、51-螺接端、6-销钉、7-套筒胀管模、71-导向区、72-胀管区、8-套筒收口模、81-收口区、a-第一步胀口工序、b-第二部收口工序、o-销孔、m-内孔、d-模端成型区。
具体实施方式
[0029]
本实用新型原理在于,采用套筒快换结构,由芯轴5、销钉6和套筒成型模组成,其中套筒成型模包括套筒胀管模7和套筒收口模8。胀管和收口工序,由套筒胀管模7和套筒收口模8分两步成型依次完成。推杆3的行程长度控制钢管1端部的管端成型区12成型的效果,需要在相同的行程下两工步成型,避免调节行程,实现快速更换套筒成型模后连续加工。套
筒胀管模7和套筒收口模8前端加工有模端成型区d
[0030]
本实用新型包括:芯轴5、套筒胀管模7和套筒收口模8。
[0031]
下面结合附图和实施例对本实用新型作进一步说明。
[0032]
实施例1:如附图3至5所示,芯轴5、套筒胀管模7和套筒收口模8中轴线重合,芯轴5后端有螺接端51,芯轴5前端有中心轴52,套筒胀管模7和套筒收口模8后端中部轴向开内孔m,中心轴52与内孔m间隙配合;套筒胀管模7前段外壁有胀管区72,套筒收口模8前端面内凹有锥台槽形收口区81,胀管区72外径大于导向区71的底部内径而小于导向区71的口沿内径;中心轴52与套筒胀管模7和套筒收口模8后端对应开有销孔o,套筒胀管模7或套筒收口模8与芯轴5通过销钉6贯穿销孔o连接定位。
[0033]
前述中,销孔o的中轴线不穿过销孔o与芯轴5、套筒胀管模7和套筒收口模8中轴线。销孔o有一个至二个。
[0034]
前述中,销孔o的中轴线穿过销孔o与芯轴5、套筒胀管模7和套筒收口模8中轴线。
[0035]
前述中,套筒胀管模7前端环绕外壁边缘有锥台形导向区71,导向区71后段外径不大于胀管区72外径。
[0036]
前述中,在芯轴5、套筒胀管模7和套筒收口模8中轴线方向上,收口区81轴向深度小于胀管区72轴向长度。
[0037]
前述中,套筒胀管模7前段中轴部开通孔并与套筒胀管模7后段内孔m连通。
[0038]
前述中,套筒收口模8后段内孔m与收口区81连通。
[0039]
前述中,中心轴52轴向长度不大于内孔m轴向长度。
[0040]
本实用新型实施例中,套筒成型模采用中空结构,以免装拆时形成排气背压和真空,同时也显著减轻模具重量,方便操作;芯轴5通过螺纹与推杆3连接,实现套筒成型模的中心定位,起到连接、定位和导向的作用;套筒成型模根据端部成型的需要,可设计多个套筒成型模,套筒成型模与芯轴5间隙配合,起到轴向定位、承受压力和端部成型的作用;销钉6通过销孔将芯轴和套筒成型模连为一体,退模时,承受脱模拉力,与销孔1mm的间隙,方便操作并只在退模时承受很小的拉力,同时装模时,还可用于旋紧芯轴螺纹,因此起到旋紧,圆周限位、承受拉力的作用。
[0041]
本实用新型实施例中,芯轴5、套筒胀管模7和套筒收口模8有很好的强度、硬度和刚性,保证受力、耐磨和不变形。
[0042]
本实用新型实施例中,套筒成型模采用中空结构,保证工作时使空气流通,起到减轻重量、避免产生背压和真空的作用。
[0043]
本实用新型实施例中,芯轴5采用原有的推杆3相配合的螺纹连接,即芯轴5尾端有螺接端51,芯轴5前端上有中心轴52;中心轴52和套筒成型模尾部内孔m间隙配合,定位套筒成型模中心;芯轴5和套筒成型模上用销钉6限位套接固定连接。芯轴5可作为通用件,不同的端部成型只需设计不同规格或尺寸的前端结构的套筒成型模,芯轴5和套筒成型模上内孔m和销孔o尺寸通用,以上结构可实现快换和连续端部成型加工;芯轴5和套筒成型模结合面添加润滑油更方便快速的装拆;推杆3前端面是套筒成型模的轴向定位面,实现轴向定位,控制端部成型的轴向尺寸;芯轴5的中心轴52和套筒成型模的内孔m间隙配合,实现中心定位,控制端部成型与钢管的同轴度;管端成型区12成型时,套筒成型模将推力作用到推杆3前端面a上;脱模时,套筒成型模从钢管1端部拉出,拉力作用在销钉6和销孔o上,脱模时的
拉力小,销钉6可以承受。
[0044]
本实用新型实施例中,工作时操作过程包括:
[0045]
1)安装套筒成型模:将芯轴5后端的螺接端51旋入推杆3前端螺孔少许,将套筒成型模后端的内孔m套在芯轴5前端的中心轴52上,并且,将套筒成型模后端和中心轴52销孔o对齐,以销钉6穿过销孔o连接定位,利用调整销钉6收紧到位;这时,套筒胀管模7和套筒收口模8后端面与推杆3前端面接触紧密结合,成型时套筒成型模受推力作用,作用力作用到推杆3前端面上;适当旋紧或旋松芯轴5,使销钉6在如附图6至5所示箭头方向,该位置方向为操作方向,方便插拔,快速更换套筒成型模;
[0046]
2)调行程:调节推杆3行程,使每工步都能有效成型;
[0047]
3)装钢管1:将钢管1放在夹模2中,确认成型区长度,夹紧钢管1;
[0048]
4)第一步胀口工序a:推杆3动作,完成第一工步,更换套筒成型模;
[0049]
5)第二部收口工序b:推杆3动作,完成第二工步,更换套筒成型模;
[0050]
6)更换工件:松开钢管1,取下成品,换上下一个待加工产品。
[0051]
本实用新型实施例中,在现有单工位的端部成型机上,轴、孔间隙配合,快速装拆更换;各工步的成型模,设计时考虑推杆相同行程下时钢管端部成型;实现一次装夹,快速、连续多工步加工,减少设备投入,提高加工效率和精度,减轻操作工人的劳动强度。