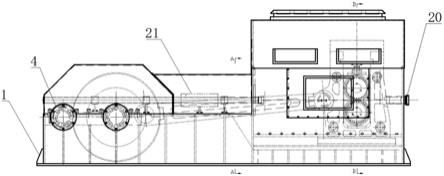
1.本实用新型属于金属无缝管材轧制技术领域,具体涉及一种高精密金属无缝管材周期轧制智能轧机。
背景技术:2.周期轧管机是带有送料机构的往复纵轧钢管轧机,是把毛管在轧制中各道次分阶段的变形工艺集中在同一个横截面连续变化的锥形轧槽中来完成。在轧辊与芯棒的共同作用下,由轧辊旋转来推动毛管发生塑性变形驱使金属发生流动,周期轧制过程存在毛管运动的方向与轧辊运动方向相反和相同两个过程,当轧辊转一周时,毛管通过轧管机孔型实现其锻轧、精轧等变形,当金属入口处全部经历锻轧、精轧等过程,毛管被轧制成荒管。在众多无缝钢管纵轧机中,周期轧管机是在一个孔型、单一道次中金属变形最为复杂且变形量最大的一种轧管机(管材延伸系数可达10以上),且产品精度高、性能提升极大。但由于周期轧管机的大变形过程和不同于其他轧管机的轧制特点,轧制的荒管有许多缺陷,有些缺陷是比较严重且难以克服的,传统的周期轧管机轧制的荒管缺陷主要包括:荒管的壁厚不均、竹节、轧破、擦伤等。此外,传统的周期轧管机,多是没有构成反馈控制和动态调节的轧管设备,生产效率低下,生产的管材质量差,设备维护困难等问题日益显著;而且,由于没有集成现代化的控制技术与检测手段,导致设备的智能化控制能力低下,设备自我保护能力不足、轧制过程稳定性差等缺点日益突出;因此发展一种智能化无缝管材周期轧制智能轧机设备迫在眉睫。
技术实现要素:3.本实用新型针对上述问题提供了本实用新型的目的是基于改进传统无缝管材周期轧制轧机的不足,将机械技术与自动控制技术有机结合,设计出一种能够有效控制产品精度的设备,从而,实现无缝管材轧制过程中根据毛管和荒管的尺寸参数、表面状态等数据自动监测与评估,获得高效率、智能化的无缝管材周期轧制智能轧机。
4.为达到上述目的本实用新型采用了以下技术方案:
5.一种高精密金属无缝管材周期轧制智能轧机,包括主机体和动力输入装置,所述动力输入装置通过联轴器与动力输入轴连接,所述动力输入轴安装在主机体左侧的一号轴承座内,在所述动力输入轴上设置有两个主动“人字形”齿轮,所述两个主动“人字形”齿轮分别啮合一个从动“人字形”大齿轮,所述从动“人字形”大齿轮安装在齿轮轴上,所述齿轮轴可转动的安装在主机体上,所述从动“人字形”大齿轮上通过曲柄销轴偏心连接有连杆,所述连杆的另一端与销轴连接,在所述销轴与连杆之间设置有滑动轴承,所述销轴安装在轧制中心的轧制机架上,所述轧制机架的底部设置在主机体上的滑槽内,在所述轧制机架上平行设置有上辊轴和下辊轴,所述上辊轴和下辊轴均通过两个二号轴承座安装在轧制机架上,且上辊轴和下辊轴所在平面垂直于主机体底面,在所述上辊轴和下辊轴的中部均安装有轧辊,在所述上辊轴的左端以及下辊轴的右端分别安装有表面硬化处理且经过精磨的
精密齿轮,在所述主机体的侧壁上固定安装有与精密齿轮啮合的精密齿条,在所述轧制机架的上部设置有两个伺服液压压下调整装置,两个伺服液压压下调整装置的活塞杆分别与上辊轴上的两个二号轴承座连接,以同步带动上辊轴上下移动,从而达到调整轧辊缝的目的,同时针对轧制过程中由于壁厚不均导致的小波幅振动进行微调实现小波幅抑振功能,在所述轧制机架的进料端与出料端分别设置有毛管检测装置和荒管检测装置,以检测毛管和荒管的直径以及表面状态信息,所述毛管检测装置和荒管检测装置均与控制台电性连接。
6.进一步,在所述连杆的中部设置有受力感应器,以检测连杆的受力状态,所述受力感应器与控制台电性连接,当感应器接收到超载的受力信号时,发出“停车”指令。
7.再进一步,在所述安装上辊轴的二号轴承座与安装下辊轴的二号轴承座之间设置有稳定阻尼,以检测轧机在轧制过程中的振动波幅,并将振动波幅信号发送至控制台,控制台根据接收到振动波幅信号对伺服液压压下调整装置发出控制指令,以维持上辊轴和下辊轴之间的辊缝恒定,实现抑振功能。
8.更进一步,所述毛管检测装置和荒管检测装置为红外线测径仪或激光测径仪。
9.更进一步,所述伺服液压压下调整装置包括缸体和活塞杆,所述活塞杆的一端设置在缸体内部,所述缸体为直接在轧制机架上掏孔形成,以增加缸体的刚度,满足伺服液压压下调整装置高精度频繁动作的需求,所述活塞杆的另一端与上辊轴上的两个二号轴承座通过球铰接的方式连接,以满足活塞杆与轴承座之间的小幅转动,避免刚性连接导致的卡死现象,提升伺服液压压下调整装置的使用寿命。
10.与现有技术相比本实用新型具有以下优点:
11.1、本实用新型通过设置毛管检测装置和荒管检测装置,来检测毛管和荒管的直径以及表面状态信息,并将检测到的信息传递至控制台,控制台根据毛管的直径信息,控制液压压下调整装置动态调整上辊轴以及下辊轴的轧制变形段的辊缝,控制台将荒管的直径信息与既定的成品荒管直径信息进行比对,并进行控制参数的补偿运算,同时转化为控制信号,传递给液压压下调整装置动态调整上辊轴以及下辊轴的精轧段和终轧段的辊缝,实现辊缝的自动调节;在控制台同时接收到毛管检测装置和荒管检测装置所发出的直径信息的时候,控制台优先根据荒管检测装置的直径信息进行辊缝的调节,控制台根据毛管和荒管的表面状态信息控制轧制变形段的冷却润滑液的流量,从而控制轧制变形段的润滑状态;
12.2、本实用新型在连杆的中部设置了受力感应器,并将受力感应器与控制台电性连接,从而通过控制台监测连杆的受力状态,如果出现受力超过允许值的状态,则控制台发出信号,产生“停车”动作,从而保护轧机部件;
13.3、本实用新型通过稳定阻尼检测轧机在轧制过程中的振动波幅,并将振动波幅信号发送至控制台,控制台根据接收到振动波幅信号对伺服液压压下调整装置发出控制指令,以维持上辊轴和下辊轴之间的辊缝恒定,实现抑振功能,当振动波幅超过辊缝的允许误差时,控制台同样发出信号,产生“停车”动作,实现管材超差预警,提示改进工艺;
14.4、本实用新型缸体为直接在轧制机架上掏孔形成,以增加缸体的刚度,满足伺服液压压下调整装置高精度频繁动作的需求。
附图说明
15.图1为本实用新型的主视图;
16.图2为本实用新型的俯视图;
17.图3为本实用新型图1中a
‑
a的剖视图;
18.图4为本实用新型图1中b
‑
b的剖视图;
19.图5为本实用新型图2中圈d的局部放大图;
20.图6为本实用新型图4中框e的局部放大图;
21.图中主机体—1、联轴器—2、动力输入轴—3、一号轴承座—4、主动“人字形”齿轮—5、从动“人字形”大齿轮—6、齿轮轴—7、曲柄销轴—8、连杆—9、销轴—10、滑动轴承—11、轧制机架—12、上辊轴—13、下辊轴—14、二号轴承座—15、轧辊—16、精密齿轮—17、精密齿条—18、液压压下调整装置—19、毛管检测装置—20、荒管检测装置—21、受力感应器—22、稳定阻尼—23、缸体—1901、活塞杆—1903。
具体实施方式
22.为了进一步阐述本实用新型的技术方案,下面通过实施例对本实用新型进行进一步说明。
23.如图1至图6所示,一种高精密金属无缝管材周期轧制智能轧机,包括主机体1和动力输入装置,所述动力输入装置通过联轴器2与动力输入轴3连接,所述动力输入轴3安装在主机体1左侧的一号轴承座4内,在所述动力输入轴3上设置有两个主动“人字形”齿轮5,所述两个主动“人字形”齿轮5分别啮合一个从动“人字形”大齿轮6,所述从动“人字形”大齿轮6安装在齿轮轴7上,所述齿轮轴7可转动的安装在主机体1上,所述从动“人字形”大齿轮6上通过曲柄销轴8偏心连接有连杆9,在所述连杆9的中部设置有受力感应器22,以检测连杆9的受力状态,所述受力感应器22与控制台电性连接,当感应器接收到超载的受力信号时,发出“停车”指令。所述连杆9的另一端与销轴10连接,在所述销轴10与连杆9之间设置有滑动轴承11,所述销轴10安装在轧制中心的轧制机架12上,所述轧制机架12的底部设置在主机体1上的滑槽内,在所述轧制机架12上平行设置有上辊轴13和下辊轴14,所述上辊轴13和下辊轴14均通过两个二号轴承座15安装在轧制机架12上,且上辊轴13和下辊轴14所在平面垂直于主机体1底面,在所述上辊轴13和下辊轴14的中部均安装有轧辊16,在所述上辊轴13的左端以及下辊轴14的右端分别安装有表面硬化处理且经过精磨的精密齿轮17,在所述主机体1的侧壁上固定安装有与精密齿轮17啮合的精密齿条18,在所述轧制机架12的上部设置有两个伺服液压压下调整装置19,所述伺服液压压下调整装置19包括缸体1901和活塞杆1903,所述活塞杆1903的一端设置在缸体1901内部,所述缸体1901为直接在轧制机架上掏孔形成,以增加缸体1901的刚度,满足伺服液压压下调整装置19高精度频繁动作的需求,所述活塞杆1903的另一端与上辊轴13上的两个二号轴承座15通过球铰接的方式连接,以满足活塞杆1903与轴承座15之间的小幅转动,避免刚性连接导致的卡死现象,提升伺服液压压下调整装置19的使用寿命。两个伺服液压压下调整装置19上的活塞杆1903分别与上辊轴13上的两个二号轴承座15连接,以同步带动上辊轴13上下移动,从而达到调整轧辊缝的目的,同时针对轧制过程中由于壁厚不均导致的小波幅振动进行微调实现小波幅抑振功能,在所述安装上辊轴13的二号轴承座15与安装下辊轴14的二号轴承座15之间设置有稳定阻尼23,
以检测轧机在轧制过程中的振动波幅,并将振动波幅信号发送至控制台,控制台根据接收到振动波幅信号对伺服液压压下调整装置19发出控制指令,以维持上辊轴13和下辊轴14之间的辊缝恒定,实现抑振功能。在所述轧制机架12的进料端与出料端分别设置有毛管检测装置20和荒管检测装置21,以检测毛管和荒管的直径以及表面状态信息,所述毛管检测装置20和荒管检测装置21均与控制台电性连接。所述毛管检测装置20和荒管检测装置21为红外线测径仪或激光测径仪。
24.工作过程:动力输入装置通过联轴器2带动动力输入轴3旋转,动力输入轴3上的主动“人字形”齿轮5带动从动“人字形”大齿轮6转动,在从动“人字形”大齿轮6偏心连接的连杆9随着从动“人字形”大齿轮6的转动而摆动,进而通过销轴10带动轧制机架12在主机体1上的滑槽内进行滑动,由于轧制机架12的滑动,上辊轴13和下辊轴14上的精密齿轮17在精密齿条18进行转动,从而将直线运动转变为旋转运动,上辊轴13和下辊轴14上的轧辊16随着精密齿轮17的旋转而进行旋转,最终完成对毛管的轧制运动。
25.在轧制机架12的进料端与出料端设置的毛管检测装置20和荒管检测装置21分别检测毛管和荒管的直径以及表面状态信息,并将检测到的信息传递至控制台,首先控制台根据毛管的直径信息,控制液压压下调整装置19动态调整上辊轴13以及下辊轴14的轧制变形段的辊缝,随后控制台接收到荒管检测装置21传递来的信息,控制台将接收到的荒管的直径信息与既定的成品荒管直径信息进行比对,并进行控制参数的补偿运算,同时转化为控制信号,传递给液压压下调整装置19动态调整上辊轴13以及下辊轴14的精轧段和终轧段的辊缝,实现辊缝的自动调节;在控制台同时接收到毛管检测装置和荒管检测装置所发出的直径信息的时候,控制台优先根据荒管检测装置的直径信息进行辊缝的调节,控制台根据毛管和荒管的表面状态信息控制轧制变形段的冷却润滑液的流量,从而控制轧制变形段的润滑状态,
26.在连杆9的中部设置的受力感应器22,将检测的信息发送至,从而通过控制台实时监测连杆的受力状态,如果出现受力超过允许值的状态,则控制台发出信号,产生“停车”动作,从而保护轧机部件;
27.稳定阻尼23检测轧机在轧制过程中的振动波幅,并将振动波幅信号发送至控制台,控制台根据接收到振动波幅信号对伺服液压压下调整装置19发出控制指令,以维持上辊轴13和下辊轴14之间的辊缝恒定,实现抑振功能,当振动波幅超过辊缝的允许误差时,控制台同样发出信号,产生“停车”动作,实现管材超差预警,提示改进工艺。
28.以上显示和描述了本实用新型的主要特征和优点,对于本领域技术人员而言,显然本实用新型不限于上述示范性实施例的细节,而且在不背离本实用新型的精神或基本特征的情况下,能够以其他的具体形式实现本实用新型。因此,无论从哪一点来看,均应将实施例看作是示范性的,而且是非限制性的,本实用新型的范围由所附权利要求而不是上述说明限定,因此旨在将落在权利要求的等同要件的含义和范围内的所有变化囊括在本实用新型内。
29.此外,应当理解,虽然本说明书按照实施方式加以描述,但并非每个实施方式仅包含一个独立的技术方案,说明书的这种叙述方式仅仅是为清楚起见,本领域技术人员应当将说明书作为一个整体,各实施例中的技术方案也可以经适当组合,形成本领域技术人员可以理解的其他实施方式。