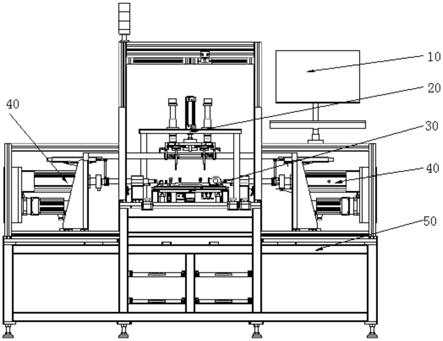
[0001]
本实用新型涉及铁道机车车辆基础制动装置检修技术领域,特别涉及一种闸片托衬套压装与过盈力检测装置。
背景技术:[0002]
本部分的描述仅提供与本实用新型公开相关的背景信息,而不构成现有技术。
[0003]
制动夹钳单元闸片托组成是制动夹钳单元的一个部件,如图1所示,闸片托组成1通过压装在其上的衬套2与纵向杆3构成铰链连接。制动夹钳的制动力通过制动杠杆4传递至闸片托34,最后作用在制动盘上。闸片托34和衬套2采用过盈连接方式,过盈连接摩擦力的大小与衬套2与闸片托34孔轴配合尺寸公差、材料、表面粗糙度、是否有润滑等许多因素都有关。因此需要在压装衬套2时设置合理的压装力。后续,闸片托34进入检修时,还需要对其过盈连接摩擦力进行检测,以保证过盈配合连接强度,确保制动夹钳单元闸片托组成1在其全寿命周期内能够安全可靠。
[0004]
目前闸片托34、衬套2的压装通过液压驱动的双向压力杆配合定位工装台面实现,其在使用时存在工件易发生变形、压装检测效率低、压装检测精度低等问题,具体问题描述如下。如图2所示,闸片托34包括整体沿着第一方向纵长延伸的本体,所述本体上在沿着所述第一方向间隔设置有多个凸耳,每个凸耳上设置有一个安装孔,所述安装孔包括相对的内侧孔和外侧孔。一般的,该凸耳的个数为四个,相应的,设置在该凸耳安装孔上的衬套2的个数也为四个。其中,该四个衬套2设置在用于和纵向杆3配合的侧面上。对于和纵向杆3相配合的侧面,为了保证后续其与纵向杆3的安装配合要求,其需要保证安装衬套2后凸出量或凹陷量不大于预设值,例如0.2毫米。
[0005]
目前,闸片托34上的四个衬套2均采用单侧压装的方式,压装外侧两个衬套2时,由于存在较大弯矩,如果定位不牢靠,闸片托34整体容易产生变形,影响产品质量。另外,采用单侧压装,完成4个衬套2的压装或检测需要液压缸带动压力轴杆走两个往复行程,压装效率偏低。
技术实现要素:[0006]
为了克服现有技术中的至少一个缺陷,本实用新型提供一种闸片托衬套压装与过盈力检测装置。
[0007]
本实用新型的上述目的可采用下列技术方案来实现:
[0008]
一种闸片托衬套压装装置,所述闸片托包括整体纵长延伸的本体,所述本体上沿着纵长延伸方向间隔设置有多个凸耳,每个凸耳上设置有一个安装孔,所述装置包括:机架,设置在所述机架上的随动止挡机构、闸片托上料机构、动力机构以及与所述随动止挡机构、所述闸片托上料机构和所述动力机构电性连通的工控机;所述闸片托上料机构包括:用于安装闸片托的托盘,所述托盘上设置有用于对所述闸片托进行定位的限位部;所述动力机构包括:拉压轴杆,输出端与所述拉压轴杆连接并带动所述拉压轴杆往复移动的动力输
出单元,所述拉压轴杆的外径小于所述安装孔的孔径;所述拉压轴杆背离所述动力输出单元的一端形成有限位槽;所述随动止挡机构包括:止挡件和用于改变所述止挡件位置的驱动机构,所述止挡件的一端设置有与所述限位槽相配合的卡合部,所述卡合部沿着厚度方向具有相对的第一表面和第二表面,当所述拉压轴杆沿着第一方向移动时,带动与所述拉压轴杆配合的所述止挡件移动,所述第一表面压装位于内侧凸耳的衬套;当所述拉压轴杆沿着与所述第一方向相反的第二方向移动时,带动与所述拉压轴杆配合的所述止挡件移动,所述第二表面压装位于外侧凸耳的衬套。
[0009]
在一个优选的实施方式中,所述闸片托上料机构还包括:第一动力源和滑动导轨,所述托盘能在所述滑动导轨上移动,启动所述第一动力源后,所述托盘能带动闸片托由装夹所述闸片托的第一工位,移动至压装所述闸片托衬套的第二工位。
[0010]
在一个优选的实施方式中,所述上料机构还包括:与所述第一工位对应设置的第一限位件、与所述第二工位对应设置的第二限位件。
[0011]
在一个优选的实施方式中,所述动力机构还包括:支撑件,所述支撑件设置有用于穿设所述拉压轴杆的开孔,所述支撑件的底面能抵靠在所述托盘的上表面。
[0012]
在一个优选的实施方式中,所述动力输出单元包括电动缸。
[0013]
在一个优选的实施方式中,所述装置还包括:用于检测作用在衬套上的压力或拉力的拉压力传感器、用于检测所述拉压轴杆位移量的位移传感器。
[0014]
在一个优选的实施方式中,所述随动止挡机构还包括:用于安装所述驱动机构的支架,所述支架上还设置有第一导向光轴,所述第一导向光轴和所述驱动机构的输出端均与用于安装所述止挡件的安装架相连接,启动所述驱动机构后,所述止挡件能沿着第一方向移动。
[0015]
在一个优选的实施方式中,所述支架包括主板和位于所述主板两端的侧板,所述主板具有相对的上表面和下表面,所述上表面与所述第一导向光轴和所述驱动机构的输出端相连接,所述下表面设置有滑轨,所述止挡件背离所述卡合部的一端与所述滑轨滑动配合。
[0016]
在一个优选的实施方式中,所述止挡件上设置有导向孔,所述随动止挡机构还包括安装在所述侧板上的第二导向光轴,所述止挡件通过所述导向孔套设在所述第二导向光轴上,所述第二导向光轴的延伸方向与所述滑轨的延伸方向相同。
[0017]
在一个优选的实施方式中,所述侧板与所述止挡件之间的第二导向光轴上还套设有第一弹性件,所述第一弹性件的一端与所述侧板相抵靠,另一端与所述止挡件相抵靠,所述止挡件背离所述第一弹性件的一侧还设置有第二弹性件。
[0018]
一种闸片托衬套过盈力检测装置,所述闸片托包括整体纵长延伸的本体,所述本体上沿着纵长延伸方向间隔设置有多个凸耳,每个凸耳上设置有一个安装孔,所述装置包括:机架,设置在所述机架上的随动止挡机构、闸片托上料机构、动力机构以及与所述随动止挡机构、所述闸片托上料机构和所述动力机构电性连通的工控机;所述闸片托上料机构包括:用于安装闸片托的托盘,所述托盘上设置有用于对所述闸片托进行定位的限位部;所述动力机构包括:拉压轴杆,输出端与所述拉压轴杆连接并带动所述拉压轴杆往复移动的电动缸,所述拉压轴杆的外径小于所述安装孔的孔径;所述拉压轴杆背离所述电动缸的一端形成有限位槽;所述随动止挡机构包括:止挡件和用于改变所述止挡件位置的驱动机构,
所述止挡件的一端设置有与所述限位槽相配合的卡合部,所述卡合部沿着厚度方向具有相对的第一表面和第二表面,当所述拉压轴杆沿着第一方向移动时,带动与所述拉压轴杆配合的所述止挡件移动,所述第一表面压装位于内侧凸耳的衬套;当所述拉压轴杆沿着与所述第一方向相反的第二方向移动时,带动与所述拉压轴杆配合的所述止挡件移动,所述第二表面压装位于外侧凸耳的衬套;拉压力传感器,用于检测作用在衬套上的压力或拉力;位移传感器,用于检测所述拉压轴杆位移量。
[0019]
有益效果:
[0020]
本申请实施方式中所提供的闸片托衬套压装装置、闸片托衬套过盈力检测装置实现了闸片托衬套的自动压装以及过盈连接强度(过盈力)的自动检测,其压装过程效率更高,检测结果更加准确可靠,其具有如下优势:
[0021]
(1)通过采用拉压结合的结构和作业方式,不仅有效减小了工件在压装过程中的变形量,提高了产品质量,同时减少了拉压轴杆往复行程次数,将作业效率至少提升了30%。
[0022]
(2)采用电动缸替代液压驱动系统,提升了输出压力的控制精度,并实现了压力轴动作速度的精确控制,在避免压力头对衬套产生瞬间冲击的同时又不影响作业效率,大幅度提高了衬套过盈力检测的准确性。
[0023]
(3)通过使用位移传感器对衬套与闸片托相对位移进行采集,实现了过盈力的自动检测和判定,提高了检测准确性和检测效率。
[0024]
(4)系统通过将各个机构与工控机电性连接可实现一键件操作,将闸片托固定在托盘上后,选择对应程序,系统可自动完成衬套压装或过盈力检测工作,并自动记录检测结果。
附图说明
[0025]
下面结合附图和实施方式对本实用新型对进一步说明。
[0026]
图1中提供的一种闸片托组成及相关部件的结构示意图;
[0027]
图2中提供了一种闸片托的结构示意图;
[0028]
图3为本申请实施方式中提供一种闸片托衬套压装装置的结构示意图;
[0029]
图4为图3中一种闸片托上料机构的结构示意图;
[0030]
图5为图3中一种动力机构的结构示意图;
[0031]
图6为图3中一种随动止挡机构的主视图;
[0032]
图7为图3中一种随动止挡机构的侧视图;
[0033]
图8为拉压轴杆、止挡件相配合进行压装衬套时的局部结构示意图;
[0034]
图9为图8中的a-a剖视图;
[0035]
图10为本申请实施方式中提供的一种闸片托衬套压装方法的步骤流程图;
[0036]
图11为本申请实施方式中提供的一种闸片托衬套过盈力检测方法的步骤流程图。
[0037]
附图标记说明:
[0038]
1、闸片托组成;111、外侧凸耳;112、内侧凸耳;
[0039]
2、衬套;
[0040]
3、纵向杆;
[0041]
4、制动杠杆;
[0042]
10、工控机;
[0043]
20、随动止挡机构;21、驱动机构;22、第一导向光轴;23、滑轨;24、第二弹性件;25、第二导向光轴;26、止挡件;260、卡合部;261、导向孔;27、第一弹性件;28、支架;281、主板;282、侧板;29、外安装架;
[0044]
30、闸片托上料机构;31、第一动力源;32、第一限位件;33、托盘;34、闸片托;35、第二限位件;36、滑动导轨;
[0045]
40、动力机构;41、支撑件;42、拉压轴杆;420、限位槽;43、拉压力传感器;44、位移传感器;45、动力输出单元;
[0046]
50、机架;y、预压装位置。
具体实施方式
[0047]
下面将结合附图和具体实施例,对本实用新型的技术方案作详细说明,应理解这些实施例仅用于说明本实用新型而不用于限制本实用新型的范围,在阅读了本实用新型之后,本领域技术人员对本实用新型的各种等价形式的修改均落入本申请所附权利要求所限定的范围内。
[0048]
需要说明的是,当元件被称为“设置于”另一个元件,它可以直接在另一个元件上或者也可以存在居中的元件。当一个元件被认为是“连接”另一个元件,它可以是直接连接到另一个元件或者可能同时存在居中元件。本文所使用的术语“垂直的”、“水平的”、“上”、“下”、“左”、“右”以及类似的表述只是为了说明的目的,并不表示是唯一的实施方式。
[0049]
除非另有定义,本文所使用的所有的技术和科学术语与属于本申请的技术领域的技术人员通常理解的含义相同。本文中在本申请的说明书中所使用的术语只是为了描述具体的实施方式的目的,不是旨在于限制本申请。本文所使用的术语“和/或”包括一个或多个相关的所列项目的任意的和所有的组合。
[0050]
请参阅图2所示,为一种典型的闸片托结构,该闸片托34包括整体纵长延伸的本体,所述本体上沿着纵长延伸方向间隔设置有多个凸耳。每个凸耳上设置有一个安装孔。例如,该凸耳的个数为4个。其中,两个凸耳位于外侧,为外侧凸耳111,两个凸耳位于内侧,为内侧凸耳112。相邻的一个外侧凸耳111和一个内侧凸耳112相配合形成一个用于与纵向杆3铰接的安装副。针对每个设置有安装孔的凸耳,均需要设置一个衬套2。也就是说,闸片托34上有四个同轴的衬套2需要装配。由于外侧两个衬套2距离远,压装时容易产生大弯矩,导致闸片托34产生变形问题,同时往复次数多,压装效率不高。
[0051]
申请人发现,针对不同位置的衬套2,通过改进压装装置和压装方式,针对外侧两个衬套2,采用拉装,从内侧向外拉,针对内侧两个衬套2,沿用压装,整体上不仅能够较佳地改善受力情况同时能够大大提高压装效率。
[0052]
请综合参阅图3至图9,本申请说明书实施方式中提供了一种闸片托衬套压装装置。应用该闸片托衬套压装装置可以直接或者改进后进行闸片托34衬套2过盈力检测。
[0053]
该闸片托衬套压装装置可以包括:所述装置包括:机架50,设置在所述机架50上的随动止挡机构20、闸片托上料机构30、动力机构40以及与所述随动止挡机构20、所述闸片托上料机构30和所述动力机构40电性连通的工控机10。
[0054]
如图4所示,为闸片托上料机构30的结构示意图,该闸片托上料机构30可以包括:用于安装闸片托34的托盘33,所述托盘33上设置有用于对所述闸片托34进行定位的限位部。
[0055]
在本实施方式中,将闸片托34放置在托盘33上,托盘33结构可以确保闸片托34在水平、前后方向具有良好的定位精度。具体的,该托盘33具有呈板状的本体,其本体上设置有多个用于对所述闸片托34进行定位的限位部。具体的,该限位部可以为预定形状的凹槽或开孔的形式。该限位部的分布位置和个数可以依据该托盘33的具体构造而进行设定,本申请在此并不作唯一的限定。例如,该限位部可以为在该本体上设置的四个开口槽,该开口槽能与托盘33下表面的凸起相卡合。相应的,该开口槽的分布位置可以根据该托盘33下表面的凸起进行设定。
[0056]
进一步的,为了提高压装时上料操作的便捷性、安全性,所述闸片托上料机构30还可以包括:动力源31和滑动导轨36。所述托盘33能在所述滑动导轨36上移动。启动所述动力源31后,所述托盘33能带动闸片托34由装夹所述闸片托34的第一工位(即上料位置),移动至压装所述闸片托34衬套2的第二工位(即压装位置)。其中,该动力源31可以为气缸的形式,在本实施方式中,以气缸为例,进行举例说明。当然,该动力源31的形式并不限于上述举例,本申请在此并不作具体的限定。
[0057]
通过设置能够推动闸片托上料机构30在滑动导轨36中移动的气缸,以及配套的滑动轨道,使用时,动力源31通过滑动导轨36带动托盘33到达压装位置,并在作业结束后自动返回闸片托34上料位置,实现了闸片托34上料和压装两个工位的不同切换,相对于在同一位置进行上料和压装而言,该结构能够保证上料时不会与压装设备进行干涉,从而提高了上料操作的便捷性、安全性。
[0058]
此外,为了保证该闸片托上料机构30在进行工位切换时定位的准确性,所述上料机构还可以包括:与所述第一工位对应设置的第一限位件32、与所述第二工位对应设置的第二限位件35。
[0059]
如图5所示,在本实施方式中,所述动力机构40可以包括:拉压轴杆42,输出端与所述拉压轴杆42连接并带动所述拉压轴杆42往复移动的动力输出单元45。所述拉压轴杆42的外径小于所述安装孔的孔径。所述拉压轴杆42背离所述动力输出单元45的一端形成有限位槽420。使用时,该拉压轴杆42的限位槽420与随动止挡机构20相配合,在动力输出单元45的驱动下,穿过外侧凸耳111的安装孔,分别对内侧凸耳112施加压力的方式进行压装衬套2或对外侧凸耳111施加拉力的方式进行压装衬套2。
[0060]
在本实施方式中,该动力机构40可以包括两个,分别为第一动力机构40和第二动力机构40。该第一动力机构40和第二动力机构40对称地设置在机架50上。其中,以图5中所示为例,左侧的第一动力机构40用于对位于闸片托34左侧的外侧凸耳111和内侧凸耳112进行压装衬套2,该右侧的第二动力机构40用于的闸片托34右侧的外侧凸耳111和内侧凸耳112进行压装衬套2。
[0061]
由于该拉压轴杆42为悬臂轴,为了保证该拉压轴杆42在压合衬套2时的刚度,所述动力机构40还可以包括:支撑件41,所述支撑件41设置有用于穿设所述拉压轴杆42的开孔,所述支撑件41的底面能抵靠在所述托盘33的上表面。
[0062]
具体的,该支撑件41可以悬挂在该拉压轴杆42上,当需要进行压装作业时,该支撑
件41随着拉压轴杆42一起伸出,从而降低了该拉压轴杆42与开孔对准的难度,能够保证该支撑件41的开孔与拉压轴杆42高精度配合,进而保证该拉压轴杆42在压装时的位置精度。
[0063]
在本实施方式中,该动力输出单元45可以为电动缸的形式。电动缸作为动力输出单元45,带动前端的拉压轴杆42水平往复动作,实现衬套2的压装和过盈力检测。
[0064]
所述闸片托衬套压装装置还可以包括:用于检测作用在衬套2上的压力或拉力的拉压力传感器43、用于检测所述拉压轴杆42位移量的位移传感器44。其中,该位移传感器44可以为光栅式位移传感器,当然,该位移传感器44还可以为其他形式的传感器,本申请在此并不作具体的限定,本说明书中,以光栅式位移传感器为例进行举例说明。使用时,拉压力传感器43和光栅式位移传感器实时采集压装力和压力轴杆的位移量,作为压力控制和过盈力检测的依据。
[0065]
整体上,该闸片托衬套压装装置使用两个电动缸作为驱动力部件,两个电动缸对向安装,并保证动力压力轴输出轴具有较高的同轴度。在两侧拉压轴杆42上分别安装有高精度拉压传感器和光栅式位移传感器,实现了压装力以及闸片托34相对衬套2的位移量的测量。
[0066]
需要说明的是:传统的动力输出单元45一般为液压系统。液压系统的速度控制大多采用节流阀,阀和液压介质本身的特性造成速度控制有延时,且无法实现精确的位置控制。过盈力检测时,最主要的干扰因素就是瞬时冲击力,所以在拉压轴杆42和随动止挡机构20靠近工件时速度要控制在低速,同时出于检测效率的考虑,要尽量提升拉压轴杆42在不接触工件时的移动速度。本实施方式中,采用电动缸替代了传动的液压系统,利用电动缸的伺服特性能够较好的兼顾以上两点要求。
[0067]
请结合参阅图6和图7,在本实施方式中,随动止挡机构20主要包括:止挡件26、用于改变所述止挡件26位置的驱动机构21。
[0068]
所述止挡件26的一端设置有与所述限位槽420相配合的卡合部260。所述卡合部260沿着厚度方向具有相对的第一表面和第二表面。当所述拉压轴杆42沿着第一方向移动时,带动与所述拉压轴杆42配合的所述止挡件26移动,所述第一表面压装位于内侧凸耳112的衬套2;当所述拉压轴杆42沿着与所述第一方向相反的第二方向移动时,带动与所述拉压轴杆42配合的所述止挡件26移动,所述第二表面压装位于外侧凸耳111的衬套2。
[0069]
具体的,该驱动机构21可以为气缸的形式,用于带动止挡件26沿着水平方向移动,当然,该驱动机构21的具体形式并不限于上述举例,本申请在此并不作唯一的限定。在一些实施方式中,该驱动机构21还可以带动止挡件26沿着水平方向、竖直方向进行移动。
[0070]
当该驱动机构21用于带动止挡件26沿着竖直方向移动时,该止挡件26的初始位置在水平方向的投影位于相邻的内侧凸耳112和外侧凸耳111之间。当该止挡件26在驱动机构21的驱动下向下移动时,可以卡入内侧凸耳112和外侧凸耳111之间的预压装位置y,以便后续与拉压轴杆42配合,进行衬套2的压装或过盈力的检测。当该驱动机构21能够带动止挡件26沿着水平方向和竖直方向进行移动时,该止挡件26的初始位置没有限制,可以根据实际的需要进行设置。
[0071]
在一个实施方式中,为了保证该止挡件26沿着第一方向移动的平稳性和定位的准确性,所述随动止挡机构20还可以包括:用于安装所述驱动机构21的支架28,所述支架28上还设置有第一导向光轴22,所述第一导向光轴22和所述驱动机构21的输出端均与用于安装
所述止挡件26的安装架相连接,启动所述驱动机构21后,所述止挡件26能沿着第一方向移动。该第一方向可以为竖直方向,当然,该第一方向也可以为垂直于所述拉压轴杆42移动方向的其他方向,本申请在此并不作唯一的限定。
[0072]
在本实施方式中,该第一方向主要以竖直方向为例进行举例说明。其中,该第一导向光轴22的根数可以为两根,两根第一导向光轴22可以对称设置在气缸的两侧,形成垂直方向的双导向机构,从而确保该随动止挡机构20动作的稳定性和位置精度。
[0073]
进一步的,所述支架28包括主板281和位于所述主板281两端的侧板282。所述主板281具有相对的上表面和下表面。所述上表面与所述第一导向光轴22和所述驱动机构21的输出端相连接,所述下表面设置有滑轨23,所述止挡件26背离所述卡合部260的一端与所述滑轨23滑动配合。
[0074]
在本实施方式中,该随动止挡机构20可以整体通过外安装架29固定。该随动止挡机构20还设置有用于安装各个部件的支架28。该第一导向光轴22和驱动机构21的输出端穿过外安装架29与该支架28相固定,能够带动该支架28以及安装在该支架28上的部件沿着竖直方向同步移动。具体的,该支架28的下表面设置有滑轨23,该止挡件26背离所述卡合部260的一端(即上端)设置有与滑轨23相配合的滑块,当该止挡件26受到作业力时,能够沿着该滑轨23的延伸方向移动。
[0075]
此外,为了进一步保证该随动止挡机构20中止挡件26动作的稳定性和位置精度,所述止挡件26上设置有导向孔261。所述随动止挡机构20还包括安装在所述侧板282上的第二导向光轴25。所述止挡件26通过所述导向孔261套设在所述第二导向光轴25上。所述第二导向光轴25的延伸方向与所述滑轨23的延伸方向相同。整体上,该第二导向光轴25与该滑轨23在水平方向形成双导向机构,改善了随动止挡机构20的受力情况,提升了随动止挡机构20的可靠性和稳定性。
[0076]
为了保证该止挡件26在于拉压轴杆42配合实现对衬套2的压装后能自动复位,所述侧板282与所述止挡件26之间的第二导向光轴25上还套设有第一弹性件27,所述第一弹性件27的一端与所述侧板282相抵靠,另一端与所述止挡件26相抵靠,所述止挡件26背离所述第一弹性件27的一侧还设置有第二弹性件24。具体的,该第一弹性件27可以为弹簧。该第二弹性件24可以为弹性限位挡块。弹性限位挡块里面设置有弹簧,该弹簧的弹簧力比另一侧的弹簧大得多,在自由状态下,该弹性限位挡块处于固定位置,这个固定位置正好可以保证止挡件26对应拉压轴杆42的限位槽420。整体上,该第一弹性件27和第二弹性件24形成对止挡件26的双向柔性定位结构,一方面能够保证止挡件26随着拉压轴杆42水平双向移动,另一方面在压装动作结束后自动回到起始位置。
[0077]
具体使用时,闸片托34通过闸片托上料机构30由上料位置到达工作位置后,气缸将随动止挡机构20推送至止挡位置,弹性限位挡块确保止挡件26插入到拉压轴杆42的限位槽420内。在衬套2压装和过盈力检测过程中,衬套2止挡随着拉压轴杆42延水平方向往复动作起到止挡作用。
[0078]
本申请实施方式中,还提供一种闸片托衬套过盈力检测装置,该闸片托衬套过盈力检测装置可以包括:机架50,设置在所述机架50上的随动止挡机构20、闸片托上料机构30、动力机构40以及与所述随动止挡机构20、所述闸片托上料机构30和所述动力机构40电性连通的工控机10;所述闸片托上料机构30包括:用于安装闸片托34的托盘33,所述托盘33
上设置有用于对所述闸片托34进行定位的限位部;所述动力机构40包括:拉压轴杆42,输出端与所述拉压轴杆42连接并带动所述拉压轴杆42往复移动的电动缸,所述拉压轴杆42的外径小于所述安装孔的孔径;所述拉压轴杆42背离所述电动缸的一端形成有限位槽420;所述随动止挡机构20包括:止挡件26和用于改变所述止挡件26位置的驱动机构21,所述止挡件26的一端设置有与所述限位槽420相配合的卡合部260,所述卡合部260沿着厚度方向具有相对的第一表面和第二表面,当所述拉压轴杆42沿着第一方向移动时,带动与所述拉压轴杆42配合的所述止挡件26移动,所述第一表面压装位于内侧凸耳112的衬套2;当所述拉压轴杆42沿着与所述第一方向相反的第二方向移动时,带动与所述拉压轴杆42配合的所述止挡件26移动,所述第二表面压装位于外侧凸耳111的衬套2;拉压力传感器43,用于检测作用在衬套2上的压力或拉力;位移传感器44,用于检测所述拉压轴杆42位移量。
[0079]
本实施方式中,所提供的闸片托衬套过盈力检测装置与上述实施方式中所提供的闸片托衬套压装装置主要区别在于两者应用的具体场景不同。对于闸片托衬套压装装置而言,其主要应用在生产过程中,闸片托34的衬套2压装;而对于闸片托衬套过盈力检测装置其主要用于对使用一段时间后的闸片托34衬套2的过盈力检测,属于后续检修阶段。
[0080]
此外,在具体的组成、结构等方面,该闸片托衬套过盈力检测装置对动力输出单元45的要求比较高,为了实现输出压力的控制精度,并实现压力轴动作速度的精确控制,在避免压力头对衬套2产生瞬间冲击的同时又不影响作业效率,大幅度提高衬套2过盈力检测的准确性的技术效果,该动力输出单元45选用电动缸替代液压驱动系统。此外,为了实现过盈力的自动检测,该检测装置设置有拉压力传感器43、位移传感器44。
[0081]
整体上,其他部分,例如:随动止挡机构20、闸片托上料机构30、动力机构40以及工控机10等可以参照上述闸片托衬套压装装置的具体描述,本申请在此不再展开描述。
[0082]
请结合参阅图9和图10,以该闸片托衬套压装装置进行衬套2压装为例,首先可以先拉装外侧衬套2,该拉压轴杆42先自起始位置移动至位于内侧凸耳112和外侧凸耳111中间的预压装位置y,然后由该预压装位置y向靠近外侧的外侧凸耳111移动预定距离,实现将外侧衬套2压装(此时该拉压轴杆42受到的是拉力);在接着该拉压轴杆42回到预压装位置y,以便于进行压装内侧衬套2。在压装内侧衬套2时,该拉压轴杆42向内侧凸耳112移动预定距离,实现将内侧衬套2压装(此时该拉压轴杆42受到的是压力)。实现内侧衬套2压装后,该拉压轴杆42返回起始位置。在本实施方式中,可在闸片托34的两侧分别设置对称的拉压轴杆42,从而同步实现该闸片托34两侧的内外衬套2的压装。相对于现有的压装过程拉压轴杆42需要往复移动两个行程,本申请的压装过程仅需要移动一个行程。
[0083]
需要说明的是,利用该闸片托衬套压装装置进行衬套2压装时,也可以先压装内侧的内侧衬套2,在压装外侧的外侧衬套2,其操作过程可以类比参照上述描述,本申请在此并不作具体的限定。
[0084]
本实用新型所提供的闸片托衬套压装装置、闸片托衬套过盈力检测装置实现了闸片托34衬套2的自动压装以及过盈连接强度(过盈力)的自动检测,其压装过程效率更高,检测结果更加准确可靠,其具有如下优势:
[0085]
(1)通过采用拉压结合的结构和作业方式,不仅有效减小了工件在压装过程中的变形量,提高了产品质量,同时减少了拉压轴杆42往复行程次数,将作业效率至少提升了30%。
[0086]
(2)采用电动缸替代液压驱动系统,提升了输出压力的控制精度,并实现了压力轴动作速度的精确控制,在避免压力头对衬套2产生瞬间冲击的同时又不影响作业效率,大幅度提高了衬套2过盈力检测的准确性。
[0087]
(3)通过使用位移传感器44对衬套2与闸片托34相对位移进行采集,实现了过盈力的自动检测和判定,提高了检测准确性和检测效率。
[0088]
(4)系统通过将各个机构与工控机10电性连接可实现一键件操作,将闸片托34固定在托盘33上后,选择对应程序,系统可自动完成衬套2压装或过盈力检测工作,并自动记录检测结果。
[0089]
请参阅图10,本申请实施方式中提供的一种闸片托衬套压装方法,该方法可以包括如下步骤:
[0090]
步骤s10:打开工控机10,将闸片托34装夹至闸片托上料机构30,并将装有闸片托34的闸片托上料机构30放置于预定的压装位置;
[0091]
步骤s12:利用动力输出单元45带动拉压轴杆42移动到预压装位置y,驱动机构21带动随动止挡机构20中的止挡件26移动到工作位置,止挡件26的卡合部260卡入拉压轴杆42的限位槽420中;
[0092]
步骤s14:将衬套2安装在拉压轴杆上,利用动力驱动单元给所述拉压轴杆42施加压力或拉力,将衬套压装在内侧凸耳112或外侧凸耳111上,进行内侧衬套2或外侧衬套2的压装;
[0093]
步骤s16:一侧衬套2压装结束后,拉压轴杆42回到预压装位置y;将衬套2安装在拉压轴杆靠近另一侧凸耳的位置,驱动机构21带动止挡件26移动到工作位置,利用动力驱动单元给所述拉压轴杆42施加拉力或压力,进行外侧衬套2或内侧衬套2的压装,各机构复位。
[0094]
在本实施方式中,主要利用上述实施方式所提供的闸片托衬套压装装置采用不同的方式进行压装,其中,对于内侧衬套2而言,通过施加给拉压轴杆42压力后,该拉压轴杆42将压力传递给随动止挡机构20的止挡件26,由该止挡件26将压力传递给内侧衬套2,从而实现压装;对于外侧衬套2而言,通过施加给拉压轴杆42拉力后,该拉压轴杆42将压力传递给随动止挡机构20的止挡件26,由该止挡件26将压力传递给内侧衬套2,从而实现压装。
[0095]
其中,在压装时,可以先压装内侧衬套2,也可以先压装外侧衬套2,本申请在此并不作具体的限定。
[0096]
利用该闸片托衬套压装装置的闸片托衬套压装方法能够实现上述闸片托衬套压装装置所实现的技术效果,具体可以参照上述实施方式的具体描述,本申请在此不再展开赘述。
[0097]
在一个实施方式中,针对设置有位移传感器44的闸片托衬套压装装置,其在压装过程中,当工控机10通过该位移传感器44接收到该拉压轴杆42的移动距离达到预设距离时,该工控机10可以控制动力驱动单元停止工作,从而使得拉压轴杆42不再进一步移动,进而保证衬套2达到理想的压装效果。
[0098]
请参阅图11,本申请实施方式中基于上述闸片托衬套过盈力检测装置,提出一种闸片托34衬套2过盈力检测方法,该方法可以包括如下步骤:
[0099]
步骤s11:打开工控机10,将闸片托34装夹至闸片托上料机构30,并将装有闸片托34的闸片托上料机构30放置于预定的压装位置;
[0100]
步骤s13:利用电动缸带动拉压轴杆42移动到预压装位置y,驱动机构21带动随动止挡机构20中的止挡件26移动到工作位置,止挡件26的卡合部260卡入拉压轴杆42的限位槽420中;
[0101]
步骤s15:利用电动缸给所述拉压轴杆42施加压力或拉力,利用拉压力传感器43进行内侧衬套2或外侧衬套2的过盈力检测;
[0102]
步骤s17:基于所述位移传感器44的检测结果判定过盈连接强度是否合格;当判断结果为合格时,拉压轴杆42回到预压装位置y;驱动机构21带动随动止挡机构20中的止挡件26移动到工作位置,利用电动缸给所述拉压轴杆42施加拉力或压力,进行外侧衬套2或内侧衬套2的过盈力检测,各机构复位。
[0103]
在本实施方式中,当基于所述位移传感器44的检测结果判定过盈连接强度不合格时,表明该闸片托34已经无法满足使用需要。
[0104]
现有的设备使用液压力作为驱动力,在进行过盈力检测时,由于液压驱动无法实现精确的速度控制和位置控制,使得检测工装在接触衬套2的瞬间会产生一定的冲击力,影响检测结果的准确性和稳定性。如果将压力轴杆速度调节的很慢,又会影响衬套2的检测效率。
[0105]
对于该闸片托34衬套2过盈力检测方法而言,动力输出单元45需要采用电动工替代传统的液压系统。因为液压系统的速度控制大多采用节流阀,阀和液压介质本身的特性造成速度控制有延时,且无法实现精确的位置控制。
[0106]
过盈力检测时,最主要的干扰因素就是瞬时冲击力,所以在拉压轴杆42和压头靠近工件时速度要控制在低速,同时出于检测效率的考虑,要尽量提升轴杆在不接触工件时的移动速度。电动缸的伺服特性能够较好的兼顾以上两点要求。
[0107]
过盈力检测合格与否的标准是检测给定压力下衬套2是否会松动,目前的判断方式为目视判断,一方面对作业人员的要求比较高,另一方面判定难度较大,容易出现错判漏判。本申请实施方式中主要采用与工控机10电性连接的位移传感器44,通过与工控机10中预存的数据进行比较,可以准确得进行过盈力的检测。
[0108]
此外,本申请针对目前不能实时检测、记录、和统计压装力。对于压装过程出现的压装力异常等情况缺少识别;过盈力检测记录表需要人工填写,自动化程度低且容易出错等问题,通过上述工控机10与拉压力传感器43和位移传感器44的设置能够彻底解决目前的问题。
[0109]
需要说明的是,在本申请的描述中,术语“第一”、“第二”等仅用于描述目的和区别类似的对象,两者之间并不存在先后顺序,也不能理解为指示或暗示相对重要性。此外,在本申请的描述中,除非另有说明,“多个”的含义是两个或两个以上。
[0110]
本说明书中的上述各个实施方式均采用递进的方式描述,各个实施方式之间相同相似部分相互参照即可,每个实施方式重点说明的都是与其他实施方式不同之处。
[0111]
以上所述仅为本实用新型的几个实施方式,虽然本实用新型所揭露的实施方式如上,但所述内容只是为了便于理解本实用新型而采用的实施方式,并非用于限定本实用新型。任何本实用新型所属技术领域的技术人员,在不脱离本实用新型所揭露的精神和范围的前提下,可以在实施方式的形式上及细节上作任何的修改与变化,但本实用新型的专利保护范围,仍须以所附权利要求书所界定的范围为准。