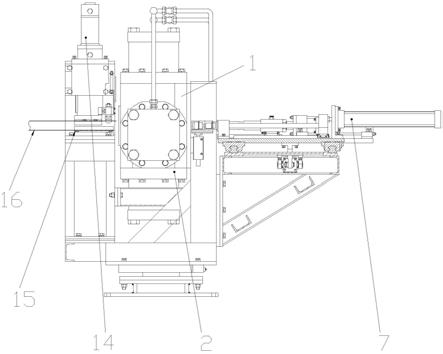
1.本实用新型涉及压尖机的技术领域,尤其是一种管材自动压尖机。
背景技术:2.随着社会的不断发展,机械加工行业得到了快速的发展。在机械加工过程中,铸轧法生产加工是重要的组成部分。在铸轧法生产工艺中,联拉设备是铜管生产线中的关键设备,主要是对管材进行拉拔,在生产线中至关重要,它直接影响整条生产线的生产运行情况,对员工技能要求较高。管材在拉拔过程中主要是采用游动芯头拉拔,对于提高生产线的生产效率、成品率极为有利,但还不能完全替代固定芯杆拉拔。不管是是游动芯头还是固定式都需要先进行压尖才能进行拉拔。压尖机主要是将铜管压制制头固定芯头,便于穿入模具进行夹紧拉拔。压尖实心长度250mm,压尖实心段至打坑处的距离为110mm,此距离太短,易压碎芯头,太长容易造成空拉,压尖段直径约23~25mm近圆柱形。压尖过程中全是人工操作,需要先进行手动吹气,吹气过程中漏气严重,吹气完成后再进行手动打坑,手动打油、手动放置芯头,操作人员根据所需位置进行手动压尖。整个操作环节全靠人工手动完成,特别是进行手动打坑,对操作人员使用铁棒进行打坑,每天需要进行200多次敲击动作,劳动强度大。放置芯头过程中为了保证芯头能和管壁完全结合,需要操作人员使用铜棒对芯头进行捣打,以此来保证芯头到位,压尖过程中因操作人员的不同,打坑位置、芯头位置都是靠经验进行,加上人员技能原因,压尖过程中变动大,往往在压尖过程中将芯头压伤,严重的直接压碎,损伤的芯头在拉拔过程中将铜管内壁划伤,直接造成产品报废,成品率下降,影响生产效率。
技术实现要素:3.本实用新型要解决的技术问题是:为了解决上述背景技术中存在的问题,提供一种管材自动压尖机,结构简单,通过电气控制可以实现完全自动化;实现自动压尖后减少了对人员技能的依赖性;节约人力成本,提高整体生产效率,保证产品质量,提高整体生产加工效率,便于广泛推广和使用。
4.本实用新型解决其技术问题所采用的技术方案是:一种管材自动压尖机,具有基座,所述的基座上端固定压尖机,所述的基座的一侧固定设置打坑组件;所述的基座的另一侧水平固定基板,所述的基板上端面上平行设置滑轨,所述的滑轨上通过滑套连接滑动板,所述的滑动板上固定设置注油及导入缸,所述的注油及导入缸一侧平行设置扩孔及吹气缸;所述的基板下端固定位移缸,所述的位移缸的伸缩端固定连接滑动板下端;所述的基板一侧正对压尖机出料位置处固定芯头存放台,所述的芯头存放台内放置芯头;所述的芯头存放台垂直方向一侧连接芯头移动缸。
5.进一步地说明,上述技术方案中,所述的芯头存放台水平方向一侧还设置导套。
6.进一步地说明,上述技术方案中,所述的打坑组件包括打坑液压缸和夹钳;所述的夹钳夹母管;所述的打坑液压缸设置在母管上端。
7.进一步地说明,上述技术方案中,所述的注油及导入缸的一侧连通注油管路。
8.进一步地说明,上述技术方案中,所述的扩孔及吹气缸的一侧连通进气管路。
9.本实用新型的有益效果是:本实用新型提出的一种管材自动压尖机,结构简单,通过电气控制可以实现完全自动化;实现自动压尖后减少了对人员技能的依赖性;节约人力成本,提高整体生产效率,保证产品质量,提高整体生产加工效率,便于广泛推广和使用。
附图说明
10.为了更清楚地说明本实用新型实施例或现有技术中的技术方案,下面将对实施例或现有技术描述中所需要使用的附图作简单地介绍,显而易见地,下面描述中的附图仅仅是本技术中记载的一些实施例,对于本领域普通技术人员来讲,在不付出创造性劳动的前提下,还可以根据这些附图获得其他的附图。
11.图1是本实用新型的结构示意图;
12.图2是图1的背部结构示意图;
13.图3是图1的俯视结构示意图。
14.附图中的标号为:1、基座,2、压尖机,3、基板,4、滑轨,5、滑套,6、滑动板,7、注油及导入缸,8、扩孔及吹气缸,9、位移缸,10、芯头存放台,11、芯头,12、芯头移动缸,13、导套,14、打坑液压缸,15、夹钳,16、母管,17、注油管路,18、进气管路。
具体实施方式
15.为了使本实用新型所解决的技术问题、技术方案及有益效果更加清楚明白,以下结合附图及实施例,对本实用新型进行进一步详细说明。应当理解,此处所描述的具体实施例仅仅用以解释本实用新型,并不用于限定本实用新型。
16.见图1、图2和图3所示的是一种管材自动压尖机,具有基座1,基座1上端固定压尖机2,基座1的一侧固定设置打坑组件;基座1的另一侧水平固定基板3,基板3上端面上平行设置滑轨4,滑轨4上通过滑套5连接滑动板6,滑动板6上固定设置注油及导入缸7,注油及导入缸7一侧平行设置扩孔及吹气缸8;基板3下端固定位移缸9,位移缸9的伸缩端固定连接滑动板6下端;基板3一侧正对压尖机2出料位置处固定芯头存放台10,芯头存放台10内放置芯头11;芯头存放台10垂直方向一侧连接芯头移动缸12。
17.其中,芯头存放台10水平方向一侧还设置导套13。打坑组件包括打坑液压缸14和夹钳15;夹钳15夹母管16;打坑液压缸14设置在母管16上端。注油及导入缸7的一侧连通注油管路17。扩孔及吹气缸8的一侧连通进气管路18。
18.该管材自动压尖机的使用原理如下:
19.首先,操作人员将待拉拔的母管16放进夹钳15处,需要压尖的长度及位置已提前进行设置,不需要在进行人工移动。夹钳15和打坑液压缸14都固定在打坑装置上。按动按钮,打坑液压缸14开始动作,液压缸头部设计有一个直径在25mm的冲头,液压缸推动夹钳15移动,夹钳15抱紧时冲头在打坑液压缸的推动下直接在母管16上方冲至一个深15mm左右的圆坑,便于芯头11位置的控制。母管16进入到压尖机2腔内,位移缸9进行动作,将扩孔及吹气缸8移送到所需位置,这时扩孔及吹气缸8开始动作,将扩孔和吹气两个动作合并完成,油缸中部安装有一个进气的过渡段,头部安装有一个锥形冲头,锥形冲头进入母管16内进行
扩孔和整圆内径,使冲头外壁和母管16内壁紧密贴合,杜绝漏气的产生,吹气时间已在程序中进行设定,无需人员操作。手动将所需的芯头11放置在芯头存放台10上面,该台可以根据所需的芯头大小对照位置放置,防止操作人员放错。吹气结束后,位移缸9回到原位,将注油及导入缸7移到指定位置,进行内膜油的注入,注油完成。芯头移动缸12进行动作,将芯头存放台10、芯头11移送到导套13处等待下一步动作,移动缸9行程已设定好。注油及导入缸7进行动作,将芯头11推送到母管16里面,缸杆收回,压尖机1开始动作,压尖完成。
20.本技术相对传统压尖设备具有如下优点:
21.本技术将原有的手动打坑、吹气、注油、芯头放置、捣芯头、压尖等功能进行自动化改造,并优化合并原来的动作,减少人员的操作干预,实现自动化。原来需要两人手动操作变为1人操作,降低了对人员技术经验的依赖,这样可以将操作人员解放到其它工位进行合并操作。动作优化并实现自动化后,降低了人员的劳动强度,杜绝了芯头11被压伤引起的质量问题,减少人工成本的同时也杜绝了质量问题的发生,提高生产效率,符合当前的自动化发展趋势。
22.以上所述的,仅为本实用新型较佳的具体实施方式,但本实用新型的保护范围并不局限于此,任何熟悉本技术领域的技术人员在本实用新型揭露的技术范围内,根据本实用新型的技术方案及其实用新型构思加以等同替换或改变,都应涵盖在本实用新型的保护范围之内。