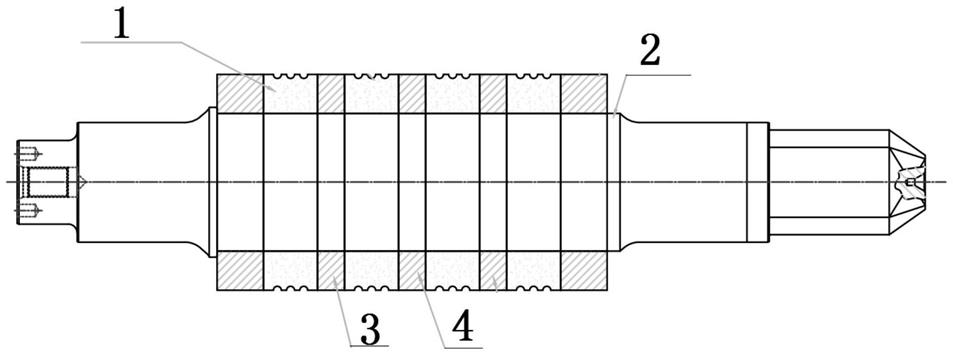
1.本实用新型属于冶金技术领域,尤其涉及一种碳化钨复合轧辊。
背景技术:2.碳化钨wc辊环一般采用ygr20
‑
40牌号,采用c、w、co、ni、cr等多种元素复合而成,其密度一般为13.73
‑
14.49g/cm3,具有硬度高,耐磨损、承受压力大等优点,但同时具有容易爆裂、成本高、生产制造难度大等特点。该材质一般以环状交付使用,最常见的是使用到高速线材轧机的预精轧、精轧的顶交45度轧机或者平立交替轧机上。
3.轧制直条螺纹钢棒材,通常使用的是带有轧槽的轧辊,材质通常有球墨铸铁轧辊或者高速钢轧辊。这种轧辊在轧制螺纹钢时,通常轧槽使用寿命为200
‑
300吨,使得生产中需要多次更换轧槽,降低了生产效率。因为wc轧辊主要以环状形状存在,在轧制螺纹钢棒直条棒材生产线很少应用。
4.轧辊与辊环生产是两种不同的工艺,一般分属于两种生产厂家,国内轧辊生产厂尚无法提供出铸铁轧辊与wc材质辊环的复合轧辊。
技术实现要素:5.针对上述技术问题,本实用新型提供一种螺纹钢棒材碳化钨复合轧辊,属于冶金行业螺纹钢直条棒材生产线使用的轧辊技术改造,本实用新型将球墨铸铁轧辊中部加工为凸环,所述凸环的两侧分别间隔布置碳化钨辊环和铸铁环,与凸环两侧紧贴的是碳化钨辊环,最外侧的是铸铁环;采用冷冻轧辊技术安装,最外侧的铸铁环与球墨铸铁轧辊螺纹连接、且在最外侧铸铁环的外侧采用满焊加工;通过本实用新型将不同材质、不同形状的两种轧辊、辊环复合成一体轧辊,应用到生产中,增加了成品轧槽的过钢量,降低了更换频率、提高生产效率。
6.本实用新型通过以下技术方案实现:一种碳化钨复合轧辊,包括碳化钨辊环、球墨铸铁轧辊和铸铁环;
7.所述球墨铸铁轧辊中部加工为凸环;所述凸环的两侧分别间隔布置碳化钨辊环和铸铁环,与凸环两侧紧贴的是碳化钨辊环,最外侧的是铸铁环;最外侧的铸铁环与球墨铸铁轧辊螺纹连接、且在最外侧铸铁环的外侧采用满焊加工;在碳化钨辊环上加工孔型。
8.上述方案中,在所述碳化钨辊环上加工螺纹孔型。
9.上述方案中,所述碳化钨辊环和铸铁环的数量均为四个。
10.与现有技术相比,本实用新型的有益效果是:本实用新型将球墨铸铁轧辊中部加工为凸环,所述凸环的两侧分别间隔布置碳化钨辊环和铸铁环,与凸环两侧紧贴的是碳化钨辊环,最外侧的是铸铁环;采用冷冻轧辊技术安装,最外侧的铸铁环与球墨铸铁轧辊螺纹连接、且在最外侧铸铁环的外侧采用满焊加工;本实用新型将wc辊环固定在现有轧辊上,通过使用wc辊环轧槽轧制螺纹钢,不但能有效提高单槽的过钢量,而且能够减少更换轧辊的次数,减少因为更换轧辊导致的副次品和堆钢次数,有效提高生产效率。将本实用新型应用
到大生产中,可以有效解决球墨铸铁轧槽过钢量低、钢材表面质量容易毛糙、更换成品轧槽频繁等问题,能够有效提高生产效率、减少因更换轧槽导致的堆钢、出现质量不合格品的风险。
附图说明
11.图1是本实用新型一实施方式的螺纹钢棒材碳化钨复合轧辊正视图;
12.图2是本实用新型一实施方式的修磨成螺纹孔型的碳化钨辊环正视图(a)及左视图(b)。
13.图中:1.碳化钨辊环;2.球墨铸铁轧辊;3.铸铁环;4.凸环。
具体实施方式
14.下面详细描述本实用新型的实施例,所述实施例的示例在附图中示出,其中自始至终相同或类似的标号表示相同或类似的元件或具有相同或类似功能的元件。下面通过参考附图描述的实施例是示例性的,旨在用于解释本实用新型,而不能理解为对本实用新型的限制。
15.在本实用新型的描述中,需要理解的是,术语“中心”、“纵向”、“横向”、“长度”、“宽度”、“厚度”、“上”、“下”、“轴向”、“径向”、“竖直”、“水平”、“内”、“外”等指示的方位或位置关系为基于附图所示的方位或位置关系,仅是为了便于描述本实用新型和简化描述,而不是指示或暗示所指的装置或元件必须具有特定的方位、以特定的方位构造和操作,因此不能理解为对本实用新型的限制。此外,术语“第一”、“第二”仅用于描述目的,而不能理解为指示或暗示相对重要性或者隐含指明所指示的技术特征的数量。由此,限定有“第一”、“第二”的特征可以明示或者隐含地包括一个或者更多个该特征。在本实用新型的描述中,“多个”的含义是两个或两个以上,除非另有明确具体的限定。
16.在本实用新型中,除非另有明确的规定和限定,术语“安装”、“相连”、“连接”、“固定”等术语应做广义理解,例如,可以是固定连接,也可以是可拆卸连接,或一体地连接;可以是机械连接,也可以是电连接;可以是直接相连,也可以通过中间媒介间接相连,可以是两个元件内部的连通。对于本领域的普通技术人员而言,可以根据具体情况理解上述术语在本实用新型中的具体含义。
17.图1所示为所述碳化钨复合轧辊的一种较佳实施方式,所述碳化钨复合轧辊,包括碳化钨辊环1、球墨铸铁轧辊2和铸铁环3。
18.所述球墨铸铁轧辊2中部加工为凸环4;所述凸环4的两侧分别间隔布置碳化钨辊环1和铸铁环3,与凸环4两侧紧贴的是碳化钨辊环1,最外侧的是铸铁环3;最外侧的铸铁环3与球墨铸铁轧辊2螺纹连接、且在最外侧铸铁环3的外侧采用满焊加工;在碳化钨辊环1上加工孔型。所述碳化钨辊环1上加工螺纹孔型,如图2所示。
19.在本实施例中,具体的,所述碳化钨辊环1和铸铁环3的数量均为四个。
20.所述碳化钨复合轧辊的制备过程如下:
21.所述球墨铸铁轧辊2加工:将所述球墨铸铁轧辊2中部加工为凸环4;
22.设定装配布置形式:所述凸环4的两侧分别间隔布置碳化钨辊环1和铸铁环3,与凸环4两侧紧贴的是碳化钨辊环1,最外侧的是铸铁环3;
23.螺纹连接加工:对最外侧的铸铁环3制作内螺纹,球墨铸铁轧辊2与最外侧的铸铁环3接触处制作外螺纹;
24.采用冷冻轧辊技术安装:将球墨铸铁轧辊2利用冷冻技术处理,再根据设定的装配布置形式,将碳化钨辊环1和铸铁环3安装到球墨铸铁轧辊2上,最外侧的铸铁环3与球墨铸铁轧辊2螺纹连接,在最外侧铸铁环3的外侧采用满焊加工;
25.孔型加工:在所述碳化钨辊环1上加工孔型。
26.所述采用冷冻轧辊技术安装具体为:将所述球墨铸铁轧辊2放置在
‑
20度冷冻环境内储存24小时,然后再根据设定的装配布置形式,将碳化钨辊环1和铸铁环3安装到球墨铸铁轧辊2上,安装后吊运出冷冻环境,再在最外侧铸铁环3的外侧采用满焊加工。本实用新型对轧辊最外侧两个铸铁环3车内螺纹,对球墨铸铁轧辊2最外端车外螺纹,其中外螺纹的长度依据轧辊和辊环直径测绘,装配时,使用最外侧铸铁环3对内部碳化钨辊环1进行紧固,然后再次满焊,可以100%保证避免wc辊环打滑。
27.所述孔型加工的步骤中,在所述碳化钨辊环1上加工螺纹孔型。
28.具体实施例:
29.采用棒五的成品轧辊技术数据,所述碳化钨辊环1的尺寸为φ370*230*90mm(外径*内径*厚度),材质牌号ygr20。依据对棒五成品φ370mm轧辊的尺寸测绘,提供8片相同的辊环,在成品k1轧辊上下辊上分别安装各4片辊环。按照测绘的结果,将原使用的成品k1轧辊车削成直径为φ230mm的轧辊,其中,碳化钨辊环1与成品k1轧辊公差与配合约有0.05mm的差距,轧辊车削呈凸环4,在突出的凸环4位置的两侧,分别安装碳化钨辊环1,在碳化钨辊环1外侧,各增加1片铸铁环3,其铸铁环3的外侧再依次安装碳化钨辊环1和铸铁环3。在最外侧的铸铁环3外侧处,采用满焊形式焊接固定,防止使用过程中碳化钨辊环1与球墨铸铁轧辊2之间产生相对滑动。球墨铸铁轧辊2的磨削尺寸,使得磨削成的直径与碳化钨辊环1内圈直径形成紧密配合。轧制过程中,碳化钨辊环1与墨铸铁轧辊2受热,直径增加,使得碳化钨辊环1内径尺寸减小,墨铸铁轧辊2的外径尺寸增加,将所述球墨铸铁轧辊2放置在冷冻环境内使得其直径变小,在进行装配,使得复合轧辊紧密配合,避免打滑。组装完毕后,对碳化钨辊环1按照要求,加工成螺纹孔型,并组装成配套轧辊上线使用。如果采用常温安装,其车削后轧辊轴尺寸一般在230
‑
(0.1
‑
0.15)mm,轧辊轴与辊环内径直接留的间隙较大,不然安装不上去,这种间隙大的安装在使用过程中,辊环与轧辊轴之间的摩擦力变小,容易打滑,导致生产无法正常,而冷冻轧辊技术安装时,轧辊轴在230
‑
0.05mm即可。
30.本实用新型中精确测绘出碳化钨辊环1的内侧直径。在修磨轧辊过程中,利用数控车床和数控磨床按照要求磨削,磨削后球墨铸铁轧辊2尺寸精确到0
‑
0.02mm范围内;测绘尺寸和修磨尺寸精度高。对最外侧的铸铁环与铸铁轧辊之间满焊,不得有虚焊现象,焊接后检查时,各个碳化钨辊环1不得出现相对移动。
31.使用原来铸铁材质的轧辊,轧制螺纹钢时,k1轧制吨位一般在200
‑
300吨/槽,特别是需要采用控轧控冷工艺的hrb500系列、出口的sd400
‑
500系列以及部分出口东南亚的美标螺纹钢,需要低温大压下技术,对轧槽的磨损量大大增加,通常轧槽使用寿命为200余吨/槽。而使用本实用新型所述碳化钨复合轧辊后,过钢量一般达到600
‑
800吨/槽。使用寿命大大增加。
32.使用铸铁轧辊时,螺纹钢孔型轧辊下线后需要全部车掉、重新铣槽,轧槽加工量一
般需要2
‑
3mm/次,铸铁辊直径明显变小,很快达到报废标准。使用本实用新型所述碳化钨复合轧辊的轧槽,每次重新加工时,修磨量一般在0.5mm以内,只需要对原轧槽外形尺寸和深度稍微加工后,即可满足孔型要求,轧槽再修磨量小。一套wc辊环的复合轧辊,能够再修磨次数达到25
‑
30次。
33.本实用新型所述碳化钨复合轧辊,每8小时更换轧槽一次即可,使用原铸铁轧辊时,一般需要更换3
‑
4次,平均班减少2次更换轧槽时间,考虑到点检时间,一般每班8小时可以增加生产时间40
‑
50min。每天可以增加产量约300
‑
400吨,提高工作效率。
34.使用原来铸铁轧辊时,每次更换轧槽,堆钢的风险增大,同时也需要出现调试的钢材,影响作业时、钢材成材率等指标。使用本实用新型所述碳化钨复合轧辊后,成品轧机和轧制线不动,仅仅检查导卫、红钢通道等,达到缩短检修时间,降低堆钢次数和调试副次品吨位,降低生产事故隐患,降低调试副次品量。
35.通过技改,使用了复合轧辊后,相同情况下,每天可以增加产量约300
‑
400吨,全月产量增约7500吨以上;成材率大约增加0.1
‑
0.2%,每月的堆钢次数减少在5
‑
8次左右,同时机时产量提高0.2
‑
0.6吨/小时,指标改善明显。
36.达到报废的复合轧辊,自然冷却到室温后,可以拆卸,将碳化钨辊环1与球墨铸铁轧辊2分离,碳化钨辊环1可以再回收后销售给辊环供应厂家,减少浪费。
37.经济效益预算:
38.生产成本增加:使用该工艺制作的复合轧辊,在永钢棒材五厂使用后,采购成本由原来的7.8元/吨增加到10.2元/吨,轧辊吨钢费用增加。该机组共有2条螺纹钢生产线,其中a线轧制和的四切分;b线轧制和的四切分;全月产量在18.2
‑
19.3万吨生产计划的规格差异,按照全月18.2万吨计算,技改后增加10.2
‑
7.8*18.2万=43.68万元/月。
39.产生效益:全月因减少更换轧辊、提高轧制作业时间增产7500吨;吨钢效益平均为200
‑
1000元/吨,按照300元/吨计算,可以增加效益225万元/月。
40.其它指标改善:因堆钢次数减少、调试副次品减少使得成材率增加0.1
‑
0.2%,每月的堆钢次数减少在5
‑
8次左右,同时机时产量提高0.2
‑
0.6吨/小时。
41.增加效益预估:225.0
‑
43.68=181.32万元/月;全年增加181.32*11=1194.5万元。
42.本实用新型包括碳化钨辊环1、球墨铸铁轧辊2、铸铁环3,并配备焊接技术、螺纹加工技术,具有可重复使用性高、投入与产出比高、生产效率提高明显等特点。有效节约更换轧辊时长、生产效率低、生产事故多、调试品吨位大等问题。通过减少更换作业时间,提高经济效益显著,具有很广的推广价值。而且具有保护设备、降低安全风险的作用。
43.上文所列出的一系列的详细说明仅仅是针对本实用新型的可行性实施例的具体说明,它们并非用以限制本实用新型的保护范围,凡未脱离本实用新型技艺精神所作的等效实施例或变更均应包含在本实用新型的保护范围之内。