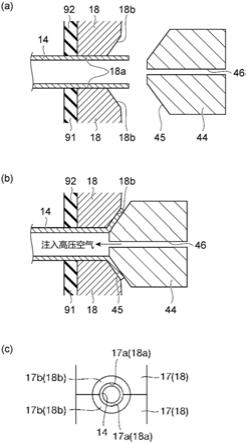
1.本发明涉及一种成型系统。
背景技术:2.以往,已知有一种向已被加热的金属管材料内供给气体以使其膨胀,从而成型出具有管部及凸缘部的金属管的成型装置。例如,在下述专利文献1中公开了一种成型装置,其具备:上下模具,其彼此配对;气体供给部,其向保持在上下模具之间的金属管材料内供给高压气体;加热机构,其对该金属管材料进行加热;及型腔部,其由上述上下模具彼此合拢而形成。
3.以往技术文献
4.专利文献
5.专利文献1:日本特开2012
‑
654号公报
技术实现要素:6.发明要解决的技术课题
7.为了提高利用上述专利文献1中示出的成型装置来成型出的金属管的生产率,需要从金属管迅速排出高压气体。此时,气体的排气声会变大,因此,对成型装置的工作人员等而言,该排气声可能会构成噪音。因此,要求应对上述排气声。
8.本发明的目的在于提供一种能够应对排气声的成型系统。
9.用于解决技术课题的手段
10.本发明涉及一种成型系统,其成型出中空形状的金属管,其中,所述成型系统具备成型装置,所述成型装置具有在成型出金属管时向已被加热的金属管材料内供给气体的气体供给部及排出成型出的金属管内的气体的排出部,排出部的排气口位于具有内部空间的结构物的内部空间内。
11.根据该成型系统,排出部的排气口位于具有内部空间的结构物的内部空间内。因此,在从排气口排出高压气体时产生的排气声在结构物内产生。此时,结构物作为排气声的消声器而发挥作用。因此,对在成型装置的周围工作的工作人员等而言,该排气声不易构成噪音。因此,通过利用上述成型系统,能够应对排气声。
12.成型系统具备:地面,其载置成型装置;及地下凹坑,其设置于地面的下部。排出部可以具有排气管,该排气管位于作为结构物的地下凹坑内并且设置有排气口。
13.根据该成型系统,包含在排出部中并且设置有排气口的排气管位于设置于地面的下部的地下凹坑内。由此,在从排气口排出高压气体时产生的排气声在地下凹坑内产生。因此,对在地面之上并且在成型装置的周围工作的工作人员等而言,该排气声不易构成噪音。因此,通过利用上述成型系统,能够应对排气声。并且,通过将作为消声器而发挥作用的结构物设置于地下凹坑,有助于缩小整个成型装置的空间。
14.成型装置还可以具有用于对金属管材料进行加热的电极及与电极连接的馈电线,
馈电线可以具有容纳于地下凹坑内的导体,在地下凹坑中,排气口可以与导体对置。此时,能够利用从排气口排出的气体来冷却随着对电极通电而被加热的导体。
15.发明效果
16.根据本发明,提供一种能够应对排气声的成型系统。
附图说明
17.图1是本实施方式所涉及的成型系统所具有的成型装置的概略结构图。
18.图2中(a)是表示电极保持金属管材料的状态的图,图2中(b)是表示气体供给喷嘴与电极抵接的状态的图,图2中(c)是电极的主视图。
19.图3是成型系统的示意俯视图。
20.图4是成型系统的主要部分概略立体图。
21.图5中(a)及(b)是表示母线与末端部之间的关系的示意图,图5中(c)是表示使母线与末端部分开的状态的图。
22.图6是表示变形例所涉及的成型系统的排气机构周边结构的示意图。
具体实施方式
23.以下,参考附图对本发明所涉及的成型系统的优选实施方式进行说明。另外,在各附图中,对相同的部分或相应的部分标注相同的符号,并省略重复说明。
24.<成型装置的结构>
25.图1是本实施方式所涉及的成型系统所具有的成型装置的概略结构图。如图1所示,成型出金属管的成型装置10具备:成型模具13,其具有上型12及下型11;驱动机构80,其使上型12及下型11中的至少一个移动;管保持机构30,其保持配置在上型12与下型11之间的金属管材料14;加热机构50,其对被管保持机构30保持的金属管材料14进行通电而进行加热;气体供给部60,其用于向保持于上型12与下型11之间并被加热的金属管材料14内供给高压气体(气体);一对气体供给机构40、40,其用于向被管保持机构30保持的金属管材料14内供给来自气体供给部60的气体;及水循环机构72,其强制性对成型模具13进行水冷,并且,成型装置10还具备控制部70,该控制部70分别控制上述驱动机构80的驱动、上述管保持机构30的驱动、上述加热机构50的驱动及上述气体供给部60的气体供给。另外,以下,金属管材料14是指成型前的中空结构体,金属管是指成型后的中空结构体。因此,金属管材料14和金属管均呈中空形状。
26.成型模具13的一个模具即下型11固定于基座15。下型11由较大的钢铁制块构成,在其上表面具备例如矩形的型腔(凹部)16。在下型11形成有冷却水通道19。并且,在下型11的大致中央具备从下方插入的热电偶21。热电偶21被弹簧22支承为上下移动自如。
27.此外,在下型11的左右端(图1中的左右端)附近设置有空间11a,在该空间11a内,以能够上下进退移动的方式配置有管保持机构30的可动部(后述的电极17、18(下侧电极)等)。而且,通过将金属管材料14载置于下侧电极17、18之上,下侧电极17、18接触到配置在上型12与下型11之间的金属管材料14。由此,下侧电极17、18与金属管材料14电连接。
28.在下型11与下侧电极17之间、下侧电极17的下部、下型11与下侧电极18之间及下侧电极18的下部,分别设置有用于防止通电的绝缘材料91。各个绝缘材料91固定于构成管
保持机构30的致动器(未图示)的可动部(即,进退杆95)。该致动器用于使下侧电极17、18等上下移动,致动器的固定部与下型11一同保持于基座15侧。
29.成型模具13的另一个模具即上型12固定于构成驱动机构80的后述滑动件81上。上型12由较大的钢铁制块构成,在其内部形成有冷却水通道25,并且在其下表面具备例如矩形的型腔(凹部)24。该型腔24设置于与下型11的型腔16对置的位置。
30.与下型11同样,在上型12的左右端(图1中的左右端)附近设置有空间12a,在该空间12a内,以能够上下进退移动的方式配置有管保持机构30的可动部(即,后述电极17、18(上侧电极)等)。而且,在金属管材料14载置于下侧电极17、18上的状态下,上侧电极17、18朝下移动,从而与配置在上型12与下型11之间的金属管材料14接触。由此,上侧电极17、18与金属管材料14电连接。
31.在上型12与上侧电极17之间、上侧电极17的上部、上型12与上侧电极18之间及上侧电极18的上部,分别设置有用于防止通电的绝缘材料92。各个绝缘材料92固定于构成管保持机构30的致动器(未图示)的可动部(即,进退杆96)。该致动器用于使上侧电极17、18等上下移动,致动器的固定部与上型12一同保持于驱动机构80的滑动件81侧。
32.在管保持机构30的右侧部分的电极18、18的彼此对置的面上,分别形成有与金属管材料14的外周面形状相对应的半圆弧状的凹槽18a(参考图2中(c))。金属管材料14能够嵌入于该凹槽18a的部分。与上述凹槽18a同样,在管保持机构30的右侧部分的绝缘材料91、92的彼此对置的暴露面上,分别形成有与金属管材料14的外周面形状相对应的半圆弧状的凹槽。并且,在电极18的正面(朝向模具的外侧方向的面)上形成有凹槽18a的周围以朝向凹槽18a圆锥状倾斜的方式凹陷而成的锥形凹面18b。因此,若利用管保持机构30的右侧部分从上下方向夹持金属管材料14,则恰好能够紧紧地包围金属管材料14的右侧端部的整个外周。
33.在管保持机构30的左侧部分的电极17、17的彼此对置的面上分别形成有与金属管材料14的外周面形状相对应的半圆弧状的凹槽17a(参考图2中(c))。金属管材料14能够嵌入于该凹槽17a的部分。与上述凹槽17a同样,在管保持机构30的左侧部分的绝缘材料91、92的彼此对置的暴露面上,分别形成有与金属管材料14的外周面形状相对应的半圆弧状的凹槽。并且,在电极17的正面(朝向模具的外侧方向的面)上形成有凹槽17a的周围以朝向凹槽17a圆锥状倾斜的方式凹陷而成的锥形凹面17b。因此,若利用管保持机构30的左侧部分从上下方向夹持金属管材料14,则恰好能够紧紧地包围金属管材料14的左侧端部的整个外周。
34.如图1所示,驱动机构80具备:滑动件81,其使上型12朝向上型12与下型11彼此合拢的方向移动;轴82,其产生用于使上述滑动件81移动的驱动力;及连杆83,其用于向滑动件81传递该轴82所产生的驱动力。轴82在滑动件81的上方沿左右方向延伸且被支承为旋转自如。该偏心曲柄82a通过连杆83与设置于滑动件81的上部且沿左右方向延伸的旋转轴81a连结。在驱动机构80中,控制部70控制轴82的旋转,从而改变偏心曲柄82a在上下方向上的高度,该偏心曲柄82a的位置变化经由连杆83传递到滑动件81,从而能够控制滑动件81的上下移动。在此,向滑动件81传递偏心曲柄82a的位置变化时产生的连杆83的摆动(旋转运动)被旋转轴81a吸收。另外,轴82例如根据被控制部70控制的马达等的驱动而旋转或停止。
35.加热机构50具备供电部55以及将供电部55与电极17、18电连接的供电线路52。供
电部55包括直流电源及开关,在电极17、18与金属管材料14电连接的状态下,供电部55可以经由供电线路52、电极17、18对金属管材料14进行通电。供电线路52具有与下侧电极17连接的馈电线52a及与下侧电极18连接的馈电线52b。
36.在该加热机构50中,从供电部55输出的直流电流通过馈电线52a传输并输入到电极17。接着,直流电流通过金属管材料14后输入到电极18。然后,直流电流通过馈电线52b传输并输入到供电部55。
37.返回到图1,一对气体供给机构40分别具有:缸体单元42;活塞杆43,其配合缸体单元42的动作而进行进退移动;及密封部件44,其连结于活塞杆43的管保持机构30侧的末端。缸体单元42载置并固定于块体41上。在密封部件44的末端形成有朝向末端变细的锥形面45,该锥形面45构成为与电极17、18的锥形凹面17b、18b相匹配的形状(参考图2)。密封部件44设置有从缸体单元42侧朝向末端延伸的气体通道46,该气体通道46供从气体供给部60供给过来的高压气体流过。
38.气体供给部60包括气体源61、积存从该气体源61供给过来的气体的储气罐62、从该储气罐62延伸至气体供给机构40的缸体单元42的第1管63、设置于该第1管63上的压力控制阀64及转换阀65、从储气罐62延伸至形成于密封部件44内的气体通道46的第2管67、设置于该第2管67上的压力控制阀68及止回阀69。压力控制阀64发挥如下作用:向缸体单元42供给与密封部件44对金属管材料14的推力相对应的工作压力的气体。止回阀69发挥如下作用:防止高压气体在第2管67内逆流。设置于第2管67的压力控制阀68发挥如下作用:通过控制部70的控制向密封部件44的气体通道46供给用于使金属管材料14膨胀的工作压力的气体。另外,第2管67从止回阀69分支为二股从而具有延伸至一个气体供给机构40的气体供给管路l1和延伸至另一个气体供给机构40的气体供给管路l2。
39.成型装置10具备排出成型出的金属管内的气体的排气机构(排出部)200a、200b。排气机构200a连接于气体供给管路l1,排气机构200b连接于气体供给管路l2。因此,排气机构200a经由气体供给管路l1及一个气体供给机构40的气体通道46而排出金属管内的气体。并且,排气机构200b经由气体供给管路l2及另一个气体供给机构40的气体通道46排出金属管内的气体。例如,排气机构200a、200b分别具有从各个供给管路分支并且设置有排气口的排气管(详细内容将在后面进行叙述)。排气机构200a、200b分别具有在控制部70的控制下进行打开或关闭的压力控制阀、安全阀等。设置压力控制阀、安全阀等的位置并不受特别限定。
40.控制部70通过控制气体供给部60的压力控制阀68能够向金属管材料14内供给所期望的工作压力的气体。并且,控制部70通过接收从图1所示的(a)传递过来的信息,从热电偶21获取温度信息,并控制驱动机构80及供电部55等。
41.水循环机构72包括:积存水的水槽73;汲取积存于该水槽73中的水并对其进行加压而送至下型11的冷却水通道19及上型12的冷却水通道25的水泵74;及配管75。在此虽然进行了省略,但在配管75上还可以设置用于降低水温的冷却塔或用于净化水的过滤器。
42.<使用成型装置进行的金属管的成型方法>
43.接着,对使用成型装置10进行的金属管的成型方法进行说明。首先,准备可淬火钢类的圆筒状的金属管材料14。例如,利用机器手臂等将该金属管材料14载置(投放)到下型11侧的电极17、18上。由于在电极17、18上形成有凹槽17a、18a,因此金属管材料14被该凹槽
17a、18a定位。
44.接着,控制部70控制驱动机构80及管保持机构30以使该管保持机构30保持金属管材料14。具体而言,通过驱动机构80的驱动使保持于滑动件81侧的上型12及上侧电极17、18等朝向下型11侧移动,并且使管保持机构30所具有的能够让上侧电极17、18等及下侧电极17、18等进退移动的致动器工作,从而利用管保持机构30从上方和下方夹持金属管材料14的两侧端部附近。就该夹持而言,由于存在形成于电极17、18上的凹槽17a、18a及形成于绝缘材料91、92上的凹槽,因此成为与金属管材料14的两侧端部附近的整周紧贴的状态。
45.此时,如图2中(a)所示,金属管材料14的电极18侧的端部在金属管材料14的延伸方向上比电极18的凹槽18a与锥形凹面18b之间的边界更向密封部件44侧突出。同样地,金属管材料14的电极17侧的端部在金属管材料14的延伸方向上比电极17的凹槽17a与锥形凹面17b之间的边界更向密封部件44侧突出。并且,上侧电极17、18的下表面与下侧电极17、18的上表面彼此接触。然而,并不只限于与金属管材料14的两端部的整周紧贴的结构,也可以采用电极17、18与金属管材料14的周向上的一部分抵接的结构。
46.接着,控制部70通过控制加热机构50而加热金属管材料14。具体而言,控制部70控制加热机构50的供电部55而进行供电。如此一来,经由供电线路52传递到下侧电极17、18的电力供给到夹持金属管材料14的上侧电极17、18及金属管材料14,并且基于金属管材料14自身所具有的电阻,金属管材料14自身基于焦耳热而发热。即,金属管材料14处于电加热状态。
47.接着,控制部70控制驱动机构80,针对加热后的金属管材料14关闭成型模具13。由此,下型11的型腔16与上型12的型腔24彼此组合,金属管材料14配置并密封于下型11与上型12之间的型腔部内。
48.然后,使气体供给机构40的缸体单元42工作以使密封部件44前进,从而密封金属管材料14的两端。此时,如图2中(b)所示,密封部件44按压金属管材料14的电极18侧的端部,比电极18的凹槽18a与锥形凹面18b之间的边界更向密封部件44侧突出的部分变形为与锥形凹面18b相同的漏斗状。同样地,密封部件44按压金属管材料14的电极17侧的端部,比电极17的凹槽17a与锥形凹面17b之间的边界更向密封部件44侧突出的部分变形为与锥形凹面17b相同的漏斗状。在完成密封之后,将高压气体吹入金属管材料14内,从而使通过加热而被软化的金属管材料14成型为与型腔部的形状相同的形状。
49.由于金属管材料14被加热成高温(950℃左右)就会软化,因此供给到金属管材料14内的气体会热膨胀。因此,作为供给气体例如供给压缩空气,通过热膨胀的压缩空气能够容易使950℃的金属管材料14膨胀。
50.通过吹塑成型而膨胀的金属管材料14的外周面与下型11的型腔16接触就会被快速冷却,并且与上型12的型腔24接触就会被快速冷却(由于上型12与下型11的热容量较大且被管理成低温,因此只要金属管材料14与上型12或下型11接触,管表面的热量就会一下子被模具侧夺去),从而进行淬火。这种冷却法被称为模具接触冷却或模具冷却。刚被快速冷却之后,奥氏体转变成马氏体(以下,将奥氏体转变成马氏体的现象称为马氏体相变)。由于在冷却的后期冷却速度变慢,因此马氏体通过回热而转变成另一组织(托氏体、索氏体等)。因此,无需另行进行回火处理。并且,在本实施方式中,可以代替模具冷却而向型腔24内供给例如冷却介质而进行冷却,或者除了模具冷却之外,还可以向型腔24内供给例如冷
却介质而进行冷却。例如,直至马氏体相变的开始温度为止,可以使金属管材料14与模具(上型12及下型11)接触而进行冷却,之后可以在开模的同时向金属管材料14喷吹冷却介质(冷却用气体),从而引起马氏体相变。
51.如上所述,在对金属管材料14进行吹塑成型之后进行冷却,然后进行开模,从而得到具有例如大致矩形筒状的主体部的金属管。
52.<成型系统的结构>
53.接着,参考图3及图4,对本实施方式所涉及的成型系统1进行说明。图3是成型系统1的示意俯视图。图4是成型系统1的主要部分概略立体图。
54.如图3所示,成型系统1具备成型装置10、载置金属管材料14的第1载置部101、载置成型后的金属管的第2载置部102、搬运金属管材料14或金属管的搬运机构103及控制部70。并且,如图4所示,成型系统1还具备载置成型装置10的一部分的地面300及设置于地面300的下部的地下凹坑400(结构物)。另外,在图4中,为了便于说明,省略了成型装置10的一部分和地面300的一部分。以下,将水平方向上的电极17与电极18彼此对置的方向作为“x轴方向”,将水平方向上的与x轴方向正交的方向作为“y轴方向”,将上下方向作为“z轴方向”。
55.第1载置部101在x方向上位于成型装置10的中心的一侧,并且在y方向上位于成型装置10的中心的一侧。并且,第2载置部102在x方向上位于成型装置10的中心的另一侧,并且在y方向上位于成型装置10的中心的一侧。搬运机构103为将金属管材料14设置于成型装置10以及从成型装置10取出成型后的金属管的机构,且其具有主体部103a及机器手臂103b。搬运机构103在x方向上位于第1载置部101与第2载置部102之间。在y方向上,主体部103a比第1载置部101及第2载置部102更远离成型装置10,但并不只限于此。
56.地面300为载置成型装置10的基座15、成型模具13、气体供给机构40及驱动机构80等的载置面。地面300例如可以是工厂等的地面,也可以是设置于该地面上的基台的表面。在地面300设置有插通馈电线52a、52b等的开口301。并且,地下凹坑400为用于容纳成型装置10的一部分的容纳空间。地下凹坑400的至少一部分与成型装置10的位于地面300之上的部分重叠。地面300之上的空间与地下凹坑400经由开口301连通。虽未图示,地下凹坑400的出入口设置于在z方向上不与成型装置10重叠的部位。另外,可以由盖子等盖住开口301。
57.加热机构50的供电部55是经由馈电线52a、52b向电极17、18供给电力的装置。供电部55在y方向上位于成型装置10的中心的另一侧,并且容纳与地下凹坑400内。供电部55配置于在z方向上不与基座15重叠的位置。
58.馈电线52a具有多个电线52a和母线52b(导体)。多个电线52a为用于连接电极17与母线52b的配线。因此,电线52a的一个端子与电极17连接,电线52a的另一个端子与母线52b连接。电线52a的大部分布线在地面300之上。电线52a的包括另一个端子在内的一部分经由设置于地面300的开口301而配置于地下凹坑400内。母线52b为连接供电部55与电线52a的导电结构体,并且容纳在地下凹坑400内。母线52b例如为铜等金属制导电体或合金制导电体,并且是馈电线52a中最有可能发热的部位。母线52b例如载置于固定在地下凹坑400内的台座401上。母线52b配置于在z方向上不与基座15重叠的位置。母线52b具有大致l字形的主体部56和安装电线52a的端子部57。端子部57在z方向上安装于主体部56的地面300侧。
59.馈电线52b具有多个电线52c和母线52d(导体)。多个电线52c为用于连接电极18与母线52d的配线。因此,电线52c的一个端子与电极18连接,电线52c的另一个端子与母线52d
连接。电线52c的大部分布线在地面300之上。电线52c的包括另一个端子在内的一部分经由设置于地面300的开口301而配置于地下凹坑400内。母线52d为连接供电部55与电线52c的导电结构体,并且与母线52b同样地,容纳在地下凹坑400内。母线52d例如为铜等金属制导电体或合金制导电体,并且是馈电线52b中最有可能发热的部位。母线52d例如也载置于固定在地下凹坑400内的台座401上。母线52d配置于在z方向上不与基座15重叠的位置。母线52d具有大致l字型的主体部58和安装电线52c的端子部59。端子部59在z方向上安装于主体部58的底面300侧。
60.如图4所示,在连接有馈电线52a的气体供给机构40安装有排气管210,在连接有馈电线52b的气体供给机构40安装有排气管220。排气管210是排气机构200a的构成要件之一,其具有主要部分211及末端部212。排气管220是排气机构200b的构成要件之一,其具有主要部分221及末端部222。主要部分211、221布线在地面300之上。末端部212、222分别经由开口301容纳在地下凹坑400内。在地下凹坑400中,末端部212沿着母线52b的外周面配设,末端部222沿着母线52d的外周面配设。在本实施方式中,末端部212沿着母线52b的主体部56中的沿着z方向延伸的部分和主体部56中的沿着x方向延伸的部分这两者配设。与末端部212同样地,末端部222沿着母线52d的主体部58中的沿着z方向延伸的部分和主体部58中的沿着x方向延伸的部分这两者配设。虽然在图3中进行了省略,但排气管210从气体供给管路l1分支,排气管220从气体供给管路l2分支。
61.排气管210、220由可承受高压气体的材质制成,例如为金属制管或合金制管。此时,排气管210、220可显示导电性。从抑制馈电线52a的电阻增加等的观点出发,末端部212与母线52b分开。从防止末端部212与母线52b接触的观点出发,可以在末端部212与母线52b之间设置绝缘材料等。同样地,末端部222也与母线52d分开。
62.在此,参考图5中(a)~(c)对地下凹坑400内的母线52b、52d和末端部212、222的配置进行说明。图5中(a)及(b)是表示母线52b、52d与末端部212、222之间的关系的示意图。图5中(c)是表示使母线52b与末端部212进一步分开的状态的图。另外,在图5中(a)~(c)中,末端部212、222分别安装有安全阀213、223。安全阀213、223可以设置于地下凹坑400内,也可以设置于地面300之上。
63.如上所述,末端部212沿着母线52b配设,末端部222沿着母线52b配设。而且,设置于末端部212的排气口214设置成与母线52b对置。由此,从排气口214排出的气体吹向母线52b。在本实施方式中,在末端部212上设置有多个排气口214,但并不只限于此。另外,虽未图示,但设置于末端部222的排气口设置成与母线52d对置。
64.在成型系统1中,控制部70例如组装在固定的控制台,在y方向上其位于成型装置10的中心的一侧。因此,控制部70在y方向上位于成型装置10的与加热机构50相反的一侧。而且,控制部70在y方向上位于成型装置10的与排气管210、220的末端部212、222相反的一侧。由此,工作人员在使用控制台时不易受从加热机构50产生的热量及从排气机构200a、200b排出的气体的影响。并且,控制部70在y方向上位于搬运机构103的与成型装置10相反的一侧。由此,在工作人员使用控制台时,搬运机构103的动作不会被工作人员阻碍。
65.<作用效果>
66.接着,对本实施方式所涉及的成型系统1的作用效果进行说明。根据成型系统1,排气机构200a的排气口214位于具有内部空间的结构物(即,地下凹坑400)的内部空间内。因
此,在从排气口214排出高压气体时产生的排气声在地下凹坑400内产生。此时,地下凹坑400作为排气声的消声器而发挥作用。因此,对在成型装置10的周围工作的工作人员等而言,该排气声不易构成噪音。因此,通过利用上述成型系统1,能够应对排气声。并且,通过将作为消声器而发挥作用的结构物设置于地下凹坑,有助于缩小整个成型装置的空间。
67.根据上述成型系统1,包含在排气机构200a中并且设置有排气口214的排气管210的末端部212位于设置于地面300的下部的地下凹坑400内。由此,在从排气口214排出高压气体时产生的排气声在地下凹坑400内产生。而且,包含在排气机构200b中并且设置有排气口的排气管220的末端部222也位于地下凹坑400内。由此,在从设置于末端部222的排气口排出高压气体时产生的排气声也在地下凹坑400内产生。因此,对在地面300之上且在成型装置10的周围工作的工作人员等而言,上述排气声不易构成噪音。因此,通过利用成型系统1,能够应对排气声。
68.在本实施方式的成型系统1中,成型装置10具有用于对金属管材料14进行加热的电极17、18及与电极17、18连接的馈电线52a、52b,馈电线52a具有容纳在地下凹坑400内的母线52b,在地下凹坑400中,排气口214与母线52b对置。因此,能够利用从排气口214排出的气体来冷却随着对电极17通电而被加热的母线52b。而且,馈电线52b具有容纳在地下凹坑400内的母线52d,在地下凹坑400中,设置于末端部222的排气口与母线52d对置。因此,也能够利用从上述排气口排出的气体来冷却随着对电极18通电而被加热的母线52d。
69.以上,对本发明的优选实施方式进行了说明,但本发明并不受上述实施方式的任何限定。例如,各馈电线也可以不具有母线。并且,末端部沿着母线的外周面配设,但也可以沿着母线的内周面配设。
70.在上述实施方式中,在地下凹坑中,排气管的排气口与母线对置,但并不只限于此。例如,在使用水冷式的电缆等来冷却母线的情况下,排气管的排气口可以不与母线对置。即,不利用从排气口排出的气体来冷却母线也可。
71.在上述实施方式中,作为消声器而发挥作用的结构物使用了地面下的地下凹坑。但是,结构物只要具有能够配置排气部的内部空间并且能够切断在该内部空间中产生的声音外泄,则并不受限定。例如,如图6所示,成型系统也可以具有罐500作为结构物。排气机构200a、200b的排气口214位于该罐500的内部空间。在使用罐500的情况下,该罐500的位置并不受特别限定。例如,罐500可以配置于地面300之上而不是地下凹坑内。
72.例如,作为比较例所涉及的结构,可举出在排气部的末端设置消声器而进行隔音的结构。但在排气压力高的情况下,这样的消声器无法承受排气压力,有可能会受损。相对于此,罐500具有足够大的内部空间,因此,即使在排气压力高的情况下,受损的可能性也较低,能够长期利用。利用地下凹坑进行隔音的情况下,也能够获得同样的效果。
73.在上述实施方式中,成型系统除了具有成型装置以外,还具备第1载置部、第2载置部及搬运机构等,但并不只限于此。例如,成型系统也可以不具备第1载置部、第2载置部及搬运机构中的至少一个。并且,第1载置部、第2载置部及搬运机构等并不只限于上述实施方式中示出的结构。
74.例如,上述实施方式中的成型装置无需一定要具有加热机构,可以使用预先被加热的金属管材料。
75.符号说明
[0076]1‑
成型系统,10
‑
成型装置,13
‑
成型模具,14
‑
金属管材料、17、18
‑
电极,40
‑
气体供给机构,50
‑
加热机构,52
‑
供电线路,52a、52b
‑
馈电线,52b、52d
‑
母线(导体),55
‑
供电部,60
‑
气体供给部,80
‑
驱动机构,103
‑
搬运机构,200a、200b
‑
排气机构,210、220
‑
排气管,212、222
‑
末端部,214
‑
排气口,300
‑
地面,301
‑
开口,400
‑
地下凹坑(结构物),500
‑
罐(结构物),l1、l2
‑
气体供给管路。