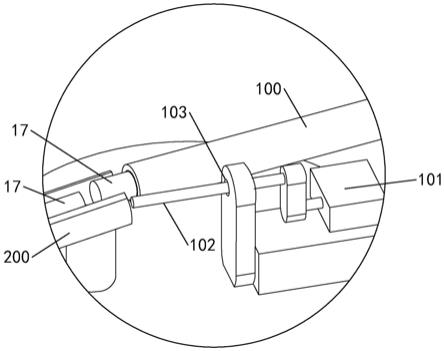
1.本发明涉及合金球整圆加工技术领域,具体涉及一种合金球整圆自动加工生产线及其加工方法。
背景技术:2.合金球加工成型包括毛胚料的整圆步骤。
3.毛胚料是通过锯床将合金棒切割成短圆柱状物料,整圆后的合金球粗产品经过后续的淬火和研磨得到一定规格的合金球。
4.目前合金球的整圆包括人工操作高温加热设备的控制面板,设置一定的参数,然后在高温加热设备中逐步放入毛胚料,待毛胚料加热至红达到可锻造整圆状态,然后其中一名工作人员采用长钳夹住毛胚料从高温加热设备中取出,并转移放入到凹形的基模中,基模上方是冲压机的冲头,然后另一名工作人员采用长钳夹住尺寸小于基模的模套套接在毛胚料上,模套内部为内凹弧形面,最后通过上方的冲头向下冲压模套,实现圆柱形毛胚料端部在模套的内凹弧形面的规矩下整圆,完成毛胚料的一端整圆后,工作人员将模套向上移出,方便另一名工作人员接着采用长钳子将毛胚料翻个,接着对另一端进行冲压整圆,如果需要提高圆润度,可以多次重复上述步骤,对毛胚料各个角度进行模具整圆,得到了合金球粗产品,最后工作人员再通过长钳子夹持合金球粗产品转移放入到收料筒内。
5.虽然上述操作步骤能够确保毛胚料的整圆具有一定圆润度,但是通过人工的方式,进行向高温加热设备投料、从高温加热设备转移物料至基模中、人工对模具翻个、人工对模套夹持向上移出基模、人工下料等,此外,该种操作步骤需要两个人默契搭配好,尤其在自动设定好冲头向下冲压时间间隔,需要工作人员及时调整好毛胚料以及放置好模套在毛胚料上面,因而传统的方式灵活度不高,且劳动成本较大。
技术实现要素:6.本发明的第一目的在于针对现有技术存在的不足,提供一种合金球整圆自动加工生产线,开辟了合金球加工中传统人工方式往机械自动化发展,加工构思新颖巧妙,自动化程度高。
7.本发明解决上述技术问题的技术方案如下:一种合金球整圆自动加工生产线,包括高频加热机、工作台、设置于工作台一侧冲压机,设置于工作台上方且位于冲压机冲头正下方的模组、设置于工作台一侧的收料筒,所述高频加热机一侧设置有自动加料的振动盘和用于推动物料前移的驱动缸,所述高频加热机与模组之间设置有上料夹具,所述工作台一侧设置有控制模组合模与分模的夹持机构,所述工作台与收料筒之间设置有下料夹具。
8.采用上述技术方案,振动盘向高频加热机加料,高频加热机对毛胚料加热至红可锻造,驱动缸驱动毛胚料进给到上料夹具内,上料夹具将毛坯料转移到模组内,夹持机构操作模组合模与分模,只需要一名工作人员对模组内的毛坯料翻个即可,完成冲压整圆后,下料模具可以对粗产品下料,整个合金球加工工艺中逐步由传统人工方式往机械自动化发
展,加工构思新颖巧妙,自动化程度大大提高。
9.本发明进一步地,所述高频加热机包括有轨道托盘,所述振动盘设置有倾斜式的轨道筒,所述轨道筒的出口与轨道托盘的尾部相连接,所述驱动缸设置于轨道托盘的尾部且驱动缸对准轨道托盘,所述轨道筒与轨道托盘呈角度设置。
10.采用上述技术方案,振动盘将物料上料至轨道筒内,当驱动缸的动力作用下逐个将轨道托盘前端的物料推出过程中,轨道筒内的物料自由落入到轨道托盘内。
11.本发明进一步地,所述轨道托盘的前部设置有挡料板、前部下方设置有盛料板,所述挡料板与轨道托盘前部形成有供物料翻转的容纳空间,所述盛料板与轨道托盘的下部形成有支撑物料的盛料空间。
12.采用上述技术方案,方便物料翻转后盛接。
13.本发明进一步地,所述上料夹具包括上料同步带输送机和上料夹爪气缸,所述上料夹爪气缸位于盛料空间内,所述上料同步带输送机位于工作台与轨道托盘之间。
14.采用上述技术方案,将被盛接在盛料空间的物料转移至工作台处,即模组内。
15.本发明进一步地,所述夹持机构包括水平气缸、竖直气缸和夹持夹爪气缸,所述水平气缸固定连接于工作台一侧,所述升降气缸固定连接于水平气缸,所述夹持夹爪气缸固定连接于升降气缸。
16.采用上述技术方案,当上料夹具将物料转移至模组内后,水平气缸驱动夹持夹爪气缸靠近模组,升降气缸驱动水平气缸和夹持夹爪气缸下降并夹住控制模组,操作完成后,夹持夹爪气缸松开模组,升降气缸抬升水平气缸和夹持夹爪气缸移开模组,而后方便下料。
17.本发明进一步地,所述下料夹具包括下料同步带输送机和下料夹爪气缸,所述下料夹爪气缸位于模组一侧,所述下料同步带输送机位于工作台与收料筒之间。
18.采用上述技术方案,下料夹爪气缸夹住物料后,下料同步带输送机将下料夹爪气缸和物料转移至收料筒处,而后下料夹爪气缸松开进行下料。
19.本发明进一步地,所述模组包括模体、基模和模套,所述模体固定连接于工作台,所述模体与基模呈固定设置,所述基模与模套呈套接设置,所述模套下部内凹且向下设置,所述基模底部对应于模套的两侧设置有顶出孔,顶出孔内设置有第一顶杆和第二顶杆,第一顶杆和第二顶杆受外动力在顶出孔内向上滑动以顶出模套;所述第一顶杆内侧设置有抵接物料的抵块,所述第二顶杆包括定位杆、滑出顶出孔后可相对定位杆移动的移动杆、以及用于连接定位杆和移动杆的链接件;所述基模内存在供移动杆移动后的暂存空间,从而获得供物料以抵块为支点转动的转动空间,所述模体设置有拨动机构,当外动力驱动第一顶杆和第二顶杆将模套顶出基模后,拨动机构受外动力驱动移动杆移动至暂存空间;所述第一顶杆位于抵块处设置有容纳槽,所述抵块转动连接于容纳槽内,且所述抵块横穿有转动轴,所述转动轴与容纳槽之间设置有扭簧。
20.采用上述技术方案,模套上方冲压机对模套冲压,实现对圆柱形物料在模套内凹面处整圆后,下方动力驱动第一顶杆和第二顶杆向上移动,第一顶杆和第二顶杆的上端抵触模套底面并将模套顶起,第一顶杆上移在将模套顶起过程中,抵块逐渐向上移动并抵触到物料底部边处,由于物料的侧面受到第二顶块的限制,以及物料的上部受到模套的限制,所以抵块能够将物料顶起,当第一顶杆和第二顶杆将模套顶出基模后,下方动力驱动拨动机构运作,拨动机构拉动移动杆往基模移动,移动后移动杆位于暂存空间处,实现物料的一
侧存在空间将不受到移动杆的限制,外部夹具将模套夹住,下方动力再驱动第一顶杆和第二顶杆下移使得模套的水平移出不受到物料限制,从而也使得物料以抵块为支点进行转动90度,因为物料用于制作合金球,因此圆柱形物料长度较小,方便在移动杆小幅度移动后的存在空间能够实现物料旋转;当完成翻转后,下方动力再驱动第一顶杆和第二顶杆向下移动,期间拨动机构也完成复原,一次自动化转动完成,然后进行第二次模套的下压整形,该方式相比于传统的人工采用钳子夹持物料翻转,自动化水平提高,安全系数也提高。
21.本发明进一步地,所述拨动机构包括上部具有齿部且受外动力先上移动的第三顶杆、转动连接于模体内部且与齿部适配的半齿轮、固定连接于半齿轮底部的弹簧、安装于弹簧下端的滑块、设置于滑块下方且具有斜坡面的滑台、以及联动连接于滑块的联动件,所述移动杆与联动件的一端呈卡接配合;所述滑台具有水平面,所述滑块抵触到水平面时,所述弹簧与竖直面的夹角为10
‑
15
°
;所述滑块包括滑动部和摩擦部,所述滑动部底部设置有转动轮,所述摩擦部设置有摩擦片,所述斜坡面为向上的凹形面。
22.采用上述技术方案,第三顶杆受到下方动力的驱动进而其上的齿部驱动半齿轮转动,半齿轮带动弹簧转动,滑块在滑台上滑动,在弹簧继续转动过程中当滑块遇到斜坡面,此时弹簧弹性势能释放,滑块直接沿着斜坡面向下弹出,并通过联动件将移动杆向一侧拉动,实现移动杆和定位杆的远离,弹簧释放弹性势能完全时,移动杆位于暂存空间内;当物料完成翻转后,齿部反向驱动半齿轮反转,然后滑块反向滑动,于此弹簧反向旋转并蓄力,最后越过斜坡面恢复原状,等待下一次动作。
23.本发明进一步地,所述联动件包括转动连接于滑块的联杆一和连接于联杆一的联杆二,所述移动杆竖直方向上开设有导槽,所述联杆二背离联杆一的一端转动连接于滑轮,所述滑轮卡接且滑动连接于导槽内;所述联杆一的一侧设置有轨道轮,所述模体设置有轨道槽,所述轨道轮滑动连接于轨道槽内;所述链接件包括转动设置的链接杆一和链接杆二,所述链接杆一转动连接于移动杆内,所述链接杆二转动连接于定位杆内。
24.采用上述技术方案,当滑块拉动联杆一和联杆二过程中,包括竖直移动和水平移动,而设置的导槽配合滑轮主要是迎合竖直上的位移,避免卡死,移动杆在移动过程中在水平方向发生位移,而定位杆位于基模内,因此两者发生了错开,发明采用链接杆一和链接杆二的衔接方式实现了两者的距离发生变化,避免了卡死。
25.本发明的第二目的在于针对现有技术存在的不足,提供一种合金球整圆自动加工生产线的加工方法,提高了物料加工的圆润度,以及提高了自动化程度,降低劳动力。
26.本发明解决上述技术问题的技术方案如下:一种合金球整圆自动加工生产线的加工方法,步骤s1,投料,向振动盘内加入物料;步骤s2,高频加热,振动盘上轨道筒内的物料进入到轨道托盘内高温加热;步骤s3,自动备料,驱动缸推动轨道托盘内的物料进入到盛料空间内待定;步骤s4,自动上料,采用上料夹具将物料转移到模组内;步骤s5,冲压整圆,采用夹持机构控制模组便于冲压机对物料进行冲压整圆;步骤s6,自动下料,采用下料夹具将物料转移到收料筒内。
27.采用上述技术方案:振动盘向高频加热机加料,高频加热机对毛胚料加热至红可锻造,驱动缸驱动毛胚料进给到盛料空间内方便上料夹具夹取物料,上料夹具将毛坯料转移到模组内,夹持机构操作模组合模与分模,只需要一名工作人员对模组内的毛坯料翻个即可,完成冲压整圆后,下料模具可以对粗产品下料,整个合金球加工工艺中逐步由传统人
工方式往机械自动化发展,加工构思新颖巧妙,自动化程度大大提高。
附图说明
28.图1为实施例3的结构示意图;图2为实施例3用于展示振动盘和高频加热机的结构示意图;图3为图2的x部结构示意图;图4为图1的y部结构示意图;图5为实施例3用于展示上料夹具和下料夹具的示意图;图6为实施例3用于展示上料夹具的组成视图;图7为实施例3的另一角度结构示意图;图8为实施例3用于展示夹持机构的组成视图;图9为实施例3用于展示模组的结构示意图;图10为实施例3的模组去除部分模体后的立体图;图11为实施例3用于展示模组的剖视图;图12为实施例3用于展示第一顶杆处抵块的示意图;图13为实施例3用于展示导槽和导轮的示意图;图14为图13的a部放大图。
29.附图标记:1、振动盘;100、轨道筒;101、驱动缸;102、顶针;103、导向孔;2、高频加热机;200、轨道托盘;201、导电铜管;202、石英管;203、挡料板;204、盛料板;205、盛料空间;3、冲压机;300、工作台;4、上料夹具;400、上料夹爪气缸;401、上料同步带输送机;5、夹持机构;500、水平气缸;501、竖直气缸;502、夹持夹爪气缸;6、下料夹具;600、下料夹爪气缸;601、下料同步带输送机;7、收料筒;8、收料斗;9、支撑架;10、模体;11、基模;1100、顶出孔;1101、凹弧面;12、模套;13、第一顶杆;1300、抵块;1301、容纳槽;1302、转动轴;1303、扭簧;14、第二顶杆;1400、定位杆;1401、移动杆;1402、链接杆一;1403、链接杆二;1404、轨道轮;1405、轨道槽;15、暂存空间;16、拨动机构;1600、第三顶杆;1601、齿部;1602、半齿轮;1603、弹簧;1604、滑块;16040、滑动轮;16041、摩擦部;1605、滑台;16050、水平面;16051、斜坡面;1607、联杆一;1608、联杆二;1609、导槽;1610、滑轮;17、物料;18、油缸。
具体实施方式
30.下面对本发明实施例中的技术方案进行清楚、完整地描述,显然,所描述的实施例仅仅是本发明一部分实施例,而不是全部的实施例。基于本发明中的实施例,本领域普通技术人员在没有做出创造性劳动前提下所获得的所有其他实施例,都属于本发明保护的范围。
31.参见图1,实施例1,一种合金球整圆自动加工生产线,按照加工工序,包括高频加热机2、工作台300、设置于工作台300一侧冲压机3,设置于工作台300上方且位于冲压机3冲头正下方的模组、设置于工作台300一侧的收料筒7。
32.参见图1
‑
4,振动盘1设置有倾斜式的轨道筒100,高频加热机2包括有轨道托盘200、石英管202和导电铜管201,轨道托盘200前端与石英管202连接,导电铜管201外绕于石英管202,轨道筒100的出口与轨道托盘200的尾部相连接,轨道筒100内的物料17进入到轨
道托盘200内,轨道托盘200内的物料17进入到石英管202内,物料17在石英管202内通过导电铜管201实现受热增温变红,设置石英管202一定倾斜角度,使得物料17需要在作用力下才能够前移,无法自行因重力下料。在高频加热机2一侧设置有自动加料的振动盘1和用于推动物料17前移的驱动缸101,驱动缸101固定安装在支撑台上,驱动缸101设置于轨道托盘200的尾部且驱动缸101对准轨道托盘200,轨道筒100与轨道托盘200呈角度设置。驱动缸101的活塞杆固定连接有传动板,传动板的上端固定连接有顶针102,驱动缸101的前侧还设置有导向板,导向板的上部开设有导向孔103,顶针102穿过导向孔103。驱动缸101驱动顶针102向前移动使得物料17向前挪动,顶针102复位后,于此在轨道托盘200的尾部形成一个空位,轨道筒100内的物料17在重力作用下或者是振动盘1动力作用下自由掉落到空位内。
33.轨道托盘200的前部设置有挡料板203、前部下方设置有盛料板204,挡料板203与轨道托盘200前部形成有供物料17翻转的容纳空间,盛料板204与轨道托盘200的下部形成有支撑物料17的盛料空间205;振动盘1将物料17上料至轨道筒100内,当驱动缸101的动力作用下逐个将轨道托盘200前端的物料17推出过程中,轨道筒100内的物料17自由落入到轨道托盘200内。
34.参见图1,图5
‑
图8,高频加热机2与模组之间设置有上料夹具4,工作台300一侧设置有控制模组合模与分模的夹持机构5,工作台300与收料筒7之间设置有下料夹具6。具体如下设置:上料夹具4包括上料同步带输送机401和上料夹爪气缸400,上料夹爪气缸400位于盛料空间205内,上料同步带输送机401位于工作台300与轨道托盘200之间,下料夹具6包括下料同步带输送机601和下料夹爪气缸600,下料夹爪气缸600位于模组一侧,下料同步带输送机601位于工作台300与收料筒7之间,而夹持机构5包括水平气缸500、竖直气缸501和夹持夹爪气缸502,水平气缸500固定连接于工作台300一侧,升降气缸固定连接于水平气缸500,夹持夹爪气缸502固定连接于升降气缸,当上料夹具4将物料17转移至模组内后,水平气缸500驱动夹持夹爪气缸502靠近模组,升降气缸驱动水平气缸500和夹持夹爪气缸502下降并夹住控制模组,操作完成后,夹持夹爪气缸502松开模组,升降气缸抬升水平气缸500和夹持夹爪气缸502移开模组,而后方便下料,下料夹爪气缸600夹住物料17后,下料同步带输送机601将下料夹爪气缸600和物料17转移至收料筒7处,而后下料夹爪气缸600松开进行下料,为了方便收料,在收料筒7上方设置有收料斗8,收料斗8与收料筒7相互连通。
35.实施例1的上料同步带输送机401和下料同步带输送机601位于同一水平面16050上,两者安装在支撑架9上,方便设置安装,以及两者是同种工装,由此方便了更换。
36.该加工生产线的加工方法为步骤s1,投料,向振动盘1内加入物料17;步骤s2,高频加热,振动盘1上轨道筒100内的物料17进入到轨道托盘200内高温加热;步骤s3,自动备料,驱动缸101推动轨道托盘200内的物料17进入到盛料空间205内待定;步骤s4,自动上料,采用上料夹具4将物料17转移到模组内;步骤s5,冲压整圆,采用夹持机构5控制模组便于冲压机3对物料17进行冲压整圆;步骤s6,自动下料,采用下料夹具6将物料17转移到收料筒7内。振动盘1向高频加热机2加料,高频加热机2对毛胚料加热至红可锻造,驱动缸101驱动毛胚料进给到盛料空间205内方便上料夹具4夹取物料17,上料夹具4将毛坯料转移到模组内,夹持机构5操作模组合模与分模,只需要一名工作人员对模组内的毛坯料翻个即可,完成冲压整圆后,下料模具可以对粗产品下料,整个合金球加工工艺中逐步由传统人工方式往机械自动化发展,加工构思新颖巧妙,自动化程度大大提高。
37.实施例2,参见图9,前述的加工生产线中的合金球加工模组包括模体10、基模11和模套12,模体10设置在工作台300上,模体10由两部分组成,包括矩形空腔体和下部圆柱形空腔体。基模11固定连接于圆柱形空腔体的上部,并位于矩形空腔体的一侧。
38.参见9和图11,模套12下部内凹且向下设置,基模11底部设置内凹弧面1101;基模11底部对应于模套12的两侧设置有顶出孔1100,顶出孔1100内设置有第一顶杆13和第二顶杆14,第一顶杆13和第二顶杆14受外动力(例如油缸18)在顶出孔1100内向上滑动以顶出模套12;第一顶杆13内侧设置有抵接合金球的抵块1300,参见图12,第一顶杆13位于抵块1300处设置有容纳槽1301,抵块1300转动连接于容纳槽1301内,且抵块1300横穿有转动轴1302,转动轴1302与容纳槽1301之间设置有扭簧1303。容纳槽1301的底面与抵块1300相互临近,由此容纳槽1301的底面起到支撑抵块1300的作用。
39.参见图10和图11,第二顶杆14包括定位杆1400、滑出顶出孔1100后可相对定位杆1400移动的移动杆1401、以及用于连接定位杆1400和移动杆1401的链接件,链接件包括转动设置的链接杆一1402和链接杆二1403,链接杆一1402转动连接于移动杆1401内,链接杆二1403转动连接于定位杆1400内。移动杆1401竖直方向上开设有导槽1609,联杆二1608背离联杆一1607的一端转动连接于滑轮1610,滑轮1610卡接且滑动连接于导槽1609内。
40.基模11内存在供移动杆1401移动后的暂存空间15,且该空间实现了供合金球以抵块1300为支点进行转动(即当第一顶杆13将模套12顶出后,第一顶杆13上的抵块1300顶起物料17后、移动杆1401从物料17一侧移开后物料17不受到第二顶杆14抵触支撑,由此合金球会翻个)。
41.基模11还设置有拨动机构16,当外动力驱动第一顶杆13和第二顶杆14将模套12顶出基模11后,拨动机构16受外动力驱动移动杆1401移动至暂存空间15,具体为拨动机构16包括上部具有齿部1601且受外动力先上移动的第三顶杆1600、转动连接于基模11内部且与齿部1601适配的半齿轮1602、固定连接于半齿轮1602底部的弹簧1603、安装于弹簧1603下端的滑块1604,滑块1604包括滑动部和摩擦部16041,滑动部底部设置有滑动轮16040,摩擦部16041设置有摩擦片,斜坡面16051为向下的凹形面;滑块1604下方设置有具有斜坡面16051的滑台1605,滑台1605具有水平面16050,滑块1604抵触到水平面16050时,弹簧1603与竖直面的夹角为
‑°
。角度越小,更加稳定。本实施例中的摩擦片有利于避免在弹簧1603的弹性势能蓄力下发生移动,而凹形面避免了弹簧1603的弹性势能释放下滑块1604滑动在斜坡面16051上时,摩擦部16041与斜坡面16051发生摩擦,造成动作减缓。
42.参见图11、图13和图14,拨动机构16还包括联动连接于滑块1604的联动件,移动杆1401与联动件的一端呈卡接配合,联动件包括转动连接于滑块1604的联杆一1607和连接于联杆一1607的联杆二1608,联杆一1607的一侧设置有轨道轮1404,基模11设置有轨道槽1405,轨道轮1404滑动连接于轨道槽1405内,本实施例中依照滑块1604驱动联杆一1607的运动轨迹设置轨道槽1405,实现了联杆一1607在被驱动移动过程中稳定性。
43.在上述方案中,其一、当滑块1604拉动联杆一1607和联杆二1608过程中,包括竖直移动和水平移动,而设置的导槽1609配合滑轮1610主要是迎合竖直上的位移,避免卡死,图14中导槽1609的最边缘深度也能够限定滑轮1610滑移距离,由此保护了联杆一1607、弹簧1603等的最大移动距离;其二、移动杆1401在移动过程中在水平方向发生位移,而定位杆1400位于基模11内,因此两者发生了错开,发明采用链接杆一1402和链接杆二1403的衔接
方式实现了两者的距离发生变化,避免了卡死实施例2的加工方法:步骤s1,投料,向振动盘1内加入物料17;步骤s2,高频加热,振动盘1上轨道筒100内的物料17进入到轨道托盘200内高温加热;步骤s3,自动备料,驱动缸101推动轨道托盘200内的物料17进入到盛料空间205内待定;步骤s4,自动上料,采用上料夹具4将物料17转移到基模11内;步骤s5,冲压整圆,当上料夹具4将物料17转移至基模11内后,水平气缸500驱动夹持夹爪气缸502靠近模套12,升降气缸驱动水平气缸500和夹持夹爪气缸502下降并夹住模套12,并将模套12盖设在基模11上方,夹持夹爪气缸502松开并微小移开(避免冲头冲压时候,模套12动作而发生撞击),此时模套12在竖直方向自由,模套12上方冲压机3对模套12冲压,实现对圆柱形物料17在模套12内凹面处整圆,进行一次整圆后,下方动力驱动第一顶杆13和第二顶杆14向上移动,第一顶杆13和第二顶杆14的上端抵触模套12底面并将模套12顶起,方便夹持夹爪气缸502夹持,而在第一顶杆13上移在将模套12顶起过程中,抵块1300逐渐向上移动并抵触到物料17底部边处,由于物料17的侧面受到第二顶块的限制,以及物料17的上部受到模套12的限制,所以抵块1300能够将物料17顶起,当第一顶杆13和第二顶杆14将模套12顶出基模11后,下方动力驱动拨动机构16运作。拨动机构16的具体原理:第三顶杆1600受到下方动力的驱动进而其上的齿部1601驱动半齿轮1602转动,半齿轮1602带动弹簧1603转动,滑块1604在滑台1605上滑动,在弹簧1603继续转动过程中当滑块1604遇到斜坡面16051,此时弹簧1603弹性势能释放,滑块1604直接沿着斜坡面16051向下弹出,并通过联动件将移动杆1401向一侧拉动,实现移动杆1401和定位杆1400的远离,弹簧1603释放弹性势能完全时,移动杆1401位于暂存空间15内;当物料17完成翻转后,齿部1601反向驱动半齿轮1602反转,然后滑块1604反向滑动,于此弹簧1603反向旋转并蓄力,最后越过斜坡面16051恢复原状,等待下一次动作。拨动机构16拉动移动杆1401往基模11移动,移动后移动杆1401位于暂存空间15处,实现物料17的一侧存在空间将不受到移动杆1401的限制,外部夹具将模套12夹住,下方动力再驱动第一顶杆13和第二顶杆14下移使得模套12的水平移出不受到物料17限制,从而也使得物料17以抵块1300为支点进行转动度,因为物料17用于制作合金球,因此圆柱形物料17长度较小,方便在移动杆1401小幅度移动后的存在空间能够实现物料17旋转;当完成翻转后,下方动力再驱动第一顶杆13和第二顶杆14向下移动,期间拨动机构16也完成复原,一次自动化转动完成,然后进行第二次模套12的下压整形,该方式相比于传统的人工采用钳子夹持物料17翻转,自动化水平提高,安全系数也提高,操作完成后,水平气缸500运作,方便夹持夹爪气缸502夹持模套12,升降气缸抬升水平气缸500和夹持夹爪气缸502带着模套12移开基模11,而后方便下料。步骤s6,自动下料,采用下料夹具6将物料17转移到收料筒7内。
44.实施例3,除此之外,为了方便取料,进行如下设置:第一顶杆13和第二顶杆14受外动力在顶出孔1100内向上滑动以顶过模套12表面时,第三顶杆1600上的齿部1601与半齿轮1602开始啮合,因为第一顶杆13和第二顶杆14受外动力在顶出孔1100内向上滑动以顶过模套12表面时,第三顶杆1600上的齿部1601与半齿轮1602开始啮合,此时移动杆1401还未移动,继续向上驱动第一顶杆13、第二顶杆14和第三顶杆1600向上移动,当半齿轮1602转动过一定角度后,滑块1604进入到斜坡面16051上,此时在弹性势能下快速下移,移动杆1401移动,此时模套12已经距离基模11上面一定距离,且外部夹持机构5夹住模套12,接着再向下驱动第一顶杆13、第二顶杆14和第三顶杆1600,物料17脱离模套12,而移动杆1401也腾出空
间,达到物料17翻转,这是正常的冲压整形和翻转的过程;当冲压整形完成后,需要出料时,采用在第一顶杆13和第二顶杆14受外动力在顶出孔1100内向上滑动以顶过模套12表面时,第三顶杆1600上的齿部1601与半齿轮1602开始啮合,此时外部夹持机构5夹持住模套12,此时不再对第一顶杆13、第二顶杆14和第三顶杆1600进行向上顶,也就是不驱动半齿轮1602转动,也就是出料操作是移动杆1401不移动,反而采用对第一顶杆13、第二顶杆14和第三顶杆1600向下拉,方便外部夹持机构5将模套12移开,移开后,物料17通过抵块1300和移动杆1401的抵触支撑,不会往下掉落,而后上方采用下料夹爪气缸600将物料17夹持,因为物料17处于基模11的较上方位置,相比于直接掉落到基模11下部,使得下料夹爪气缸600夹取物料17得以实现,下料夹爪气缸600夹住物料17后,下料同步带输送机601将下料夹爪气缸600和物料17转移至收料筒7处,而后下料夹爪气缸600松开进行下料。除了该种取料方式之外,也可以采用吸料罩将物料17吸走,同样因为物料17处于基模11的较上方位置,相比于直接掉落到基模11下部,使得吸料罩更加容易吸料。
45.以上所述仅为本发明的较佳实施例,并不用以限制本发明,凡在本发明的精神和原则之内,所作的任何修改、等同替换、改进等,均应包含在本发明的保护范围之内。