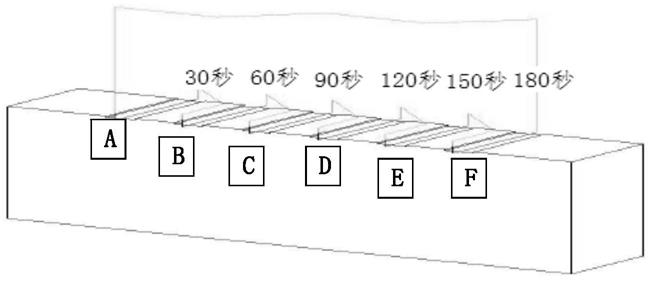
nc主轴动态伸长量的检测方法
技术领域
1.本发明涉及cnc机床加工技术领域,尤其涉及一种nc主轴动态伸长量的检测方法。
背景技术:2.目前所有cnc数控加工设备,在加工的过程中因为主轴长时间的高速运转,机床z轴会产生一定量的热变形,这个变形量会根据主轴运转的转数与时间的长短而变化,最后达到一个稳定的峰值维持不变。如果不能掌握这个变量值,加工容易产生台阶,甚至过切。
技术实现要素:3.为了克服现有技术的不足,本发明的目的在于提供一种nc主轴动态伸长量的检测方法,其可找到机床在不同的运转时间产生的变形量,从而根据机床要加工的时间长短,给予前期变形量预调整,来保证工件加工后的尺寸精度要求。
4.本发明的目的采用以下技术方案实现:
5.nc主轴动态伸长量的检测方法,包括,
6.步骤一,在工件加工面上设定连续的若干加工点,若干加工点在 nc主轴的x轴或者y轴上依次分布;
7.步骤二,nc主轴在各个加工点进行z轴方向的加工;相邻两个加工点的加工时间间隔为t;
8.步骤三,测量各个加工点在z轴方向的加工深度d1,比较相邻两个加工点的加工深度。
9.进一步地,步骤一中,在工件加工面上设定六个加工点,依次标记为加工点a、加工点b、加工点c、加工点d、加工点e、加工点 f,加工点a、加工点b、加工点c、加工点d、加工点e、加工点f 在x轴或者y轴方向依次分布;nc主轴在加工点a、加工点b、加工点c、加工点d、加工点e、加工点f依次加工。
10.进一步地,步骤二中的t为30s;nc主轴在加工点a的加工时间为30s,nc主轴在加工点b的加工时间为60s,nc主轴在加工点c的加工时间为90s,nc主轴在加工点d的加工时间为120s,nc 主轴在加工点e的加工时间为150s,nc主轴在加工点f的加工时间为180s。
11.进一步地,重复步骤二以及步骤三,每次加工过程中,步骤二中的nc主轴的加工转速不同。
12.进一步地,所述步骤三中,cnc机床内预设加工深度值d2,nc 主轴根据预设加工深度值d2进行加工,记录各个加工点的实际加工深度值与预设加工深度值为d3,d3=d2
‑
d1。
13.进一步地,步骤三中,根据各个加工点的d3值绘制曲线图,曲线图的曲线开始趋于稳定,则nc主轴伸长量趋于稳定。
14.进一步地,步骤三中,用测高仪测量加工点的加工深度。
15.进一步地,步骤一中,nc主轴在x轴或者y轴方向行进时,不与工件或者cnc机床接触。
16.相比现有技术,本发明的有益效果在于:其可通过cnc机床控制nc主轴,在不同的位置,给定不同的转速和空转停留不同的时间,然后对不同的位置行进铣切,之后对铣切工件的加工位置进行高度测量,得出结果分析出结论。如此,找到cnc机床的nc主轴在不同的转数和不同的运转时间产生的变形量,从而根据机床要加工的时间长短,给予前期变形量预调整,来保证工件加工后的尺寸精度要求。
附图说明
17.图1为本发明的工件加工面上的加工点设定的结构示意图;
18.图2为本发明的各个加工点配合加工时间绘制的曲线图。
具体实施方式
19.下面,结合附图以及具体实施方式,对本发明做进一步描述:
20.本发明的nc主轴动态伸长量的检测方法,包括,
21.步骤一,在工件加工面上设定连续的若干加工点,若干加工点在 nc主轴的x轴或者y轴上依次分布;
22.步骤二,nc主轴在各个加工点进行z轴方向的加工;相邻两个加工点的加工时间间隔为t;
23.步骤三,测量各个加工点在z轴方向的加工深度d1,比较相邻两个加工点的加工深度。
24.本实施例中,nc主轴可在cnc机床上沿y轴方向行进,在y 轴方向上的第一个加工点进行加工后,在行进至第二个加工点进行加工,然后再行进至下个点,直至完成最后一个加工点的加工,在此过程中,nc主轴会逐渐产生热形变拉长,在各个加工点的加工深度会逐渐超过预定的加工深度,将相邻两个的加工点的加工深度进行对比,便可得出nc主轴从哪个加工点开始发生形变,且形变量开始变大并逐渐趋于稳定。
25.参见图1,本实施例中的步骤一中,可在工件加工面上设定六个加工点,依次标记为加工点a、加工点b、加工点c、加工点d、加工点e、加工点f,加工点a、加工点b、加工点c、加工点d、加工点e、加工点f在x轴或者y轴方向依次分布;nc主轴在加工点 a、加工点b、加工点c、加工点d、加工点e、加工点f依次加工。
26.进一步地,步骤二中的t为30s;nc主轴在加工点a的加工时间为30s,nc主轴在加工点b的加工时间为60s,nc主轴在加工点 c的加工时间为90s,nc主轴在加工点d的加工时间为120s,nc 主轴在加工点e的加工时间为150s,nc主轴在加工点f的加工时间为180s。
27.加工后对a
‑
f六个点的位置进行检测,测量其深度差,同时结合在各个点的加工时间进行分析,即可得出nc主轴伸长量在哪个时间点有变化,以及加工多久后开始趋于稳定。
28.进一步地,重复步骤二以及步骤三,每次加工过程中,步骤二中的nc主轴的加工转速不同。
29.具体的是,将初始nc主轴转速设定5000转/min,在a点到f 点,停留一定时间后进行切削,之后移动到下一点,停留再切削不断重复,直到结束。
30.从a
‑
f加工都是连续的,中途不对机器和工件产生任何接触,
31.加工后对a
‑
f六个点的位置进行检测,测量其深度差,即可得出其主轴伸长量在何
时有变化,到多久后开始趋于稳定。
32.此后,之后换另外的转速,重复上述动作,即可得到相应的转速在nc主轴的热伸长量在加工多久后开始趋于稳定的结论。
33.如此,可通过cnc机床控制nc主轴,在不同的位置,给定不同的转速和空转停留不同的时间,然后对不同的位置行进铣切,之后对铣切工件的加工位置进行高度测量,得出结果分析出结论。如此,找到cnc机床的nc主轴在不同的转数和不同的运转时间产生的变形量,从而根据机床要加工的时间长短,给予前期变形量预调整,来保证工件加工后的尺寸精度要求。
34.步骤三中,cnc机床内预设加工深度值d2,nc主轴根据预设加工深度值d2进行加工,记录各个加工点的实际加工深度值与预设加工深度值为d3,d3=d2
‑
d1,根据d3值可显示相邻两点的形变量变化大小。当然,可在cnc机床控制系统的控制器内预设上述加工深度值,该d2值为理论加工值,因而在与实际加工值对比后,便可得出nc主轴的形变量。
35.进一步地,步骤三中,将上述加工点a
‑
f各点得出的d3配合各点的加工时间,绘制曲线图表(参见图2),根据图表上曲线,可更加直观的观察在什么加工时间点,nc主轴伸长量趋于稳定。
36.进一步地,步骤三中,用测高仪测量加工点的加工深度,具体测高仪可选用为现有技术中的红外测高仪,测量精度更高。
37.进一步地,步骤一中,nc主轴在x轴或者y轴方向行进时,不与工件或者cnc机床接触,防止外部环境对整个加工过程造成干扰。
38.对本领域的技术人员来说,可根据以上描述的技术方案以及构思,做出其它各种相应的改变以及形变,而所有的这些改变以及形变都应该属于本发明权利要求的保护范围之内。