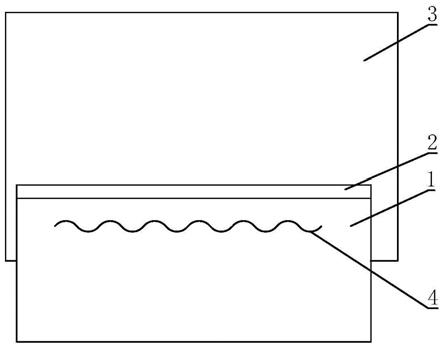
1.本发明涉及异种金属焊接技术领域,尤其涉及一种锂电池极耳用双层铝合金与镀镍铜的焊接工艺。
背景技术:2.铜具有良好的加工性能、耐磨及耐蚀性能等优点,镍具有化学活性低、耐蚀性强、强度高、韧性好等优点,镍与铜结合,不管是在液态还是固态,都能够无限互熔,这增强了铜的材料性能和焊接性能。铝合金具有质量轻、耐腐蚀等优点。目前,镀镍铜和铝合金已广泛用于锂电池极耳。但铜合金难熔合,易变性,易产生气孔,非常容易生成低熔点的共晶物,出现热裂纹,且铝合金的焊接性能较差,极易形成致密的三氧化二铝氧化膜吸附水分,造成焊缝裂纹等缺陷。
3.目前,锂电池极耳中双层铝合金层与镀镍铜层的焊接通常使用yag(钇铝石榴石)脉冲激光器。yag脉冲激光器光斑较大,焦点处热量不如单模激光器集中,生产效率较低并且焊缝易产生裂纹以及晶粒粗大等现象,严重影响焊接接头的抗拉抗剪性能。因此,亟需一种新的锂电池极耳用双层铝合金与镀镍铜的焊接工艺。
技术实现要素:4.本发明要解决的技术问题是提供一种锂电池极耳用双层铝合金与镀镍铜的焊接工艺,能够减少焊接缺陷、改善焊接性能,以克服现有技术的上述缺陷。
5.为了解决上述技术问题,本发明采用如下技术方案:一种锂电池极耳用双层铝合金与镀镍铜的焊接工艺,依次包括以下步骤:步骤一、选取一组待焊接的样件,样件包括第一铝合金层、第二铝合金层和镀镍铜层;步骤二、对样件进行清洗,然后将第一铝合金层、第二铝合金层和镀镍铜层从上至下依次叠放并固定;步骤三、编辑焊接轨迹曲线:将一条直线轨迹曲线异化为正弦曲线,并将正弦曲线再次曲线异化,形成焊接轨迹曲线;步骤四、采用激光焊接装置按焊接轨迹曲线对样件进行焊接;步骤五、对焊接完成后的样件进行检测。
6.优选地,在步骤一中,第一铝合金层的厚度为0.2mm
‑
0.3mm,第二铝合金层的厚度为0.2mm
‑
0.3mm,镀镍铜层的厚度为3mm
‑
4mm。
7.优选地,在步骤二中,采用无水酒精对第一铝合金层、第二铝合金层和镀镍铜层的贴合表面及待焊接表面进行擦拭清洗。
8.优选地,在步骤二中,第一铝合金层与第二铝合金层的贴合面之间的间隙、第二铝合金层与镀镍铜层的贴合面之间的间隙均不大于0.1mm。
9.优选地,在步骤三中,正弦曲线的周期为6mm
‑
8mm、振幅为1.2mm
‑
1.4mm。
10.优选地,在步骤三中,正弦曲线再次曲线异化的异化周期为0.2mm
‑
0.3mm、异化振幅为0.3mm
‑
0.4mm。
11.优选地,在步骤四中,焊接时的焊接激光功率为1100w
‑
1300w。
12.优选地,在步骤四中,焊接开始时,激光焊接装置的激光功率在0.5秒内从0w上升
至焊接激光功率,然后保持焊接激光功率至焊接结束。
13.优选地,在步骤四中,激光焊接装置的焊接参数为:光斑直径0.02mm
‑
0.05mm,氮气流量15l/min
‑
20l/min,离焦量
‑
2mm
‑
+1mm,焊接速度350mm/s
‑
450mm/s。
14.优选地,在步骤四中,焊接时样件背面的温度不超过260℃。
15.与现有技术相比,本发明具有显著的进步:
16.本发明的锂电池极耳用双层铝合金与镀镍铜的焊接工艺,通过将一条直线轨迹曲线异化为正弦曲线,并将正弦曲线再次曲线异化,形成焊接轨迹曲线,按照这种焊接轨迹曲线进行焊接,能够有效减少裂纹出现率和虚焊率,避免产生焊接缺陷,增加样件焊接后的抗拉强度,保证焊接性能。
附图说明
17.图1是本发明实施例锂电池极耳用双层铝合金与镀镍铜的焊接工艺中,样件及焊接位置示意图。
18.图2是本发明实施例锂电池极耳用双层铝合金与镀镍铜的焊接工艺中,焊接轨迹曲线示意图。
19.图3是图2中a部的放大示意图。
20.其中,附图标记说明如下:
[0021]1ꢀꢀꢀꢀꢀꢀꢀꢀꢀꢀꢀꢀꢀꢀꢀꢀꢀ
第一铝合金层
[0022]2ꢀꢀꢀꢀꢀꢀꢀꢀꢀꢀꢀꢀꢀꢀꢀꢀꢀ
第二铝合金层
[0023]3ꢀꢀꢀꢀꢀꢀꢀꢀꢀꢀꢀꢀꢀꢀꢀꢀꢀ
镀镍铜层
[0024]4ꢀꢀꢀꢀꢀꢀꢀꢀꢀꢀꢀꢀꢀꢀꢀꢀꢀ
焊缝
[0025]5ꢀꢀꢀꢀꢀꢀꢀꢀꢀꢀꢀꢀꢀꢀꢀꢀꢀ
焊接轨迹曲线
具体实施方式
[0026]
下面结合附图对本发明的具体实施方式作进一步详细说明。这些实施方式仅用于说明本发明,而并非对本发明的限制。
[0027]
在本发明的描述中,需要说明的是,术语“中心”、“纵向”、“横向”、“上”、“下”、“前”、“后”、“左”、“右”、“竖直”、“水平”、“顶”、“底”“内”、“外”等指示的方位或位置关系为基于附图所示的方位或位置关系,仅是为了便于描述本发明和简化描述,而不是指示或暗示所指的装置或元件必须具有特定的方位、以特定的方位构造和操作,因此不能理解为对本发明的限制。此外,术语“第一”、“第二”仅用于描述目的,而不能理解为指示或暗示相对重要性。
[0028]
在本发明的描述中,需要说明的是,除非另有明确的规定和限定,术语“安装”、“相连”、“连接”应做广义理解,例如,可以是固定连接,也可以是可拆卸连接,或一体地连接;可以是机械连接,也可以是电连接;可以是直接相连,也可以通过中间媒介间接相连,可以是两个元件内部的连通。对于本领域的普通技术人员而言,可以根据具体情况理解上述术语在本发明中的具体含义。除非另有说明,“多个”的含义是两个或两个以上。
[0029]
如图1至图3所示,本发明的锂电池极耳用双层铝合金与镀镍铜的焊接工艺的一种实施例。本实施例的锂电池极耳用双层铝合金与镀镍铜的焊接工艺依次包括以下步骤。
[0030]
步骤一、选取一组待焊接的样件,样件包括第一铝合金层1、第二铝合金层2和镀镍铜层3。具体为选取合适牌号、尺寸和规格的铝合金材料和镀镍铜材料分别作为锂电池极耳制作中待焊接的第一铝合金层1、第二铝合金层2和镀镍铜层3。优选地,第一铝合金层1的厚度为0.2mm
‑
0.3mm,第二铝合金层2的厚度为0.2mm
‑
0.3mm,镀镍铜层3的厚度为3mm
‑
4mm。优选地,镀镍铜层3的镀镍铜材料规格为t2紫铜镀镍,镍牌号为n6。
[0031]
步骤二、在进行焊接前,先对样件进行清洗,优选地,采用无水酒精对第一铝合金层1、第二铝合金层2和镀镍铜层3的贴合表面及待焊接表面进行擦拭清洗,去除表面油污,以保证焊接后的产品性能。然后,如图1所示,将第一铝合金层1、第二铝合金层2和镀镍铜层3从上至下依次叠放并固定,即将第一铝合金层1放在第二铝合金层2的上表面,再将第二铝合金层2放在镀镍铜层3的上表面。则样件的贴合表面包括第一铝合金层1的下表面、第二铝合金层2的上表面、第二铝合金层2的下表面和镀镍铜层3的上表面,样件的待焊接表面为第一铝合金层1的上表面。叠放时各合金层之间不得有杂物。叠放好后的样件的固定可以通过夹具实现,利用夹具施加压力将第一铝合金层1和第二铝合金层2压固在镀镍铜层3上。夹具的形式并不局限,可以采用现有的夹具,例如可以采用现有的plc控制专用夹具如铜杯,施加20n
‑
30n的力将第一铝合金层1和第二铝合金层2压固在镀镍铜层3上。优选地,样件叠放并固定好后,第一铝合金层1与第二铝合金层2的贴合面之间的间隙、第二铝合金层2与镀镍铜层3的贴合面之间的间隙均不大于0.1mm,以避免产生裂纹和虚焊等焊接缺陷,确保焊接性能。在样件叠放并固定好后,确定样件上的焊接位置,如图1所示,焊缝4所在位置即为焊接位置。
[0032]
步骤三、编辑焊接轨迹曲线,编辑方法为:先编辑一条直线轨迹,然后将该直线轨迹曲线异化为正弦曲线,并将正弦曲线再次曲线异化,形成焊接轨迹曲线5,如图2和图3所示。其中,将直线轨迹曲线异化为正弦曲线时,优选地,正弦曲线的周期为6mm
‑
8mm、振幅为1.2mm
‑
1.4mm。将正弦曲线再次曲线异化是指将正弦曲线的线条再次异化为正弦曲线(参见图3),优选地,正弦曲线再次曲线异化的异化周期为0.2mm
‑
0.3mm、异化振幅为0.3mm
‑
0.4mm。由此最终形成的焊接轨迹曲线5如图2所示。按照这种焊接轨迹曲线5进行焊接,能够有效减少裂纹出现率和虚焊率,避免产生焊接缺陷,增加样件焊接后的抗拉强度,保证焊接性能。
[0033]
步骤四、采用激光焊接装置按焊接轨迹曲线5对叠放并固定好的样件上的焊接位置进行焊接。激光焊接装置为现有装置,例如可以采用现有的两轴伺服搭载激光振镜系统进行激光焊接。优选地,激光焊接装置所用的激光器为单模激光器,能够提升焊接速度,有效提高生产效率和生产合格率,节约生产成本。激光焊接装置可以采用的一种激光器的型号为mfsc
‑
2000c
‑
bjw3.0。优选地,焊接时样件背面的温度不超过260℃,以免影响样件焊接后的抗拉强度。
[0034]
优选地,焊接时的焊接激光功率为1100w
‑
1300w,以避免产生裂纹和虚焊等焊接缺陷,确保焊接性能。
[0035]
优选地,焊接开始时,激光焊接装置的激光功率在0.5秒内从0w上升至所需的焊接激光功率,然后保持焊接激光功率至焊接结束,该焊接结束是指一次焊接的焊缝结束,完成该次焊接。由此能够有效改善焊缝起始位置的性能和焊缝质量。
[0036]
优选地,激光焊接装置进行焊接时的焊接参数为:光斑直径0.02mm
‑
0.05mm,氮气
流量15l/min
‑
20l/min,离焦量
‑
2mm
‑
+1mm,焊接速度350mm/s
‑
450mm/s。由此可以获得最佳的焊缝质量。
[0037]
步骤五、对焊接完成后的样件进行检测。用显微镜观察焊缝表面,检测是否存在虚焊和焊缝表面裂纹;用万能试验机检测焊接完成后的样件的抗拉强度,焊接完成后的样件的抗拉强度应大于1400n,实际作业时焊接完成后的样件的抗拉强度大于2000n。
[0038]
下面,通过试验对本实施例的锂电池极耳用双层铝合金与镀镍铜的焊接工艺的焊接效果进行检验和验证。
[0039]
试验一、采用本实施例的锂电池极耳用双层铝合金与镀镍铜的焊接工艺,依照上述步骤,对10组待焊接的样件依次进行焊接,焊接完成后的检测结果见下表1。
[0040]
表1试验一的检测结果
[0041][0042]
可见,采用本实施例的锂电池极耳用双层铝合金与镀镍铜的焊接工艺,焊接合格率为100%,能够极大地保障焊接质量,从而有效提高生产效率、降低生产成本。
[0043]
试验二、对第一铝合金层1与第二铝合金层2的贴合面之间的间隙、第二铝合金层2与镀镍铜层3的贴合面之间的间隙大于0.1mm的情况进行试验,试验间隙值为0.12mm、0.14mm、0.16mm、0.18mm,每个间隙值各进行10组试验,每组试验中除上述间隙值外,其余参数及操作过程均与试验一相同,检测结果见下表2。
[0044]
表2试验二的检测结果
[0045][0046]
可见,当第一铝合金层1与第二铝合金层2的贴合面之间的间隙、第二铝合金层2与镀镍铜层3的贴合面之间的间隙大于0.1mm时,会出现焊缝裂纹、虚焊、焊接后的样件抗拉强度不合格的情况,并且,随着贴合面间隙的增大,各种缺陷的出现几率均呈上升趋势。因此,将第一铝合金层1与第二铝合金层2的贴合面之间的间隙、第二铝合金层2与镀镍铜层3的贴
合面之间的间隙控制在0.1mm以内,能够确保不产生裂纹、虚焊、抗拉强度不合格等焊接缺陷,保证焊接性能合格。
[0047]
试验三、对焊接时的焊接激光功率在1100w
‑
1300w范围之外的情况进行试验,试验焊接激光功率为1000w、1050w、1100w、1150w、1200w、1250w、1300w、1350w、1400w、1450w,每个焊接激光功率值各进行10组试验,每组试验中除上述焊接激光功率值外,其余参数及操作过程均与试验一相同,检测结果见下表3。
[0048]
表3试验三的检测结果
[0049][0050]
可见,当焊接激光功率低于1100w时,会出现虚焊,进而影响抗拉强度,导致焊接后的样件抗拉强度不合格;当焊接激光功率高于1300w时,焊缝会出现裂纹,焊接时样件背面的温度会超过260℃,进而影响抗拉强度,导致焊接后的样件抗拉强度不合格。而将焊接激光功率控制在1100w
‑
1300w范围之内,能够确保不产生裂纹、虚焊、焊接时样件背面的温度、抗拉强度不合格等焊接缺陷,保证焊接性能合格。
[0051]
综上所述,采用本实施例的锂电池极耳用双层铝合金与镀镍铜的焊接工艺,能够减少焊接缺陷,提升极耳的焊接速度,提高生产效率,降低成产成本,满足客户要求。
[0052]
以上所述仅是本发明的优选实施方式,应当指出,对于本技术领域的普通技术人员来说,在不脱离本发明技术原理的前提下,还可以做出若干改进和替换,这些改进和替换也应视为本发明的保护范围。