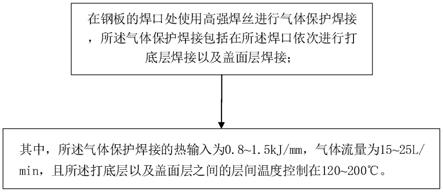
1.本申请属于金属冶炼方法技术领域,尤其涉及一种高强钢的焊接方法。
背景技术:2.高强钢因其具有高的强度和较好的塑韧性等优点,逐渐应用于工程机械、港口机械、煤矿机械等领域,如大吨位起重机吊臂、混凝土泵车的臂架、消防车泵车的臂架、高性能液压支架、超大吨位港口吊车等。由于轻量化要求越来越高,在降低自重、提高承载能力、降低运输安装成本等方面,高强钢有极大优势。高强度级别的低合金高强钢的应用,已经成为这些行业机械产品的卖点和优势。国内的钢厂,已经成功开发了屈服强度1300mpa级超高强钢。
3.现有工业生产中也有高强钢的焊接方法,但是,其采用的焊接工艺复杂,需要低强焊丝打底焊、高强钢焊丝填充焊、气刨清根、低强焊丝封底和盖面、焊后保温等工艺步骤。焊缝背面采用气刨等手段进行清根,然后再焊一道进行封底。此工艺一般用于采用y形坡口的关键焊缝,一方面,为了避免焊穿,所以采用钝边,另一方面,为了避免钝边焊不透,因此把焊缝背面清理出一个凹槽,然后焊满。工艺比较复杂,生产效率比较低。特别是焊接的过程中其中需要两次更换焊丝,严重影响生产效率,并且对于较高级别的高强钢的焊接,其焊接效果不理想,焊口位置的强度无法达到要求。
技术实现要素:4.本申请实施例的目的在于提供一种高强钢的焊接方法,以解决现有技术中存在的焊口强度低,焊接过程需要更换焊丝的技术问题。
5.为实现上述目的,本申请采用的技术方案是:提供一种高强钢的焊接方法,包括如下步骤:在钢板的焊口处使用高强焊丝进行气体保护焊接,所述气体保护焊接包括在所述焊口依次进行打底层焊接以及盖面层焊接;其中,所述气体保护焊接的热输入为0.8~1.5kj/mm,气体流量为15~25l/min,且所述打底层焊接以及盖面层焊接之间的层间温度控制在120~200℃。
6.根据本申请的一个实施例,所述气体保护焊接还包括填充层焊接,所述填充层焊接在打底层焊接以及盖面层焊接之间进行。
7.根据本申请的一个实施例,打底层焊接的参数为:焊接电压19~22v,焊接电流100~160a,焊接速度100~200mm/min。
8.根据本申请的一个实施例,填充层焊接以及盖面层焊接的参数为:焊接电压22~30v,焊接电流180~280a,焊接速度260~450mm/min。
9.根据本申请的一个实施例,所述钢板厚度小于或等于8mm时,所述气体保护焊接包括打底层焊接以及盖面层焊接;所述钢板厚度大于8mm时,所述气体保护焊接包括打底层焊接、填充层焊接以及盖面层焊接。
10.根据本申请的一个实施例,打底层焊接的厚度≤5mm,所述填充层焊接的厚度3~
4mm,所述盖面层焊接的厚度3~4mm。
11.根据本申请的一个实施例,高强焊丝的抗拉强度≥940mpa,形成的焊缝抗拉强度≥1200mpa。
12.根据本申请的一个实施例,高强焊丝采用实心焊丝或药芯焊丝,焊丝直径0.8~1.6mm。
13.根据本申请的一个实施例,所述钢板的焊口为v形坡口,所述焊口的间隙为1~4mm,所述v形坡口的角度为50~60
°
。
14.根据本申请的一个实施例,气体保护焊接之前,还包括对焊口进行预处理,预处理包括预热、打磨以及贴焊接衬垫。
15.本申请提供的高强钢的焊接方法的有益效果在于:本申请高强钢的焊接方法,采用高强焊丝进行焊接,通过严格控制热输入和层间温度在适当范围内,保证焊接材料的组织和晶粒度,从而保证焊缝获得良好的强韧性匹配。保证焊丝强度的同时具有一定的韧性,获得高强度、良好韧塑性能的焊接接头,并且光滑、无裂纹、气孔等缺陷,力学性能良好具有稳定的强度。同时,采用本方法生产的高强钢的焊接方法全程采用同一种高强钢焊丝,避免来回切换焊丝,操作简单,生产中易于执行,且可推广到自动化机器人焊接,实现高效生产。
附图说明
16.为了更清楚地说明本申请实施例中的技术方案,下面将对实施例或现有技术描述中所需要使用的附图作简单地介绍,显而易见地,下面描述中的附图仅仅是本申请的一些实施例,对于本领域普通技术人员来讲,在不付出创造性劳动性的前提下,还可以根据这些附图获得其他的附图。
17.图1为本申请实施例提供的高强钢的焊接方法的流程框图;
18.图2为本申请实施例提供的高强钢的焊接方法的坡口结构示意图;
19.图3为本申请实施例提供的高强钢的焊接方法的焊接层结构示意图。
20.其中,图中各附图标记:
[0021]1‑
钢板;2
‑
坡口;3
‑
焊口;d
‑
对口间隙;a
‑
板厚;α
‑
坡口角度;4
‑
打底层焊接;5
‑
盖面层焊接;6
‑
填充层焊接。
具体实施方式
[0022]
为了使本申请所要解决的技术问题、技术方案及有益效果更加清楚明白,以下结合附图及实施例,对本申请进行进一步详细说明。应当理解,此处所描述的具体实施例仅仅用以解释本申请,并不用于限定本申请。
[0023]
现有技术中的高强钢的焊接,一般采用低强焊丝打底,高强焊丝中间层填充焊接,气刨清根然后以低强焊丝进行盖面。打底和盖面使用低强焊丝是为了保证钢材的韧性,高强焊丝进行中间层的填充为了保证焊接的强度以及牢固性。然而盖面和打底处使用低强焊丝,导致该处强度无法达到焊接强度要求。并且这样的方法,焊接过程中需要更换焊丝,生产效率低下,而且焊接中低强焊丝的焊接效果不好。
[0024]
而本申请中的高强钢指的是屈服强度≥1300mpa的钢材,厚度6~12mm,其具有高的强度和较好的塑韧性等优点。但是尚未有对该等级的高强度的钢进行焊接的方法,通过
现有的方法进行焊接,焊口位置的强度低于钢材本体的强度焊口易断开,因此钢材无法达到强度的标准要求。
[0025]
为了克服上述的技术问题,本申请提供了一种高强钢的焊接方法。请结合参阅图1以及图2,现对本申请实施例提供的高强钢的焊接方法进行说明。本实施例中的高强钢的焊接方法包括如下步骤:在高强钢钢板1上开设用于焊接的坡口2,得到具有焊口3的钢板组对;对钢板组对的焊口3及其附近进行预处理,预处理包括打磨处理以及预热处理,得到预处理钢板组;焊前打磨范围一般为焊口及其附近20~30mm以内的区域,打磨见金属光泽;预热范围一般为焊口及其附近100mm以内的区域。在预处理钢板组的焊口处使用高强焊丝进行气体保护焊接,气体保护焊接包括在打底层4上进行打底层焊接,以及在盖面层5上进行盖面层焊接;其中,气体保护焊接的热输入为0.8~1.5kj/mm,气体流量为15~25l/min,且打底层以及盖面层之间的层间温度控制在120~200℃。
[0026]
本申请提供的高强钢的焊接方法的有益效果在于:通过严格控制热输入和层间温度在适当范围内,保证组织和晶粒度,从而保证焊缝获得良好的强韧性匹配。在保证焊接材料与钢板之间形成良好的熔合的同时,为焊缝储存一定的韧塑性能,减少焊缝中的裂纹以及缺陷提升焊缝质量;采用高强焊丝进行气体保护焊接,可以获得光滑的焊接接头,无裂纹、气孔等缺陷,力学性能良好具有稳定的强度。并且,采用本方法生产的高强钢的焊接方法全程采用高强钢焊丝,避免来回切换焊丝,操作简单,生产中易于执行,且可推广到自动化机器人焊接,实现高效生产。
[0027]
在其中的一个实施例中,气体保护焊接还包括填充层焊接6,打底层和填充层之间以及填充层和盖面层之间的层间温度控制在120~200℃。根据钢板1的板厚,当板厚较厚时,在打底层以及盖面层间添加填充层。
[0028]
具体的,请结合参考图2以及图3,当钢板厚度小于或等于8mm时,气体保护焊接包括打底层焊接以及盖面层焊接;当钢板厚度大于8mm时,气体保护焊接包括打底层焊接、填充层焊接以及盖面层焊接。其中,打底层焊接的厚度≤5mm,填充层焊接的厚度3~4mm,盖面层焊接的厚度3~4mm。通过合理分配各层的厚度,能够保证焊接的熔融效果以及效率,保证焊口质量。
[0029]
在其中的一个实施例中,高强焊丝的熔敷金属抗拉强度≥940mpa,焊缝抗拉强度≥1200mpa。本申请采用标准aws a5.28的er120s
‑
g高强钢焊丝。采用该焊丝,焊缝抗拉强度能达到1200mpa级别;气体保护焊接的热输入为0.8~1.5kj/mm时,能够保证焊丝的熔融也能保留焊丝中的韧性,达到较好的焊接效果。
[0030]
在其中的一个实施例中,预处理具体包括如下步骤:打磨、预热、加临时衬垫、永久衬垫或者不加衬垫,根据板厚选择合适的根部组对间隙,具体如下:
[0031]
1)打磨钢板组对间隙的焊口处,漏出金属光泽;这样能够避免焊后出现气孔、裂纹等缺陷。
[0032]
2)预热温度100~150℃;该预热区间能有效降低焊接接头的冷却速度,延长奥氏体冷却转变的时间,避免或减少产生淬硬组织的倾向,并促使焊缝中氢的扩散逸出,从而防止产生冷裂纹。其次,预热还可以降低焊接区与周围母材金属之间的温差,使温度梯度在较宽范围内能相对均匀分布,从而减小焊接应力峰值。
[0033]
3)根据结构形式、设计要求等,综合确定是否在根部增加临时衬垫、永久衬垫或者
不加衬垫。
[0034]
4)根据板厚选择合适的根部组对间隙,保证根部熔熔透。
[0035]
在其中的一个实施例中,打底层焊接的参数为:焊接电压19~22v,焊接电流100~160a,焊接速度100~200mm/min。通过上述的焊接电压、焊接电流以及焊接速度能够保证打底层焊接时的热输入达到0.8~1.5kj/mm,气体流量达到15~25l/min,保证焊接的稳定以及熔融效率,保证焊缝的质量以及力学性能的稳定。
[0036]
在其中的一个实施例中,填充层焊接以及盖面层焊接的参数为:焊接电压22~30v,焊接电流180~280a,焊接速度260~450mm/min。通过上述的焊接电压、焊接电流以及焊接速度能够保证填充层以及盖面层焊接时的热输入达到0.8~1.5kj/mm,气体流量达到15~25l/min,保证焊接的稳定以及熔融效率,保证焊缝的质量以及力学性能的稳定。
[0037]
在其中的一个实施例中,高强焊丝采用实心焊丝或药芯焊丝,焊丝直径为0.8~1.6mm,保证焊接工艺性和生产效率。
[0038]
在其中的一个实施例中,高强焊丝的保护气为富氩气体,有助于形成稳定柔和电弧,降低飞溅,提升焊缝的质量。
[0039]
如图2所示,在其中的一个实施例中,钢板组对口间隙为d=1~4mm。钢板组对口的间隙d根据板厚a来进行选择,保证根部熔熔透,不同的间隙d能够适应不同厚度钢板的焊接。采用此方法能够保证焊缝的力学性能稳定。
[0040]
在其中的一个实施例中,钢板的坡口为v形坡口,v形坡口的角度为α=50~60
°
无需留钝边,以降低加工难度。坡口角度由板厚决定,当板厚增加,坡口角度可减小,以减少熔敷金属量,并同时保证焊缝质量。且本方法加工的坡口,无需留钝边,能方便加工。
[0041]
进一步的,v形坡口的钢板还包括预处理:在预热处理后,对钢板焊口背面加焊接衬垫。焊接衬垫包括临时衬垫以及永久衬垫。设置临时衬垫时,应保证临时衬垫能够方便地与焊接后的材料分离。焊接衬垫可保证焊接后的焊口背面成型平整美观,达到单面焊双面成型的效果;但是,对于手工气体保护焊接,如果焊接操作人员手法熟练,能保证不采用焊接衬垫也能实现单面焊双面成型时,可以不采用焊接衬垫。
[0042]
在其中的一个实施例中,坡口采用热切割或机械加工的方式进行加工。热切割方式加工的坡口通过机械方式去除热影响区,能够降低对钢板力学性能的影响。
[0043]
本申请的另一方面,提供了一种高强钢焊接接头,采用如上的高强钢的焊接方法制备焊接接头。
[0044]
1)焊接接头可以采用富氩气体和实心焊丝焊接;
[0045]
2)盖面层焊接后无需保温缓冷,除非环境温度≤10℃,或者,环境湿度≥90%;焊后无需后热处理,除非有特殊要求;对于焊接过程中断而导致待焊部位温度低于预热温度的情况,重新焊接之前应按预热温度要求再次加热。
[0046]
3)打底层、填充层和盖面层焊接,通过严格控制热输入和层间温度在如上所述的范围内,即可保证组织和晶粒度,从而保证焊缝和焊接接头获得良好的强韧性匹配。
[0047]
下面采用三个具体实施例对本申请的方法做详细说明。
[0048]
实施例一
[0049]
采用6mm厚的屈服强度1300mpa钢板,开50
°
v型坡口,焊前预热100℃,采用伯乐gm120焊丝完成打底层焊接和盖面层焊接,焊接参数分别如下:(1)打底:焊接电流130a,焊
接电压20v,焊接速度160mm/min;(2)盖面层焊接:焊接电流260a,焊接电压27.5v,焊接速度450mm/min。层间温度控制在120~200℃。可适当摆动,保证焊缝与坡口两侧熔合良好。
[0050]
通过上述方法可以获得光滑的焊接接头,无裂纹、气孔等缺陷,力学性能良好;焊缝金属的室温抗拉强度大于1217mpa,
‑
40℃试验温度下焊缝金属的v形缺口冲击试验的冲击功大于47j,6a冷弯试验合格。
[0051]
实施例二
[0052]
采用8mm厚的屈服强度1300mpa钢板,开60
°
v型坡口,焊前预热100℃,采用伯乐gm120焊丝完成打底层焊接和盖面层焊接,焊接参数分别如下:(1)打底层焊接:焊接电流140a,焊接电压20.5v,焊接速度170mm/min;(2)盖面层焊接:焊接电流270a,焊接电压29v,焊接速度430mm/min。层间温度控制在120~200℃。可适当摆动,保证焊缝与坡口两侧熔合良好。
[0053]
通过上述方法可以获得光滑的焊接接头,无裂纹、气孔等缺陷,力学性能良好;焊缝金属的室温抗拉强度大于1240mpa,
‑
40℃试验温度下焊缝金属的v形缺口冲击试验的冲击功大于47j,6a冷弯试验合格。
[0054]
实施例三
[0055]
采用12mm厚的屈服强度1300mpa钢板,开60
°
v型坡口,焊前预热130℃,采用伯乐gm120焊丝完成打底层焊接、填充层焊接和盖面层焊接,焊接参数分别如下:(1)打底层焊接:焊接电流140a,焊接电压20.5v,焊接速度170mm/min;(2)填充层焊接和盖面层焊接:焊接电流260a,焊接电压27.5v,焊接速度450mm/min。层间温度控制在120~200℃。可适当摆动,保证焊缝与坡口两侧熔合良好。
[0056]
通过上述方法可以获得光滑的焊接接头,无裂纹、气孔等缺陷,力学性能良好;焊缝金属的室温抗拉强度大于1220mpa,
‑
40℃试验温度下焊缝金属的v形缺口冲击试验的冲击功大于47j,6a冷弯试验合格。
[0057]
以上所述仅为本申请的较佳实施例而已,并不用以限制本申请,凡在本申请的精神和原则之内所作的任何修改、等同替换和改进等,均应包含在本申请的保护范围之内。