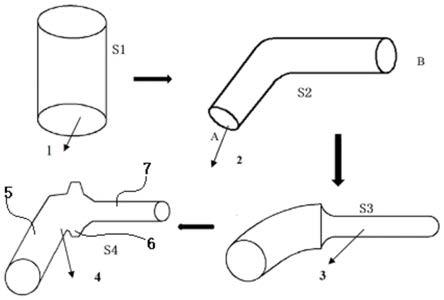
一种镍基高温合金gh3536模锻件及其成型方法
技术领域
1.本发明属于材料加工技术领域,具体涉及一种镍基高温合金gh3536模锻件及其成型方法。
背景技术:2.高温合金是以铁、镍、钴为基,能在高于600℃以上的高温及一定应力作用下长期工作的一类金属材料,具有优异的高温强度,良好的抗热腐蚀性能,良好的疲劳性能、断裂韧性等综合性能。高温合金为单一奥氏体组织,在各种温度下具有良好的组织稳定性和使用可靠性,被广泛应用于航空、航天、石油、化工、舰船等领域,镍基高温合金gh3536具有较好的抗高温氧化性能,主要用于航空发动机火焰筒、燃烧室等部件。
3.现有技术中,某镍基高温合金gh3536材质的模锻件存在以下的缺点和不足:
4.如图1所示,该模锻件的形状类似于手枪形状,包括尾部细杆5、中间多边形盘6和头部圆柱7,该模锻件在航空航天领域得到广泛的应用,是发动机中的重要零部件,它的工作要求耐高压、长寿命、高可靠、高稳定性的需求,这对其模锻件成型后的使用性能有了非常高的要求,特别是模锻件成型后晶粒度的要求,要求模锻件成型后晶粒度≧4级,但现有锻造技术锻造后易造成粗晶,无法满足使用要求。
技术实现要素:5.为解决现有技术中存在的问题,本发明的目的在于提供一种镍基高温合金gh3536模锻件及其成型方法,本发明能够提高所述gh3536模锻件的晶粒度等级,使其满足使用要求。
6.本发明采用的技术方案如下:
7.一种镍基高温合金gh3536模锻件成型方法,包括如下过程:
8.模锻件成型,模锻件成型包括如下步骤:
9.将拔杆锻件进行加热、保温,使拔杆锻件的温度为1120~1160℃;
10.将所述加热、保温完成后的拔杆锻件进行两次模压,第二次模压后进行切边,得到第一锻坯,其中第一次模压时打击能量为8~16kj,第二次模压时打击能量为80~112kj,第一次模压、第二次模压的终锻温度不低于860℃;
11.将第一锻坯进行加热、保温,使第一锻坯的温度为1120~1160℃;
12.将所述加热、保温后的第一锻坯进行模压,模压后进行切边,得到锻件;其中,模具的预热温度为350℃~400℃,终锻温度不低于860℃,打击能量为64~96kj;
13.将所述锻件进行固溶,得到所述镍基高温合金gh3536模锻件。
14.优选的,拔杆锻件进行加热、保温时,保温的时间为40~80min。
15.优选的,将所述加热、保温完成后的拔杆锻件进行两次模压过程中,坯料转移时间为≤13s。
16.优选的,将所述加热、保温完成后的拔杆锻件进行两次模压过程中,第一次模压结
束后,将模具型腔及坯料表面的氧化皮去除,然后喷涂润滑剂进行第二次模压。
17.优选的,所述润滑剂使用石墨乳与水的混合物,石墨乳与水的体积比例为1:4~1:10。
18.优选的,采用风枪将模具型腔及坯料表面的氧化皮去除。
19.优选的,将所述锻件进行固溶过程中,保温温度为1150~1170℃,保温时间为50~60min;保温后采用油淬,采用油温不低于30~40℃。
20.优选的,所述镍基高温合金gh3536模锻件成型方法还包括制坯阶段,制坯阶段包括下过程:
21.将棒坯随炉升温至1120~1160℃,保温时间为40~120min
22.将锤头、锤砧以及工装预热至250~380℃,将所述棒坯锻造为弯杆锻件,锻造过程中,坯料转移时间不超过15s,终锻温度不低于860℃。
23.优选的,所述镍基高温合金gh3536模锻件成型方法还包括制坯阶段,制坯阶段包括如下过程:
24.将弯杆锻件随炉升温至1120~1160℃,保温40~100min;
25.将锤头、锤砧以及工装预热至250~380℃;对弯杆锻件进行拔杆,在弯杆锻件的一端加工出尾部细杆,拔杆过程中,加热温度为1120~1160℃,坯料转移时间不超过13s,终锻温度不低于860℃,锻后进行空冷,得到拔杆锻件。
26.本发明还提供了一种镍基高温合金gh3536模锻件,所述镍基高温合金gh3536模锻件通过本发明如上所述的成型方法制得,所述镍基高温合金gh3536模锻件的晶粒度达到均匀的5级。
27.本发明具有如下技术效果:
28.本发明为镍基高温合金gh3536模锻件成型方法,通过系统合理设定加热温度、保温时间、锻造火次、终锻温度,热处理制度等锻造参数,解决现有锻件粗晶的问题,模锻件最终成型后的晶粒度达到均匀的5级,提高了产品质量。
附图说明
29.图1是本发明所加工的gh3536模锻件坯料锻造外形变化荒形图;
30.图2为本发明实施例1加工得到的gh3536模锻件的金相图;
31.图3为本发明实施例2加工得到的gh3536模锻件的金相图;
32.图4为本发明实施例3加工得到的gh3536模锻件的金相图;
33.图中,1
‑
坯料,2
‑
弯杆锻件,3
‑
拔杆锻件,4
‑
模压成型荒形图,5
‑
尾部细杆,6
‑
中间多边形盘,7
‑
头部圆柱。
具体实施方式
34.以下结合附图对本发明做进一步详细说明。
35.本发明镍基高温合金gh3536模锻件成型方法的主要工艺过程包括:
36.下料
→
制坯
→
模锻件成型
→
晶粒度检测
→
总检
→
入库
37.参照图1,具体过程如下:
38.采用锯床下料,在制坯时,将棒料置于ⅲ类电炉中1120~1160℃,最短保温时间
45min,热料回炉时保温时间按0.4min/mm计算,最长保温时间120min,保温完成后利用560kg空气锤上进行锻造弯杆,将弯杆后的锻件继续装入ⅲ类电炉中加热到1120~1160℃,最短保温时间40min,保温时间按0.4min/mm计算,最长保温时间80min,保温完成后在750kg空气锤上进行锻造拔杆,拔杆后空冷。
39.模锻件成型:将拔杆后的锻件置于ⅲ类电炉中加热到1120~1160℃,最短保温时间40min,热料回火炉时保温时间按0.4min/mm计算,最长保温时间80min,保温完成后进行模压一火,在10mn电动螺旋压力机上将坯料正放后模压,设备总打击能为160kj,先轻击一锤,打击能量:5%~10%;将坯料整体取出,使用风枪迅速清除上、下模具型腔及锻件表面氧化皮,润滑剂使用石墨乳+水,体积比例1:4~1:10,随后重击,打击能量50%~70%模压后趁热切边,两次模压后的终锻温度不低于860℃。
40.将模压一火后的模锻件置于ⅲ类电炉中加热到1120~1160℃,最短保温时间30min,热料回火炉时保温时间按0.4min/mm计算,最长保温时间80min,保温完成后进行模压二火成型,模具预热温度350℃~400℃,预热时间5h≤5.5h,坯料转移时间≤10s,终锻温度不低于850℃,将坯料依型腔放正放稳后,进行模压,打击能量:40%~60%,模压后趁热切边,切边后进行校正、空冷。
41.将模压二火后的锻件进行热处理,热处理过程是将锻件进行固溶,固溶时的加热温度:1150~1170℃,保温时间为50~60min,然后进行油淬,油淬时的油温为30~40℃。等待冷却后进行切取试样晶粒度检测。
42.实施例1
43.本实施中坯料1的下料规格为φ50
×
112
±
1mm;
44.在制坯阶段:在ⅲ类电炉中对坯料进行加热,坯料的装炉数量为20件,炉温850℃时装炉,随炉升温至温度1130℃,保温时间为85min,将锤头、锤砧以及工装预热至380℃。弯曲过程中:坯料转移时间≤15s,终锻温度为860℃,锻后空冷;弯曲时距a端50mm处进行弯曲,得到弯杆锻件2。
45.在制坯阶段:在ⅲ类电炉中对弯杆锻件2加热,弯杆锻件2的装炉数量为20件,850℃装炉,随炉升温至加热温度1130℃,保温时间:50min,锤头、锤砧以及工装预热380℃。拔杆:锻造:如图1的s3所示,距b端30mm处进行分料拔长;坯料转移时间13s,终锻温度865℃,锻后进行空冷,得到拔杆锻件3。
46.图1的s4为模锻件成型后的荒型图,模锻件成型的过程包括:工步一:加热:在ⅲ类电炉中对拔杆锻件3进行加热,拔杆锻件3的装炉数量为20件,于850℃装炉,随炉升温至加热温度1130℃;保温时间为60min;工步二:模压一火,坯料转移时间13s,终锻温度860℃,将坯料正放后模压,先轻击一锤,打击能量:14kj;将坯料整体取出,使用风枪迅速清除上、下模具型腔及锻件表面氧化皮,随后重击,打击能量80kj,模压后趁热进行切边。工步三:加热:在ⅲ类电炉中对工步二加工后的工件进行加热,装炉数量为20件,随炉升温,加热温度为1130℃;最短保温时间为30min,最长保温时间为70min;工步四:模压二火,模具预热温度至380℃,预热时间5h,坯料转移时间10s,终锻温度860℃,将坯料依型腔放正放稳后,进行模压,打击能量:85kj,模压后趁热切边。
47.将工步四加工得到的锻件进行固溶,固溶时保温温度为1160℃,保温时间为55min,冷却时采用油淬,油淬时的油温为40℃,得到最终的gh3536模锻件。
48.晶粒度检测:在gh3536模锻件上切长度为20的晶粒度试样进行检测,按gb/t 6394进行晶粒度检测,检测后得到晶粒度为均匀5级。本实施例gh3536模锻件的金相图如图2所示,由图2可以看出,本实施例制得的gh3536模锻件组织的晶粒度为均匀的5级。
49.实施例2
50.本实施中坯料1的下料规格为φ55
×
112
±
1mm;
51.在制坯阶段:在ⅲ类电炉中对坯料进行加热,坯料的装炉数量为10件,炉温850℃时装炉,随炉升温至温度1140℃,保温时间为90min,将锤头、锤砧以及工装预热至390℃。弯曲过程中:坯料转移时间≤15s,终锻温度为870℃,锻后空冷;弯曲时距a端50mm处进行弯曲,得到弯杆锻件2。
52.在制坯阶段:在ⅲ类电炉中对弯杆锻件2加热,弯杆锻件2的装炉数量为10件,850℃装炉,随炉升温至加热温度1140℃,保温时间:65min,锤头、锤砧以及工装预热390℃。拔杆:锻造:如图1的s3所示,距b端30mm处进行分料拔长;坯料转移时间13s,终锻温度870℃,锻后进行空冷,得到拔杆锻件3。
53.图1的s4为模锻件成型后的荒型图,模锻件成型的过程包括:工步一:加热:在ⅲ类电炉中对拔杆锻件3进行加热,拔杆锻件3的装炉数量为10件,于850℃装炉,随炉升温至加热温度1140℃;保温时间为60min;工步二:模压一火,坯料转移时间13s,终锻温度870℃,将坯料正放后模压,先轻击一锤,打击能量:10kj;将坯料整体取出,使用风枪迅速清除上、下模具型腔及锻件表面氧化皮,随后重击,打击能量100kj%,模压后趁热进行切边。工步三:加热:在ⅲ类电炉中对工步二加工后的工件进行加热,装炉数量为10件,随炉升温,加热温度为1140℃;最短保温时间为30min,最长保温时间为70min;工步四:模压二火,模具预热温度至390℃,预热时间5h,坯料转移时间10s,终锻温度870℃,将坯料依型腔放正放稳后,进行模压,打击能量:90kj,模压后趁热切边。
54.将工步四加工得到的锻件进行固溶,固溶时保温温度为1150℃,保温时间为50min,冷却时采用油淬,油淬时的油温为40℃,得到最终的gh3536模锻件。
55.晶粒度检测:在gh3536模锻件上切长度为20的晶粒度试样进行检测,按gb/t 6394进行晶粒度检测,检测后得到晶粒度为均匀5级。本实施例gh3536模锻件的金相图如图2所示,由图3可以看出,本实施例制得的gh3536模锻件组织的晶粒度为均匀的5级。
56.实施例3
57.本实施中坯料1的下料规格为φ50
×
112
±
1mm;
58.在制坯阶段:在ⅲ类电炉中对坯料进行加热,坯料的装炉数量为5件,炉温850℃时装炉,随炉升温至温度1160℃,保温时间为85min,将锤头、锤砧以及工装预热至380℃。弯曲过程中:坯料转移时间≤13s,终锻温度为880℃,锻后空冷;弯曲时距a端50mm处进行弯曲,得到弯杆锻件2。
59.在制坯阶段:在ⅲ类电炉中对弯杆锻件2加热,弯杆锻件2的装炉数量为5件,850℃装炉,随炉升温至加热温度1160℃,最短保温时间:40min,最长保温时间:100min,锤头、锤砧以及工装预热380℃。拔杆:锻造:如图1的s3所示,距b端30mm处进行分料拔长;坯料转移时间13s,终锻温度880℃,锻后进行空冷,得到拔杆锻件3。
60.图1的s4为模锻件成型后的荒型图,模锻件成型的过程包括:工步一:加热:在ⅲ类电炉中对拔杆锻件3进行加热,拔杆锻件3的装炉数量为5件,于850℃装炉,随炉升温至加热
温度1160℃;最短保温时间为40min;最长保温时间为80min。工步二:模压一火,坯料转移时间13s,终锻温度880℃,将坯料正放后模压,先轻击一锤,打击能量:16kj;将坯料整体取出,使用风枪迅速清除上、下模具型腔及锻件表面氧化皮,随后重击,打击能量112kj,模压后趁热进行切边。工步三:加热:在ⅲ类电炉中对工步二加工后的工件进行加热,装炉数量为5件,随炉升温,加热温度为1160℃;最短保温时间为30min,最长保温时间为70min;工步四:模压二火,模具预热温度至400℃,预热时间5h,坯料转移时间10s,终锻温度880℃,将坯料依型腔放正放稳后,进行模压,打击能量:96kj,模压后趁热切边。
61.将工步四加工得到的锻件进行固溶,固溶时保温温度为1170℃,保温时间为60min,冷却时采用油淬,油淬时的油温为40℃,得到最终的gh3536模锻件。
62.晶粒度检测:在gh3536模锻件上切长度为20的晶粒度试样进行检测,按gb/t 6394进行晶粒度检测,检测后得到晶粒度为均匀5级。本实施例gh3536模锻件的金相图如图2所示,由图4可以看出,本实施例制得的gh3536模锻件组织的晶粒度为均匀的5级。
63.综上可以看出,本发明通过调整锻造参数、锻造火次、改变变形量、控制转移时间、终锻温度、锤砧预热温度等锻造过程的关键点改善了gh3536模锻件成型后的晶粒度。