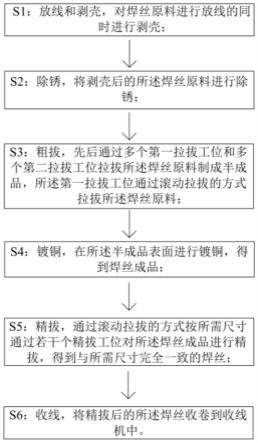
1.本发明涉及焊丝生产技术领域,尤其涉及一种焊丝的生产方法。
背景技术:2.焊接技术在多个基础建设领域有着非常重要的作用。焊丝作为焊接材料中一项重要的分支,以焊接速度快、焊接质量好在焊接材料中占比较高。传统的焊丝生产过程如下:原材料放线—剥壳—除锈—涂硼—高压水洗—机械涂粉—粗拉和精拉—机械除脂—水洗—镀铜—高压水洗—热风吹干—抛光—收线。由于该生产过程中的粗拉和精拉均是将焊丝原料通过拉拔板上直径小于此工位焊丝原料的拉拔孔,通过拉拔孔的边缘将焊丝原料的挤压作用将焊丝原料的直径变小。
3.传统的焊丝生产方法中存在的问题有:
4.1、在对焊丝原料进行拉拔之前需要保证焊丝原料表面的光滑,否则容易因焊丝原料表面粗糙导致摩擦力很大,焊丝原料无法通过拉拔孔而断丝。且拉拔结束后表面会产生大量毛刺,无法直接进行镀铜操作。故该生产过程需要多道水洗工序,且质量控制点多,生产工艺复杂,容易出现质量事故。老式生产工艺采用单条镀铜线配多条粗拉及细拉生产线,存在占地面积大、耗能大、人力成本高等问题。
5.2、由于该生产过程是利用摩擦力进行拉拔,故无法大幅度降低焊丝的直径尺寸,只能通过多次拉拔使焊丝达到尺寸要求,如该生产过程需要12次拉拔才能将5.5mm的焊丝原料拉拔成1.2mm的焊丝产品。
6.3、当焊丝镀铜后,其直径各不相同且均大于精拔后的焊丝直径,导致最终产品的尺寸存在偏差,且无法通过再次精拔矫正尺寸,否则容易将镀铜层剥落。
7.针对上述问题,需要开发一种焊丝的生产方法,以解决传统焊丝生产方法中存在大量工位导致占地面积大、拉拔效率低及最终产品尺寸不符要求的问题。
技术实现要素:8.本发明的目的在于提出一种焊丝的生产方法,能够减少工位以降低占地面积、提高拉拔效率以及提升最终产品的合格率。
9.为达此目的,本发明采用以下技术方案:
10.一种焊丝的生产方法,包括以下步骤:
11.s1:放线和剥壳,对焊丝原料进行放线的同时进行剥壳;
12.s2:除锈,对剥壳后的所述焊丝原料进行除锈;
13.s3:粗拔,先后通过多个第一拉拔工位和多个第二拉拔工位拉拔所述焊丝原料制成半成品,所述第一拉拔工位通过滚动拉拔的方式拉拔所述焊丝原料;
14.s4:镀铜,在所述半成品表面进行镀铜,得到焊丝成品;
15.s5:精拔,通过滚动拉拔的方式按所需尺寸通过若干个精拔工位对所述焊丝成品进行精拔,得到与所需尺寸完全一致的焊丝;
16.s6:收线,将精拔后的所述焊丝收卷到收线机中。
17.优选地,步骤s3中的所述第一拉拔工位包括拉拔机构,所述拉拔机构包括两个拉拔件,两个所述拉拔件为轮盘状且朝相反方向转动,每个所述拉拔件的边缘沿周向都设置有半圆形的凹槽,两个所述拉拔件所述凹槽拼合成一个圆形的第一拉拔孔,所述焊丝原料通过所述第一拉拔孔时完成一次拉拔。
18.优选地,步骤s3中的所述第二拉拔工位包括拉拔板,所述拉拔板上设置有第二拉拔孔,所述焊丝原料通过所述第二拉拔孔时完成一次拉拔。
19.优选地,多个所述第一拉拔工位的所述第一拉拔孔及多个所述第二拉拔工位的所述第二拉拔孔的直径依次减小。
20.优选地,最后一个所述第二拉拔工位的所述第二拉拔孔的直径为0.8mm-1.2mm。
21.优选地,第一个所述拉拔工位之前设置有润滑工位,所述润滑工位包括盒体,所述盒体内设置有润滑粉,所述焊丝原料从所述盒体的一端穿入,从所述盒体的相对一端穿出。
22.优选地,步骤s3中得到所述半成品后,清理所述半成品的表面。
23.优选地,步骤s4中的所述镀铜的速度为30m/s-40m/s。
24.优选地,步骤s1剥壳之后,还包括利用负压设备对剥落的氧化皮进行收集。
25.优选地,步骤s6中的所述收线机包括驱动电机及收线轴,所述收线轴与所述驱动电机的输出轴相连,所述收线轴与所述焊丝的一端固定连接。
26.本发明的有益效果:
27.本发明提供了一种焊丝的生产方法。该生产方法中,粗拔步骤分为多个工位,其中第一拉拔工位通过滚动拉拔的方式拉拔焊丝原料,大大降低了拉拔过程中焊丝原料表面受到的摩擦力,主要具有以下优点:
28.1、滚动拉拔对焊丝原料的表面质量不敏感,且不会因表面粗糙使得阻力较大导致断丝,同时拉拔后不会产生毛刺等表面缺陷,清理杂质后可直接进行镀铜操作。故该生产方法仅需要对焊丝进行一次水洗,而且不需要前期大量的准备工序,质量控制点少,生产工艺简单,设备占地面积小、人力成本低。
29.2、由于粗拔工序的前几道工序均为滚动拉拔,故每一次直径的减小量较之前有较大幅度提升,而不需要担心阻力过大导致断丝的问题。利用该生产方法生产焊丝,利用较少的拉拔工序即可将焊丝原料拉拔成需要的焊丝尺寸。
30.3、镀铜之后增加一次精拔,通过滚动拉拔的方式对镀铜后的焊丝成品进行尺寸矫正,保证收线时焊丝的直径尺寸符合最终产品的要求,且不会破坏镀铜层。
附图说明
31.图1是本发明提供的焊丝的生产方法的流程图;
32.图2是本发明提供的拉拔机构的结构示意图;
33.图3是本发明提供的拉拔机构的正视图;
34.图4是本发明提供的盒体的结构示意图。
35.图中:
36.1、拉拔机构;2、盒体;
37.11、拉拔件;
38.111、凹槽;112、第一拉拔孔。
具体实施方式
39.下面详细描述本发明的实施例,实施例的示例在附图中示出,其中自始至终相同或类似的标号表示相同或类似的元件或具有相同或类似功能的元件。下面通过参考附图描述的实施例是示例性的,旨在用于解释本发明,而不能理解为对本发明的限制。
40.在本发明的描述中,需要说明的是,术语“中心”、“上”、“下”、“左”、“右”、“竖直”、“水平”、“内”、“外”等指示的方位或位置关系为基于附图所示的方位或位置关系,仅是为了便于描述本发明和简化描述,而不是指示或暗示所指的装置或元件必须具有特定的方位、以特定的方位构造和操作,因此不能理解为对本发明的限制。此外,术语“第一”、“第二”仅用于描述目的,而不能理解为指示或暗示相对重要性。其中,术语“第一位置”和“第二位置”为两个不同的位置。
41.除非另有明确的规定和限定,术语“安装”、“相连”、“连接”、“固定”应做广义理解,例如,可以是固定连接,也可以是可拆卸连接;可以是机械连接,也可以是电连接;可以是直接相连,也可以通过中间媒介间接相连,可以是两个元件内部的连通或两个元件的相互作用关系。对于本领域的普通技术人员而言,可以根据具体情况理解上述术语在本发明中的具体含义。
42.除非另有明确的规定和限定,第一特征在第二特征之“上”或之“下”可以包括第一特征和第二特征直接接触,也可以包括第一特征和第二特征不是直接接触而是通过它们之间的另外的特征接触。而且,第一特征在第二特征“之上”、“上方”和“上面”包括第一特征在第二特征正上方和斜上方,或仅仅表示第一特征水平高度高于第二特征。第一特征在第二特征“之下”、“下方”和“下面”包括第一特征在第二特征正下方和斜下方,或仅仅表示第一特征水平高度小于第二特征。
43.下面结合附图并通过具体实施方式来进一步说明本发明的技术方案。
44.本实施例提供了一种焊丝的生产方法。如图1所示,该生产方法包括以下步骤:
45.s1:放线和剥壳,对焊丝原料进行放线的同时进行剥壳。
46.对原材料进行放线同时对原材料进行机械剥壳去除原材料表面的氧化皮。
47.s2:除锈,对剥壳后的焊丝原料进行除锈。
48.即便有氧化皮的保护,焊丝原料也会存在一定的锈迹,需要在拉拔之前除掉以免影响拉拔效果。可将焊丝原料通过砂布袋,利用砂布袋与焊丝原料之间的摩擦进行除锈。
49.s3:粗拔,先后通过多个第一拉拔工位和多个第二拉拔工位拉拔焊丝原料制成半成品,第一拉拔工位通过滚动拉拔的方式拉拔焊丝原料。
50.焊丝原料在开始进行拉拔时直径较大,可通过滚动拉拔的方式利用少数工位使焊丝原料的直径大幅降低,既能够提高效率,又使拉拔后的焊丝表面质量高,无毛刺。该生产方法在拉拔时可通过较少次数的拉拔使直径为5.5mm-6.5mm的焊丝原料拉拔成直径为0.8mm-1.2mm的焊丝产品,拉拔能力与效率均大幅提升。
51.优选地,第一拉拔工位与第二拉拔工位的数量均为5个,通过10次拉拔得到焊丝产品。通过5次滚动拉拔可大幅降低焊丝原料的直径,与焊丝产品要求的直径尺寸之间的差距较小,之后即可通过传统的拉拔方式继续对焊丝原料进行拉拔得到焊丝产品。
52.s4:镀铜,在半成品表面进行镀铜,得到焊丝成品。
53.s5:精拔,通过滚动拉拔的方式按所需尺寸通过若干个精拔工位对焊丝成品进行精拔,得到与所需尺寸完全一致的焊丝。
54.镀铜后焊丝成品的直径发生变化,导致其尺寸可能会大于所需尺寸,造成产品合格率降低。而通过滚动拉拔的方式进行若干次精拔,拉拔时仅是在焊丝成品表面滚动以减小焊丝成品的直径,而不会对镀铜层造成破坏,且能对焊丝的尺寸进行校正,大幅提高产品的合格率,降低成本。
55.s6:收线,将精拔后的焊丝收卷到收线机中。
56.该生产方法的好处在于利用滚动拉拔的方式,避免了传统生产方法中摩擦拉拔时需要保证焊丝原料表面的光滑以及拉拔结束后产生的大量毛刺的问题,从而降低了水洗工序的数量,仅需要一次水洗,且不需要前期大量的准备工序,质量控制点少,生产工艺简单,设备占地面积小、人力成本低。
57.优选地,步骤s3中的第一拉拔工位包括拉拔机构1,如图2所示,拉拔机构1包括两个拉拔件11,两个拉拔件11为轮盘状且朝相反方向转动,每个拉拔件11的边缘沿周向都设置有半圆形的凹槽111,两个拉拔件11凹槽111拼合成一个圆形的第一拉拔孔112,焊丝原料通过第一拉拔孔112时完成一次拉拔。
58.滚动拉拔需要通过拉拔机构1实现。两个轮盘装的拉拔件11设置于同一平面,各自的凹槽111拼合成一个完整的第一拉拔孔112,在工作时,两个拉拔件11朝相反方向转动,并将焊丝原料压入第一拉拔孔112,焊丝原料在两个拉拔件11的转动作用下不断进入第一拉拔孔112,第一拉拔孔112另一侧出来的焊丝原料的直径与第一拉拔孔112的直径相等,完成一次拉拔。
59.与传统的拉拔相比,利用拉拔机构1能够使焊丝原料与第一拉拔孔112的边缘之间由滑动摩擦变为滚动摩擦,大大降低了焊丝原料表面受到的轴向的阻力,拉拔过程既省力,又能够保证不产生毛刺。且由于焊丝原料受到的轴向的阻力减小,就能够使相邻的第一拉拔工位的第一拉拔孔112的尺寸差增大,而不必担心焊丝原料通过过小的第一拉拔孔112导致轴向的阻力过大而断丝的问题,从而大大提高了拉拔效率。
60.其中,第二拉拔工位也可以利用滚动拉拔的方式对焊丝原料进行拉拔,但相对来说设备成本较高,为了解决这个问题,步骤s3中的第二拉拔工位包括拉拔板,拉拔板上设置有第二拉拔孔,焊丝原料通过第二拉拔孔时完成一次拉拔。
61.通过多个第一拉拔工位能够将焊丝原料的直径大幅降低,再通过多个第二拉拔工位的拉拔板直接进行拉拔也能够得到符合尺寸要求的产品,且拉拔效率也比传统的焊丝生产方式高。但由于第二拉拔工位是通过滑动摩擦对焊丝原料进行拉拔,即便焊丝原料的直径已经大幅降低,第二拉拔工位每一次的拉拔量可以设置的很小,但依然会在焊丝半成品的表面产生毛刺。
62.为了解决这个问题,第一个拉拔工位之前设置有润滑工位,润滑工位包括盒体2,盒体2内设置有润滑粉,焊丝原料从盒体2的一端穿入,从盒体2的相对一端穿出。
63.在对焊丝原料进行拉拔之前,先将焊丝原料通过一个盛有润滑粉的盒体2,使焊丝原料表面附着一层润滑粉,使焊丝原料行进到第二拉拔工位时对焊丝原料与第二拉拔孔的边缘进行润滑,降低摩擦力,以降低毛刺的产生量及大小。
64.由于拉拔后的焊丝半成品表面存在一定的毛刺以及润滑粉,故需要在步骤s3中得到半成品后,清理半成品的表面。可以利用砂纸打磨半成品的表面,将毛刺及润滑粉磨掉。然后利用热水对半成品进行水洗,保证半成品表面的质量。
65.为了使焊丝原料的直径随着每一次拉拔逐渐减小,在设计拉拔工位时,5个第一拉拔工位的第一拉拔孔112及5个第二拉拔工位的第二拉拔孔的直径依次减小。
66.优选地,最后一个第二拉拔工位的拉拔孔的直径为0.8-1.2mm。该生产方法能够将直径为5.5mm-6.5mm的焊丝原料通过10次拉拔制成直径为0.8-1.2mm的焊丝,故最后一次拉拔孔的直径为0.8-1.2mm。该焊丝的生产方法最多能够将直径6.5mm的焊丝原料通过10次拉拔制成直径为0.8mm的焊丝,极大地提高了效率。具体地,最终焊丝的直径可以是0.8mm、0.9mm、1.0mm、1.1mm及1.2mm。
67.可以理解的是,若要得到尺寸较为精准的直径为1mm的焊丝,步骤s6的精拔工位中,精拔孔的直径也为1mm。由于经过镀铜后,焊丝成品的直径必然大于1mm,且根据不同部位镀铜量的不同,其直径也必不相同。为了使最终焊丝直径的准确度和均匀度都合格,在镀铜后利用滚动拉拔的方式对焊丝成品进行精拔,既不会破坏镀铜层,又能够校准尺寸,提高合格率。
68.精拔工位的结构与第一拉拔工位相同,都是通过两个轮盘状拉拔件11进行拉拔,此处不再赘述。
69.优选地,步骤s4中的镀铜的速度为30m/s-40m/s。该生产方法中焊丝表面的质量较高,故在镀铜过程中,铜离子很容易与焊丝表面发生置换反应从而附着在焊丝的表面,故能够达到30m/s-40m/s的镀铜速度,提高了镀铜效率。
70.优选地,步骤s1剥壳之后,还包括利用负压设备对剥落的氧化皮进行收集。剥落的氧化皮为废料,若任由氧化皮留在设备中,容易影响后面焊丝剥壳的效果,且氧化皮碎裂后产生粉尘,严重影响操作人员的身体健康。故需要对氧化皮进行收集,集中处理。
71.优选地,步骤s6中的收线机包括驱动电机及收线轴,收线轴与驱动电机的输出轴相连,收线轴与焊丝的一端固定连接。焊丝的一端固定于收线轴上,当驱动电机带动收线轴转动时,焊丝开始缠绕在收线轴上,完成收线操作。将收线轴与电机的输出轴直接相连,降低了传动时的能量损失,且可通过控制电机的转速直接控制收线的速度,操作便捷。
72.以上内容仅为本发明的较佳实施例,对于本领域的普通技术人员,依据本发明的思想,在具体实施方式及应用范围上均会有改变之处,本说明书内容不应理解为对本发明的限制。