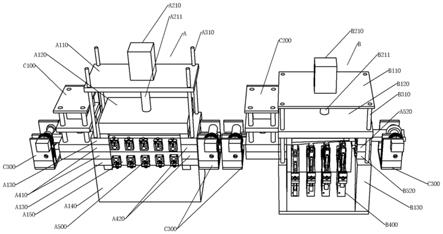
1.本发明涉及火工技术,特别是涉及聚能切割索,具体涉及一种聚能切割索加工装置。
背景技术:2.聚能切割索是利用聚能效应(通常称为“门罗效应”),即炸药爆炸后,起爆炸产物在高温高压来切割金属材料,爆破碎片基本是沿炸药表面的法线方向向外飞散的。带凹槽(聚能角)的铜管装药在引爆后,在凹槽轴线上会出现一股汇聚的、速度和压强都和高的爆炸产物流,在一定的范围内使炸药爆炸释放出来的化学能集中起来,目前主要应用于火箭的分离技术上。
3.在现有文献1中提到,切割索的截面形状对切割索的性能起到了关键的作用。参见图1,切割索的截面形状达到6号是最理想的状态,这种状态下聚能角α能够更加线性、集中地释放出爆炸的能量。但是目前没办法加工至6号状态,只能加工至5号的状态(参见现有文献2)。究其原因,只要存在管材的加工上,切割索加工前需要将炸药全部压紧在管材内,管材外径一般在5
‑
10
㎜
、壁厚一般在0.2
‑
0.5
㎜
左右;然后将管材逐渐加工至6号或接近6号状态,目前主要采用冷拔技术,这种方式需要保持切割索在70℃以下加工,而且冷拔过程中产热量较大,管材很容易走偏(横截面歪斜)、卡管,在卡管时需要拆开模具取出废品后才能继续新的加工,因此成品率极低,效率也非常低,目前一台设备一天也只能加工6根左右。
4.现有文献1:美国nasa technical memorandum 在1984年5月公开的名为“pyrotechnic shock: a literature survey of the linear shaped charge (lsc)”、文章编号nasa tm
ꢀ‑
82583。
5.现有文献2:american institute of aeronautics and astronautics在2005年、41st aiaa/asme/sae/asee joint propulsion conference & exhibit 10
ꢀ‑ꢀ
13 july 2005, tucson, arizona,发表的
ꢀ“
performance analysis of linear shaped charge for aerospace applications”,作者:meryl mallery* and tom kozlowski
†ꢀ
ensign
‑
bickford aerospace and defense company simsbury, ct 06070。
技术实现要素:6.有鉴于现有技术的上述缺陷,本发明所要解决的技术问题是提供一种聚能切割索加工装置,其能够实现切割索从圆管状态逐步加工至“v”形状态,且其横截面非常接近6号状态。
7.为实现上述目的,本发明提供了一种聚能切割索加工装置,包括:菱形辊压机,用于将圆管加工成扁管;v形辊压机,用于将扁管加工成v形管。
8.预压输送模块,预压输送模块包括:输送机构,用于输送切割索;
第一预压机构,用于在圆管一端压出扁管,以便于后续菱形辊压机的加工;第二预压机构,用于在扁管一端压出凹槽,以获得槽管,从而方便后续v形辊压机辊压加工出v形管。
9.优选地,菱形辊压机包括菱形油缸、第一菱形板、第二菱形板、菱形座、存储箱、菱形侧板,所述菱形座两两为一对,且菱形侧板分别有一对菱形座;靠近第一预压机构的一对菱形座分别与一个第一菱形模装配固定,靠近第二预压机构的一对菱形座分别与一个第二菱形模装配固定;位于下方的菱形座分别固定在存储箱上,且此菱形座与菱形导向轴底部装配固定,菱形导向轴顶部分别穿过两个第一菱形模、另一菱形座后与第一菱形板装配固定,第一菱形板上固定有菱形油缸,菱形油缸的菱形伸缩轴穿过第一菱形板后与第二菱形板装配固定;位于上方的菱形座与菱形导向轴可轴向滑动装配且此菱形座通过第二菱形气管固定在第二菱形板上或直接固定在第二菱形板上;所述菱形侧板有两块,且两块菱形侧板的底部分别固定在存储箱上,两块菱形侧板之间沿着切割索加工方向上安装有多根菱形辊,所述菱形辊可圆周转动地套装在菱形辊轴上;所述菱形辊上设置有与第二过渡管贴合的菱形辊槽。
10.优选地,所述菱形辊轴两端分别穿出两块菱形侧板后与菱形让位组件的让位滑块装配固定,所述菱形让位组件还包括固定在菱形侧板上的两块让位导向板,让位滑块卡合、可滑动地安装在两块让位导向板之间,让位滑块与让位弹簧一端装配固定,让位弹簧另一端装入让位调节筒内且与让位调节环装配,所述让位调节筒内部为让位滑孔,让位调节环可圆周转动、可轴向滑动地安装在让位滑孔内,所述让位调节筒固定在让位固定板上,让位固定板固定在菱形侧板上,所述菱形侧板上还设置有与让位滑块卡合、可滑动装配的菱形侧板槽,所述让位滑块可在菱形侧板槽内上下滑动;所述让位调节环固定在让位调节杆一端,让位调节杆另一端穿过让位固定板后与让位旋钮装配固定,所述让位调节杆与让位固定板通过螺纹旋合装配。
11.优选地,菱形辊内部为中空的菱形辊孔,菱形辊槽处设置有贯穿的、与菱形通槽连通的菱形降温孔,所述菱形辊轴安装在菱形辊孔内,所述菱形通槽设置在菱形辊孔内壁上且两端在轴向上贯穿菱形辊;菱形辊两端分别装入菱形介质箱内,所述菱形介质箱内部为中空的菱形介质腔,菱形介质腔与菱形通槽两端,且菱形介质箱与菱形辊密封、可圆周转动、不可轴向移动装配;所述菱形介质箱内安装有菱形感温板,菱形感温板与菱形辊的外壁贴合;所述菱形感温板内设置有感温孔,所述感温孔的开口端安装有感温限位环;且感温孔内卡合、可轴向滑动地安装有感温环,感温环安装在感温轴一端上,感温轴另一端穿过感温限位环后进入调节滑板槽内且与调节滑板装配固定,所述感温环不能穿过感温限位环,且感温孔内、感温环与感温孔封闭端之间安装有记忆弹簧;菱形介质箱安装在菱形侧板内侧。
12.优选地,所述调节滑板槽设置在第三菱形管内,且第三菱形管内还分别设置有节流槽、连通孔、主流通道,所述调节滑板还与节流推杆一端装配固定,节流推杆另一端穿过调节滑板槽后装入连通孔内且与节流块装配固定,所述节流块卡合、可滑动地安装在节流槽内,且所述节流推杆位于调节滑板与调节滑板槽靠近节流槽的内壁之间的部分上套装有复位弹簧,复位弹簧用于产生阻碍调节滑板上移的弹力,调节滑板卡合、可滑动地安装在调
节滑板槽内;所述节流槽位于节流块的两侧分别与连通孔、节流管一端连通,节流管另一端与菱形介质腔连通,所述节流块初始状态时部分遮挡连通孔、节流管与节流槽连通处;所述主流通道两端分别与一根第二菱形气管内部连通,所述第二菱形气管、第三菱形气管分别安装在菱形侧板上,两根第二菱形气管分别通过第四菱形气管与与之对应的第二菱形模通道、第一菱形模通道一端连通,所述第二菱形模通道、第一菱形模通道另一端分别与第一菱形进料管、第一菱形排料管一端连通,且第二菱形模通道、第一菱形模通道分别设置在第二菱形模第一菱形模内。
13.优选地,v形辊压机包括第二v形板、v形座、第一v形模、第二v形模、v形辊机构、v形油缸、第一v形板,v形辊机构用于通过v形辊挤压第三过渡管两侧以加工v形管;所述第二v形板位于第一v形模、第二v形模之间的部分上安装有v形辊压架,v形辊压架包括两块相互平行安装在v形辊压侧板,两块v形辊压侧板之间安装有多个沿着第三过渡管移动方向分布的v形辊压轮,v形辊压轮套装在第一v形辊轴上,第一v形辊轴与两块v形辊压侧板可圆周转动装配;v形支架与v形导向轴底部装配固定,v形导向轴顶部穿过第二v形板后与第一v形板装配固定,第二v形板可在v形导向轴轴向上滑动;所述v形油缸安装在第一v形板上,且v形油缸的v形伸缩轴穿过第一v形板后与第二v形板装配固定。
14.优选地,所述v形辊机构包括两根v形辊、两根第二v形辊轴,两根v形辊分别可圆周转动、不可轴向移动地套装在与之对应的第二v形辊轴上,两根第二v形辊轴相互靠近一端通过第一v形销铰接,所述第一v形销位于v形管的v形底正下方;第一v形销安装在第一v形连杆顶部,第一v形连杆底部固定在v形支板上;v形支板的两端上分别设置有第一v形立板、第二v形立板、支板滑槽,所述第一v形立板、第二v形立板分别固定在支板滑槽两端;所述第二v形辊轴另一端上固定有辊轴铰接块,辊轴铰接块通过第二v形销与第二v形连杆顶部铰接,所述第二v形连杆底部穿过支板滑槽且与之卡合、可滑动装配;所述第二v形连杆靠近第二v形销一端通过第三v形销与第三v形连杆一端铰接,所述第三v形连杆另一端通过第四v形销与v形升降台铰接,所述v形升降台固定在v形升降杆顶部装配固定,v形升降杆底部穿过v形支板且与之卡合、可滑动装配,所述v形升降杆上设置有升降螺纹孔,升降螺纹孔与升降螺杆顶部通过螺纹旋合装配,升降螺杆底部与v形底板可圆周转动、不可轴向移动装配,v形底板通过v形支撑板与v形支板装配固定,所述升降螺杆上套装固定有蜗轮,蜗轮与蜗杆部分啮合并构成蜗轮蜗杆传动机构,蜗杆设置在升降驱动轴上,升降驱动轴与升降电机的输出轴通过联轴器连接固定。
15.优选地,还包括侧推组件,所述侧推组件包括第一v形立板、第二v形立板、侧推弹簧、侧推调节筒、侧推调节杆、测推导向轴、侧推受力板,所述侧推弹簧一端固定在侧推受力板上、另一端装入侧推调节筒内且与侧推调节杆的端面压紧,所述侧推调节筒固定在第一v形立板上,所述侧推调节杆一端穿过第一v形立板后装入侧推调节筒内且与第一v形立板通过螺纹旋合装配,所述侧推调节杆另一端上固定有侧推旋钮,所述侧推受力板通过侧推弹簧的弹力压紧在第二v形连杆侧面上,且所述侧推受力板上还设置有侧推导向块,侧推导向块卡装入v形连杆槽内且与之卡合、可滑动装配;所述测推导向轴固定在侧推受力板上且穿
过第一v形立板,测推导向轴可相对于第一v形立板轴向滑动。
16.优选地,所述第一预压机构包括第一预压板、第二预压板、第三预压板、预压油缸、预压模,所述预压模有两个,两个预压模相互贴紧;位于下方的预压模、第一预压板、第二预压板分别固定在第三预压板上,位于上方的预压模与预压油缸的预压伸缩轴装配固定,所述预压伸缩轴穿过第二预压板后装入安装在第二预压板上的预压油缸内;所述预压模内部设置有成型槽,所述成型槽用于将切割索预压成需要的形状;所述第二预压机构的预压模内有与扁管卡合装配的成型槽,且位于上方的预压模上固定有预压凸块,在位于上方的预压模向位于下方的预压模下压时,通过预压凸块在扁管上压出凹槽。
17.优选地,还包括输送机构、预压电磁铁,用于输送切割索;所述输送机构包括输送电机、输送架,所述输送电机安装在输送架上,输送架上分别安装有第一输送立板、第二输送立板、第三输送立板,所述第二输送立板、第三输送立板之间安装有两根输送辊,两根输送辊分别套装固定在两根输送辊轴上,输送辊轴分别与第二输送立板、第三输送立板可圆周转动装配,其中一根输送辊轴一端穿过第一输送立板后与输送电机的输出轴通过联轴器连接固定;两根输送辊轴上还分别套装固定有一个相互啮合传动的输送齿轮;预压电磁铁安装在第五预压板上,第五预压板固定在第三预压板上,第五预压板上还固定有第四预压板,预压电磁铁的电磁伸缩轴一端穿过第四预压板、第三预压板后进入预压模上方,且此端上设置有伸缩斜面,所述电磁伸缩轴位于第四预压板、第三预压板之间的部分上固定有预压限位环,所述电磁伸缩轴位于第四预压板、预压限位环之间的部分上套装有预压弹簧;位于上方的预压模与伸缩斜面对应处设置有能与之配合的预压模斜面。
18.本发明的有益效果是:1、本发明可以实现切割索从圆管状态逐渐加工至“v”形状态,且采用辊压和冷拔综合的设计,能够实现切割索的快速加工,因此效率较高,目前样机效率已经能达到合格品一天20根左右。另外通过过载设计,使得不易卡管,同时还能自动纠偏,从而既提高效率,又提高了合格率。
19.2、本发明的预压输送模块能够通过第一预压机构实现圆管加工成类似于菱形的扁管,从而为后期菱形辊压机连续辊压圆管提供基础。同时,还能够通过第二预压机构在扁管上压出聚能角,以便于后续v形辊压机连续辊压成型。另外还通过多个输送机构实现切割索的送料、牵拉。
20.3、本发明的菱形辊压机通过辊压加拉拔的方式可以实现圆管逐渐变为标准的扁管。而且由于采用菱形辊圆周转动辊压的方式,可以大大降低摩擦力,从而降低系统能耗、发热量,同时在菱形辊上设置渐变的菱形辊槽可以有效地对切割索进行引导、纠偏、辊压,从而可以大大增加生产效率和产品合格率。
21.4、本发明的v形辊压机通过每对v形辊向槽管两侧同时挤压的方式能够快速地加工出切割索两侧的v形,而且v形辊采用可圆周转动的方式进行辊压,可以有效降低加工中的发热量,从而降低能耗。另外每对v形辊采用通过第一辊压销相互同步转动的联动方式,可以有效地保证加工出来的v形侧面基本对称,从而提高合格率。
附图说明
22.图1是现有聚能切割索截面的研究结构示意图。
23.图2
‑
图3是本发明的结构示意图。
24.图4是第一预压机构、输送机构、菱形辊压机的结构示意图。
25.图5是第一预压机构、输送机构在圆管轴线所在中心面处剖视图。
26.图6是菱形辊压机、输送机构在圆管轴线所在中心面处剖视图。
27.图7
‑
图9是第一预压机构的结构示意图。
28.图10是第二预压机构在槽管横截面方向上的剖视图(预压伸缩轴轴线上)。
29.图11是输送机构改进结构示意图。
30.图12
‑
图17为菱形辊压机结构示意图。其中图14、图16分别为感温轴轴线所在中心面、菱形辊轴轴线所在中心面处剖视图。图15、图17分别为图14、图16中f1处、f2处放大图。
31.图18
‑
图19为第一菱形模、第二菱形模结构示意图。
32.图20
‑
图21为v形辊压机结构示意图。其中图20为v形辊压机在v形伸缩轴轴线所在中心面处剖视图。
33.图22
‑
图24是v形辊机构的结构示意图,其中图22为最靠近槽管一侧的v形辊机构,图23为最靠近v形管一侧的v形辊机构。图23为v形辊轴轴线所在中心面处剖视图。图24为侧推组件结构示意图。
34.图25
‑
图26为第一v形膜、第二v形膜结构示意图。
具体实施方式
35.下面将结合本发明实施例中的附图,对本发明实施例中的技术方案进行清楚、完整地描述。
36.在本发明的描述中,需要理解的是,术语“上”、“下”、“前”、“后”、“左”、“右”、“顶”、“底”、“内”、“外”等指示的方位或位置关系为基于附图所示的方位或位置关系,仅是为了便于描述本发明和简化描述,而不是指示或暗示所指的装置或元件必须具有特定的方位、以特定的方位构造和操作,因此不能理解为对本发明的限制。为了便于表述,本案将聚能切割索简称为切割索。
37.参见图2
‑
图24,本实施例的聚能切割索加工装置,包括:菱形辊压机a,用于将圆管110加工成扁管120;v形辊压机b,用于将扁管120加工成v形管140。
38.还包括预压输送模块,预压输送模块包括:输送机构c300,用于输送切割索;第一预压机构c100,用于在圆管110一端压出扁管120,以便于后续菱形辊压机a的加工;第二预压机构c200,用于在扁管120一端压出凹槽131,以获得槽管130,从而方便后续v形辊压机b辊压加工出v形管140。本实施例中,圆管110、第一过渡管111、扁管120、第二过渡管121、槽管130、第三过渡管141、v形管140各为切割索的各个加工成型状态。
39.参见图2
‑
图11,所述输送机构c300包括输送电机c310、输送架c320,所述输送电机c310安装在输送架c320上,输送架c320上分别安装有第一输送立板c321、第二输送立板
c322、第三输送立板c323,所述第二输送立板c322、第三输送立板c323之间安装有两根输送辊c330,两根输送辊c330分别套装固定在两根输送辊轴c340上,输送辊轴c340分别与第二输送立板c322、第三输送立板c323可圆周转动装配,其中一根输送辊轴c340一端穿过第一输送立板c321后与输送电机c310的输出轴通过联轴器连接固定,从而使得输送电机c310能够驱动输送辊轴c340圆周转动;两根输送辊轴c340上还分别套装固定有一个相互啮合传动的输送齿轮c350,这就使得两根输送辊轴c340可以同步以相反方向转动,从而驱动两根输送辊c330将切割索夹紧以输送切割索。本实施例中,输送辊c330采用高摩擦系数材料制成,如橡胶,这种设计主要是为了保证输送辊c330与切割索的摩擦力,从而保证对切割索施加足够的推力或拉力,以驱动切割索运行。
40.参见图11,由于输送辊c330长时间使用时会大量生热,这个热量会影响输送辊c330的输送能力以及或传导至切割索,造成合格率下降,对此发明人进行如下改进:在位于下方的输送辊c330处设置冷却箱c360,冷却箱内部为中空的冷却腔c361,冷却腔内装有冷却液c370,冷却液c370用于冷却切割索100,本实施例的冷却液可以直接选择现有的切屑冷却液。位于下方的输送辊c330底部浸入冷却液c370内。从而在输送切割索时能够将冷却液不断涂抹在切割索上以起到冷却效果,同时也是对此输送辊c330进行了冷却。优选地,为了避免输送辊c330一次携带过多的冷却液至切割索,申请人还设计了刮板380,刮板380用于刮掉输送辊c330上多余的冷却液。
41.在位于上方的输送辊c330上设置输送散热孔c331,同时在与此输送辊c330装配的输送辊轴c340上设置输送送风槽c341,输送送风槽c341与输送散热孔c331一端连通,输送散热孔c331另一端贯穿输送辊c330。使用时,输送送风槽c341接入冷风,冷风从输送散热孔c331内输出,从而可以对切割索、输送辊c330进行散热、降温,而输送散热孔c331的设计也增加了输送辊c330的摩擦系数。
42.所述第一预压机构c100包括第一预压板c121、第二预压板c122、第三预压板c123、预压油缸c110、预压模c140,所述预压模c140有两个,两个预压模c140相互贴紧;位于下方的预压模c140、第一预压板c121、第二预压板c122分别固定在第三预压板c123上,位于上方的预压模c140与预压油缸c110的预压伸缩轴c111装配固定,所述预压伸缩轴c111穿过第二预压板c122后装入安装在第二预压板c122上的预压油缸c110内,预压油缸c110能够驱动预压伸缩轴c111轴向移动,从而驱动位于上方的预压模c140向上移动。
43.位于下方的预压模c140、第一预压板c121还分别与预压导向轴c130两端装配固定;预压导向轴c130穿过位于上方的预压模c140,且与此预压模c140可轴向滑动装配,以为此预压模c140的移动提供导向。
44.所述预压模c140内部分别设置有成型槽c141、过度槽c142、定位槽c143,所述定位槽c143用于使需要预压的切割索进入,所述成型槽c141用于将切割索预压成需要的形状,所述过度槽c142用于容纳预压后的切割索与未压的切割索的过度连接部分。
45.优选地,还包括预压电磁铁c150,预压电磁铁c150安装在第五预压板c125上,第五预压板c125固定在第三预压板c123上,第五预压板c125上还固定有第四预压板c124,预压电磁铁c150的电磁伸缩轴c170一端穿过第四预压板c124、第三预压板c123后进入预压模c140上方,且此端上设置有伸缩斜面c171,所述电磁伸缩轴c170位于第四预压板c124、第三
预压板c123之间的部分上固定有预压限位环c172,所述电磁伸缩轴c170位于第四预压板c124、预压限位环c172之间的部分上套装有预压弹簧c160,预压弹簧c160用于对预压限位环c172施加向伸缩斜面c171推动的推力。预压电磁铁c150通电后能够驱动电磁伸缩轴c170向其内部克服预压弹簧c160的弹力回缩。位于上方的预压模c140与伸缩斜面c171对应处设置有能与之配合的预压模斜面c144,在此预压模c140上移时,预压模斜面c144与伸缩斜面c171配合以挤压电磁伸缩轴c170,从而使得此预压模c140穿过电磁伸缩轴c170,然后电磁伸缩轴c170在预压弹簧c160的弹力下复位字防止预压模c140下移复位。需要预压模c140下移复位时,预压电磁铁得电,将电磁伸缩轴c170拉出预压模c140下方,然后预压油缸c110启动,从而驱动预压模c140下移复位即可。这种设计是因为预压只需要在每根切割索前端加工时才需要,后续不需要,因此预压完成后,需要将两个预压模分离,从而防止影响切割索的运行。
46.所述第二预压机构c200与第一预压机构c100的结构基本一样,不同之处在于,第一预压机构c100用于将圆管110预压为扁管120,第二预压机构c200用于在扁管120上压制凹槽131从而获得槽管130。具体为:所述第二预压机构c200的预压模c140内只有为与扁管120卡合装配的成型槽c141,且位于上方的预压模c140上固定有预压凸块c180,在位于上方的预压模c140向位于下方的预压模c140下压时,能够通过预压凸块c180在扁管120上压出凹槽131,从而获得槽管130。预压完成后位于上方的预压模c140上移穿过电磁伸缩轴c170,从而通过电磁伸缩轴c170限制其下移即可。
47.参见图2
‑
图6、图12
‑
图19,所述菱形辊压机a包括菱形油缸a210、第一菱形板a110、第二菱形板a120、菱形座a130、存储箱a140、菱形侧板a150,所述菱形座a130两两为一对,且菱形侧板a150分别有一对菱形座a130;靠近第一预压机构的一对菱形座a130分别与一个第一菱形模a410装配固定,靠近第二预压机构的一对菱形座a130分别与一个第二菱形模a420装配固定;位于下方的菱形座a130分别固定在存储箱a140上,且此菱形座a130与菱形导向轴a310底部装配固定,菱形导向轴a310顶部分别穿过两个第一菱形模a410、另一菱形座a130后与第一菱形板a110装配固定,第一菱形板a110上固定有菱形油缸a210,菱形油缸a210的菱形伸缩轴a211穿过第一菱形板a110后与第二菱形板a120装配固定,从而在菱形油缸a210启动后能够驱动第二菱形板a120沿着菱形伸缩轴a211轴向移动。
48.位于上方的菱形座a130与菱形导向轴a310可轴向滑动装配且此菱形座a130通过第二菱形气管a620或直接固定在第二菱形板a120上;所述菱形侧板a150有两块,且两块菱形侧板a150的底部分别固定在存储箱a140上,两块菱形侧板a150之间沿着切割索加工方向上安装有多根菱形辊a220,所述菱形辊a220可圆周转动地套装在菱形辊轴a320上,所述菱形辊轴a320两端分别穿出两块菱形侧板a150后与菱形让位组件a500的让位滑块a570装配固定,所述菱形让位组件a500还包括固定在菱形侧板a150上的两块让位导向板a510,让位滑块a570卡合、可滑动地安装在两块让位导向板a510之间,让位滑块a570与让位弹簧a560一端装配固定,让位弹簧a560另一端装入让位调节筒a530内且与让位调节环a540装配,所述让位调节筒a530内部为让位滑孔a531,让位调节环a540可圆周转动、可轴向滑动地安装在让位滑孔a531内,所述让位调节筒a530固定在让位固定板a520上,让位固定板a520固定在菱形侧板a150上,所述菱形侧板a150上还设置有与让位滑块a570卡合、可滑动装配的菱
形侧板槽a151,所述让位滑块a570可在菱形侧板槽a151内上下滑动。所述让位调节环a540固定在让位调节杆a550一端,让位调节杆a550另一端穿过让位固定板a520后与让位旋钮a551装配固定,所述让位调节杆a550与让位固定板a520通过螺纹旋合装配。在需要调节让位弹簧对让位滑块a570的阻尼时,可以通过调节转让位调节环a540在让位滑孔a531内的位置以调节对让位弹簧的预先压缩情况。
49.优选地,所述让位滑块a570上设置有让位导向条a571,所述让位导向板a510与让位导向条对应处设置有与之卡合装配的让位导向槽a511。这种设计主要是为了防止菱形辊轴产生轴向位移。
50.所述菱形辊a220上设置有与第二过渡管121贴合的菱形辊槽a221,且菱形辊a220内部为中空的菱形辊孔a224,菱形辊槽a221处设置有贯穿的、与菱形通槽a223连通的菱形降温孔a222,所述菱形辊轴a320安装在菱形辊孔a224内,所述菱形通槽a223设置在菱形辊孔a224内壁上且两端在轴向上贯穿菱形辊a220;菱形辊a220两端分别装入菱形介质箱a160内,所述菱形介质箱a160内部为中空的菱形介质腔a161,菱形介质腔a161与菱形通槽a223两端,且菱形介质箱a160与菱形辊a220密封、可圆周转动、不可轴向移动装配。所述菱形介质箱a160内安装有菱形感温板a170,菱形感温板a170与菱形辊a220的外壁贴合且采用高导热系数材料制成,如铜、铝合金、碳纤维等。所述菱形感温板a170内设置有感温孔a171,所述感温孔a171的开口端安装有感温限位环a172;且感温孔a171内卡合、可轴向滑动地安装有感温环a331,感温环a331安装在感温轴a330一端上,感温轴a330另一端穿过感温限位环a172后进入调节滑板槽a631内且与调节滑板a840装配固定,所述感温环a331不能穿过感温限位环a172,且感温孔a171内、感温环a331与感温孔a171封闭端之间安装有记忆弹簧a810,记忆弹簧a810在50
‑
60℃受热伸长,在低于50℃时自动回缩复位。菱形介质箱a160安装在菱形侧板a150内侧。
51.所述调节滑板槽a631设置在第三菱形管a630内,且第三菱形管a630内还分别设置有节流槽a632、连通孔a633、主流通道a634,所述调节滑板a840还与节流推杆a340一端装配固定,节流推杆a340另一端穿过调节滑板槽a631后装入连通孔a633内且与节流块a850装配固定,所述节流块a850卡合、可滑动地安装在节流槽a632内,且所述节流推杆a340位于调节滑板a840与调节滑板槽a631靠近节流槽a632的内壁之间的部分上套装有复位弹簧a820,复位弹簧a820用于产生阻碍调节滑板a840上移的弹力,调节滑板a840卡合、可滑动地安装在调节滑板槽a631内。
52.所述节流槽a632位于节流块a850的两侧分别与连通孔a633、节流管a650一端连通,节流管a650另一端与菱形介质腔a161连通,所述节流块a850初始状态时部分遮挡连通孔a633、节流管a650与节流槽a632连通处从而使得连通孔a633、节流管a650之间未全部连通。一旦感温板受热,从而使得记忆弹簧伸长,感温轴a330驱动调节滑板a840克服复位弹簧的弹力上移,从而使得节流块a850上移,也就使得连通孔a633、节流管a650与节流槽a632连通处逐渐变大,也就是增加连通孔a633向节流管a650的流量,从而使得进入菱形降温孔的降温介质(冷却液或冷风)增加,以使得菱形辊快速降温,这种设计无需温度传感器等电子设备的使用,且能够实现自动调节流量,从而可以按需进入冷却介质,以降低能耗。
53.所述主流通道a634两端分别与一根第二菱形气管a620内部连通,所述第二菱形气管a620、第三菱形气管a630分别安装在菱形侧板a150上,两根第二菱形气管a620分别通过
第四菱形气管a640与与之对应的第二菱形模通道a424、第一菱形模通道a414一端连通,所述第二菱形模通道a424、第一菱形模通道a414另一端分别与第一菱形进料管a611、第一菱形排料管a612一端连通,且第二菱形模通道a424、第一菱形模通道a414分别设置在第二菱形模a420第一菱形模a410内。使用时,第一菱形进料管a611进入恒压的冷却介质,冷却介质流过第二菱形模通道a424从而对第二菱形模a420进行降温,然后冷却介质进入第二菱形气管a620内,再分别进入第三菱形管a630的主流通道a634内,部分冷却介质进入菱形介质腔a161内、剩余部分进入第一菱形模通道a414内以对第一菱形模a410进行降温,最后通过第一菱形排料管a612排出。这种设计同时对第一菱形模、第二菱形模、菱形辊进行散热,从而能够有效地保证加工温度不超70℃。
54.所述第一菱形模a410上分别设置有可与扁管120卡合装配的菱形扁管槽a411、可与圆管110卡合装配的菱形圆管槽a412,从而使得预压后的扁管120、需要加工的圆管120均能穿过两个第一菱形模a410之间,从而实现对切割索的定位(横截面方向上),以防止后续辊压时产生偏移。优选地,靠近第一预压机构一端处设置有第一菱形倒料口a413,第一菱形倒料口a413用于便于预压后的扁管120、需要加工的圆管110进入菱形扁管槽a411、菱形圆管槽a412中。
55.所述第二菱形模a420上分别设置有可与扁管120卡合装配的扁管拉拔槽a421,所述扁管拉拔槽a421用于严格限制扁管120的通过,从而使得能够穿过扁管拉拔槽a421的扁管均为合格品,起到检测作用。一旦辊压后的扁管有少量的偏移,也能通过扁管拉拔槽a421的拉拔、限位作用实现冷拔,从而进行矫正,以增加合格率。优选地,所述扁管拉拔槽a421靠近第一菱形模a410一端上设置有第二菱形倒料口a423,第二菱形倒料口a423用于便于辊压后的扁管120进入扁管拉拔槽a421内。
56.优选地,所述菱形辊a220上的菱形辊槽a221沿着第一过渡管111的横截面逐渐变化,从而能够贴合与之对应的第一过渡管111的横截面。这种设计在对第一过渡管111辊压的同时,还通过菱形辊槽a221限制第一过渡管111的变形,从而增加产品合格率。
57.参见图2
‑
图3、图20
‑
图26,所述v形辊压机b包括v形油缸b210、第一v形板b110、第二v形板b120、v形支架b130、v形座b140、第一v形模b510、第二v形模b520、v形辊机构b400,所述第一v形模b510、第二v形模b520分别有两个,且第一v形模b510、第二v形模b520分别安装在v形支架b130靠近第二预压机构、远离第二预压机构的两端上;位于下方的第一v形模b510、第二v形模b520分别固定在v形支架b130上,位于上方的第一v形模b510、第二v形模b520分别固定在v形座b140上,v形座b140固定在第二v形板b120上;v形支架b130与v形导向轴b310底部装配固定,v形导向轴b310顶部穿过第二v形板b120后与第一v形板b110装配固定,第二v形板b120可在v形导向轴b310轴向上滑动;所述v形油缸b210安装在第一v形板b110上,且v形油缸b210的v形伸缩轴b211穿过第一v形板b110后与第二v形板b120装配固定,从而在v形油缸b210驱动v形伸缩轴b211轴向移动时能够驱动第二v形板b120同步移动。
58.所述第二v形板b120位于第一v形模b510、第二v形模b520之间的部分上还安装有v形辊压架b150,v形辊压架b150包括两块相互平行安装在v形辊压侧板b151、v形限位条b152,所述v形辊压侧板b151上下两端分别与第二v形板b120、v形限位条b152装配固定,所述v形限位条b152底面上设置有与第三过渡管141两个顶端逐渐贴合的v形限位槽b153;两
块v形辊压侧板b151之间安装有多个沿着第三过渡管141移动方向分布的v形辊压轮b220,v形辊压轮b220套装在第一v形辊轴b320上,第一v形辊轴b320与两块v形辊压侧板b151可圆周转动装配。优选地,至少两个v形辊压轮b220沿着第二过渡管121位于凹槽131处逐渐由切割索移动方向下移,直到v形辊压轮b220与凹槽131完全贴合装配。这种设计主要是为了在加工凹槽131时,逐渐通过多级v形辊压轮b220对第二过渡管121的凹槽过度部分122处进行逐渐辊压,从而实现逐渐变形以加工出合格的凹槽131,且这种加工效率比较高,不可控变形小。
59.每个v形辊压轮b220下方分别对应一个v形辊机构b400,所述v形辊机构b400包括两根v形辊b230、两根第二v形辊轴b330,两根v形辊b230分别可圆周转动、不可轴向移动地套装在与之对应的第二v形辊轴b330上,两根第二v形辊轴b330相互靠近一端通过第一v形销b341铰接,所述第一v形销b341位于v形管140的v形底142正下方,具体为第一v形销b341的轴线位于与v形底142轴向中线的正下方。这种设计主要是为了保证两根v形辊b230形成的夹角始终与v形底142的角度贴合,从而保证v形管140的加工精度。
60.第一v形销b341安装在第一v形连杆b410顶部,第一v形连杆b410底部固定在v形支板b460上;v形支板b460的两端上分别设置有第一v形立板b461、第二v形立板b462、支板滑槽b463,所述第一v形立板b461、第二v形立板b462分别固定在支板滑槽b463两端;所述第二v形辊轴b330另一端上固定有辊轴铰接块b331,辊轴铰接块b331通过第二v形销b342与第二v形连杆b420顶部铰接,所述第二v形连杆b420底部穿过支板滑槽b463且与之卡合、可滑动装配,从而使得第二v形连杆b420在正常状态时只能沿着其长度方向上移动。优选地,所述第二v形连杆b420上设置有v形连杆槽b421,所述支板滑槽b463内固定有与v形连杆槽b421卡合、可滑动装配的v形滑动导向块b463,这种设计就进一步保证了第二v形连杆b420在其长度方向上的移动。
61.所述第二v形连杆b420靠近第二v形销b342一端通过第三v形销b343与第三v形连杆b430一端铰接,所述第三v形连杆b430另一端通过第四v形销b344与v形升降台b440铰接,所述v形升降台b440固定在v形升降杆b450顶部装配固定,v形升降杆b450底部穿过v形支板b460且与之卡合、可滑动装配,所述v形升降杆b450上设置有升降螺纹孔b451,升降螺纹孔b451与升降螺杆b370顶部通过螺纹旋合装配,升降螺杆b370底部与v形底板b470可圆周转动、不可轴向移动装配,v形底板b470通过v形支撑板b471与v形支板b460装配固定,所述升降螺杆b370上套装固定有蜗轮b262,蜗轮b262与蜗杆部分b261啮合并构成蜗轮蜗杆传动机构,蜗杆部分b261设置在升降驱动轴b360上,升降驱动轴b360与升降电机b250的输出轴通过联轴器连接固定,从而使得升降电机能够驱动升降驱动轴圆周转动。
62.所述升降电机安装在v形底板b470上,且v形底板b470上还安装有拉绳位移传感器b240、拉绳导向板b472,拉绳导向板b472与拉绳转轴b380可圆周转动装配,拉绳转轴b380外套装有拉绳导向轮b270,拉绳位移传感器b240的拉绳b241绕过拉绳导向轮b270后与v形升降杆b450装配固定,从而通过拉绳位移传感器探测v形升降杆b450的位移量。
63.在第三过渡管141依次穿过各个v形辊机构b400时,首先在第三过渡管141端部达到与之对应的v形辊机构b400的v形辊b220后,第三过渡管141暂停移动,然后升降电机启动,以驱动v形升降杆b450轴向上移,从而驱动v形升降台b440上移,v形升降台b440通过第三v形连杆b430驱动第二v形连杆b420上移,第二v形连杆b420驱动两根第二v形辊轴b330以
第一v形销b341为中心相互靠近转动以挤压第三过渡管141两侧,从而挤压出第三过渡管141与此v形辊对应的侧面,此时第三过渡管141顶部进入v形限位槽b152内以完成形变。这样就通过多个v形辊逐渐将槽管130加工成v形管140。而在第一段第三过渡管141通过后各个v形辊机构保持不动,从而在后续的切割索通过时就能不断地对切割索进行辊压,从而连续加工出v形管140。
64.优选地,由于第二v形连杆b420在运行过程中会在v形支板b460的长度方向上产生位移,也就是与切割索移动方向的垂直方向。为了避免这种移动造成v形辊不稳定,从而影响成品,发明人还增加了侧推组件,所述侧推组件包括第一v形立板b461、第二v形立板b462、侧推弹簧b710、侧推调节筒b720、侧推调节杆b730、测推导向轴b350、侧推受力板b740,所述侧推弹簧b710一端固定在侧推受力板b740上、另一端装入侧推调节筒b720内且与侧推调节杆b730的端面压紧,所述侧推调节筒b720固定在第一v形立板b461上,所述侧推调节杆b730一端穿过第一v形立板b461后装入侧推调节筒b720内且与第一v形立板b461通过螺纹旋合装配,所述侧推调节杆b730另一端上固定有侧推旋钮b731,所述侧推受力板b740通过侧推弹簧的弹力压紧在第二v形连杆b420侧面上,且所述侧推受力板b740上还设置有侧推导向块b741,侧推导向块b741卡装入v形连杆槽b421内且与之卡合、可滑动装配。所述测推导向轴b350固定在侧推受力板b740上且穿过第一v形立板b461,测推导向轴b350可相对于第一v形立板b461轴向滑动。第二v形立板b462用于限制第二v形连杆b420向上移动的最大位移量。且在图23状态时,第二v形连杆b420受到v形辊施加的挤压力较大,因此此时第二v形连杆b420与第二v形立板b462贴合,可以有效增加第二v形立板b462的稳定性。
65.使用时,可以通过侧推旋钮调节侧推调节杆b730装入侧推调节筒b720内的深度,从而调节侧推弹簧的初始压缩弹力,使用时,通过这个弹力保持对v型辊b230的支撑。一旦v型辊b230处所受压力过大,则会对第二v形连杆b420产生一个以第三v形销b343为中心向v形升降杆b450转动的推力,这个推力对侧推受力板b740产生一个侧推的推力,一旦这个推力超过侧推弹簧的初始弹力则会驱动侧推受力板b740压缩侧推弹簧而移动,从而获得过载保护功能。
66.所述第一v形模b510上设置有与扁管120卡合装配的v形扁管槽b511,这种设计主要是为了定位扁管,同时对第二过渡管b121进行矫正,以增加加工精度。
67.所述第二v形模b520上设置有v形贴合槽b521、v形冷却通道b522,v形导向槽b523,所述v形导向槽b523设置在v形贴合槽b521靠近v形辊机构b400一端,用于引导加工后的v形管进入v形贴合槽b521,v形贴合槽b521的内壁与v形管的外壁完全贴合。v形冷却通道b522一端与v形进风管b610连通、另一端通过v形连接管b620与v形吹气块b630内部连通,v形吹气块b630面向v形辊机构b400一端上设置有无数贯穿的v形吹气孔b631。使用时,冷风从v形进风管b610进入,然后流经v形冷却通道b522以带走第二v形模b520上的热量,然后从v形吹气孔分别吹向v形辊b230、v形辊轮b220,从而实现对v形辊b230、v形辊轮b220的降温。由于v形辊b230、v形辊轮b220采用转动辊压的方式,因此产生的热量很少。而v形冷却通道b522可以通过冷拔的方式矫正变形的v形管,从而大大增加成品合格率,另外有冷风进行降温、且矫正量不大,因此加工温度一般不会超70℃。
68.本发明的运行过程如下:s1、切割索100为圆管110,此时需要通过第一预压机构在其一端上加工出扁管
120,然后第一预压机构驱动两个预压模分离;s2、输送机构将s1处理后的切割索100送入菱形辊压机a内,从而输出连续的扁管120;s3、第二预压机构在扁管120一端上压出凹槽131,获得槽管130;s4、槽管130进入v形辊压机,然后通过v形辊压辊b220辊压出连续的凹槽131,也就是连续的槽管130。同时,各个v形辊机构依次运行以通过v形辊挤压第三过渡管141两侧以逐渐挤压出v形管。
69.本发明未详述之处,均为本领域技术人员的公知技术。
70.以上详细描述了本发明的较佳具体实施例。应当理解,本领域的普通技术人员无需创造性劳动就可以根据本发明的构思作出诸多修改和变化。因此,凡本技术领域中技术人员依本发明的构思在现有技术的基础上通过逻辑分析、推理或者有限的实验可以得到的技术方案,皆应在由权利要求书所确定的保护范围内。