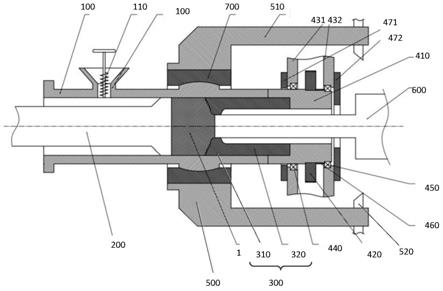
1.本发明涉及金属回收与塑性加工技术领域,尤其涉及一种金属切屑固态回收装置。
背景技术:2.金属切削加工过程会产生大量的金属切屑废料,从而造成资源的浪费。传统的金属切屑是通过重新冶炼
‑
铸造
‑
成形的方式进行制坯回收,这种方法的缺点是能耗大,回收过程涉及多个环节,会造成环境二次污染和回收费用高等问题。
3.近年来,金属切屑的回收利用开始广泛应用直接转换方法。应用直接转换法回收铝合金切屑时,金属利用率高,可以获得具有良好力学性能的回收材料。金属切屑回收再利用,将极大的减少开采和处理原材料的需求,从而节省大量的能源和水,同时,极大地限制原材料在开采过程中产生的环境退化问题。
4.在相关技术中,世界各国广泛对切削回收成形展开了大量研究,为了节约资源、保护环境以及提高经济效益,金属在固态回收领域的研究成为趋势。但是,传统的直接转换法多采用直接挤压的方式,这种方法会涉及相当大的能源消耗,且产品质量低,对切屑形态要求高,获得大的变形需要施加相当大的力,产品在挤压受力较大的部分易发生断裂伤,成形产品经质量检测普遍存在组织不均匀的现象,这增加了回收产品应用的安全风险。
5.目前很多工厂不够重视废物及切屑的处理,存在切屑露天堆放且抛酒严重的现象,回收利用金属切削碎屑成为了一个棘手的问题。然而,相比于其他金属废料,金属切削过程中产生的切屑形状及结构十分复杂,这使得金属切屑回收利用难度较大。因此研发一种处理彻底、回收快速、操作方便的金属切削碎屑回收利用装置,实现金属切屑的高性价比回收具有重要意义。
技术实现要素:6.本发明实施例提供了一种金属切屑固态回收装置,能够实现金属切屑的回收,且可对金属塑性加工,通过模具的设计实现高性能棒材的塑性成形。
7.本发明实施例所提供的技术方案如下:
8.本发明提供了一种金属切屑固态回收装置,包括:
9.内部中空的固定挤压筒,所述固定挤压筒包括相对的第一开口端和第二开口端,所述第一开口端和所述第二开口端之间的侧壁上设有切屑投料口;
10.挤压冲头,所述挤压冲头包括相对的第一端和第二端,所述第一端套入所述第一开口端内,且所述挤压冲头能够在所述固定挤压筒内部往复运动,以对从所述切屑投料口进入所述固定挤压筒内的金属切屑进行冲压;
11.成形模具,所述成形模具设置于所述第二开口端,且能够相对所述固定挤压筒进行旋转,所述成形模具包括具有锥形模具腔室的锥形模具部分和中空的旋转轴部分;所述锥形模具部分的模具腔室包括相对的入模口和出模口,所述入模口与所述挤压冲头的第一
端相对,所述出模口与所述旋转轴部分连接,所述锥形模具部分的模具腔室从所述入模口至所述出模口逐渐收敛,且所述旋转轴部分的远离所述锥形模具部分的一端为出料口;
12.旋转机构,与所述成形模具的旋转轴部分传动连接,用于驱动所述成形模具旋转;
13.推杆,设置于所述模具腔室内,并能够在所述模具腔体内往复运动。
14.示例性的,所述切屑投料口设置有螺旋下料机构,所述螺旋下料机构包括能够旋转的杆体,所述杆体的外周面设有螺旋挤压纹。
15.示例性的,所述锥形模具部分的模具腔室侧壁上设有螺旋状刀口面。
16.示例性的,所述锥形模具部分的锥度为45
°
~60
°
;所述入模口的边缘倒圆角,圆角半径r为10~20mm;所述出模口的边缘倒圆角,圆角半径r<0.1mm。
17.示例性的,所述成形模具的旋转方式包括单一方向旋转方式和/或往复旋转方式,旋转频率取值范围为2~8hz,所述单一方向旋转方式包括正转或反转,所述往复旋转方式的往复旋转角α=
±8°
。
18.示例性的,所述挤压冲头从所述第一端向所述第二端运动以冲压所述金属切屑时,运动速度为0.5~1mm/s。
19.示例性的,所述旋转机构包括齿轮传动机构,所述齿轮传动机构包括:
20.齿轮传动轴,所述齿轮传动轴包括齿轮传动轴和齿轮环,所述齿轮传动轴的外周面上设有轮齿,所述齿轮与所述轮齿啮合,所述齿轮传动轴与所述旋转轴部分通过花键连接;
21.齿轮箱,所述齿轮箱套设于所述齿轮传动轴上,并罩住所述齿轮环,所述齿轮箱包括位于所述齿轮环相对两侧的第一侧壁和第二侧壁,其中所述第一侧壁位于所述第二侧壁的靠近所述第一端的一侧;
22.设置于所述第一侧壁与所述齿轮传动轴之间的圆柱滚子轴承;
23.设置于所述第二侧壁与所述齿轮传动轴之间的推力球滚子轴承;
24.以及,套筒,所述套筒设置于所述第二侧壁与所述齿轮环之间。
25.示例性的,所述金属切屑固态回收装置还包括:设置于所述出料口处的切割机构,用于对所述出料口的坯料切割。
26.示例性的,所述金属切屑固态回收装置还包括固定座,所述固定座上设有装配口,所述固定挤压筒穿设于所述装配口,且所述装配口的内侧壁与所述固定挤压筒的外周面之间设有调心部件。
27.示例性的,所述固定座上沿所述固定挤压筒的轴向延伸,并位于所述固定挤压筒的相对两侧的两个支架,每一所述支架上设有一剪切片。
28.本发明实施例所带来的有益效果如下:
29.本发明实施例所提供的金属切屑固态回收装置,主要包括固定挤压筒、位于固定挤压筒上的切屑投料口、可往复移动的设置于所述固定挤压筒的第一端的挤压冲头、位于固定挤压筒第二端的可旋转的成形模具、可往复运动的设置于所述成形模具内部的推杆、及驱动所述成形模具旋转的旋转机构,该金属切屑固态回收装置对金属切屑的处理过程主要包括:预压实过程和旋转挤压成形过程,其中,所述挤压冲头往复运动,用于对从所述切屑投料口进入所述固定挤压筒内的金属切屑进行预压实(冷压实),具体的,在预压实过程中,所述挤压冲头往复运动进行冲压,所述推杆的靠近所述第一端的一端位于其往复运动
行程的最靠近第一端的位置(也就是,位于所述成形模具的所述入模口处),所述成形模具和所述推杆保持静止不动,这样,金属切屑会被所述挤压冲头的冲压而被压实在所述挤压冲头、所述固定挤压筒、所述成形模具及所述推杆的靠近所述第一端的一端所围设形成的空间内,这个预压实过程可压实挤压金属切屑,将切屑之间的较大缝隙去除而形成冷压实坯料;随后,进行旋转挤压成型过程,此时,所述挤压冲头仍往复运动进行冲压,所述成形模具不断旋转,所述推杆以预定速度向所述出模口所在一侧运动,此时,冷压实坯料在所述成形模具旋转与所述挤压冲头的反复冲压下发生旋转挤压变形,最终形成金属棒坯料,从所述出料口出料。
30.由此可见,本发明实施例所提供的金属切屑固态回收装置,相较于传统金属切屑回收方法中金属切屑的重铸以及铸造会产生大量的能源消耗的问题,通过成形模具旋转效应的挤压法直接对金属切屑转换,无需重新铸造,大大降低了能源消耗,同时,也提升了金属的回收利用效率;且本发明实施例的金属切屑固态回收装置通过将引入成形模具,进行旋转来改变金属切屑的塑性变形路径,增加金属在挤压过程中的流动性能,能减少成形过程中可能出现的缺陷。也就是说,通过挤压,改变材料微观组织结构,可以获得具有良好力学性能的回收材料,旋转挤压的过程中细化晶粒的过程更加均匀,降低了挤压模具周围的精度要求,提高了成品件的尺寸精度,同时细化的晶粒为成形棒材带来了均匀的质地和更高的强度和韧性,使适合之后更复杂的生产环境与更广泛的应用场景;此外,成形方式为塑性成形,大大降低了金属成型过程中的温度要求,减少了能源消耗,实现了对金属切屑的物理回收;同时,使用该加工成形方法时切屑为直接投入,避免了研磨中可能带入的杂质,是制备符合强度、韧性要求的优质金属棒材的有效工艺,具有很大的工业应用潜力。
附图说明
31.图1为本发明的金属切屑固态回收装置在冷压实过程的结构示意图;
32.图2为本发明的金属切屑固态回收装置中成形模具的侧面示意图;
33.图3为本发明的金属切屑固态回收装置中旋转机构的局部剖面图;
34.图4为图3中b
‑
b向中成形模具与齿轮传动轴配合示意图;
35.图5为图3中a
‑
a向齿轮环与齿轮传动轴装配示意图;
36.图6为本发明的金属切屑固态回收装置中成形模具的入模口的侧视图;
37.图7为本发明的金属切屑固态回收装置中在旋转挤压过程的结构示意图。
38.其中,各部件标记如下:
39.固定挤压筒100;切屑投料口110;挤压冲头200;成形模具300;锥形模具部分310;旋转轴部分320;旋转机构400;推杆600;调心部件700;螺旋状刀口面3111;入模口311;齿轮传动轴410;齿轮环420;齿轮箱430;圆柱滚子轴承440;推力球滚子轴承450;套筒460;第一端盖471;第二端盖472;固定座500;调心部件700;支架510;剪切片520;第一侧壁431;第二侧壁432。
具体实施方式
40.为使本发明实施例的目的、技术方案和优点更加清楚,下面将结合本发明实施例的附图,对本发明实施例的技术方案进行清楚、完整地描述。显然,所描述的实施例是本发
明的一部分实施例,而不是全部的实施例。基于所描述的本发明的实施例,本领域普通技术人员在无需创造性劳动的前提下所获得的所有其他实施例,都属于本发明保护的范围。
41.除非另外定义,本发明使用的技术术语或者科学术语应当为本发明所属领域内具有一般技能的人士所理解的通常意义。本发明中使用的“第一”、“第二”以及类似的词语并不表示任何顺序、数量或者重要性,而只是用来区分不同的组成部分。同样,“一个”、“一”或者“该”等类似词语也不表示数量限制,而是表示存在至少一个。“包括”或者“包含”等类似的词语意指出现该词前面的元件或者物件涵盖出现在该词后面列举的元件或者物件及其等同,而不排除其他元件或者物件。“连接”或者“相连”等类似的词语并非限定于物理的或者机械的连接,而是可以包括电性的连接,不管是直接的还是间接的。“上”、“下”、“左”、“右”等仅用于表示相对位置关系,当被描述对象的绝对位置改变后,则该相对位置关系也可能相应地改变。
42.如图1至图7所示,本发明实施例提供了一种金属切屑固态回收装置,包括:
43.内部中空的固定挤压筒100,所述固定挤压筒100包括相对的第一开口端和第二开口端,所述第一开口端和所述第二开口端之间的侧壁上设有切屑投料口110;
44.挤压冲头200,所述挤压冲头200包括相对的第一端和第二端,所述第一端套入所述第一开口端内,且所述挤压冲头200能够在所述固定挤压筒100内部往复运动,以对从所述切屑投料口110进入所述固定挤压筒100内的金属切屑进行冲压;
45.成形模具300,所述成形模具300设置于所述第二开口端,且能够相对所述固定挤压筒100进行旋转,所述成形模具300包括具有锥形模具腔室的锥形模具部分310和中空的旋转轴部分320;所述锥形模具部分310的模具腔室包括相对的入模口311和出模口,所述入模口311与所述挤压冲头200的第一端相对,所述出模口与所述旋转轴部分320连接,所述锥形模具部分310的模具腔室从所述入模口311至所述出模口逐渐收敛,且所述旋转轴部分320的远离所述锥形模具部分310的一端为出料口;
46.旋转机构400,与所述成形模具300的旋转轴部分320传动连接,用于驱动所述成形模具300旋转;
47.推杆600,设置于所述模具腔室内,并能够在所述模具腔体内往复运动。
48.本发明实施例所提供的金属切屑固态回收装置,主要包括固定挤压筒100、位于固定挤压筒100上的切屑投料口110、可往复移动的设置于所述固定挤压筒100的第一端的挤压冲头200、位于固定挤压筒100第二端的可旋转的成形模具300、可往复运动的设置于所述成形模具300内部的推杆600、及驱动所述成形模具300旋转的旋转机构400,该金属切屑固态回收装置对金属切屑的处理过程主要包括:预压实过程和旋转挤压成形过程,其中,所述挤压冲头200往复运动,用于对从所述切屑投料口110进入所述固定挤压筒100内的金属切屑进行预压实(冷压实),具体的,如图1所示,在预压实过程中,所述挤压冲头200往复运动进行冲压,所述推杆600的靠近所述第一端的一端位于其往复运动行程的最靠近第一端的位置(也就是,位于所述成形模具300的所述入模口311处),所述成形模具300和所述推杆600保持静止不动,这样,金属切屑会被所述挤压冲头200的冲压而被压实在所述挤压冲头200、所述固定挤压筒100、所述成形模具300及所述推杆600的靠近所述第一端的一端所围设形成的空间内,这个预压实过程可压实挤压金属切屑,将切屑之间的较大缝隙去除而形成冷压实坯料1,也就是说,冷压实过程实现切屑初步压实,得到的冷压实坯料1有利于后续
的旋转挤压成形;随后,如图7所示,进行旋转挤压成型过程,此时,所述挤压冲头200仍往复运动进行冲压,所述成形模具300不断旋转,所述推杆600以预定速度向所述出模口所在一侧运动,此时,冷压实坯料1在所述成形模具300旋转与所述挤压冲头200的反复冲压下发生旋转挤压变形,最终形成金属棒坯料2,从所述出料口出料。
49.由此可见,本发明实施例所提供的金属切屑固态回收装置,相较于传统金属切屑回收方法中金属切屑的重铸以及铸造会产生大量的能源消耗的问题,通过成形模具300旋转效应的挤压法直接对金属切屑转换,无需重新铸造,大大降低了能源消耗,同时,也提升了金属的回收利用效率;且本发明实施例的金属切屑固态回收装置通过将引入成形模具300,进行旋转来改变金属切屑的塑性变形路径,增加金属在挤压过程中的流动性能,能减少成形过程中可能出现的缺陷。也就是说,通过旋转挤压,改变材料微观组织结构,可以获得具有良好力学性能的回收材料,旋转挤压的过程中细化晶粒的过程更加均匀,降低了挤压模具周围的精度要求,提高了成品件的尺寸精度,同时细化的晶粒为成形棒材带来了均匀的质地和更高的强度和韧性,使适合之后更复杂的生产环境与更广泛的应用场景;此外,成形方式为塑性成形,利用摩擦力降低预热温度,大大降低了金属成型过程中的温度要求,减少了能源消耗,避免长时间加热而引起的晶粒长大,实现了对金属切屑的物理回收;同时,使用该加工成形方法时切屑为直接投入,避免了研磨中可能带入的杂质,是制备符合强度、韧性要求的优质金属棒材的有效工艺,具有很大的工业应用潜力。
50.以下对本发明实施例提供的金属切屑固态回收装置进行更为详细的说明。
51.在一些示例性的实施例中,如图1和图7所示,所述金属切屑固态回收装置还包括:设置于所述出料口处的切割机构,用于对所述出料口的坯料切割。
52.在一些示例性的实施例中,如图1和图7所示,所述切屑投料口110设置有螺旋下料机构111,所述螺旋下料机构111包括能够旋转的杆体,所述杆体的外周面设有螺旋挤压纹。所述螺旋下料机构111可设于所述切屑投料口110的中央。金属切屑在投料时,可通过搅拌粉碎下料,起到金属切屑初步搅拌粉碎的作用,同时防止切屑投料口110的堵塞发生,避免了研磨中可能带入的杂质。
53.在另一些实施例中,如图1和图6所示,所述锥形模具部分310的模具腔室侧壁上设有螺旋状刀口面3111。这样,具有锥形螺旋状刀口面3111的锥形模具部分310的入模口311使冷压实坯料1在受到挤压的同时,也较好地实现了扭转,从而大大增加了坯料的塑性变形程度,使得晶粒细化能力更强。
54.此外,在一些实施例中,所述锥形模具部分310的锥度为45
°
~60
°
;所述入模口311的边缘倒圆角,圆角半径r为10~20mm;所述出模口的边缘倒圆角,圆角半径r<0.1mm。需要说明的是,冷压实过程,推杆600位于所述锥形模具部分310的入模口311圆角尾端,这样,可使得冷压实坯料1更贴合模具,并且结合入模口311圆角的出模口圆角设计,进一步防止了挤压过程中坯料断裂的发生;此外,成形模具300入模口311为适当圆角设计,降低了材料成型过程中入模口311断裂的风险,出模口圆角半径小于0.1mm,减少了材料的粘连,加强了成形棒材坯料的表面质量。
55.在一些示例性的实施例中,所述成形模具300的旋转方式包括单一方向旋转方式和/或往复旋转方式,旋转频率取值范围为2~8hz,所述单一方向旋转方式包括正转或反转,所述往复旋转方式的往复旋转角α=
±8°
。采用上述方案,所述成形模具300进行旋转挤
压时的旋转方式可选,实现了不同形式的旋转挤压。
56.此外,一些实施例中,所述挤压冲头200从所述第一端向所述第二端运动以冲压所述金属切屑时,运动速度为0.5~1mm/s。
57.在一些实施例中,如图1至图7所示,所述旋转机构400包括齿轮传动机构,所述齿轮传动机构包括:齿轮传动轴410、齿轮环420、齿轮箱430、圆柱滚子轴承440、推力球滚子轴承450和套筒460;所述齿轮传动轴410的外周面上设有轮齿;所述齿轮环420与所述轮齿啮合,所述齿轮传动轴410与所述旋转轴部分320通过花键连接;所述齿轮箱430套设于所述齿轮传动轴410上,并罩住所述齿轮环420,所述齿轮箱430包括位于所述齿轮环420相对两侧的第一侧壁431和第二侧壁432,其中所述第一侧壁431位于所述第二侧壁432的靠近所述第一端的一侧;所述圆柱滚子轴承440设置于所述第一侧壁431与所述齿轮传动轴之间;所述推力球滚子轴承450设置于所述第二侧壁432与所述齿轮传动轴410之间;所述套筒460设置于所述第二侧壁432与所述齿轮环420之间。
58.上述方案中,所述旋转机构400通过齿轮传动轴410轴与所述成形模具300的旋转轴部分320通过花键配合,这种连接方式可拆卸,同时满足较大的挤压强度需求,实现了灵活的尺寸变化;此外,上述方案中采用滚动轴承代替滑动轴承减少转动过程中的摩擦力减少设备损耗。
59.此外,如图1所示,在所述齿轮箱430的相对两侧还设有第一端盖471和第二端盖472。
60.装配该传动机构时,可将第二端盖472与齿轮箱430的第二侧壁432依次套在齿轮传动轴上,并将第二端盖472与齿轮箱430之间通过螺栓固定,再将圆柱滚子轴承440、齿轮环420、套筒460、推力球滚子轴承450安装在齿轮传动轴460上,用第一端盖471与齿轮箱430的第一侧壁431通过螺栓固定。
61.此外,如图1所示,在一些示例性的实施例中,所述金属切屑固态回收装置还包括固定座500,所述固定座500上设有装配口,所述固定挤压筒100穿设于所述装配口,且所述装配口的内侧壁与所述固定挤压筒100的外周面之间设有调心部件700。
62.上述方案中,固定挤压筒100与调心部件700共同组成调心式推力滑动轴承,可一定程度降低对设备对心精度的要求。
63.此外,如图1和图7所示,所述固定座500上沿所述固定挤压筒100的轴向延伸,并位于所述固定挤压筒100的相对两侧的两个支架510,每一所述支架510上设有一剪切片520。采用上述方案,当旋转挤压出的金属棒坯料达到所需长度尺寸后,可停止挤压与旋转,两个剪切片520对心下降切除压余,得到所需产品,或用于后续的车削等加工场景。
64.需要说明的是,本实施例中,所述推杆600在冷压实过程中静止于成形模具300的入模口311,在旋转挤压过程中向出料口方向撤出,这样,利用推杆600的进退,实现冷压实、旋转挤压两个过程的连续,冷压实过程推杆600位于成形模具300入模口311圆角尾端,使冷压实坯料1形状更贴合模具,进一步防止了挤压过程中坯料断裂的发生。此外,成形模具300与固定挤压筒100、齿轮传动轴之间为可拆卸连接,实现了灵活的尺寸变化,可成形不同尺寸的棒材。
65.下面结合具体实施例对本发明所提供的金属切屑固态回收装置予以详细说明。
66.如图1至图7所示的金属切屑固态回收装置,以镁锂合金切屑为例,该装置的使用
步骤如下:
67.步骤s01、将第二端盖472与齿轮箱430的右半部分(第二侧壁432)依次套在齿轮传动轴上,并通过螺栓固定,再将圆柱滚子轴承440、齿轮环420、套筒、推力球轴承安装在齿轮传动轴上,用第一端盖471与齿轮箱430的左半部分(第一侧壁431)通过螺栓固定,齿轮环420与齿轮传动轴的装配如图5所示;
68.步骤s02、固定挤压筒100与调心部件700共同组成调心式推力滑动轴承;
69.步骤s03、根据所需尺寸的如图2所示的成形模具300进行安装,成形模具300的首端(锥形模具部分310)与固定挤压筒100滑动配合,尾端(旋转轴部分320)与齿轮传动轴通过如图3和图4所示花键配合;
70.步骤s04、推杆600向靠近所述第一端方向移动至成形模具300入模口311圆角尾端后停止;
71.步骤s05、采用液压机等控制所述挤压冲头200与所述固定挤压筒100对心后,向第二端所在方向移动至所述切屑投料口110的靠近第一端的一侧,将待挤压的镁锂合金切屑通过螺旋下料机构111内的螺旋挤压纹搅拌粉碎下料,进入所述固定挤压筒100中;
72.步骤s06、通过液压机等控制所述挤压冲头200向所述第二端方向移动(图中箭头x’所示方向),将镁锂合金切屑推入至由挤压冲头200的端部、固定挤压筒100、锥形模具部分310以及推杆600共同围设成的空间内;
73.步骤s07、通过液压机等控制控制挤压冲头200以一定速度挤压镁锂合金切屑得到初步压实后的冷压实坯料1;
74.步骤s08、将镁锂合金切屑与固定挤压筒100内温度预热至200℃左右并保温,使成形过程晶粒分布均匀;
75.步骤s09、推杆600向出料口所在方向移动(图中箭头x’所示方向),直至退出旋转挤压成形区域;
76.步骤s010、通过液压机等继续控制挤压冲头200向靠近第二端方向,按照一定速度往复挤压镁锂合金切屑,同时所述固定挤压筒100静止,所述齿轮传动轴通过传动装置带动成形模具300按照一定方式、方向与频率旋转,挤压过程中带有锥形螺旋状刀口面的成形模具300不断旋转,具有锥形螺旋状刀口面的入模口311,使坯料在受到挤压的同时,也较好地实现了扭转,旋转挤压的过程中细化晶粒的过程更加均匀,细化的晶粒为成形后的镁锂合金棒材带来了均匀的质地和更高的强度和韧性;
77.步骤s011、如图7所示,镁锂合金棒材达到所需长度尺寸后停止挤压与旋转,对称剪切片对心下降切除压余,得到所需产品,或用于后续的车削等加工场景。
78.由以上可知,本发明实施例提供的金属切屑固态回收装置可带来的有益效果如下:
79.(1)冷压实挤压将切屑之间的较大缝隙去除形成坯料,随后旋转挤压过程中坯料在成形模具300旋转与挤压冲头200的反复挤压下发生变形;
80.(2)同时在挤压过程中带有螺旋状刀口面的成形模具300不断旋转,具有锥形螺旋状刀口面的入模口311使坯料在受到挤压的同时,也较好地实现了扭转,从而大大增加了坯料的塑性变形程度;
81.(3)旋转挤压的过程中细化晶粒的过程更加均匀,降低了挤压模具周围的精度要
求,提高了成品件的尺寸精度,同时细化的晶粒为成形棒材带来了均匀的质地和更高的强度和韧性,使适合之后更复杂的生产环境与更广泛的应用场景;
82.(4)成形模具300入模口311为适当圆角设计降低了材料成型过程中入模口311断裂的风险,出模口圆角半径小于0.1mm,减少了材料的粘连,加强了成形棒材的表面质量;
83.(5)成形方式为塑性成形,利用摩擦力降低预热温度,大大降低了金属成型过程中的温度要求,减少了能源消耗,避免长时间加热而引起的晶粒长大,实现了对金属切屑的物理回收;
84.(6)通过一个装置,利用推杆600的进退实现冷压实、旋转挤压两个过程的连续,冷压实过程推杆600位于成形模具300入模口311圆角尾端,使冷压实坯料1形状更贴合模具,进一步防止了挤压过程中坯料断裂的发生。
85.(7)加工成形方法为切屑直接投入,旋转下料装置内为螺旋状刀口面形式,通过旋转将金属切屑送入固定挤压筒100内,旋转过程中能够对切屑进行初步的搅拌粉碎,同时防止入料口的堵塞发生,避免了研磨中可能带入的杂质;
86.(8)滚动轴承代替滑动轴承减少转动过程中的摩擦力减少设备损耗,轴向挤压采用调心式滑动轴承,可一定程度降低对设备对心精度的要求;
87.(9)成形模具300与齿轮传动轴以花键装配,可拆卸同时满足较大的挤压强度需求,实现了灵活的尺寸变化;
88.本发明为金属切屑的回收提供了一种物理方法,设计了多尺寸、高性能圆棒成形的金属切屑固态回收装置,通过一个装置,利用推杆600的进退实现冷压实、旋转挤压两个过程的连续,优化了工艺流程,实现了工序集中,具有很大的工业应用潜力,以上所述的使本发明的优选实施方式,应当指出的是,对于本技术领域考虑本发明所述的原理之下,还可有适当优化与改进,而这也应视作本发明的权利保护范围。