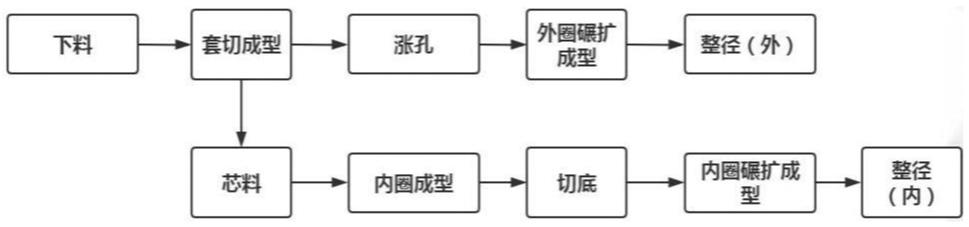
1.本发明涉及圆锥轴承套锻技术领域,尤其是涉及全自动套锻方法及工艺。
背景技术:2.轴承是汽车工业的重要基础零部件,而作为轴承类型之一的圆锥滚子轴承以其内、外套可分离、便于安装、可承受很大的径向和轴向联合负荷、负荷能力大且长寿命的特点而得到国内、外广泛应用。分析轴承结构,我们不难发现,影响圆锥滚子轴承产品质量、制造成本关键在于内、外套圈毛坯的锻压加工。统计显示,40%的制造成本消耗在轴承内外套圈锻压加工工序,其毛坯加工工艺的先进与否,决定制造成本的高低,从而直接影响该类产品的市场定位。
3.目前,国内生产厂家对圆锥轴承锻件的生产,一直沿用挤压扩孔的工艺模式,内、外圈分锻制成,内圈和外圈均是由一整个毛坯料制成,内圈是经挤压
‑
冲底制成,其中剔除的废料多,损耗的材料多;
4.外圈是经镦粗
‑
碾扩成型,各胚料均需要经过加热,能耗大,并且由于每个坯料都需要经过繁琐的处理工艺,因此生产的效率低下,技术含量不高,没有成本优势。
技术实现要素:5.根据现有技术存在的不足,本发明的目的是提供全自动套锻方法及工艺,具有减小材料损耗、提高生产效率、降低工艺成本的效果。
6.本发明的上述技术目的是通过以下技术方案得以实现的:
7.全自动套锻方法,将钢料加热至1000
‑
1050℃,再将加热的钢料分离成圆柱孔锥形料和圆柱形料芯两部分,圆柱孔锥形料和圆柱形料芯同时锻造得到相配套的外圈成品和内圈成品。
8.实现本发明所述的全自动套锻方法的工艺,包括如下步骤:
9.s1加热:通过输送辊将长条钢料送至中频感应透热炉一中一次升温,经过剪切冲床剪切得加热料段,加热料段放入中频感应透热炉二中二次升温得预热件;
10.s2镦粗、套切:将预热件在外圈压力机中镦粗成形、套切使预热件分离形成圆柱孔锥形料和圆柱形料芯两部分;
11.s3外圈锻造:将圆柱孔锥形料在外圈扩孔机内进行涨孔、碾扩成型处理,再送至外圈整径机中整外径得外圈锻件;
12.s4内圈锻造:机械手将圆柱形料芯翻转180
°
送至内圈压力机中镦粗、挤压成型、切底,再送至内圈整径机中整内径得内圈锻件;
13.s5:退火、车削:将外圈锻件、内圈锻件冷却后车加工得相配套的外圈成品和内圈成品。
14.本发明在一较佳示例中可以进一步配置为:所述s1步骤中,长条钢料一次升温的温度为750
‑
900℃,加热料段二次升温的温度为1000
‑
1050℃。
15.1.本发明采用两个中频感应透热炉对于生产的料段二次加热,加热质量好,且稳定,一次升温是在输送长料段的过程中预热,因此可以节省大量的加热时间,二次升温加热温度幅度小,可在锻造间隙中有充足的时间备料;
16.2.本发明中采用将一个毛坯料分套为圆柱孔锥形料及圆柱形料芯两部分,两部分在分料后可分别进行碾扩、挤压、整径处理,得到配套的轴承内外圈,各毛坯料只需要经过一次处理,可以降低能耗,改变了传统的轴承加工方式,简化工艺流程,成倍加快锻造效率,每分钟可生产11
‑
15个;
17.采用以上的工艺,可在套锻与单锻之间自由切换,设备的灵活度高,由于内圈是利用套切后的料芯制成,故剔除的废料少,降低了材料的耗损。
附图说明
18.图1是本发明的工艺流程示意图;
19.图2是本发明的工艺平面布置示意图;
20.图3是本发明的坯料加工流程示意图。
21.图中,1圆柱孔锥形料、2圆柱形料芯。
具体实施方式
22.以下结合附图对本发明作进一步详细说明。
23.参照图1
‑
3,全自动套锻方法,将钢料加热至1000
‑
1050℃,再将加热的钢料分离成圆柱孔锥形料1和圆柱形料芯2两部分,圆柱孔锥形料1和圆柱形料芯2同时锻造得到相配套的外圈成品和内圈成品。
24.实现本发明所述的全自动套锻方法的工艺,包括如下步骤:
25.加热:通过输送辊将长条钢料送至中频感应透热炉一中一次升温,一次升温的温度在750
‑
900℃之间,长条钢料由托架堆叠放置在工作台上,当一个长条钢料耗完后,下一个长条钢料自动地上料抬至输送辊道上,经过剪切冲床剪切得加热料段,加热料段放入中频感应透热炉二中二次升温得预热件,二次升温在1000
‑
1050℃之间。
26.镦粗、套切:将预热件在外圈压力机中镦粗成形、套切使预热件分离形成圆柱孔锥形料1和圆柱形料芯2两部分,镦粗使加热的坯料高度减少而横截面增大,其作用一是去除锻造氧化、作用二是为下一步挤压工步的制坯做准备,套切处理是利用压力机将一个预热件切成两个部分,圆柱孔锥形料1和圆柱形料芯2见图3,圆柱孔锥形料1用于锻造圆锥轴承的外圈,是原预热件的外边缘部分,圆柱形料芯2用于锻造圆周轴承的内圈,是原预热件的中间部分,该外圈与内圈相匹配。在镦粗、套切两个步骤是在外圈压力机中连续进行,料件由步进梁机器人自动地取料、运料。
27.外圈锻造:将圆柱孔锥形料1在外圈扩孔机内进行涨孔、碾扩成型处理,再送至外圈整径机中整外径得外圈锻件;圆柱孔锥形料1是通过机械手从外圈压力机中抓取至外圈扩孔机内部,外圈扩孔机采用“双工位”模式,可以连续处理料件。
28.内圈锻造:机械手将圆柱形料芯2翻转180
°
送至内圈压力机中镦粗、挤压成型、切底,再送至内圈整径机中整内径得内圈锻件;圆柱形料芯2由套切得到后落下定位在外圈压力机设置在底部的一运料机械手中夹紧,而内圈压力机安装在外圈压力机的一侧,机械手
作翻转动作后将圆柱形料芯2定位送至内圈压力机,镦粗使加热的圆柱形料芯2高度减少而横截面增大,挤压成型是采用相配套的模具将圆柱形料芯2挤压成型,切底即为“冲孔”,去除圆柱形料芯2中部废料,将其内孔打通。
29.退火、车削:将外圈锻件、内圈锻件冷却后车加工得相配套的外圈成品和内圈成品。
30.实施例1:
31.全自动套锻工艺,包括如下步骤:s1加热:通过输送辊将长条钢料送至中频感应透热炉一中一次升温,长条钢料一次升温的温度为750℃,经过剪切冲床剪切得加热料段,加热料段二次升温的温度为1000℃,加热料段放入中频感应透热炉二中二次升温得预热件;s2镦粗、套切:将预热件在外圈压力机中镦粗成形、套切使预热件分离形成圆柱孔锥形料1和圆柱形料芯2两部分;s3外圈锻造:将圆柱孔锥形料1在外圈扩孔机内进行涨孔、碾扩成型处理,再送至外圈整径机中整外径得外圈锻件;s4内圈锻造:机械手将圆柱形料芯2翻转180
°
送至内圈压力机中镦粗、挤压成型、切底,再送至内圈整径机中整内径得内圈锻件;s5:退火、车削:将外圈锻件、内圈锻件冷却后车加工得相配套的外圈成品一和内圈成品一。
32.实施例2:
33.全自动套锻工艺,包括如下步骤:s1加热:通过输送辊将长条钢料送至中频感应透热炉一中一次升温,长条钢料一次升温的温度为800℃,经过剪切冲床剪切得加热料段,加热料段二次升温的温度为1025℃,加热料段放入中频感应透热炉二中二次升温得预热件;s2镦粗、套切:将预热件在外圈压力机中镦粗成形、套切使预热件分离形成圆柱孔锥形料1和圆柱形料芯2两部分;s3外圈锻造:将圆柱孔锥形料1在外圈扩孔机内进行涨孔、碾扩成型处理,再送至外圈整径机中整外径得外圈锻件;s4内圈锻造:机械手将圆柱形料芯2翻转180
°
送至内圈压力机中镦粗、挤压成型、切底,再送至内圈整径机中整内径得内圈锻件;s5:退火、车削:将外圈锻件、内圈锻件冷却后车加工得相配套的外圈成品二和内圈成品二。
34.实施例3:
35.全自动套锻工艺,包括如下步骤:s1加热:通过输送辊将长条钢料送至中频感应透热炉一中一次升温,长条钢料一次升温的温度为900℃,经过剪切冲床剪切得加热料段,加热料段二次升温的温度为1050℃,加热料段放入中频感应透热炉二中二次升温得预热件;s2镦粗、套切:将预热件在外圈压力机中镦粗成形、套切使预热件分离形成圆柱孔锥形料1和圆柱形料芯2两部分;s3外圈锻造:将圆柱孔锥形料1在外圈扩孔机内进行涨孔、碾扩成型处理,再送至外圈整径机中整外径得外圈锻件;s4内圈锻造:机械手将圆柱形料芯2翻转180
°
送至内圈压力机中镦粗、挤压成型、切底,再送至内圈整径机中整内径得内圈锻件;s5:退火、车削:将外圈锻件、内圈锻件冷却后车加工得相配套的外圈成品三和内圈成品三。
36.本具体实施方式的实施例均为本发明的较佳实施例,并非依此限制本发明的保护范围,故:凡依本发明的结构、形状、原理所做的等效变化,均应涵盖于本发明的保护范围之内。