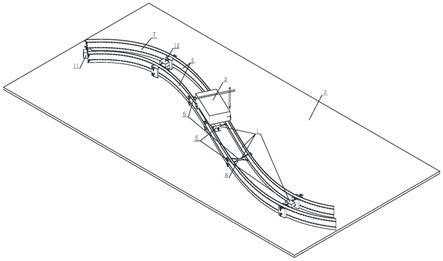
1.本发明涉及一种施工方法,尤其是涉及一种用于超大型异形曲线钢板切割的施工方法,属于大型钢结构物设计制造工艺技术领域。
背景技术:2.大型曲线钢结构的钢板下料切割,为减少热变形影响尺寸,采用先拼接后切割形状的方法,由于数控切割机床的尺寸有限,无法在数控切割机上完成切割,而半自动切割机的轨道都是直线形,也无法完成曲线的切割,因此通常只能采用人工切割。但人工切割的工作量大、效率低、切割质量不高。
3.公开号为cn108907352a的现有专利技术公开了一种应用于钢板曲线切割的简易轨道,但其存在以下的显著不足:
4.1、其磁吸方式难以取下,因此也不便于对轨道位置进行调节;
5.2、其磁块与轨道接触边为直线,对于曲线轨道难以控制其曲线形状;
6.3、其磁场开放,没有屏蔽,会对半自动切割机的滚动行径造成干扰;
7.4、其磁块只能对轨道下缘有一定约束,对上缘完全无约束,使轨道容易侧向失稳。
8.使用时,半自动切割机两侧均需要卡入滚轮凹槽,对于曲线情况下,需要对两条轨道的曲线进行精确定位,但要保持两条曲线轨道始终相等距离是比较困难的。
9.为此需要研发一种适用于半自动切割机使用的曲线轨道及其切割方法,以适应在数控切割机上完成的大型曲线钢结构的钢板的下料切割。
技术实现要素:10.本发明所要解决的技术问题是:提供一种切割质量相对较高,能有效提高切割效率的用于超大型异形曲线钢板切割的施工方法。
11.为解决上述技术问题所采用的技术方案是:一种用于超大型异形曲线钢板切割的施工方法,所述的施工方法以仿型切割工装作为支撑切割机的切割导轨,并将所述的仿型切割工装按规定形状布置到需要切割的钢板的相应位置处,然后通过所述的切割导轨在操作人员的配合下移动切割机完成所述超大型异形曲线钢板切割的切割工作,
12.其中所述的仿型切割工装至少包括导轨组件、支撑固定组件和连接安装组件,在所述连接安装组件配合下可拆卸的连接为一个整体的所述导轨组件,通过所述的支撑固定组件按要求的异形曲线可拆卸的布置在需要切割的钢板上。
13.进一步的是,所述的导轨组件包括两根高强柔韧的金属导轨板,两根沿竖向平行布置的金属导轨板通过所述的连接安装组件可拆卸的连接为一个整体,分别与两根金属导轨板连接的支撑固定组件可拆卸的吸附在需要切割的钢板上。
14.上述方案的优选方式是,两根所述的金属导轨板中包括一根主导轨板和一根辅助导轨板,所述主导轨板的顶端设置有走行结构,在所述的走行结构上设置有细密走行齿,所述辅助导轨板的顶端为平面结构。
15.进一步的是,所述的走行结构为设置在主导轨板顶端的三角形横截面或圆弧形横截面,所述的细密走行齿相应的设置在所述的三角形横截面或圆弧形横截面上。
16.上述方案的优选方式是,所述的连接安装组件包括多组x型安装连接架,沿竖向平行布置的两根金属导轨板通过沿长度方向顺序设置的各组x型安装连接架连接为一个整体。
17.进一步的是,每一组所述的x型安装连接架均包括一块连接板和四套固定连接螺杆件组,各套所述的固定连接螺杆件组从四个方向呈x型的与所述的连接板可拆卸的固定连接,各套固定连接螺杆件组通过未与连接板连接的一端与相应位置的金属导轨板可拆卸的连接。
18.上述方案的优选方式是,所述的支撑固定组件包括简式磁吸固定装置和复式磁吸固定装置,通过x型安装连接架连接为一个整体的两根金属导轨板在简式磁吸固定装置和复式磁吸固定装置的配合下按要求的异形曲线可拆卸的布置在需要切割的钢板上。
19.进一步的是,所述的简式磁吸固定装置包括一个开关式磁力座和四套固定连接螺杆件组,各套所述的固定连接螺杆件组从四个方向呈x型的与所述的开关式磁力座可拆卸的固定连接,各套固定连接螺杆件组通过未与开关式磁力座连接的一端与相应位置的金属导轨板可拆卸的连接,
20.所述的复式磁吸固定装置包括曲线调节块组、固定连接调整螺杆组和所述的开关式磁力座,所述的曲线调节块组通过所述的固定连接调整螺杆组可拆卸的布置在开关式磁力座的两端,分别布置在两组曲线调节块组中的两根金属导轨板在所述的固定连接调整螺杆组的配合下按要求弯曲成型,弯曲处的两根金属导轨板在开关式磁力座的配合下吸附在在需要切割的钢板上。
21.上述方案的优选方式是,每一组所述的曲线调节块组均包括圆弧面凹块和圆弧面凸块,每一组的所述圆弧面凹块和所述圆弧面凸块均通过相应的固定连接调整螺杆组圆弧面相互适应的布置在开关式磁力座的一个端部,
22.在简式磁吸固定装置的开关式磁力座上还设置有固定连接板,在复式磁吸固定装置的开关式磁力座上还设置有安装块,位于相应开关式磁力座上方的两组固定连接螺杆件组通过所述的固定连接板与该开关式磁力座连接,位于相应开关式磁力座上方的两组固定连接调整螺杆组通过所述的安装块与该开关式磁力座连接,
23.每一组固定连接螺杆件组和每一组固定连接调整螺杆组均包括螺母、锁紧旋钮和带有螺纹的连杆,每一根连杆分别通过未设置螺纹的一端与开关式磁力座和/或固定连接板和/或安装块连接,每一根连杆分别通过设置有螺纹的一端在螺母和锁紧旋钮的配合下与金属导轨板的相应位置连接。
24.进一步的是,以仿型切割工装作为支撑切割机的切割导轨,采用布置在被切割钢板相应位置处的仿型切割工装在操作人员的配合下移动切割机切割所述的超大型异形曲线钢板是按下述步骤进行的,
25.1)从钢结构bim模型中获取被切割零件钢板的单元轮廓,如果是曲面,则获取曲面展开后的轮廓;
26.2)根据切割机切割悬臂可调节长度,对曲线轮廓线进行仿型切割工装布置位置偏移获得的曲线作为仿型切割工装的轨道的定位曲线;
27.3)在轨道的定位曲线上选择曲线的驻点、拐点,获得其坐标定位数据;
28.4)将被切割的钢板材料平铺,将切割曲线和轨道的定位曲线在钢板上进行放样,并标注出轨道的定位曲线驻点、拐点,并沿轨道方向绘制出法线;
29.5)根据钢结构构件的曲率半径选择磁吸固定装置的形式,并将所选择的磁吸固定装置固定到驻点、拐点处,并根据轨道的定位曲线和法线调节好位置,打开磁吸开关进行固定;
30.6)沿定位曲线安装轨道,并用磁吸固定装置进行固定;
31.7)将改装的半自动火焰切割机装置在轨道上,调节切割枪头对准切割线,不点火进行行走,观察切割是否与切割线契合,通过微调修改偏差;
32.8)切割机点火,根据板厚调节好火焰,打开切割机行走开关,完成钢板切割。
33.本发明的有益效果是:本申请提供的施工方法通过先设计制作一套至少包括导轨组件、支撑固定组件和连接安装组件的仿型切割工装,并使在所述连接安装组件配合下可拆卸的连接为一个整体的所述导轨组件,通过所述的支撑固定组件按要求的异形曲线可拆卸的布置在需要切割的钢板上。这样,在进行具体的异型曲线切割时,便可以以仿型切割工装作为支撑切割机的切割导轨,并将所述的仿型切割工装按规定形状布置到需要切割的钢板的相应位置处,然后通过所述的切割导轨在操作人员的配合下移动切割机完成所述超大型异形曲线钢板切割的切割工作。由于本申请的施工方法解决了现有技术没有可以依赖的切割工装切割超大型异曲线钢板的技术问题,而且解决了采用半自动切割机依赖本申请提供的仿型切割工装来完超大型异形曲线钢板的切割工作,使大型异形曲线钢板切割的质量相对较高,并能有效提高切割效率。
附图说明
34.图1为本发明用于超大型异形曲线钢板切割的施工方法涉及到的仿型切割工装处于使用状态的三维结构示意图;
35.图2为本发明涉及到的仿型切割工装的结构示意图;
36.图3为本发明涉及到的仿型切割工装的x型安装连接架的结构示意图;
37.图4为发明涉及到的仿型切割工装的简式磁吸固定装置的结构示意图;
38.图5为发明涉及到的仿型切割工装的复式磁吸固定装置的结构示意图。
39.图中标记为:仿型切割工装1、切割机2、钢板3、导轨组件4、支撑固定组件5、连接安装组件6、金属导轨板7、x型安装连接架8、连接板9、固定连接螺杆件组10、简式磁吸固定装置11、复式磁吸固定装置12、开关式磁力座13、曲线调节块组14、圆弧面凹块15、圆弧面凸块16、固定连接板17、安装块18、固定连接调整螺杆组19、螺母20、锁紧旋钮21、连杆22。
具体实施方式
40.如图1~图5所示是本发明提供的一种切割质量相对较高,能有效提高切割效率的用于超大型异形曲线钢板切割的施工方法。所述的施工方法以仿型切割工装1作为支撑切割机2的切割导轨,并将所述的仿型切割工装1按规定形状布置到需要切割的钢板3的相应位置处,然后通过所述的切割导轨在操作人员的配合下移动切割机2完成所述超大型异形曲线钢板切割的切割工作,
41.其中所述的仿型切割工装1至少包括导轨组件4、支撑固定组件5和连接安装组件6,在所述连接安装组件6配合下可拆卸的连接为一个整体的所述导轨组件4,通过所述的支撑固定组件5按要求的异形曲线可拆卸的布置在需要切割的钢板3上。本申请提供的施工方法通过先设计制作一套至少包括导轨组件、支撑固定组件和连接安装组件的仿型切割工装,并使在所述连接安装组件配合下可拆卸的连接为一个整体的所述导轨组件,通过所述的支撑固定组件按要求的异形曲线可拆卸的布置在需要切割的钢板上。这样,在进行具体的异型曲线切割时,便可以以仿型切割工装作为支撑切割机的切割导轨,并将所述的仿型切割工装按规定形状布置到需要切割的钢板的相应位置处,然后通过所述的切割导轨在操作人员的配合下移动切割机完成所述超大型异形曲线钢板切割的切割工作。由于本申请的施工方法解决了现有技术没有可以依赖的切割工装切割超大型异曲线钢板的技术问题,而且解决了采用半自动切割机依赖本申请提供的仿型切割工装来完超大型异形曲线钢板的切割工作,使大型异形曲线钢板切割的质量相对较高,并能有效提高切割效率。
42.上述实施方式中,由于本申请的施工方法需要依赖仿型切割工装1,故为了便于超大型异形曲线钢板的切割施工操作,同时便于将其布置到被切割的钢板3的相应位置上,所述的导轨组件4包括两根高强柔韧的金属导轨板7,两根沿竖向平行布置的金属导轨板7通过所述的连接安装组件6可拆卸的连接为一个整体,分别与两根金属导轨板7连接的支撑固定组件5可拆卸的吸附在需要切割的钢板3上。此时,两根所述的金属导轨板7中包括一根主导轨板和一根辅助导轨板,所述主导轨板的顶端设置有走行结构,在所述的走行结构上设置有细密走行齿,所述辅助导轨板的顶端为平面结构。并且将所述的走行结构设置为在主导轨板顶端的三角形横截面或圆弧形横截面,所述的细密走行齿相应的设置在所述的三角形横截面或圆弧形横截面上。相应的,本申请将所述的连接安装组件6优选为包括多组x型安装连接架8,沿竖向平行布置的两根金属导轨板7通过沿长度方向顺序设置的各组x型安装连接架8连接为一个整体。具体来说就是,每一组所述的x型安装连接架8均包括一块连接板9和四套固定连接螺杆件组10,各套所述的固定连接螺杆件组10从四个方向呈x型的与所述的连接板9可拆卸的固定连接,各套固定连接螺杆件组10通过未与连接板9连接的一端与相应位置的金属导轨板7可拆卸的连接。
43.进一步的,为了保证导轨组件4尽可能牢固的布置在钢板上,同时又方便拆卸安装以及方便形成异形曲线,本申请所述的支撑固定组件5包括简式磁吸固定装置11和复式磁吸固定装置12,通过x型安装连接架8连接为一个整体的两根金属导轨板7在简式磁吸固定装置11和复式磁吸固定装置12的配合下按要求的异形曲线可拆卸的布置在需要切割的钢板3上。此时,所述的简式磁吸固定装置11包括一个开关式磁力座13和四套固定连接螺杆件组10,各套所述的固定连接螺杆件组10从四个方向呈x型的与所述的开关式磁力座13可拆卸的固定连接,各套固定连接螺杆件组10通过未与开关式磁力座13连接的一端与相应位置的金属导轨板7可拆卸的连接,所述的复式磁吸固定装置12包括曲线调节块组14、固定连接调整螺杆组19和所述的开关式磁力座13,所述的曲线调节块组14通过所述的固定连接调整螺杆组19可拆卸的布置在开关式磁力座13的两端,分别布置在两组曲线调节块组14中的两根金属导轨板7在所述的固定连接调整螺杆组19的配合下按要求弯曲成型,弯曲处的两根金属导轨板7在开关式磁力座13的配合下吸附在在需要切割的钢板3上。作为异型曲线成形最关键的部件,本申请提供的每一组所述的曲线调节块组14均包括圆弧面凹块15和圆弧面
凸块16,每一组的所述圆弧面凹块15和所述圆弧面凸块16均通过相应的固定连接调整螺杆组19圆弧面相互适应的布置在开关式磁力座13的一个端部,
44.在简式磁吸固定装置11的开关式磁力座13上还设置有固定连接板17,在复式磁吸固定装置12的开关式磁力座13上还设置有安装块18,位于相应开关式磁力座13上方的两组固定连接螺杆件组10通过所述的固定连接板17与该开关式磁力座13连接,位于相应开关式磁力座13上方的两组固定连接调整螺杆组19通过所述的安装块18与该开关式磁力座13连接,
45.每一组固定连接螺杆件组10和每一组固定连接调整螺杆组19均包括螺母20、锁紧旋钮21和带有螺纹的连杆22,每一根连杆22分别通过未设置螺纹的一端与开关式磁力座13和/或固定连接板17和/或安装块18连接,每一根连杆22分别通过设置有螺纹的一端在螺母20和锁紧旋钮21的配合下与金属导轨板7的相应位置连接。
46.鉴于有了上述的仿型切割工装1,这样以所述的仿型切割工装1作为支撑切割机2的切割导轨,采用布置在被切割钢板相应位置处的仿型切割工装1在操作人员的配合下移动切割机切割所述的超大型异形曲线钢板是按下述步骤进行的,
47.1)从钢结构bim模型中获取被切割零件钢板的单元轮廓,如果是曲面,则获取曲面展开后的轮廓;
48.2)根据切割机切割悬臂可调节长度,对曲线轮廓线进行仿型切割工装布置位置偏移获得的曲线作为仿型切割工装的轨道的定位曲线;
49.3)在轨道的定位曲线上选择曲线的驻点、拐点,获得其坐标定位数据;
50.4)将被切割的钢板材料平铺,将切割曲线和轨道的定位曲线在钢板上进行放样,并标注出轨道的定位曲线驻点、拐点,并沿轨道方向绘制出法线;
51.5)根据钢结构构件的曲率半径选择磁吸固定装置的形式,并将所选择的磁吸固定装置固定到驻点、拐点处,并根据轨道的定位曲线和法线调节好位置,打开磁吸开关进行固定;
52.6)沿定位曲线安装轨道,并用磁吸固定装置进行固定;
53.7)将改装的半自动火焰切割机装置在轨道上,调节切割枪头对准切割线,不点火进行行走,观察切割是否与切割线契合,通过微调修改偏差;
54.8)切割机点火,根据板厚调节好火焰,打开切割机行走开关,完成钢板切割。
55.综上所述,本申请的技术方案结构精巧,操作简便,适应性好。磁吸固定装置通常只需要安装有限的数个,对辅助轨道装配精度有要求很低,都给轨道装配提高了效率。同时可适应直线、曲线、椭圆形、圆形等切割线形的切割。
56.本申请的技术方案解决了大型钢板曲线切割中,数控切割机无法放下大尺寸板材,半自动切割机只能切割直线,人工切割效率低、质量差等问题,显著提高了切割效率和质量。
57.具体实施例
58.本装置轨道采用具有一定结构强度、柔性的金属材料,固定装置和支架采用具有一定结构强度的金属材料。
59.1)本装置由轨道一即上述的主导轨板、轨道二上述的辅助导轨板、x支架即上述的x型安装连接架、磁吸固定装置a型即上述的简式磁吸固定装置和/或磁吸固定装置b型即上
述的复式磁吸固定装置组成一套。一般需要两套,以便在超长曲线切割中可以续接。
60.2)轨道一和轨道二侧面长圆孔规格、间距相同,长圆孔的长度尺寸为中间间隔的3倍,这样可以保证两条轨道在弯曲情况下,无论如何错位,均有孔位可以对穿固定螺杆。
61.3)轨道一和轨道二仅顶面不同,轨道一为辅助轨道,顶面为平面,有横向细密齿线。轨道二为切割线形主控轨道,分为a型和b型。对于曲率较小的线形,可以采用较厚的钢板带,钢板带厚度较大时,采用a型轨道。a型轨道顶端为双坡口形,双坡口面有横向细密齿线,双坡口夹角与半自动切割机前轮一致,有钝边,钝边宽度大于半自动切割机前轮的槽口。因零件尺寸太大无法上切割机床的零件才需要使用本切割装置和方法,隐藏a型轨道在实际生产中最常用。
62.4)对于曲率较大的线形,较厚的钢板带不易弯曲,因而采用厚度较薄的钢板带。此时钢板带厚度小于半自动切割机前轮槽口,因此采用b型轨道。因圆形截面的弯曲性优于三角形及多边形截面,因此b型轨道顶端采用圆形截面,直径大于前轮槽口宽度。圆形截面有环向细密齿线。
63.5)磁吸固定装置分为a型和b型。a型较简便,为左右对称结构,适用于切割线曲率较小的情况,实际生产中最常用。连接板即上述的固定连接板与开关式磁力座顶面中心固定连接,连杆一端与固定连接板固定连接,另一端折弯到平直,端部有螺纹,有一个螺母和一个锁紧旋钮,锁紧旋钮螺纹完全贯通。连杆与磁力座即上述的开关式磁力座侧面固定连接,另一端为螺纹,有一个螺母和一个锁紧旋钮。螺母与锁紧旋钮将轨道一或二锁紧。
64.6)b型磁吸固定装置通过与轨道三点接触的方式将轨道压弯,适用于切割线曲率大的情况。固定块与磁力座顶面固定连接,连杆与磁力座或固定块侧面固定连接。连杆穿过卡紧块组即上述的圆弧面凹块和圆弧面凸块,卡紧块穿孔无螺纹,孔径比连杆直径稍大。卡紧块即上述的圆弧面凹块与轨道接触的一面为凹圆弧形柱面,卡紧块即上述的圆弧面凸块与轨道接触的一面为凸圆弧形柱面。通过螺母与锁紧旋钮对轨道卡紧和弯曲形态控制。
65.7)x支架通过4根连杆与连接板固定连接组成x形状,连杆的端部折弯成水平,同一侧上下连杆端部的距离与轨道上下孔的距离相同。通过螺母与锁紧旋钮锁紧轨道。其作用为,在磁吸固定装置间隔较远时,使用x支架防止轨道侧向失稳。
66.对半自动切割小车的滚轮进行改进,远离切割线一侧,即位于辅助轨道一上的前轮主动轮,改进为加长的圆柱形滚轮,可以在轨道一的安装中,不必保证其线形、与主控轨道11的距离非常精确。圆柱滚轮表面有环向细密齿线,确保其与轨道一顶面有足够的摩擦力。同侧的后轮卸下不予使用。
67.实施例一
68.从钢结构bim模型中获取零件板单元轮廓,如果是曲面,则获取曲面展开后的轮廓。
69.1)根据切割机切割悬臂可调节长度,对曲线轮廓线进行偏移,例如从轮廓线偏移150mm获得的曲线,作为轨道11的定位曲线。以华威cg1
‑
30半自动火焰切割机为例,其滚轮中心距离为180mm,将轨道11的定位曲线再偏移180mm获得的曲线作为轨道一的定位曲线。
70.2)在轨道二的定位曲线上选择曲线的驻点、拐点,获得其坐标定位数据。
71.3)将被切割的钢板材料平铺,将切割曲线、轨道二和轨道一的定位曲线在钢板进行放样,并标注出轨道二的定位曲线驻点、拐点,并向轨道一方向绘制出法线。
72.4)通常大型钢结构构件的曲率较小,因此选择a型磁吸固定装置,将固定装置在驻点、拐点处,根据轨道二定位曲线和法线调节好位置,打开磁吸开关进行固定。
73.5)沿定位曲线安装轨道二,并用磁吸固定装置进行固定,如有偏差,可对磁吸固定装置进行微调,然后同样的方法安装轨道一,轨道一的安装不必太精确,可加快安装速度,如果磁吸固定装置距离较远,可在其间增加磁吸固定装置或x支架,确保轨道稳定。
74.6)将改装的华威cg1
‑
30半自动火焰切割机装置在轨道上,调节切割枪头对准切割线,不点火进行行走,观察切割是否与切割线契合,如有偏差,需微调修正。
75.切割机点火,根据板厚调节好火焰,打开切割机行走开关,开始切割钢板。