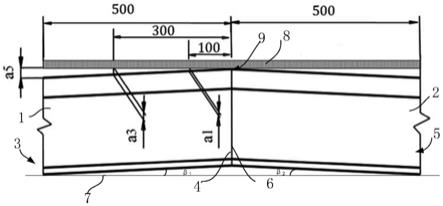
1.本发明涉及钢轨焊接技术领域,更具体地,涉及一种贝氏体钢轨的焊接生产方法。
背景技术:2.贝氏体钢轨具有良好的耐磨性和抗剥离性能,若将贝氏体钢轨应用在铁路钢轨中,能够提高重载铁路钢轨的使用寿命,进而降低换轨大修费用。
3.铁路钢轨需要若干个钢轨依次焊接在一起以制成能够使用的长钢轨,钢轨焊接时在焊接处形成焊接接头,并且由于焊接高温和变形的影响,焊接接头处会产生一定的变形量,影响其平直度。目前,由于贝氏体钢轨的屈强比较高,若对焊接后的贝氏体钢轨焊接接头采用矫直工艺使焊接接头处的平直度达到铁道行业标准要求(铁道行业标准tb/t1632.1
‑
2014)时,上述矫直力产生塑性变形,进而使焊接接头存在开裂风险;另外,若采用现有技术中的珠光体钢轨焊接接头的焊后正火处理工艺焊接贝氏体钢轨焊接接头,将在贝氏体钢轨的焊缝内部产生大量的马氏体等脆性组织,进而导致焊接处在使用时会发生疲劳断裂的风险。
4.因此,有必要解决上述技术问题。
技术实现要素:5.有鉴于此,本发明的目的在于提出一种贝氏体钢轨的焊接生产方法,以保证贝氏体钢轨的焊接接头的平直度,提高贝氏体钢轨焊接接头的组织应力,提高贝氏体钢轨焊接后的使用寿命,降低了换轨大修费用。
6.基于上述目的,本发明提供一种贝氏体钢轨的焊接生产方法,包括以下步骤:加工第一贝氏体钢轨和第二贝氏体钢轨,所述第一贝氏体钢轨包括沿长度方向相对设置的第一安装端和第一焊接端,所述第二贝氏体钢轨包括沿长度方向相对设置的第二安装端和第二焊接端;将所述第一安装端与所述第二安装端均抵接在平行于水平面的安装面上,将所述第一焊接端的端面和所述第二焊接端的端面对接放置;将所述第一焊接端向上并朝远离所述安装面的方向倾斜设置,所述第一焊接端与所述安装面的倾斜角度为锐角β1;将所述第二焊接端向上并朝远离所述安装面的方向倾斜设置,所述第二焊接端与所述安装面的倾斜角度为锐角β2,且β2=β1;将所述第一焊接端的端面和所述第二焊接端的端面相对接并焊接,形成焊接接头;将冷却后的焊接接头进行回火工艺处理。
7.可选的,所述焊接为闪光焊接。
8.可选的,所述第一焊接端的端面和所述第二焊接端的端面相对接后形成对接顶面,在所述对接顶面上放置水平直尺,测量所述第一贝氏体钢轨上距离所述对接顶面水平距离为100mm处到所述水平直尺的垂直距离为0.25mm~0.45mm;测量所述第一贝氏体钢轨上距离所述对接顶面水平距离为300mm处到所述水平直尺的垂直距离为0.75mm~1.4mm;测量所述第一贝氏体钢轨上距离所述对接顶面水平距离为500mm处到所述水平直尺的垂直距离为0.92mm~1.50mm。
9.可选的,通过在所述闪光焊接和所述回火工艺之间设置时效放置工序,以使所述焊接接头自然冷却。
10.可选的,所述时效放置工序的时间为等于或大于6小时。
11.可选的,在时效放置工序与所述闪光焊接之间设置焊筋整形工序。
12.可选的,在所述闪光焊接之前设置将所述第一贝氏体钢轨和所述第二贝氏体钢轨均进行焊前检查与除锈工序。
13.可选的,在所述回火工艺之后设置对所述焊接接头进行精磨处理工序。
14.可选的,在所述精磨处理工序之后设置对所述焊接接头进行外观检验和超声波探伤工序。
15.可选的,在所述外观检验和超声波探伤工序之后设置成品焊接钢轨存放工序。
16.本发明提供的贝氏体钢轨的焊接生产方法,首先,加工第一贝氏体钢轨和第二贝氏体钢轨;然后,将第一安装端与第二安装端均抵接在安装面上,并将第一焊接端的端面和第二焊接端的端面对接放置;将第一焊接端向上并朝远离安装面的方向倾斜设置;将第二焊接端向上并朝远离安装面的方向倾斜设置;将第一焊接端的端面和第二焊接端的端面相对接并焊接;最后,将冷却后的焊接接头进行回火工艺处理。长钢轨可以采用将两两贝氏体钢轨按照上述焊接生产方法依次相焊接获取。采用本发明提供的贝氏体钢轨的焊接生产方法,焊接前设置的倾斜上拱量抵消了焊接接头因焊接高温和变形产生的下沉变形量,保证了贝氏体钢轨的焊接接头的平直度,避免了焊接接头通过矫直工艺造成开裂的风险,回火工艺提高了贝氏体钢轨焊接接头的组织应力,降低了焊接接头处发生疲劳断裂的风险,提高了贝氏体钢轨焊接后的使用寿命,进而降低了换轨大修费用。
附图说明
17.下面将通过附图详细描述本发明中优选实施例,将有助于理解本发明的目的和优点,其中:
18.图1为本发明一实施例的贝氏体钢轨的焊接生产方法中第一贝氏体钢轨和第二贝氏体钢轨焊接前的放置姿态示意图;
19.图2为本发明一实施例的贝氏体钢轨的焊接生产方法的生产工序示意图;
20.图3为本发明一实施例的贝氏体钢轨的焊接生产方法中第一贝氏体钢轨和第二贝氏体钢轨的端面示意图。
21.附图标记说明:
22.1:第一贝氏体钢轨;2:第二贝氏体钢轨;3:第一安装端;4:第一焊接端;5:第二安装端;6:第二焊接端;7:安装面;8:水平直尺;9:对接顶面。
具体实施方式
23.下面结合实施例对本发明进行详细说明。其中相同的零部件用相同的附图标记表示。需要说明的是,下面描述中使用的词语“前”、“后”、“左”、“右”、“上”和“下”指的是附图中的方向,词语“内”和“外”分别指的是朝向或远离特定部件几何中心的方向。
24.如图1、图2及图3所示,本发明提供的贝氏体钢轨的焊接生产方法,包括以下步骤:加工第一贝氏体钢轨1和第二贝氏体钢轨2,第一贝氏体钢轨1包括沿长度方向相对设置的
第一安装端3和第一焊接端4,第二贝氏体钢轨2包括沿长度方向相对设置的第二安装端5和第二焊接端6;将第一安装端3与第二安装端5均抵接在平行于水平面的安装面7上,将第一焊接端4的端面和第二焊接端6的端面对接放置;将第一焊接端4向上并朝远离安装面7的方向倾斜设置,第一焊接端4与安装面7的倾斜角度为锐角β1;将第二焊接端6向上并朝远离安装面7的方向倾斜设置,第二焊接端6与安装面7的倾斜角度为锐角β2,且β2=β1;将第一焊接端4的端面和第二焊接端6的端面相对接并焊接,形成焊接接头;将冷却后的焊接接头进行回火工艺处理。
25.需要说明的是,如图3所示,第一贝氏体钢轨1和第二贝氏体钢轨2的端面为工字型;可以通过同时移动第一贝氏体钢轨1和移动第二贝氏体钢轨2,从而使第一焊接端4的端面和第二焊接端6的端面相对接,进而实现下一步的焊接操作;也可以通过固定第一贝氏体钢轨1,只移动第二贝氏体钢轨2,从而使第一焊接端4的端面和第二焊接端6的端面相对接,进而实现下一步的焊接操作。
26.本发明提供的贝氏体钢轨的焊接生产方法,首先,加工第一贝氏体钢轨1和第二贝氏体钢轨2;然后,将第一安装端3与第二安装端5均抵接在安装面7上,并将第一焊接端4的端面和第二焊接端6的端面对接放置;将第一焊接端4向上并朝远离安装面7的方向倾斜设置;将第二焊接端6向上并朝远离安装面7的方向倾斜设置;将第一焊接端4的端面和第二焊接端6的端面相对接并焊接;最后,将冷却后的焊接接头进行回火工艺处理。长钢轨可以采用将两两贝氏体钢轨按照上述焊接生产方法依次相焊接获取。采用本发明提供的贝氏体钢轨的焊接生产方法,焊接前设置的倾斜上拱量抵消了焊接接头因焊接高温和变形产生的下沉变形量,保证了贝氏体钢轨的焊接接头的平直度,避免了焊接接头通过矫直工艺造成开裂的风险,回火工艺提高了贝氏体钢轨焊接接头的组织应力,降低了焊接接头处发生疲劳断裂的风险,提高了贝氏体钢轨焊接后的使用寿命,进而降低了换轨大修费用。
27.本发明一实施例中,焊接为闪光焊接。闪光焊是电流通过两个对接工件的接触表面时,其细小的接触点的电阻及其接触表面的电弧产生热量,将对接表面加热,在适当时间后,对接头施加压力,使两个对接表面的整个区域同时牢固结合起来的电阻焊方法。闪光焊热影响区的范围极小,且由于表面氧化物与其他杂质成为四溅的火花被清除,不致混入焊接接头内,焊接接头的可靠性高,提高了贝氏体钢轨焊接后的使用寿命,进而降低了换轨大修费用。
28.如图1所示,第一焊接端4的端面和第二焊接端6的端面相对接后形成对接顶面9,在对接顶面9上放置水平直尺8,测量第一贝氏体钢轨1上距离对接顶面9水平距离为100mm处到水平直尺8的垂直距离为0.25mm~0.45mm;测量第一贝氏体钢轨1上距离对接顶面9水平距离为300mm处到水平直尺8的垂直距离为0.75mm~1.4mm;测量第一贝氏体钢轨1上距离对接顶面9水平距离为500mm处到水平直尺8的垂直距离为0.92mm~1.50mm。需要说明的是,上述垂直距离即为对接顶面9与贝氏体钢轨上不同位置处之间的间隙,上述测量的垂直距离可以测量一个,两个或多个;也可以测量第二贝氏体钢轨2上对应的上述不同位置到水平直尺8的垂直距离;本实施例中,第一贝氏体钢轨1和第二贝氏体钢轨2的上述垂直距离保证了贝氏体钢轨焊接后的平直度在标准规定的范围内(铁道行业标准tb/t1632.1
‑
2014《钢轨焊接第1部分:通用技术条件》规定的钢轨焊接接头轨顶面的平直度是(0.1~0.4)mm/m)。
29.结合图1所示,焊接前第一贝氏体钢轨1和第二贝氏体钢轨2的放置姿态与焊接后
焊接接头的平直度的测量结果如表1所示:
[0030][0031][0032]
表1焊接前钢轨的放置姿态与焊接后焊接接头的平直度的测量结果
[0033]
需要说明的是,a1为测量第一贝氏体钢轨1上距离对接顶面9水平距离为100mm处到水平直尺8的垂直距离;a3为测量第一贝氏体钢轨1上距离对接顶面9水平距离为300mm处到水平直尺8的垂直距离;a5为测量第一贝氏体钢轨1上距离焊缝水平距离为500mm处到水平直尺8的垂直距离。从上述表1的测量结果可以看出:焊接后的焊接接头的平直度均在标准范围内。
[0034]
如图2所示,通过在闪光焊接和回火工艺之间设置时效放置工序,以使焊接接头自然冷却。本实施例中,时效放置工序保证了焊接接头在焊接后自然冷却至常温,从而使贝氏体钢轨焊接接头彻底完成贝氏体转变,提高了贝氏体钢轨的焊接后的使用寿命,进而降低了换轨大修费用。具体地,时效放置工序的时间为等于或大于6小时,进一步地使贝氏体钢轨焊接接头更彻底地完成贝氏体转变,提高了贝氏体钢轨的焊接后的使用寿命,进而降低了换轨大修费用。
[0035]
如图2所示,在时效放置工序与闪光焊接之间设置焊筋整形工序。本实施例中,将第一贝氏体钢轨1和第二贝氏体钢轨2进行闪光焊接后,立即采用磨削方式对热态焊接接头进行去除焊筋的表面整形作业,即在焊接接头处于热态时将钢轨焊筋打磨至与钢轨母材基本平齐,消除棱角,在焊筋整形后,检查表面未见裂纹,避免出现冷态加工可能产生的缺陷,提高了贝氏体钢轨焊接后的使用寿命,进而降低了换轨大修费用。
[0036]
如图2所示,本实施例中,在闪光焊接之前设置将第一贝氏体钢轨1和第二贝氏体钢轨2均进行焊前检查与除锈工序,使除锈后的钢轨符合焊接导电要求,进一步地保证了焊接后的焊接质量。需要说明的是,在进行焊前检查与除锈工序之前,可以将待焊接的贝氏体钢轨进行存放,方便了待焊贝氏体钢轨的提取。
[0037]
如图2所示,本实施例中,在回火工艺之后设置对焊接接头进行精磨处理工序。需要说明的是,在回火工序与精磨工序之间,可以设置一个以上的空置工位,在空置工位不进行任何作业,目的是辅助接头冷却,使回火工序与精磨工序可以平行作业,提高了焊接接头的平整度。
[0038]
本发明另一实施中,也可以将精磨处理工序设置在时效放置工序之后,即焊接后先对焊接接头进行精磨处理,再进行回火工序。
[0039]
如图2所示,本发明一实施例中,在精磨处理工序之后设置对焊接接头进行外观检验和超声波探伤工序,保证了贝氏体钢轨的焊接质量。
[0040]
如图2所示,本发明一实施例中,在外观检验和超声波探伤工序之后设置成品焊接钢轨存放工序,将焊接好的长钢轨移动至成品场存放,便于焊接钢轨的提取使用。
[0041]
本发明一实施例中的贝氏体钢轨的焊接生产方法可以按以下步骤进行:首先,将待焊接的贝氏体钢轨由待焊钢轨存放场,吊运至钢轨焊接生产线上,生产线由若干辊轮组成,钢轨可在辊轮上沿着钢轨长度方向移动;将待焊钢轨移动至焊前检查与除锈工位,对待焊接的贝氏体钢轨进行表面质量检查与除锈处理,使除锈后的钢轨符合焊接导电要求;将待焊钢轨移动至钢轨焊接工位,在焊接前首先通过调整焊机起拱辊轮及夹持装置,使待焊的两支钢轨按照表1中的参数放置;
[0042]
然后,将两支待焊钢轨的第一焊接端4面和第二焊接端6面对接并进行闪光焊接;移动钢轨,使焊接接头到达焊筋整形工位,在焊接接头处于热态时将钢轨焊筋表面打磨至与钢轨母材平齐,并打磨消除棱角,在焊筋整形后,检查表面未见裂纹;移动钢轨,使焊接接头到达时效工位,将该焊接接头置于时效放置场自然冷却8小时,此时,焊接接头表面温度为10℃,将该焊接后的长钢轨吊运至生产线上;移动钢轨,使焊接接头到达回火工序工位,停止长钢轨移动,对处于回火工序工位的焊接接头按照回火加热工艺进行回火作业;移动钢轨,将已经完成回火处理的焊接接头进入到下一个空置工位进行自然冷却,经过四个空置工位后,回火后的焊接接头的表面温度为40℃,此时该焊接接头到达精磨工位,对该焊接接头进行精磨作业,精磨作业后测量焊接接头的平直度为0.35mm/m;
[0043]
最后,移动钢轨,使焊接接头到达外观检验和超声波探伤工位,检查焊接接头外观质量,并对焊接接头进行探伤检查;外观检验和超声波探伤合格后,继续移动长钢轨,将该支焊接好的长钢轨移动至成品场存放。
[0044]
本发明提供的贝氏体钢轨的焊接生产方法,首先,加工第一贝氏体钢轨1和第二贝氏体钢轨2;然后,将第一安装端3与第二安装端5均抵接在安装面7上,并将第一焊接端4的端面和第二焊接端6的端面对接放置;将第一焊接端4向上并朝远离安装面7的方向倾斜设置;将第二焊接端6向上并朝远离安装面7的方向倾斜设置;将第一焊接端4的端面和第二焊接端6的端面相对接并焊接;最后,将冷却后的焊接接头进行回火工艺处理。长钢轨可以采用将两两贝氏体钢轨按照上述焊接生产方法依次相焊接获取。采用本发明提供的贝氏体钢轨的焊接生产方法,焊接前设置的倾斜上拱量抵消了焊接接头因焊接高温和变形产生的下沉变形量,保证了贝氏体钢轨的焊接接头的平直度,避免了焊接接头通过矫直工艺造成开裂的风险,回火工艺提高了贝氏体钢轨焊接接头的组织应力,降低了焊接接头处发生疲劳断裂的风险,提高了贝氏体钢轨焊接后的使用寿命,进而降低了换轨大修费用。
[0045]
最后应说明的是:以上实施例仅用以说明本发明的技术方案,而非对其限制;尽管
参照前述实施例对本发明进行了详细的说明,本领域的普通技术人员应当理解:其依然可以对前述各实施例所记载的技术方案进行修改,或者对其中部分技术特征进行等同替换;而这些修改或者替换,并不使相应技术方案的本质脱离本发明各实施例技术方案的范围。