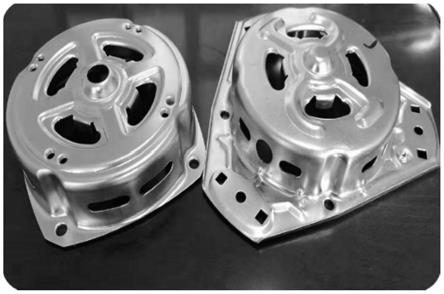
1.本发明涉及钢铁生产技术领域,具体涉及一种低能耗无头铁素体带钢生产的轧制工艺。
背景技术:2.薄板坯连铸连轧装置是钢铁生产的主要设备之一,在带钢生产中至关重要。目前的薄板坯为冷轧产品,轧制工艺过程为:热轧
‑
酸洗
‑
冷轧
‑
退火,在此过程中,具有废气量高的缺点,另外,在轧制过程中感应加热炉的使用,使得该类型的薄板坯成本高,不利于薄板坯的长期生产。
3.近些年,从成本、环保等方面综合来看,“以冷代热”越来越得到国内外的认可。然而,由于传统热轧和以csp为代表的薄板连铸连轧工艺在生产规格上的局限性,限制了“以热代冷”的发展。
4.目前的薄板无头连铸连轧虽然可以生产薄规格带钢,但是因其产线结构紧凑,铸坯偏薄,且轧制过程中受制于连铸拉速影响,温度热履历偏低、强度偏高,使其难以替代冷轧产品使用,同时因感应加热炉的存在,电耗较高,对成本影响较大。因此迫切需要一种可以优化的结构设计及生产方法来规范弥补现有的不足。
技术实现要素:5.针对现有技术的上述不足,本发明提供了一种低能耗无头铁素体带钢生产的轧制工艺,该轧制工艺中,充分利用薄板连铸连轧生产线热履历偏低的条件,将劣势转为优势,有效提高了带钢的表面质量和性能,使获得的带钢可替代冷轧钢使用。该轧制工艺具有易于控制的优点,且使用该轧制工艺生产的带钢,具有表面质量可替代非电镀等中低端冷轧产品。
6.本发明的技术方案如下:
7.一种低能耗无头铁素体带钢生产的轧制工艺,轧制工艺的主要过程为连铸机连轧、粗轧除磷、二机架粗轧、摆剪、推出堆垛机、精轧除鳞、五机架精轧、层流冷却和地下卷取机卷制。
8.优选的,上述轧制工艺,具体过程如下:
9.(1)钢水经大包浇铸进入结晶器中,经结晶器结晶后,以拉速≥4.8m/min的速度经连铸机处理后,获得厚度为120
‑
130mm的铸坯ⅰ;
10.(2)铸坯ⅰ进行粗轧除鳞处理,将表面氧化铁皮及保护渣清理干净,然后经过二机架粗轧,获得厚度≤20mm中间坯ⅰ,且控制中间坯ⅰ的温度≥1020℃;
11.(3)中间坯ⅰ经摆剪切头后,经推出堆垛机辊道后进行精轧除鳞,获得中间坯ⅱ,中间坯ⅱ的温度为930
‑
950℃;精轧除鳞的压力为150
‑
300bar;经过精轧除磷处理,可清除中间坯ⅰ表面氧化铁皮;
12.(4)中间坯ⅱ经过五机架精轧处理,轧制成0.8
‑
3.0mm的带钢;
13.(5)带钢经过层流冷却至温度为680
‑
750℃,获得回复组织,由地下卷取机卷制成钢卷。
14.优选的,在步骤(2)的二机架粗轧过程中,使用二机架大压下轧机,该大压下轧机的轧制能力为0
‑
4500t;由于机架越多,轧件的温降越大,因此,选用二机架大压下轧机,可有效降低温降,且可保证足够的轧制能力。
15.优选的,在步骤(3)中,为使中间坯ⅰ在经过推出堆垛机辊道时保持一定的温度,设定推出堆垛机辊道的长度为5
‑
8m;对中间坯ⅰ的温度进行控制,利于后续处理。
16.优选的,在步骤(5)中,层流冷却的长度为8
‑
15m;带钢经过该长度范围内的层流冷却后,可维持一定的温度,进而保证带钢的性能。
17.上述低能耗无头铁素体带钢生产的轧制工艺中,所述铁素体带钢含有下述重量百分比的组分:
18.c≤0.05%,si≤0.20%,mn≤0.30%,p≤0.030%,s≤0.015%,nb+ti+v≤0.10%,余量铁。
19.优选的,采用上述轧制工艺生产的铁素体带钢的厚度为0.8
‑
3.0mm;该铁素体带钢可替代非电镀等中低端冷轧产品。
20.相对于现有技术,本发明的有益效果在于:
21.1、充分利用现有的设备条件(薄板连铸连轧生产线),通过设置二机架粗轧、推出堆垛机、五机架精轧、层流冷却等过程,使获得的带钢为铁素体组织形态,从而使带钢具有表面质量好、强度低的优点,适于替代非电度等中低端冷轧产品。
22.2、通过控制铸坯ⅰ的厚度,并结合二机架粗轧装置设置,可有效控制中间坯ⅰ的温度,结合对推出堆垛机辊道设计,减少由铸坯ⅰ到中间坯ⅱ之间的热损失,从而在带钢轧制工艺中避免使用感应加热炉,既减少设备投入,又减少热能消耗,有效降低了生产成本。
附图说明
23.图1为实施例1带钢制成的产品与冷轧dc01制成的产品照片对比图。
具体实施方式
24.为了使本技术领域的人员更好地理解本发明中的技术方案,下面将结合本发明的实施例,对本发明实施例中的技术方案进行清楚、完整地描述,显然,所描述的实施例仅仅是本发明一部分实施例,而不是全部的实施例。基于本发明中的实施例,本领域普通技术人员在没有做出创造性劳动前提下所获得的所有其他实施例,都应当属于本发明保护的范围。
25.实施例1
26.一种铁素体带钢,该铁素体带钢含有下述重量百分比的组分:
27.c 0.05%,si 0.20%,mn 0.30%,p 0.030%,s 0.015%,nb+ti+v=0.10%,余量铁。
28.上述铁素体带钢的轧制工艺,具体过程如下:
29.(1)钢水经大包浇铸进入结晶器中,经结晶器结晶后,以拉速4.8m/min的速度经连铸机处理后获得120mm的铸坯ⅰ;
30.(2)铸坯ⅰ进行粗轧除鳞处理,将表面氧化铁皮及保护渣清理干净,然后经过二机架大压下轧机,获得厚度为20mm中间坯ⅰ,且控制中间坯ⅰ的温度为1020℃;单个大压下轧机的轧制能力为4500t,压下率为80%;
31.(3)中间坯ⅰ经摆剪切头后,经推出堆垛机辊道后进行精轧除鳞,获得中间坯ⅱ,中间坯ⅱ的温度为940℃;其中,推出堆垛机辊道的长度为6m;精轧除鳞的压力为220bar;经过精轧除磷处理,可清除中间坯ⅰ表面氧化铁皮;
32.(4)中间坯ⅱ经过五机架精轧处理,轧制成带钢;带钢公称厚度为1.8mm;该带钢可替代非电镀等中低端冷轧产品;精轧机的出口温度为780℃;
33.(5)带钢经过层流冷却至温度为710℃,获得回复组织,层流冷却的长度为11m,继续由地下卷取机卷制成钢卷。
34.实施例2
35.一种铁素体带钢,该铁素体带钢含有下述重量百分比的组分:
36.c 0.04%,si 0.10%,mn 0.20%,p 0.015%,s 0.010%,nb+ti+v=0.05%,余量铁。
37.上述铁素体带钢的轧制工艺,具体过程如下:
38.(1)钢水经大包浇铸进入结晶器中,经结晶器结晶后,以拉速5.2m/min的速度经连铸机处理后获得125mm的铸坯ⅰ;
39.(2)铸坯ⅰ进行粗轧除鳞处理,将表面氧化铁皮及保护渣清理干净,然后经过二机架大压下轧机,获得厚度为8mm中间坯ⅰ,且控制中间坯ⅰ的温度为1150℃;单个大压下轧机的轧制能力为2000t,压下率为85%;
40.(3)中间坯ⅰ经摆剪切头后,经推出堆垛机辊道后进行精轧除鳞,获得中间坯ⅱ,中间坯ⅱ的温度为930℃;其中,推出堆垛机辊道的长度为5m;精轧除鳞的压力为150bar;经过精轧除磷处理,可清除中间坯ⅰ表面氧化铁皮;
41.(4)中间坯ⅱ经过五机架精轧处理,轧制成带钢;带钢公称厚度为0.8mm;该带钢可替代非电镀等中低端冷轧产品;精轧机的出口温度为800℃;
42.(5)带钢经过层流冷却至温度为680℃,获得回复组织,层流冷却的长度为11m,继续由地下卷取机卷制成钢卷。
43.实施例3
44.一种铁素体带钢,该铁素体带钢含有下述重量百分比的组分:
45.c 0.01%,si 0.15%,mn 0.10%,p 0.010%,s 0.007%,nb+ti+v=0.01%,余量铁。
46.上述铁素体带钢的轧制工艺,具体过程如下:
47.(1)钢水经大包浇铸进入结晶器中,经结晶器结晶后,以拉速5.5m/min的速度经连铸机处理后获得130mm的铸坯ⅰ;
48.(2)铸坯ⅰ进行粗轧除鳞处理,将表面氧化铁皮及保护渣清理干净,然后经过二机架大压下轧机,获得厚度为8mm中间坯ⅰ,且控制中间坯ⅰ的温度为1300℃;单个大压下轧机的轧制能力为3500t,压下率为82%;
49.(3)中间坯ⅰ经摆剪切头后,经推出堆垛机辊道后进行精轧除鳞,获得中间坯ⅱ,中间坯ⅱ的温度为950℃;其中,推出堆垛机辊道的长度为8m;精轧除鳞的压力为300bar;经过
精轧除磷处理,可清除中间坯ⅰ表面氧化铁皮;
50.(4)中间坯ⅱ经过五机架精轧处理,轧制成带钢;带钢公称厚度为3.0mm;该带钢可替代非电镀等中低端冷轧产品;精轧机的出口温度为810℃;
51.(5)带钢经过层流冷却至温度为750℃,获得回复组织,层流冷却的长度为15m,继续由地下卷取机卷制成钢卷。
52.对实施例1
‑
3的带钢性能和表面特征进行检测,结果见表1。
53.表1 带钢性能检测
[0054][0055]
注:
a
当屈服现象不明显时,屈服强度采用r
p0.2
;
[0056]
b
屈服强度及弯曲试样方向为纵向;
[0057]
冷轧dc01是市面上常用的冷轧带钢。
[0058]
对实施例1
‑
实施例3的带钢表面特征分级,分级标准如下:
[0059]
一般级表面:代号a,特征:表面允许有深度或高度不超过钢带厚度公差之半的麻点、凹面、划痕等轻微、局部的缺陷,但应保证钢带允许的最小厚度;
[0060]
较高级表面:代号b,特征:表面允许有少量不影响成形性及涂、镀附着力的轻微手感缺陷,如轻微的划伤、压痕、麻点、辊印及氧化色等。
[0061]
在图1中,左图为实施例1带钢产品,右图为冷轧dc01带钢产品;结合图1可以看出,本发明实施例1提供的带钢制成的产品与冷轧dc01带钢制成的产品表面无明显差异。实施例1带钢制备的产品表面光滑,开设的通孔边缘圆润,表明使用本发明生产的带钢强度低,能够适用于各种造型设计,生产的产品可替代冷轧产品。
[0062]
尽管通过参考优选实施例的方式对本发明进行了详细描述,但本发明并不限于此。在不脱离本发明的精神和实质的前提下,本领域普通技术人员可以对本发明的实施例进行各种等效的修改或替换,而这些修改或替换都应在本发明的涵盖范围内/任何熟悉本技术领域的技术人员在本发明揭露的技术范围内,可轻易想到变化或替换,都应涵盖在本发明的保护范围之内。因此,本发明的保护范围应所述以权利要求的保护范围为准。