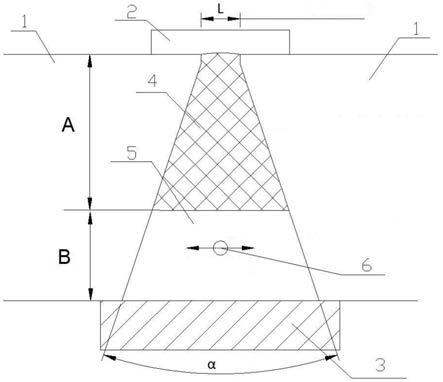
1.本发明涉及船舶建造技术领域,尤其涉及一种提高厚板立对接焊焊接效率的方法。
背景技术:2.船舶建造及钢结构建造过程中,气电立焊是一种高效的自动焊技术,质量稳定,但只能完成35mm厚度以内的立焊对接。当板厚大于35mm时,因气电立焊本身的技术局限,厚板立对接往往只能采用co2气体保护焊完成。气电立焊焊接效率可达到co2气体保护焊的5倍以上,而且进行co2气体保护焊时,多采用多层多道焊,焊渣清理、层间温度控制等工艺技术要求也进一步降低了co2气体保护焊的效率。因此35-50mm厚度区间的厚板立对接效率提升问题亟待解决。
技术实现要素:3.有鉴于此,本发明提供了一种提高厚板立对接焊焊接效率的方法,用以解决上述背景技术中存在的问题。
4.一种提高厚板立对接焊焊接效率的方法,具体包括以下步骤:
5.s1,焊前预处理:安装焊接辅件;
6.s2,启动co2气体保护焊机,以设定的焊接电流、焊接电压以及焊接速度对两个待焊结构面板之间的焊缝进行打底焊和填充焊,当填充层焊缝表面距离待焊结构面板的正面10mm-15mm时,结束co2气体保护焊的焊接工作;
7.s3,安装并调整气电立焊机使其焊丝位于未焊坡口宽度方向和深度方向的中心;
8.s4,启动气电立焊机,以设定的焊接电流、焊接电压以及焊接速度对两个待焊结构面板之间的未焊坡口进行盖面焊,焊接过程中,焊丝沿着未焊坡口的宽度方向往复摆动,同时根据熔池成型自动往上行走,直至完成焊接。
9.优选地,所述步骤s1中焊前预处理的具体步骤为:
10.首先,将两个待焊结构面板相对放置,在焊缝坡口背面安装多个与待焊结构面板相垂直的马板,多个马板的底部共同构成一道卡槽;
11.然后,根据两个待焊结构面板之间的焊缝坡口位置安装用以固定气电立焊机的轨道;
12.然后,将焊接衬垫塞入多个马板底部形成的卡槽内,使焊接衬垫与焊缝坡口背面相贴合。
13.优选地,所述马板的底部开设有u形槽。
14.优选地,所述待焊结构面板的厚度为35mm-50mm,两个待焊结构面板之间形成的焊缝坡口间隙为4mm~9mm,坡口角度为40
°±5°
。
15.优选地,所述轨道与焊缝坡口之间的距离为200
±
10mm。
16.优选地,所述步骤s2中启动co2气体保护焊机,以设定的焊接电流、焊接电压以及
焊接速度对两个待焊结构面板之间的焊缝进行打底焊和填充焊的具体步骤为:
17.首先,启动co2气体保护焊机,以设定的焊接电流、焊接电压以及焊接速度对两个待焊结构面板之间的焊缝进行打底焊;
18.然后,保持焊接电流和焊接电压不变,增加焊接速度,在打底层焊缝表面进行填充焊,形成填充层;
19.当填充层焊缝表面距离待焊结构面板的正面10mm-15mm时,结束co2气体保护焊的焊接工作,并打磨填充层焊缝表面使其表面与未焊坡口面平滑过渡。
20.优选地,进行打底焊的过程中,co2气体保护焊机的焊丝在焊缝坡口的两根趾处左右摆动并在根趾处略作停顿。
21.优选地,在打底层焊缝表面进行填充焊的过程中,当未焊坡口的宽度大于 25mm时,进行分道焊接。
22.优选地,所述步骤s3中安装并调整气电立焊机的具体步骤为:
23.首先,将气电立焊机安装在轨道上,在气电立焊机上安装铜滑块并使铜滑块与待焊结构面板的正面贴合;
24.然后,调整气电立焊机的摆动装置使其焊枪能够在焊缝坡口区域实现横向摆动;
25.然后,将焊枪上的焊丝末端调整至未焊坡口宽度方向和深度方向的中心;
26.最后,根据待焊结构面板的厚度设定气电立焊机的焊接参数。
27.本发明的有益效果是:
28.1、本技术的方法能够提高船舶建造及钢架构制造领域内35mm-50mm厚板立对接的焊接效率,在不增加成本投入的前提下,将常用的co2气体保护焊与气电立焊技术相结合,进行高效焊接,焊缝性能能够满足相关技术指标要求,能够有效缩短厚板的焊接周期,提高建造效率和质量。
29.2、由于立焊位置co2气体保护焊劳动强度非常大,需要通过手势摆动才能实现良好成形,尤其是夏天在预热150℃的情况下进行焊接,焊工作业劳动强度非常大,本技术的这种焊接方法组合不但有效地提高了工作效率,劳动强度也得到了极大缓解。
附图说明
30.为了更清楚地说明本发明实施例的技术方案,下面将对实施例中所需要使用的附图作简单地介绍,显而易见地,下面描述中的附图仅仅是本发明的一些实施例,对于本领域普通技术人员来讲,在不付出创造性劳动的前提下,还可以根据这些附图获得其它的附图。
31.图1是焊缝坡口的示意图。
32.图2是焊道布置图。
33.图3是焊丝在坡口中的位置的俯视图。
34.图4是焊丝在坡口中的位置的侧视图。
35.图5是待焊结构面板上冲击取样位置示意图。
36.图中标号的含义为:
37.1为待焊结构面板,2为焊接衬垫,3为铜滑块,4为co2气体保护焊焊缝,5为气电立焊焊缝,6为焊丝。
具体实施方式
38.为了更好的理解本发明的技术方案,下面结合附图对本发明实施例进行详细描述。
39.应当明确,所描述的实施例仅仅是本发明的一部分实施例,而不是全部的实施例。基于本发明中的实施例,本领域普通技术人员在没有作出创造性劳动前提下所获得的所有其它实施例,都属于本发明保护的范围。
40.下面通过具体的实施例并结合附图对本技术做进一步的详细描述。
41.本发明给出一种提高厚板立对接焊焊接效率的方法,该焊接方法采用 co2气体保护焊与气电立焊组合的方式,对35mm-50mm厚的船体结构面板1 进行焊接。
42.本方法是在立焊位置采用v形坡口,在v形坡口的背面粘贴陶质衬垫,正面先使用co2气体保护焊方法进行打底及填充焊接,待焊缝表面距离船体结构面板的正面10mm-15mm时,结束co2气体保护焊工作。然后,将垂直气电立焊机的摆动装置调整为横向摆动,使焊枪能够实现坡口区域内的横向摆动功能。
43.具体地,本发明的提高厚板立对接焊焊接效率的方法,包括以下步骤:
44.s1,焊前预处理:安装焊接辅件,如图3、图4所示。
45.安装焊接辅件时,首先,将两个待焊结构面板相对放置,使两者之间形成一个v形焊缝。焊缝坡口间隙不能太小,也不能太大,若焊缝坡口根部间隙太小,容易导致未焊透,反面焊缝需碳刨后进行封底焊;若焊缝坡口根部间隙太大,则会超出滑块的宽度范围无法进行焊接,因此,如图1所示,本技术的焊接方法针对的焊缝坡口间隙l为4mm~9mm,坡口角度α为40
°±5°
,坡口参数选用参照表1。
46.表1坡口参数
[0047][0048]
然后,应用砂轮清除焊缝坡口两侧50mm范围内钢板表面的气割毛刺、马脚、金属飞溅物以及纵向接缝的焊缝余高,以确保后续安装的焊接衬垫和冰冷铜滑块与待焊结构面板贴紧。
[0049]
然后,在焊缝坡口背面安装多个与待焊结构面板相垂直的马板,多个马板的底部共同构成一道卡槽,将焊接衬垫塞入多个马板底部形成的卡槽内,使焊接衬垫与焊缝坡口背面相贴合。焊接衬垫必须与待焊结构面板紧密贴合,焊接衬垫2 安装后,局部如有粘合不紧的情况,在定位处用木楔敲紧,以防止衬垫在焊接中受热而松动。
[0050]
然后,根据两个待焊结构面板之间的焊缝坡口位置安装用以固定气电立焊机的轨道,轨道与焊缝坡口之间的距离设置为200
±
10mm。气电立焊接的轨道的安装可在本步骤进行,也可在步骤s3中进行。
[0051]
本实施例中,马板的底部开设有u形槽;由于采用双丝气电立焊技术焊接厚度高达
84mm的钢板时,焊接热输入可高达500~600kj/cm,因此马板板厚至少为20mm,该厚度的马板可以避免根部间隙发生明显收缩。
[0052]
为了保证大线能量板焊接过程中,不出现因焊接收缩,导致焊缝间隙缩小,以至于反面无法成型的情况,马板除了需要达到厚度要求以外,还必须保证一定的数量和尺寸要求。原则上,相邻两块马板的间距约为400mm,至少一根焊接衬垫对应2块马板,马板尺寸可设计为200mm*120mm,必要时可增加马板大小,可将其尺寸设计为500*200mm。
[0053]
s2,启动co2气体保护焊机,以设定的焊接电流、焊接电压以及焊接速度对两个待焊结构面板之间的焊缝进行打底焊和填充焊。
[0054]
具体地,首先,启动co2气体保护焊机,以设定的焊接电流、焊接电压以及焊接速度对两个待焊结构面板之间的焊缝进行打底焊(焊接电流严格控制在 160a-200a范围内,以防止产生裂纹)。进行打底焊的过程中,co2气体保护焊机的焊丝在焊缝坡口的两根趾处左右摆动并在根趾处略作停顿,以确保焊缝背面成型良好。
[0055]
然后,保持焊接速度和焊接电压不变,增加焊接电流(焊接电流可增大至 250a),在打底层焊缝表面进行填充焊,形成填充层。进行填充焊的过程中,随着未焊坡口宽度的增大,可调整焊接方式,即当未焊坡口的宽度大于25mm时,可进行分道焊接。
[0056]
当填充层焊缝表面距离待焊结构面板的正面10mm-15mm时,结束co2气体保护焊的焊接工作,并打磨填充层焊缝表面使其表面与未焊坡口面平滑过渡。
[0057]
s3,安装并调整气电立焊机使其焊丝位于未焊坡口宽度方向和深度方向的中心。
[0058]
具体地,首先,将气电立焊机安装在轨道上,在气电立焊机上安装铜滑块并使铜滑块与待焊结构面板的正面贴合,铜滑块的规格尺寸如表2所示。
[0059]
表2滑块尺寸
[0060]
板厚t(mm)35﹤t≤50滑块尺寸(mm)42、48
[0061]
然后,将焊枪固定在气电立焊焊机上,安装焊丝6,倾斜角度β为10
°
左右,焊丝伸长l均30mm~35mm,调整气电立焊机的摆动装置使其焊枪能够在焊缝坡口区域实现横向摆动。
[0062]
然后,调整焊枪上的焊丝在未焊坡口中的位置,如若焊丝6距离坡口正面太近,电弧覆盖不到填充层表面,容易在焊缝内部出现未熔合缺陷;如若焊丝6 距离坡口正面太远,一方面喷嘴可能与坡口发生导电,阻碍正常焊接,另一方面当喷嘴粘附熔渣时,可能因为间隙太小而阻碍行走机构向上爬行,因此,将焊枪上的焊丝末端调整至未焊坡口宽度方向和深度方向的中心。
[0063]
最后,根据待焊结构面板的厚度设定气电立焊机的焊接参数,本技术的待焊结构面板的板厚为35mm-50mm,因此将气电立焊机的焊接电流设定为360-380a,焊接电压设定为34-36v,焊接参数选用见表3。
[0064]
表3焊接参数
[0065]
板厚t(mm)电流(a)电压(v)速度(cm/min)35-50360~38034~364~8
[0066]
s4,启动气电立焊机,以设定的焊接电流、焊接电压以及焊接速度对两个待焊结构面板之间的未焊坡口进行盖面焊(焊接电流为360-380a,电压为34-36v),焊接过程中,焊丝沿着未焊坡口的宽度方向往复摆动,同时根据熔池成型自动往上行走,直至完成焊接。焊接
时焊丝摆动幅度为6-16mm,焊接时焊丝的摆动停留时间为1-1.5秒,焊丝摆动参数见表4。
[0067]
表4焊丝摆幅
[0068]
焊接位置板厚t(mm)摆动摆幅(mm)左停(sec)右停(sec)垂直35-50必须采用6~161-1.51-1.5
[0069]
焊丝6需在焊接时保持适当摆幅、在距离焊缝正面合适的距离处做适当停留才能确保焊缝的成形。实际焊接过程中必须保证焊丝足够的停留时间,尤其摆动到靠近坡口边缘位置时,停留时间太短很容易导致坡口边缘出现夹渣、未熔合缺陷,因此,焊丝的最佳停留时间为1.5秒。同时,焊丝的摆动距离不能太小,太小则坡口边缘处温度太低,析出熔渣阻碍焊缝与母材熔合;摆动距离太大,则焊缝中心温度不够,同样会导致未熔合缺陷。
[0070]
下面通过举例具体说明本发明的具体实施方式。
[0071]
假设待焊结构面板选用的是厚度为50mm的钢板,co2气体保护焊焊丝的牌号为q460c,直径为1.2mm,气电立焊焊丝的牌号为sc-eg3,直径为1.6mm,两个焊丝也可替换为其他等效焊材。
[0072]
焊接衬垫选用的是陶质衬垫,型号为tc-3。安装焊接衬垫时,应使衬垫中心的红线处于焊缝中心位置,并使用铁砧将焊接衬垫压紧。
[0073]
两个待焊结构面板之间的对接焊缝的根部间隙为9mm,坡口角度为45
°
,坡口的正面宽度为45mm,因此选择宽度为48mm的铜滑块3。
[0074]
采用co2气体保护焊方式打底层焊接时,焊接电流为200a,以防止产生裂纹,焊枪手动摆动焊缝背面成型良好;填充层焊接,焊接参数调至250a,在第6层焊接时,采用双道焊接;第7层填充焊接完成后,待焊缝表面距离结构面板正面距离为15mm,此时结束co2气体保护焊的焊接工作,对焊缝面进行打磨处理,使焊缝表面与结构面板平滑过渡。
[0075]
然后,将气电立焊焊机摆动装置由纵向摆动调整为横向摆动,使焊枪能够在坡口区域内横向摆动;气电立焊焊丝倾斜角度为10
°
,焊丝伸长均30mm~35mm,焊丝处于未焊坡口宽度中心位置,与坡口正面距离保持7.5mm,焊接时焊丝摆动幅度为16mm,焊接电流为380a,电压为36v。焊接时焊丝的摆动停留时间为1.5 秒。气电立焊线能量200kj/cm,而co2气体保护焊线能量仅为30kj/cm。
[0076]
通过利用本发明的焊接方法对上述50mm钢板进行焊接,得到以下表格的试验数据:
[0077]
表5试验数据
[0078]
[0079]
表6焊接参数
[0080][0081]
表7力学性能检测
[0082][0083]
表8低温冲击性能检测
[0084][0085]
通过对上述表格中的试验数据进行分析发现:
[0086]
1)焊接性
[0087]
操作性能良好,焊缝表面成形优良。
[0088]
2)拉伸强度
[0089]
试验的试样,其焊接接头的抗拉强度均能满足的拉伸力学性能要求。
[0090]
3)弯曲试验
[0091]
2组侧弯试验均合格,焊接接头各位置均没有出现任何裂纹。
[0092]
5)冲击韧性
[0093]
试验试样均满足bv船级社规范中的焊接接头冲击韧性要求akj(-20℃)≥ 39j。
[0094]
图5是待焊结构面板上冲击取样位置示意图,从距待焊结构面板表面1-2mm (图5中h)位置分别取上、中、下层三组取样,该图中a、b、c、d均指冲击试验试样的缺口所处位置。其中,a为焊缝中心,b为熔合线,c为距熔合线2mm 的热影响区,d为距熔合线5mm的热影响区,e为距熔合线10mm的热影响区。
[0095]
因此,本技术的焊接方法能够有效提高35mm-50mm厚板立对接焊接效率,焊接接头满足相关技术指标要求,能够有效缩短厚板的焊接周期,提高建造效率和质量。
[0096]
以上所述仅为本发明的较佳实施例而已,并不用以限制本发明,凡在本发明的精神和原则之内,所做的任何修改、等同替换、改进等,均应包含在本发明保护的范围之内。