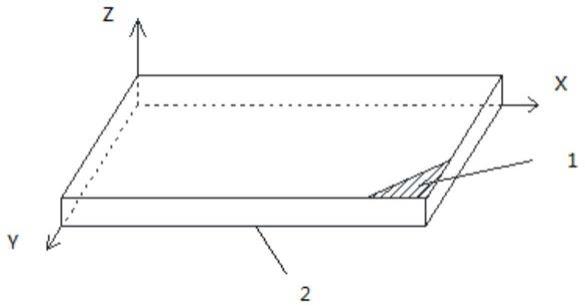
1.本发明涉及航空航天数控加工技术领域,特别是一种航空用高强铝合金厚板整体结构件的加工方法。
背景技术:2.目前,航空用高强铝合金厚板为al
‑
zn
‑
mg
‑
cu合金,该合金在热处理过程中由于温度梯度而引入大量残余应力,最终态厚板表面一般l向分应力约
‑
30~22mpa,t向分应力约55~24mpa,因此,各大主机厂在加工该合金整体结构件时,由于残余应力的存在,粗加工时需经过多次翻面加工厚板上下表面变形凸起部分,上下表面总加工掉的厚度多达14~20mm,加工量较大,并且粗、精加工连续进行,经常导致加工后出现结构件变形超差甚至开裂等问题,同时厚板加工后变形稳定性差,一般变形量在4
‑
8mm,加工合格率极低。加工后的整体结构件表面残余应力呈拉应力状态,残余应力值经检测l向分应力约93~165mpa,t向分应力约78~127mpa,整体应力水平较高。
3.综上所述,现有技术铝合金厚板整体结构件的加工量较大,并且粗、精加工连续进行,导致加工后出现结构件变形超差甚至开裂,同时也存在典型零件机加工合格率低的问题。
技术实现要素:4.本发明是为了解决现有技术的加工量较大,并且粗、精加工连续进行,导致加工后出现结构件变形超差甚至开裂,同时也存在典型零件机加工合格率低的问题,采用一种航空用高强铝合金厚板整体结构件的加工方法。
5.本发明的技术方案是:
6.一种航空用高强铝合金厚板整体结构件的加工方法,它包括以下步骤:
7.步骤一、确定厚板加工基准面:
8.以下料后的厚板外廓尺寸平面为加工基准面;
9.步骤二、选择不同工序所用刀具:
10.选用d32r0刀具、d63r0.8刀具、d20r0刀具、d12r6球刀和d10r0刀具;
11.步骤三、对厚板进行一次开粗型面:
12.厚板上下表面均加工去除1.0~2.0mm,加工厚度至50mm,平面度不超过
±
0.1mm,选用d32r0刀具,上表面对刀,每刀下切0.5~1.0mm,按数模全型均匀留量2mm,四周精加工作为基准边,此加工面标记加工面,将加工面绕x轴旋转180度,以基准边拉直找正分中,选用d63r0.8刀具,下平面对刀,每刀下切深0.5mm,按数模全型均匀留量2mm;
13.步骤四、对厚板进行自然时效处理:
14.将步骤三一次开粗型面后的厚板放置平地处自然时效释放残余应力;
15.步骤五、对厚板进行二次开粗型面:
16.将步骤四厚板释放残余应力后,对厚板进行二次开粗型面,标记加工面1向上,按
基准找正分中,上表面去量0.5mm,选用d20r0刀具,上表面对刀,每刀下切深0.1~0.3mm,按照数模均匀留量0.3mm,选用d12r6球刀进行全型精加工,将加工面绕x轴旋转180度,按基准边找正分中,下表面对刀,选用d20r0刀具,每刀下切深0.3mm,按照数模型面全型留量0.3mm;
17.步骤六、对厚板进行全型精加工:
18.步骤五对厚板进行二次开粗型面后,选用d12r6球刀每刀跨步0.10~0.15mm进行全型精加工,选用d10r0刀具进行四周切断,保留四处连接筋;
19.步骤七、钳工:
20.沿切断处顺型切断连接筋,修整并打磨切断的连接筋;
21.步骤八、校验:
22.校验之后符合标准,则加工完成;
23.校验之后不符合标准,则继续重复步骤一至步骤七,再校验之,直至符合标准,则加工完成。
24.本发明与现有技术相比具有以下效果:
25.一、本发明加工的航空用高强铝合金厚板整体结构件粗加工时不需要经过多次翻面加工,可以减少构件机加工量,同时,粗加工后将构件进行自然时效处理以释放残余应力,可避免构件在机加工过程中出现变形超差甚至开裂等问题,同时提高机加工合格率达到90%以上。
26.二、本发明通过此方法加工后的整体结构件表面残余应力仍呈拉应力状态,残余应力值l向分应力约70~133mpa,t向分应力约47~109mpa,整体残余应力有较大程度降低。
附图说明
27.图1是本发明厚板的示意图。
具体实施方式
28.具体实施方式一:结合图1说明本实施方式,本实施方式的一种航空用高强铝合金厚板整体结构件的加工方法,=它包括以下步骤:
29.步骤一、确定厚板加工基准面:
30.以下料后的厚板外廓尺寸平面为加工基准面;
31.步骤二、选择不同工序所用刀具:
32.选用d32r0刀具、d63r0.8刀具、d20r0刀具、d12r6球刀和d10r0刀具;
33.步骤三、对厚板进行一次开粗型面:
34.厚板上下表面均加工去除1.0~2.0mm,加工厚度至50mm,平面度不超过
±
0.1mm,选用d32r0刀具,上表面对刀,每刀下切0.5~1.0mm,按数模全型均匀留量2mm,四周精加工作为基准边2,此加工面标记加工面1,将加工面1绕x轴旋转180度,以基准边2拉直找正分中,选用d63r0.8刀具,下平面对刀,每刀下切深0.5mm,按数模全型均匀留量2mm;
35.步骤四、对厚板进行自然时效处理:
36.将步骤三一次开粗型面后的厚板放置平地处自然时效释放残余应力;
37.步骤五、对厚板进行二次开粗型面:
38.将步骤四厚板释放残余应力后,对厚板进行二次开粗型面,标记加工面1向上,按基准找正分中,上表面去量0.5mm,选用d20r0刀具,上表面对刀,每刀下切深0.1~0.3mm,按照数模均匀留量0.3mm,选用d12r6球刀进行全型精加工,将加工面1绕x轴旋转180度,按基准边2找正分中,下表面对刀,选用d20r0刀具,每刀下切深0.3mm,按照数模型面全型留量0.3mm;
39.步骤六、对厚板进行全型精加工:
40.步骤五对厚板进行二次开粗型面后,选用d12r6球刀每刀跨步0.10~0.15mm进行全型精加工,选用d10r0刀具进行四周切断,保留四处连接筋;
41.步骤七、钳工:
42.沿切断处顺型切断连接筋,修整并打磨切断的连接筋;
43.步骤八、校验:
44.校验之后符合标准,则加工完成;
45.校验之后不符合标准,则继续重复步骤一至步骤七,再校验之,直至符合标准,则加工完成。
46.如此设置步骤三厚板上下表面均抄1.0~2.0mm是去除表面氧化皮的缺陷,光平厚板四周作为基准边是作翻面定位使用。
47.具体实施方式二:结合图1说明本实施方式,本实施方式的步骤三一次开粗型面中每刀下切深为0.5mm。其他与具体实施方式一相同。
48.具体实施方式三:本实施方式的步骤三一次开粗型面中厚板上下表面均加工去除1.0mm,步骤五二次开粗型面中每刀下切为0.3mm,步骤六全型精加工中选用d12r6球刀每刀跨步为0.15mm进行全型精加工。其他与具体实施方式一或二相同。
49.具体实施方式四:结合图1说明本实施方式,本实施方式的步骤三一次开粗型面中厚板上下表面均加工去除2.0mm,步骤五二次开粗型面中每刀下切为0.1mm,步骤六全型精加工中选用d12r6球刀每刀跨步为0.1mm进行全型精加工。其他与具体实施方式一、二或三相同。
50.具体实施方式五:结合图1说明本实施方式,本实施方式的步骤四中自然时效的时间为72h。其他与具体实施方式一、二、三或四相同。
51.具体实施方式六:结合图1说明本实施方式,本实施方式的步骤三一次开粗型面中厚板上下表面均加工去除2.0mm,步骤五二次开粗型面中每刀下切深为0.15mm。其他与具体实施方式一、二、三、四或五相同。
52.具体实施方式七:结合图1说明本实施方式,本实施方式的步骤六全型精加工中选用d12r6球刀每刀跨步为0.1mm进行全型精加工。其他与具体实施方式一、二、三、四、五或六相同。
53.本发明已以较佳实施案例揭示如上,然而并非用以限定本发明,任何熟悉本专业技术人员,未脱离本发明技术方案的内容,依据本发明的技术实质对以上实施案例所做的任何简单修改、等同变化与修饰,均仍属本发明技术方案范围。