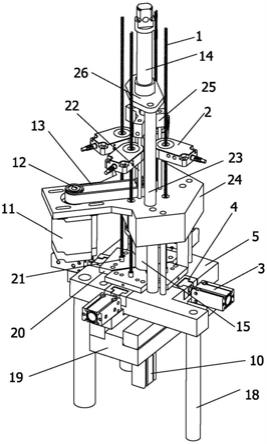
1.本发明涉及自动化设备技术领域,尤其是一种高效的自动装针机构。
背景技术:2.目前轴承或者十字轴万向节轴套装配滚针时,大多采用自动装针机进行装配,如中国发明cn01210727.1公开的一种自动装针机,系由电机经传动机构和设于装针漏斗的上盖,驱动装针漏斗内的芯轴,在所述装针漏斗下方设有转盘,其上固定设有外套,并在所述外套内设有套置于芯轴上的模套,其上开口部与所述芯轴间构成一个与滚针排列相适配的环槽。
3.现有自动装针机的缺陷是:1、运用电动机、传动带带动曲柄摇杆机构,曲柄摇杆机构的摇杆快速来回摆动,利用其振动特性来进行滚针的下料和排序,振动频率高,噪音较大;2、滚针的下料和排序过程中,存在卡料而无法排满滚针的情况,从而导致后序滚针漏装;3、滚针排序后,需要需要人工手动将轴承外圈或者轴套套在排好的滚针上,操作手法不当也容易造成滚针丢失,且效率低下。
技术实现要素:4.本发明的目的是克服上述背景技术中的不足,提供一种高效的自动装针机构,能够减小振动噪音,规避漏排、漏装滚针的情况,实现全自动化,省去人工装配操作,提高装针效率。
5.本发明采用的技术方案如下:
6.一种高效的自动装针机构,包括顶部水平设置有方形底座的机架、安装在方形底座底部的至少一个轴套送料组件、安装在方形底座上侧的至少一个下料组件、安装在方形底座中心的装针组件和一个推针组件,以及安装在方形底座侧边的至少一个顶针组件;
7.所述轴套送料组件包括送料槽、向上推动气缸以及顶推块;送料槽的开口朝上布置,槽宽与轴套直径适应,槽底开设有竖直向下的通孔,顶推块可上下滑动地配合在通孔内,向上推动气缸固定在送料槽底部并且与顶推块连接;
8.所述下料组件包括下料管道以及固定块,下料管道竖直固定在方形底座上侧,固定块固定在方形底座的顶面,固定块竖直固定有一贯通其顶面和底面的固定管,下料管道的下端与固定管连接;
9.所述装针组件包括开设在方形底座中心的中心装针孔、竖直插入中心装针孔内的中心柱、带动中心柱转动的步进电机,所述中心柱的下段外壁与中心装针孔之间保持一段距离作为滚针排列的环形槽,中心柱的下端伸出方形底座的底面一段距离,中心柱的上端通过轴承安装在安装座上,该安装座通过两条立柱水平固定在方形底座上放,安装座上安装有所述步进电机,步进电机通过同步带以及带轮带动中心柱转动;
10.所述推针组件包括一个推套、导向杆、连接块以及向下推动气缸,向下推动气缸通过固定座竖直安装在立柱的顶端,向下推动气缸的顶杆竖直朝下布置并且与连接块连接,
连接块连接着至少两根导向杆,导向杆竖直布置并且向下穿过安装座上的导向孔后与所述推套连接,推套套设在所述中心柱上并且与所述环形槽相适应;
11.所述顶针组件包括开设在方形底座上的针槽、顶块以及水平推动气缸,针槽位于下料组件的固定管下方,滚针竖直排列在针槽内,针槽的宽度与滚针的直径相适应,深度与滚针的长度相适应,针槽从环形槽向外延伸,针槽的外端设有顶块,顶块的内端制有与针槽相适应的顶尖,顶块的外端与水平推动气缸的顶杆连接,水平推动气缸的缸体固定在方形底座的侧边。
12.进一步的方案,所述轴套送料组件还包括垂悬固定在方形底座底面的至少三个定位柱,各定位柱环绕方形底座中心的中心装针孔均匀排列,定位柱和中心装针孔轴线之间的距离与轴套的外径相适应。
13.进一步的方案,所述下料管道采用弹簧制作,弹簧的内径与滚针的直径相适应。
14.进一步的方案,所述下料管道上设置有用于检测滚针的环形接近开关。
15.进一步的方案,所述针槽的侧面开设有至少一条与其在水平面内正交的导向槽,导向槽内安装有顶紧块,顶紧块朝向针槽的一端制成与滚针外壁相适应的圆柱面,另一端抵靠着顶紧弹簧。
16.进一步的方案,所述顶尖的内端制成滚针外壁相适应的圆柱面。
17.进一步的方案,所述针槽制有与固定管上下对应的进针口,进针口的孔径大于滚针的内径。
18.进一步的方案,所述固定块靠近方形底座中心的一侧制有与推套外壁间隙配合的弧形口。
19.进一步的方案,所述中心柱的下段外壁沿圆周方向均匀开设有一圈向内凹陷的圆柱槽,圆柱槽沿中心柱的母线向下延伸到中心柱的下端。
20.进一步的方案,所述中心柱开设有沿轴线的中心注油孔,中心注油孔从中心柱的顶端向下延伸到中心柱的下段,中心柱的下段外壁向内开设有若干个连通中心注油孔的出油孔。
21.本发明具有的有益效果是:
22.(1)本发明大幅度降低了振动噪音;
23.(2)本发明实现了全自动化装配,省去人工装配环节,较大的提高了装配效率,根据实际生产统计,装配节拍比人工半自动装配的节拍提高了30%,在单班生产总数上,产量提高了125%;
24.(3)本发明的整套机构动作少、紧凑,机构中不存在漏排、漏装滚针的情况,因此能够极大的提高装针的稳定性,不会出现因机构问题而出现的漏装滚针和滚针卡滞而停机的情况。
附图说明
25.图1是本发明的总装结构立体图。
26.图2是本发明的仰视结构示意图。
27.图3是中心柱的立体结构图。
28.图4是本发明的主视结构示意图。
29.图5是图4的a
‑
a剖视图。
30.图6是图4的b
‑
b剖视图。
31.图7是图4的c
‑
c剖视图。
具体实施方式
32.为使本领域的普通技术人员更加清楚地理解本发明的目的、技术方案和优点,以下结合附图和实施例对本发明做进一步的阐述,但本发明并不局限于以下实施例。
33.在本发明的描述中,需要说明的是,除非另有明确的规定和限定,对于本领域的普通技术人员而言,可以具体情况理解一般术语在本发明中的具体含义。
34.如图1到图7所示,本发明提供的一种高效的自动装针机构,包括顶部水平设置有方形底座5的机架18、安装在方形底座5底部的至少一个轴套送料组件、安装在方形底座5上侧的至少一个下料组件(图中设有四个下料组件)、安装在方形底座5中心的装针组件和一个推针组件,以及安装在方形底座5侧边的至少一个顶针组件(图中设有四个下料组件)。
35.所述轴套送料组件包括送料槽19、向上推动气缸10以及顶推块29;送料槽19的开口朝上布置,槽宽与轴套17直径适应,槽底开设有竖直向下的通孔,顶推块29可上下滑动地配合在通孔内,向上推动气缸10固定在送料槽19底部并且与顶推块29连接。
36.所述下料组件包括下料管道1以及固定块20,下料管道1竖直固定在方形底座5上侧,固定块20固定在方形底座5的顶面,固定块20竖直固定有一贯通其顶面和底面的固定管21,下料管道1的下端与固定管21连接。所述下料管道1采用弹簧制作,弹簧的内径与滚针16的直径相适应。所述下料管道1上设置有用于检测滚针16的环形接近开关2。利用重力和噪音较小的振动将滚针16单个竖直排列,利用了弹簧的孔道是单排的、唯一的、顺畅的特点,因此可以完全避免滚针16之间的干扰和滚针的卡滞。
37.所述装针组件包括开设在方形底座5中心的中心装针孔27、竖直插入中心装针孔27内的中心柱9、带动中心柱9转动的步进电机11,所述中心柱9的下段外壁9.1与中心装针孔27之间保持一段距离作为滚针16排列的环形槽31,中心柱9的下端伸出方形底座5的底面一段距离,中心柱9的上端通过轴承28安装在安装座24上,该安装座24通过两条立柱23水平固定在方形底座5上放,安装座24上安装有所述步进电机11,步进电机11通过同步带13以及带轮12带动中心柱9转动。
38.所述推针组件包括一个推套15、导向杆22、连接块25以及向下推动气缸14,向下推动气缸14通过固定座26竖直安装在立柱23的顶端,向下推动气缸14的顶杆竖直朝下布置并且与连接块25连接,连接块25连接着至少两根导向杆22,导向杆22竖直布置并且向下穿过安装座24上的导向孔后与所述推套15连接,推套15套设在所述中心柱9上并且与所述环形槽31相适应。
39.所述中心柱9、推套15、中心装针孔27、环形槽31、轴套17共轴线布置。
40.所述顶针组件包括开设在方形底座5上的针槽6、顶块4以及水平推动气缸3,针槽6位于下料组件的固定管21下方,滚针16竖直排列在针槽6内,针槽6的宽度与滚针16的直径相适应,深度与滚针16的长度相适应,针槽6从环形槽31向外延伸,针槽6的外端设有顶块4,顶块4的内端制有与针槽6相适应的顶尖4.1,所述顶尖4.1的内端制成滚针16外壁相适应的圆柱面。顶块4的外端与水平推动气缸3的顶杆连接,水平推动气缸3的缸体固定在方形底座
5的侧边。所述针槽6制有与固定管21上下对应的进针口6.1,进针口6.1的孔径大于滚针16的内径,便于滚针16竖直落入针槽6。
41.所述轴套送料组件还包括垂悬固定在方形底座5底面的至少三个定位柱30,各定位柱30环绕方形底座5中心的中心装针孔27均匀排列,定位柱30和中心装针孔27轴线之间的距离与轴套17的外径相适应。
42.所述针槽6的侧面开设有至少一条与其在水平面内正交的导向槽,导向槽内安装有顶紧块7,顶紧块7朝向针槽6的一端制成与滚针16外壁相适应的圆柱面,另一端抵靠着顶紧弹簧8。顶紧块7、顶紧弹簧8的作用是顶住滚针,保证滚针竖直排列而不倒下或者倾斜。
43.所述固定块20靠近方形底座5中心的一侧制有与推套15外壁间隙配合的弧形口。
44.所述中心柱9的下段外壁9.1沿圆周方向均匀开设有一圈向内凹陷的圆柱槽9.4,圆柱槽9.4沿中心柱9的母线向下延伸到中心柱9的下端。所述中心柱9开设有沿轴线的中心注油孔9.2,中心注油孔9.2从中心柱9的顶端向下延伸到中心柱9的下段,中心柱9的下段外壁9.1向内开设有若干个连通中心注油孔9.2的出油孔9.3。中心注油孔是润滑油脂的注入通道,粘稠的润滑油从细小的出油孔流出与每个滚针相粘结,保证滚针排列在轴套内壁而不倒下。
45.本发明的工作原理是:
46.首先外部振动上料机构将滚针送入下料管道1中,滚针在下料管道1中一个接连一个的串联排列,落入针槽6的进针口6.1,环形接近开关2的作用是检测弹簧中是否排列有滚针16,从而防止漏装滚针16。向上推动气缸10通过顶推块29将需要装针的轴套17顶到方形底座5的底面,三个定位柱定位轴套17的外圆,来保证轴套17的轴线和方形底座5的中心装针孔27的轴线重合。水平推动气缸3向前推动一个行程,将滚针16从针槽16推入中心柱9与中心装针孔27之间的环形槽31中,步进电机11旋转一个角度,通过同步轮12和同步带13带动中心柱9旋转一个角度,步进电机11旋转一次(一个角度),水平推动气缸3就向前推动一次,滚针16由圆柱槽9.4定位,直到步进电机11总共旋转360度,水平推动气缸3就按照设置的数量将滚针16推满一圈圆柱槽9.4,然后向下推动气缸14的顶杆向下顶出,通过推套15将已经排列好的一整圈滚针压入轴套17内,推套15和中心柱9是同轴线的,当一整圈滚针16完全压入轴套内之后,向上推动气缸10就开始缩回,保证已经装配好滚针16的轴套17回到原始位置,然后向下推动气缸14缩回到极限状态。滚针16排列采用步进电机11逐步旋转,四个顶针组件的水平推动气缸3同时前推的方式,这种方式结构简单,动作少,节拍快。
47.可以通过改变装针机构中各部件的尺寸,装配的滚针16的总数量n、单个滚针直径¢、单个滚针长度l都可以在一定范围内改变,从而能够满足不同规格滚针的全自动化装配。
48.以上所述仅为本发明的优选实施例,对于本领域的技术人员来说,本发明可以有各种更改和变化。凡在本发明的精神和原则之内,所作的任何修改、等同替换、改进等,均应包含在本发明的保护范围之内。