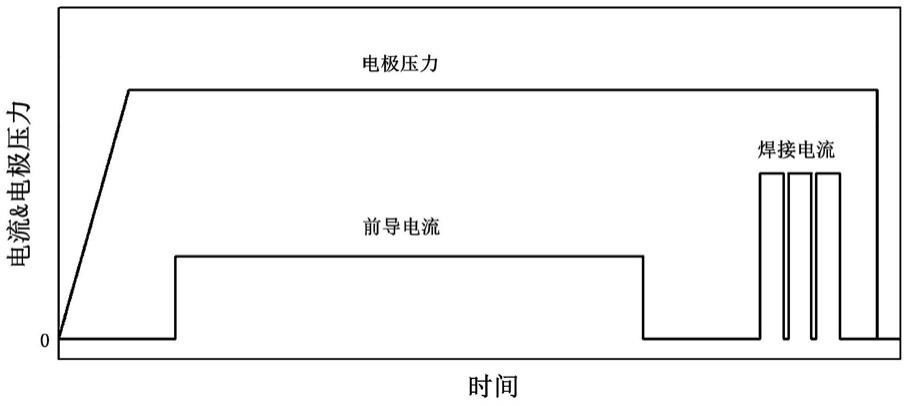
welding by heat input dependent hold time adaption》(science and technology of welding and joining,2020,25(7):617
‑
624)中提到通过延长焊后保压时间能够抑制液态金属脆裂纹。以上工艺方法虽然均能够在一定程度上抑制液态金属脆裂纹,但是一方面抑制效果有限,另一方面无法改善点焊接头的力学性能。he等人在文献《suppression of liquid metal embrittlement in resistance spot welding of trip steel》(science and technology of welding and joining,2019,24(6):579
‑
586)中提出通过在镀锌trip钢和点焊电极之间插入厚度约为25μm的铝箔,能够抑制液态金属脆裂纹,他们认为裂纹被抑制的原因是焊接过程中铝箔和钢反应形成的金属间化合物阻止了液态锌向钢中的渗透。该方法虽然能够抑制液态金属脆裂纹并且提高点焊接头力学性能,但是大大增加了工艺复杂性。
技术实现要素:5.本发明的目的就是为了克服上述现有技术存在的缺陷而提供一种用于抑制镀锌高强钢电阻点焊接头中液态金属脆裂纹的工艺,即在传统点焊工艺的焊接电流之前附加一段长时间恒定的前导电流。使用该工艺后,得到的镀锌高强钢电阻点焊接头中的液态金属脆裂纹数量大大减少,并且接头的力学性能能够得到提高。
6.本发明的目的可以通过以下技术方案来实现:一种抑制镀锌高强钢电阻点焊接头液态金属脆裂纹的点焊工艺,预备待焊的镀锌超高强钢材料,在常规点焊工艺的焊接电流之前附加一段长时间且数值恒定的前导电流,该前导电流较小,在前导期间不形成点焊熔核,前导电流起到改变焊接过程中焊点表面温度和应力状态以及合金化镀锌层的作用,从而抑制点焊接头中的液态金属脆裂纹。
7.进一步的,所述前导电流施加时间为1000
‑
3000ms,前导电流为3
‑
4ka。
8.进一步的,前导电流结束后焊接电流施加前的冷却时间为500ms。
9.进一步的,所述镀锌高强钢中的镀锌层为热镀锌或电镀锌。
10.进一步的,所述镀锌高强钢中的钢板强度级别为500mpa
‑
1500mpa。
11.进一步的,电阻点焊机的电极采用带端面的铬锆铜球形电极。
12.进一步的,所述电阻点焊机的球形电极外径为13
‑
16mm。
13.进一步的,所述电阻点焊机的球形电极端面直径为7
‑
9mm。
14.进一步的,电阻点焊过程中,常规点焊工艺依据需要选取。
15.进一步的,电阻点焊过程中,焊接电流脉冲数为3,即设置三段焊接电流,每段焊接电流时间为120ms,每段焊接电流之间的冷却时间为20ms,保压时间为200
‑
500ms。
16.液态金属脆发生的条件一般包括:所需的温度(约600
‑
1000℃)、应力(存在拉伸应力)以及与液态金属接触(熔化的镀锌层铺展),在满足这些条件的情况下,易在焊点表面产生液态金属脆导致裂纹。
17.本发明通过对点焊接头金相横截面进行显微观察后可以发现,在使用前导电流之后,在相同的焊接电流下,接头中的裂纹数量大大减少。通过对点焊过程进行有限元数值模拟,获取了焊点表面的温度和应力历史,可以发现使用前导电流之后,由于焊点表面冷却速率变慢,受到的拉伸应力发生了下降。此外,通过在扫描电镜下进行元素分析发现,在前导电流期间,由于钢板表面温度升高,镀锌层能够与钢发生反应,经历前导电流之后的镀锌层
中的铁元素含量大幅升高,依据铁
‑
锌二元相图可知,这会导致镀锌层熔点的升高。在后续施加焊接电流过程中,焊点表面的液态锌含量会降低,进而降低了液态锌向钢中的渗透和扩散。这些因素使得焊点表面发生液态金属脆的条件不易得到满足,因此液态金属脆裂纹得到了抑制。此外,在使用前导电流之后,点焊接头能够获得更大的熔核直径,使接头的力学性能得到提高。
18.与现有技术相比,本发明在不需要引入任何新焊接设备的基础上,仅在常规的焊接工艺之前附加一段长时间的前导电流即可实现抑制点焊接头中液态金属脆裂纹以及提高点焊接头力学性能这两个有益效果,因此非常方便在生产中进行应用;该工艺方法能够推广到各种镀锌高强钢的电阻点焊之中。
19.本发明通过调控焊点表面温度应力以及合金化镀锌层,使得电阻点焊过程中产生液态金属脆所需的温度、应力和液态金属的条件不易得到满足,最终使得液态金属脆裂纹得到抑制。此外,使用该工艺还能够使焊接飞溅在更高的焊接电流下才会产生,增大了焊点的熔核直径,得到力学性能更优的点焊接头。
附图说明
20.图1为本发明提出的电阻点焊过程的工艺简图;
21.图2为常规电阻点焊过程的工艺简图;
22.图3为焊点表面的液态金属脆裂纹;
23.图4为使用常规工艺获得的点焊接头中液态金属脆裂纹数量统计结果;
24.图5为使用本发明的工艺获得的点焊接头中液态金属脆裂纹数量统计结果;
25.图6为使用常规工艺在7ka焊接电流下焊点表面的温度和应力历程;
26.图7为使用本发明的工艺在7ka焊接电流下焊点表面的温度和应力历程;
27.图8为原始镀锌层的元素分布;
28.图9为经历前导电流后焊点表面镀锌层的元素分布;
29.图10为使用常规工艺与本发明的工艺获得的点焊接头熔核直径测量结果;
30.图11为使用常规工艺与本发明的工艺获得的点焊接头力学性能测试结果。
具体实施方式
31.下面结合附图和具体实施例对本发明进行详细说明。本实施例以本发明技术方案为前提进行实施,给出了详细的实施方式和具体的操作过程,但本发明的保护范围不限于下述的实施例。
32.实施例1:
33.一、焊接材料及设备
34.1)待焊试板为1.2mm厚的热镀锌q&p980超高强钢,尺寸为125
×
38mm,搭接区域尺寸38
×
38mm。
35.2)焊接设备使用了固定式中频逆变直流电阻点焊机,气动加压,冷却水流速4l/min。
36.二、焊前准备
37.用酒精清洗热镀锌q&p980超高强钢,去除表面油污。
38.三、焊接工艺
39.采用本发明的有前导电流的焊接过程的工艺流程参见图1,其中,电极压力设置为4kn,前导时间为2000ms,前导电流为4ka,前导后的冷却时间为500ms。每个焊接电流脉冲的时间设置为120ms,焊接电流脉冲之间的冷却时间设置为20ms,保压时间设置为300ms。初始焊接电流值设置为5.5ka,并以0.5ka为间隔递增,直到出现焊接飞溅时,焊接试验结束。
40.除使用了图1所示的焊接工艺外,还使用了常规的无前导电流的焊接工艺作为对比例,如图2所示,该工艺除无前导电流外,所有参数设置与有前导电流时的工艺一致。每组电流值焊接六个试样,三个用于焊点横截面金相检测,三个用于点焊接头剪切拉伸力学性能测试。实验中使用的点焊电极端面直径均为8mm。
41.四、液态金属脆裂纹数量统计
42.使用常规的无前导电流的焊接工艺时,在焊点表面会出现大量的液态金属脆裂纹,如图3所示。对试验中所有焊点横截面金相中的裂纹进行了统计。使用常规的无前导电流的焊接工艺时的裂纹统计结果如图4所示,当焊接电流达到6.5ka时裂纹即会产生,在焊接电流达到8.0ka时发生飞溅,焊接试验结束,在6.5
‑
8.0ka的焊接电流范围内均存在数量很多的裂纹。使用本发明提出的附加前导电流焊接工艺时的裂纹统计结果如图5所示,在6.5
‑
8.0ka的电流范围内裂纹并未产生。由于使用该工艺后焊接飞溅在9.5ka才会产生,因此电流一直增加到9.5ka后焊接试验方才结束。虽然在焊接电流为8.0
‑
9.5ka的高电流范围内同样会产生裂纹,但裂纹数量依然很少。因此使用本发明的工艺方法能够有效抑制液态金属脆裂纹的产生。
43.五、液态金属脆裂纹的抑制原因
44.液态金属脆现象产生的本质原因是其该现象产生所需的温度、应力和液态金属这些条件同时得到满足。使用ansys有限元仿真得到了电阻点焊过程中焊点表面容易产生液态金属脆裂纹区域经历的的温度和应力历程,图6和图7分别为无前导电流和有前导电流时,在焊接电流7ka下焊点表面的温度和应力历程。将温度和应力同时满足条件(温度600
‑
1000℃,应力大于0)的时刻用阴影背景进行标识,可以看到无前导电流时焊点表面经历的峰值拉伸应力达到了800mpa,而有前导电流时焊点表面经历的峰值应力仅为100mpa左右,即使用前导电流后大大降低了焊点表面的拉伸应力。此外,图8和图9分别展示了原始镀锌层和经历前导电流之后焊点表面镀锌层的元素分布,可以看到在经历前导电流后,焊点表面镀锌层中zn元素含量明显下降,而fe元素含量明显上升,这表明在施加前导电流期间镀锌层与钢发生了冶金反应,这使得镀锌层的熔点升高,进而导致在随后施加焊接电流的期间,液态锌的含量发生下降。这些因素共同导致了使用前导电流后,液态金属脆产生所需的条件得到了改善与缓解,使得液态金属脆裂纹不易产生。
45.六、力学性能测试结果
46.使用传统工艺与新型工艺获得的点焊接头熔核直径如图10所示,剪切拉伸力如图11所示。可以看到,接头的熔核直径随着焊接电流的升高而增大,但在产生焊接飞溅之后由于大量熔融的金属被挤出,会导致熔核直径大幅降低。接头剪切拉伸力的变化趋势与熔核直径一致,即熔核直径越大,剪切拉伸力越高。使用附加前导电流的焊接工艺后,由于焊接飞溅在更高的焊接电流下才会产生,因此点焊接头能够获得更大的熔核直径和更高的剪切拉伸力,相比于常规工艺二者分别提升了20.9%及14.1%。
47.上述的对实施例的描述是为便于该技术领域的普通技术人员能理解和使用发明。熟悉本领域技术的人员显然可以容易地对这些实施例做出各种修改,并把在此说明的一般原理应用到其他实施例中而不必经过创造性的劳动。因此,本发明不限于上述实施例,本领域技术人员根据本发明的揭示,不脱离本发明范畴所做出的改进和修改都应该在本发明的保护范围之内。