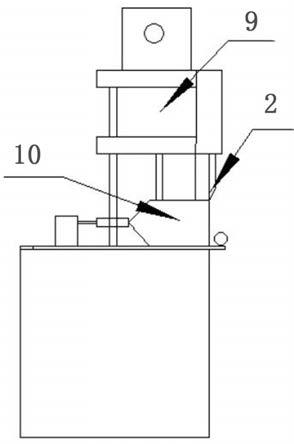
1.本发明涉及有色金属冶炼设备技术领域,具体涉及用于提升海绵钛切割疏松小粒度产量的分离式锯齿切刀。
背景技术:2.海绵钛是由精镁和四氯化钛发生还原反应生成的,同时生成的副产品为氯化镁,氯化镁再电解生成精镁和氯气,氯气与富钛矿反应生成四氯化钛,精镁和四氯化钛又用于生产海绵钛,由此形成一个闭式循环。精镁和四氯化钛的还原反应是在反应釜内进行的,蒸馏后的海绵钛呈“带帽近似圆柱形”,称之为钛坨,钛坨需破碎成0.83~25.4mm粒度的钛块,因整个钛坨体积大,无法整体破碎,需切割成合适尺寸,再使用破碎机破碎,最后将成品海绵钛包装入桶。
3.钛坨的切割需要使用大型油压机,如图1所示,在大型油压机的刀架上安装一把特殊切刀,切刀刀刃为直线形、与油压机本体采用通孔螺栓连接。然而,现有的切刀在使用中存在以下技术问题,其一,在切割过程中因海绵钛强度高、韧性好、易粘刀,一次切割后钛块尺寸依然较大,且大于300mm的钛块占比55%左右,需进行二次切割;其二,大粒度海绵钛块造成破碎机使用负荷大、故障率高和破碎机刀齿使用寿命短等问题;其三,海绵钛钛坨在切割过程中会由于自然断裂形成3
‑
12.7mm标准小粒度产品,该部分产品未经过后期破碎挤压、溜管碰撞,疏松度最好,疏松度是小粒度海绵钛的重要指标,因此需要提高切割处小粒度产量;其四,切刀为易损件,切刀破损时主要集中在刃口部位崩裂,而整体更换成本比较大。
技术实现要素:4.本发明针对目前普遍采用的海绵钛钛坨切割切刀的不足之处,设计了一种用于提升海绵钛切割疏松小粒度产量的分离式锯齿切刀,以解决一次切割成型率低、使用寿命短、切割后料块尺寸大、切割处小粒度产量低,成本高的问题。
5.为了达到上述目的,本发明所采用的技术方案是:用于提升海绵钛切割疏松小粒度产量的分离式锯齿切刀,包括固定块和与固定块相配合的斜锯齿状刀刃,固定块和斜锯齿状刀刃两者共同可拆卸的安装在油压机的刀架上,其中,斜锯齿状刀刃的底部沿其轴线方向倾斜设置,且斜锯齿状刀刃的底部间隔开设有若干贯穿其端面的通槽,该通槽相对于斜锯齿状刀刃的轴向倾斜设置。
6.进一步的,若干通槽较高的一端形成锯齿状的上刀刃,较低的一端形成锯齿状的下刀刃,且上刀刃与下刀刃间平行设置。
7.进一步的,所述上刀刃与下刀刃两者刃口的形状包括但不仅限于由若干条直线和圆弧组合后形成的向内凹陷的槽形结构。
8.进一步的,组成槽形结构的若干条直线和圆弧之间以及两者与斜锯齿状刀刃之间均具有圆形的过渡角。
9.进一步的,上刀刃与下刀刃两者刃口的形状及尺寸相同。
10.进一步的,上刀刃与下刀刃两者刃口的形状和尺寸均不相同。
11.进一步的,所述斜锯齿状刀刃的底部一侧向外延伸形成与斜锯齿状刀刃的端面平行设置的防磨凸台。
12.与现有技术相比,本发明的有益效果是:本发明通过将斜锯齿状刀刃的底部沿其轴线方向倾斜设置,且斜锯齿状刀刃的底部间隔开设有若干贯穿其端面的通槽,该通槽相对于斜锯齿状刀刃的轴向倾斜设置,从而可在若干通槽较高的一端形成锯齿状的上刀刃,较低的一端形成锯齿状的下刀刃,该斜锯齿状刀刃相对于现有刀刃成型率高,只需一次切割就可满足破碎机入料尺寸要求;同时,本发明中的分离式锯齿切刀包括固定块和与固定块相配合的斜锯齿状刀刃,再结合斜锯齿状刀刃的独特结构设计,使得切刀具有切割效率高和使用寿命长的优点,且在切割时产生的3
‑
12.7mm小粒度的产量提升了3倍。
附图说明
13.图1为本发明分离式锯齿切刀在油压机上的安装位置示意图;图2为本发明用于提升海绵钛切割疏松小粒度产量的分离式锯齿切刀的结构示意图;图3为图2沿a
‑
a向的剖视图;图4为图3中b处的放大示意图;图5为实施例中固定块的尺寸示意图;图6为实施例中斜锯齿状刀刃的尺寸示意图;图7为图6中c处的局部放大示意图;图中标记:1、固定块,2、斜锯齿状刀刃,3、防磨凸台,4、沉头螺栓,5、通槽,6、上刀刃,7、下刀刃,8、刃口,9、油压机,10、钛坨。
具体实施方式
14.为使本发明实施例的目的、技术方案和优点更加清楚,下面将结合本发明中的附图,对本发明实施例中的技术方案进行清楚、完整地描述,显然,所描述的实施例是本发明一部分实施例,而不是全部的实施例,基于本发明中的实施例,本领域普通技术人员在没有作出创造性劳动前提下所获得的所有其他实施例,都属于本发明保护的范围。
15.用于提升海绵钛切割疏松小粒度产量的分离式锯齿切刀,包括固定块1和与固定块相配合的斜锯齿状刀刃2,固定块和斜锯齿状刀刃两者共同可拆卸的安装在油压机9的刀架上,在安装时,固定块1可通过沉头螺栓与油压机的刀架连接,该连接方式在切割时增加了竖直方向的阻力,避免出现连接松动的问题,沉头螺栓及对应的沉孔数量可设置为16~32个,从而可实现将固定块1长久的存放于刀架上,更换时仅更换斜锯齿状刀刃2即可。
16.如图2所示,斜锯齿状刀刃2的底部沿其轴线方向倾斜设置,且斜锯齿状刀刃2的底部间隔开设有若干贯穿其端面的通槽5,该通槽5相对于斜锯齿状刀刃2的轴向倾斜设置。
17.如图6所示,若干通槽5较高的一端形成锯齿状的上刀刃6,较低的一端形成锯齿状的下刀刃7,且上刀刃与下刀刃间平行设置。在分离式锯齿切刀下行过程中,下刀刃7先与钛坨10接触起到切割作用,通过通槽5的挤压可形成更多的小粒度海绵钛,随后上刀刃6将大
块海绵钛再次切割,最终将钛坨切割成尺寸较小、满足破碎机入料尺寸的钛块。该斜锯齿状刀刃相对于现有刀刃成型率高,只需一次切割就可满足破碎机入料尺寸要求,一次切割小于300mm钛块成型率大于90%,为目前直线形切刀的2倍。
18.进一步的,所述上刀刃与下刀刃两者刃口的形状包括但不仅限于由若干条直线和圆弧组合后形成的向内凹陷的槽形结构。为了达到最佳的使用效果,组成槽形结构的若干条直线和圆弧之间以及两者与斜锯齿状刀刃2之间均具有圆形的过渡角。
19.实施例1本实施例中,如图7所示,所述刃口8的形状由一条倾斜设置的直线、一条水平设置的直线以及一段圆弧组合而成,三者通过圆形的过渡角依次连接后连接至斜锯齿状刀刃2,形成向内凹陷的槽形结构。
20.实施例2本实施例中与实施例1的区别在于:所述刃口的形状由两条倾斜设置的直线组合而成,两条倾斜设置的直线对称设置且两者通过圆形的过渡角连接后连接至斜锯齿状刀刃2,形成倒立的v型结构。
21.实施例3本实施例中与实施例1的区别在于:所述刃口的形状由若干条倾斜设置的直线组合而成,若干条倾斜设置的直线之间通过圆形的过渡角连接后连接至斜锯齿状刀刃2,形成m型结构。
22.实施例4本实施例中,上刀刃6与下刀刃7两者刃口8的形状及尺寸相同,均采用实施例1
‑
3中任意一种公开的槽形结构,当然,也可根据需要,采用若干条直线和圆弧自行组合后形成的向内凹陷的槽形结构。
23.实施例5本实施例中,上刀刃6与下刀刃7两者刃口8的形状和尺寸均不相同,且两者刃口的形状可在实施例1
‑
3中随机选择,当然,也可根据需要,采用若干条直线和圆弧自行组合后形成的向内凹陷的槽形结构。
24.实施例6本实施例与实施例4的区别在于:如图3所示,本实施例在所述斜锯齿状刀刃2的底部一侧向外延伸形成与斜锯齿状刀刃的端面平行设置的防磨凸台3,防磨凸台用于防止切割过程中刀具磨损污染海绵钛,本实施例中将防磨凸台设置在斜锯齿状刀刃2的背部。
25.实施例7本实施例对各部件的尺寸做进一步限定,以作为实施本发明的较佳的一个实施例,如图5和图6所示,斜锯齿状刀刃2的顶部具有凸起部,凸起部的长度为l4,固定块1靠近防磨凸台的一侧具有与凸起部相匹配的凹槽,凹槽的长度为l3,高度为l2,如图4所示,固定块1与斜锯齿状刀刃2两者的装配间隙为l1,其中,l1为0~50mm,l2为0~200mm,l3为20~800mm。l1用于调整固定块1与斜锯齿状刀刃2之间的贴合度,切刀左右两侧需预留间隙,便于两者间的贴合紧密,并防止切刀在切割过程中因受力不均匀造成断裂,其中l3=l4+2l1,圆角r1保证固定块1与斜锯齿状刀刃2的强度,防止断裂。
26.斜锯齿状刀刃的下刀刃7选择合适的斜锯齿宽度l5,相邻斜锯齿间距l6,斜锯齿倾
斜角θ,锯齿刀深度l7和过渡圆角r2,其中l5为0~800mm,l6为0~400mm,l7为0~300mm,倾斜角θ为0~90
°
,如图7所示,θ为上刀刃的设置方向与通槽的设置方向之间具有的夹角,θ角的大小决定了切割过程中断裂形成小粒度海绵钛的量,l5与l6决定切刀锯齿的宽度和密度,l7决定切刀切割时的厚度。圆角r2为1~200mm,避免切割时作用力集中,造成的刀刃崩口或断裂。
27.本发明中的分离式锯齿切刀包括固定块和与固定块相配合的斜锯齿状刀刃,再结合斜锯齿状刀刃的独特结构设计,使得切刀具有切割效率高和使用寿命长的优点,其使用寿命约为直线形切刀的2倍;在切割时产生3
‑
12.7mm小粒度产量提升3倍,切刀采购成本降低1倍。
28.对所公开的实施例的上述说明,使本领域专业技术人员能够实现或使用本发明。对这些实施例的多种修改对本领域的专业技术人员来说将是显而易见的,本文中所定义的一般原理可以在不脱离本发明的精神或范围的情况下,在其它实施例中实现。因此,本发明将不会被限制于本文所示的这些实施例,而是要符合与本文所公开的原理和新颖特点相一致的最宽的范围。