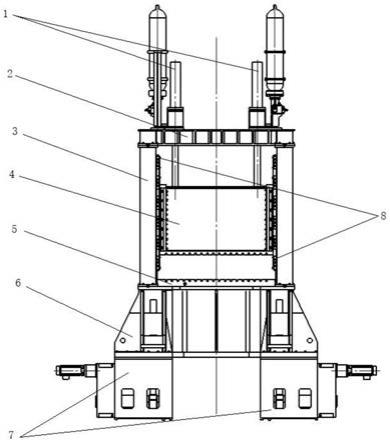
1.本发明涉及锻压装备技术领域,具体涉及一种四点分布式模块化组合底传动压力机。
背景技术:2.随着汽车家电等行业产品向“多品种、小批量”发展,配套的冲压厂生产线也随之改变,单工序模向多工位模具集成,机械手、机器人等广泛应用于自动化冲压线,对冲压设备的工作台面要求越来越宽、吨位越来越大、冲次越来越高、稳定性越来越好,压力机市场的特殊要求定货越来越多。
3.底传动压力机是现有的压力机的一种,例如中国专利公开的一种底传动压力机结构(cn206690587u);包括底座,底座上设置有工作台,工作台上方设有滑块,滑块下部固定连接有导柱,底座为封闭式箱体,工作台上对应各导柱设置有通孔,各导柱穿过对应通孔后向下伸入底座内部,底座的左侧和右侧同轴设置有用于水平安装曲轴的支撑孔,曲轴的偏心端设置有连杆,各导柱下端通过传动块与连杆上端传动连接;曲轴水平伸出底座的一端与驱动机构传动连接。工作台上设置有立柱,立柱上端与顶板固定,顶板上安装有平衡缸,平衡缸的活塞杆伸出端经挂块与滑块相连。
4.上述技术存在的不足在于:第一、 采用传统底传动压力机主传动结构模式,一根传动轴+两侧曲柄连杆机构,将传动机构装进底座,该模式的缺陷有:装配维修困难、工作台面和公称力吨位不宜做大、工作台两侧因布置连杆而无法进出料等;缺少曲柄连杆偏心力的抵消机构,开口不宜做大、冲次不宜做高;第二、无封闭高度自动调整机构,对模不方便,影响了底传动压力机的通用性;第三、对于特殊定货的压力机,其需要重新进行尺寸设计,单台的生产制造组织难度大、周期长、成本高,对于习惯于批量生产的压力机厂商构成较大的压力。
技术实现要素:5.针对上述现有技术存在的问题,本发明提供一种四点分布式模块化组合底传动压力机。本发明采用四点分布式动力系统,即使用四个分立的伺服电机驱动曲柄连杆机构动力箱模块、共用一套总控驱动器系统实现联驱,通过“四匹小马拉大车、水平方向偏心力相互抵消”的方式,实现冲次高、台面大、吨位大、开口大等设计目标。
6.为了实现上述目的,本发明采用的技术方案是:一种四点分布式模块化组合底传动压力机,包括上横梁、下横梁,上横梁、下横梁之间连接有立柱;滑块滑动安装在立柱上;还包括4个位于下横梁下方的结构相同的动力箱机构,所述动力箱机构通过高度可调的拉杆螺母机构连接所述滑块;所述滑块与立柱之间安装有磁尺机构。
7.其进一步是:4个所述动力箱机构以下横梁中心对称布置;动力箱机构通过圆柱销和螺钉固定在下横梁下面;所述立柱共有四个,四个立柱以下横梁中心对称布置。
8.所述拉杆螺母机构包括拉杆;所述拉杆竖向穿设在所述滑块上,拉杆通过整体螺母和剖分螺母与滑块固定;所述动力箱机构的动力输出端是竖向滑动安装于动力箱机构导向孔中的导柱;所述拉杆下端通过螺纹配合连接在导柱上。
9.所述导柱可转动安装于动力箱机构的导向孔中;所述动力箱机构包括用于调节拉杆螺母机构的蜗轮箱机构;所述蜗轮箱机构包括固定在动力箱体上的蜗轮箱体,蜗轮箱体内安装有相互配合的蜗轮、蜗轮轴;所述蜗轮滑动套装在所述导柱外,蜗轮与导柱之间通过滑键连接;所述蜗轮轴输入端通过联轴套和键与调整伺服电机连接,调整伺服电机固定在电机支架上,电机支架安装在动力箱体上。
10.所述动力箱机构包括曲轴、球头连杆、减速机和主伺服电机;所述导柱下端通过上球碗压盖安装有下球碗、上球碗;所述球头连杆的球头与下球碗、上球碗配合连接,球头连杆远离球头的一端与曲轴转动连接;所述曲轴两端连接有前支承座、后支承座,前支承座、后支承座安装在动力箱体;所述减速机输出轴与曲轴输入端通过曲轴联轴套和键连接;所述主伺服电机输出端与减速机输入端连接。
11.所述上横梁、立柱、下横梁通过方键和螺钉固定连接,下横梁上固定有与滑块相对的工作台板;四个所述立柱呈矩形布置,立柱内侧设有与滑块配合的立柱导轨;所述立柱导轨包括一根矩形直角导轨,矩形直角导轨通过多个固定块固定在立柱内侧;所述滑块的四角位置分别固定有滑块导轨,滑块导轨与矩形直角导轨竖向滑动配合。
12.所述磁尺机构共有四个,磁尺机构磁尺和磁头;所述磁尺一一对应固定在立柱上,磁头固定在滑块侧面与磁尺相对配合的位置上。
13.所述上横梁两侧分别固定有一个平衡缸机构;所述平衡缸机构包括与上横梁固定连接的平衡器架,平衡器架上安装有控制阀块、蓄能器和竖向布置的柱塞缸;所述控制阀块通过油管与柱塞缸和蓄能器分别连通,控制阀块还通过另一路油管和补油泵站系统连通;所述柱塞缸活塞杆下端连接有一个联接块,联接块安装在滑块上;所述平衡器架由柱塞缸座、阀块支架、蓄能器支柱和架底板焊接或铸造而成;所述架底板通过螺栓连接安装在上横梁上;所述柱塞缸通过螺栓连接安装在柱塞缸座上;所述控制阀块通过螺栓连接安装在阀块支架上;所述蓄能器通过托板和抱箍固定在蓄能器支柱一侧。
14.所述动力箱机构安装在基础安装地坑内,基础安装地坑底部设置有轻轨;所述轻轨上安装有用于将动力箱机构移出或移进下横梁的地轨升降车。
15.所述动力箱机构用液压缸机构模块替换。
16.本发明的有益效果是:1、压力机采用模块化组合结构;通过将压力机动力机构设计成一个四点分布式动力系统,即四个结构完全相同的动力箱部件模块,和下横梁模块、滑块模块、拉杆模块、立柱模块、上横梁模块等。采用不同模块的组合,可组装成吨位、行程、工作台面等不同参数的底传动压力机。
17.2、动力机构采用四点分布式动力系统;使用四个分立的伺服电机驱动曲柄连杆机构(动力箱),共用一套总控驱动器系统实现联驱,采用了“四匹小马拉大车”的模式。与同吨位的压力机传动机构相比,该模式的优点是,每个动力箱输出的压力(拉力)只有其四分之一,显著降低了设计制造难度,成本也随之下降。
18.3、四个分立的动力箱,可两两抵消“水平方向偏心惯性分力”,提高运转平稳性;使用四个分立的动力箱(伺服电机驱动曲柄连杆机构),共用一套总控驱动器系统实现联驱,两两对称布置的曲柄连杆机构,运转时,可采用两曲轴反向同步旋转,使得曲柄连杆机构的“水平方向偏心惯性分力”相互抵消,进而满足压力机高冲次、运转平稳的要求。
19.4、压力机制造维修便捷;四个分立的伺服电机驱动曲柄连杆机构(动力箱机构),采用模块化设计,结构完全一致、可以互换;每个伺服电机驱动曲柄连杆机构等装配在动力箱上、构成一体,可通过地轨升降车移出下横梁,然后用车间行车吊出地坑维护,克服了传统底传动压力机不方便装配维护的缺点。
20.5、滑块封闭高度机构装在动力箱上,减小了滑块运动惯量;四个动力箱部件,都有单独伺服电机驱动的曲柄连杆封闭高度调整机构;通过总控系统控制,四个分立机构可同步动作,完成滑块封闭高度调整功能。滑块封闭高度机构装在动力箱上,减小了滑块运动惯量,提高了压力机运转平稳性。
21.6、滑块不仅可实现封闭高度自动调整,还具有“四点调平”功能;四点分布式的曲柄连杆封闭高度调整机构,可通过总控系统,对每个分立的调整伺服电机进行同步驱动,借助固定在立柱上的磁尺所反馈数据,形成闭环,实现封闭高度的自动调整;四点分布式的曲柄连杆封闭高度调整机构,也可通过总控系统进行单独控制,对每个分立的伺服电机单独驱动,借助固定在相应立柱上的磁尺所反馈的数据,完成滑块的“四点调平”功能。
22.7、滑块不仅具有过载保护功能,还具有偏载过载保护功能;四点分布式动力箱的曲柄连杆机构的驱动伺服电机,具有过载保护功能;滑块的过载保护值,为四个分立的伺服电机过载保护值之和。当需要对滑块进行偏载过载保护时,只需要在总控系统上增加一段程序,对四个驱动伺服电机的电流差异值大小进行设定检测,当超过设定值时,即停机保护。
23.8、滑块承受偏载能力增强;将滑块施力点由传统底传动压力机的两侧两点,改进为四角四点,提高了滑块负载刚性,特别是抗偏载能力。
24.9、突破了底传动压力机不能左右方向进料的禁忌;滑块施力点由传统底传动压力机的两侧两点,改进为四角四点后,将机床侧开口原放置连杆机构的空间释放出来,可实现左右方向进出物料(模具、或移台)。
25.10、立柱和上横梁基本不承受工作负载,可进行轻量化设计,降低重量和制造成本。
26.11、下横梁四脚增加减振垫后,可吸收压力机振动能,适宜设计为大行程、快速压力机,拓展底传动压力机的应用领域。
附图说明
27.图1为本发明实施例一主视图;图2为本发明实施例一左视图;
图3为本发明实施例一俯视图;图4为本发明实施例一仰视图;图5为本发明实施例一立体示意图;图6为本发明实施例一传动机构图(a
‑
a剖面图)图7为本发明实施例一中动力箱部件主视图;图8为本发明实施例一中动力箱部件左视图;图9为本发明实施例一中动力箱部件俯视图;图10为本发明实施例一中动力箱部件剖视图(b
‑
b剖面图);图11为本发明实施例一中立柱导轨、滑块导轨处放大图;图12为本发明实施例一中平衡缸机构处的放大图;图13为本发明实施例一中地坑里的地轨升降车;图14为本发明实施例二主视图;图15为本发明实施例二左视图;图中:1、平衡缸机构,2、上横梁,3、立柱,4、滑块,5、工作台板,6、下横梁,7、动力箱机构,8、立柱导轨,9、拉杆螺母机构,10、磁尺机构,11、整体螺母,12、剖分螺母,13、拉杆,14、导柱,15、下球碗,16、上球碗,17、上球碗压盖,18、后支承座,19、球头连杆,20、连杆盖,21、曲轴,22、动力箱体,23、减速机,24、主伺服电机,25、调整伺服电机,26、电机支架,27、蜗轮箱机构,28、蜗杆轴联接套,29、滑键,30、蜗轮箱压盖,31、蜗轮,32、蜗轮箱体,33、油池板,34、前支承座,35、曲轴联轴套,36、蓄能器,37、柱塞缸,38、控制阀块,39、平衡器架,40、联接块,41、磁尺,42、磁头,43、方键,44、滑块导轨,45、固定块,46、矩形直角导轨,47、蓄能器支柱、48、阀块支架, 49、架底板,50、柱塞缸座,51、托板,52、抱箍,53、基础安装地坑,54、轻轨,55、地轨升降车,56、液压缸机构。
具体实施方式
28.下面结合附图对本发明作进一步说明。
29.实施例一结合图1至图5所示,一种四点分布式模块化组合底传动压力机,分体式框架包括上横梁2、下横梁6和四根立柱3,四根立柱3呈矩形布置,上横梁2、立柱3、下横梁6通过方键43和螺钉固定连接。滑块4竖向滑动安装在立柱3上,下横梁6上固定有与滑块4相对的工作台板5。下横梁6四角下面分别固定有结构相同的动力箱机构7,动力箱机构7上端连接有竖向布置的拉杆螺母机构9,拉杆螺母机构9上端连接滑块4。立柱3和滑块4四角上安装有磁尺机构10。
30.再结合图6所示,拉杆螺母机构9包括拉杆13,拉杆13竖向布置,拉杆13通过整体螺母11和剖分螺母12固定在滑块4上。拉杆13下端通过螺纹配合与动力箱机构7中的导柱14连接。拉杆13与滑块4的连接采用剖分螺母,主要是便于装配、可减少拉杆的台阶轴设计降低成本。
31.再结合图7至图10所示,导柱14是动力箱机构7的动力输出端,导柱14竖向滑动安装于动力箱机构7导向孔中,并且导柱14可以在动力箱机构7导向孔中转动;动力箱机构7还包括曲轴21、球头连杆19、连杆盖20等。下球碗15、上球碗16通过上球碗压盖17安装在导柱14下。球头连杆19的球头动配合安装于下球碗15、上球碗16,球头连杆19另一端通过连杆盖20与曲轴21可转动固定连接。曲轴21通过动配合的前支承座33、后支承座18,安装在动力箱体22上。曲轴21输入端通过曲轴联轴套35和键,与减速机23输出轴连接。主伺服电机24安装在对应的减速机23输入端。曲轴没有直接安装在动力箱体32上,主要是当曲轴偏心距过大时,要求动力箱体上的曲柄装配工艺孔也相应增大,设计制造成本也随之增加。曲轴通可拆卸支承座安装在动力箱体上,方便于模块化设计生产。
32.动力箱机构7还包括一个用于带动导柱14转动的蜗轮箱机构27,以此调节拉杆螺母机构9的高度;蜗轮箱机构27包括蜗轮31、蜗轮轴28、蜗轮箱压盖30等。蜗轮31、蜗轮轴28安装在蜗轮箱体30内,蜗轮箱体30安装在动力箱体32上。滑键29安装在蜗轮31孔槽内,导柱14在动力箱体32的导向孔内滑动,导柱14的键槽同时与滑键29动配合进行竖向滑动。蜗轮轴28输入端通过联轴套和键与调整伺服电机25连接。调整伺服电机25固定在电机支架26上,电机支架26安装在动力箱体32上。蜗轮箱机构选择设计在动力箱体上、而不是滑块上,主要是避免滑块结构过于复杂、增加重量,导致惯性力增大、影响压力机运转稳定性。
33.再结合图11和图12所示,上横梁2两侧分别固定有一个平衡缸机构1;平衡缸机构1包括与上横梁2固定连接的平衡器架39,平衡器架39由柱塞缸座50、阀块支架48、蓄能器支柱47和架底板49焊接或铸造而成。平衡器架39采用模块化集成设计,可对平衡缸机构独立装配完成后,再进行总装,方便组合分解,维护性好。架底板49通过螺栓连接安装在上横梁2上;柱塞缸37通过螺栓连接安装在柱塞缸座50上;控制阀块38通过螺栓连接安装在阀块支架48上;蓄能器36通过托板51和抱箍52固定在蓄能器支柱47一侧。控制阀块38通过油管与柱塞缸37和蓄能器36分别连通,控制阀块38还通过另一路油管和补油泵站系统连通。柱塞缸37活塞杆下端连接有一个联接块40,联接块40安装在滑块4上。柱塞缸37、阀块38和蓄能器36等构成一个液压弹簧,通过柱塞缸活塞杆,将液压弹力作用于固定在滑块的联接块40上。
34.平衡缸机构的柱塞缸、阀块和蓄能器等构成一个液压弹簧,通过柱塞缸活塞杆,将大于滑块部件重量、以近似常数值的液压拉力作用于联接块上,联接块通过固定在滑块两侧,将滑块部件向上拉起,直至拉杆13、导柱14的螺纹齿面接触贴实,从而实现消除螺纹轴向间隙、提高滑块下死点重复定位精度的目标。
35.结合图11所示,立柱3内侧设有立柱导轨8,立柱导轨8包括一根矩形直角导轨46,矩形直角导轨46通过若干固定块45固定在立柱3内侧。滑块4的四角位置分别固定有滑块导轨44,滑块导轨44与矩形直角导轨46竖向滑动配合。固定块45上安装有螺钉调整,可通过螺钉调整矩形直角导轨46和滑块4上的滑块导轨44的摩擦副间隙,使滑块沿矩形直角导轨方向上下滑动。
36.结合图11所示,磁尺机构10共有四个,包括磁尺41和磁头42。磁尺41固定在立柱3上,磁头42相对应的固定滑块4侧面上并随滑块4在立柱3内竖向滑动。滑块4四角安装磁尺机构10,主要目的是即时测量滑块每个角与工作台板上平面的精确距离,可反馈总控系统,
实现滑块四角自动调平目标、和完成自动调模功能要求。
37.结合图13所示,基础安装地坑53内,预埋有轻轨54;动力箱机构7可通过地轨升降车55移出或移进下横梁6。然后用车间行车吊出地坑维护,克服了传统底传动压力机不方便装配维护的缺陷。
38.工作原理:压力机运行原理:按下压力机运行启动按钮,总控系统向四个动力箱机构的主伺服电机驱动器发讯,四个主伺服电机中,两个正转、两个同步反转。如图6所示,沿压力机前后方向对称布置的动力箱机构主伺服电机,前面的一个正转、后面的一个同步反转,或相反。同步反向旋转的目的,是为了抵消曲柄连杆机构水平方向的偏心惯性力,提高机床运转平稳性。
39.传动过程:主伺服电机24驱动减速机23,减速机23驱动曲轴21,曲轴21带动球头连杆19、连杆盖20,推动导柱14竖向上下滑动;导柱14通过螺纹连接带动拉杆13同步滑动,拉杆13通过整体螺母11、剖分螺母12驱动滑块4同步竖向移动,完成滑块冲压过程。
40.本实施例与传统底传动压力机相比,改变了“一根传动轴+两侧曲柄连杆机构”装进下横梁内的设计思路,采用将传动拉杆放到滑块四角、在下横梁四角下面分别固定有结构相同的动力箱机构模块的模式,克服了传统底传动压力机装配维修困难、工作台面和公称力吨位不宜做大、工作台两侧因布置连杆而无法进出料、曲柄连杆没有偏心力抵消机构时开口不宜做大、冲次不宜做高等一系列缺陷。
41.其次,采用四点分布式动力系统,即使用四个分立的伺服电机驱动曲柄连杆机构(动力箱机构)、共用一套总控驱动器系统实现联驱,采用了“四匹小马拉大车”的模式。与同吨位的压力机传动机构相比,该模式的优点是,每个动力箱机构输出的压力(拉力)只有其四分之一,显著降低了设计制造难度,成本也随之下降。
42.再者,本发明公布的一种四点分布式模块化组合底传动压力机,也是一种伺服机械压力机,可对滑块位移、压力、速度运行曲线进行编程控制,完成伺服压力机的功能要求。
43.最后,滑块封闭高度调整原理:四点分布式的动力箱蜗杆蜗轮封闭高度调整机构,可通过总控系统,对每个分立的调整伺服电机进行同步驱动,借助固定在立柱上的磁尺所反馈数据,形成闭环,实现封闭高度的自动调整。四点分布式的封闭高度调整机构,也可通过总控系统进行单独控制,对每个分立的伺服电机单独驱动,借助固定在相应立柱上的磁尺所反馈的数据,完成滑块的“四点调平”功能。
44.实施例二结合图14、图15所示,本实施例二与实施例一的区别在于:动力箱机构模块替换成液压缸机构模块,底传动机械压力机转换成了底传动液压机。