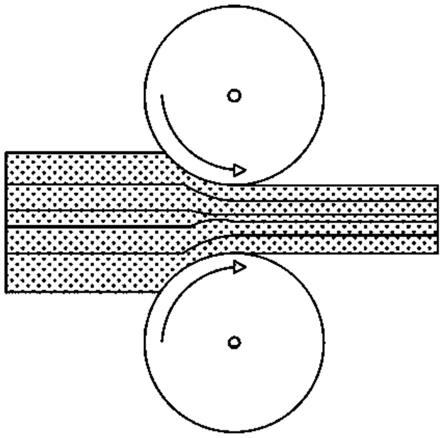
1.本发明涉及金属复合材料制备技术领域,具体涉及一种循环梯度叠轧制备高强度高塑性铝合金板材的方法。
背景技术:2.一般的制作高强度铝合金的方法,例如等通道角挤压法(ecap)、高压扭转法(hpt)、多向锻造法(mf)、累积叠轧法(arb)、循环挤压法(cec),都是通过剧烈形变技术制取超细晶材料,但是通过这些方法所得到的超细晶材料往往表现为强度比较高而韧塑性比较差。
3.金属材料的强度与韧塑性通常不可兼得;强度高主要是因为在剧烈塑性过程中晶粒不断细化,而且在材料内部产生大量的晶体缺陷;韧塑性下降的原因则是多方面的,主要可以归纳为以下两种:第一种是塑性变形过程中产生大量的缺陷,包括夹杂和微裂纹等,这些缺陷的存在很大程度上影响了材料的塑性;第二种是由于在超细晶材料中晶粒细小而且界面之间的距离很小,位错只能在很小的区域内滑移,并且很难在晶体内部聚集,造成只能有很小的应变硬化,进一步的影响了材料的塑性变形能力。但是经研究发现晶粒细化是在提高材料强度的同时,还能有效提高塑性的一种重要方法,而梯度材料也能够很好的兼得两种属性,在获得高强度的同时仍具有良好的塑性;但是以往的制作梯度材料的方法往往是在材料表层形成超细晶颗粒;因此,如何在现有条件下实现中心层细晶梯度材料制备是研究的重点问题之一。
技术实现要素:4.本发明的目的是提供一种循环梯度叠轧制备高强度高塑性铝合金板材的方法,通过不同厚度板材的循环梯度排布,产生表层粗晶粒中心层细晶粒,再经过反复叠轧,制成高强度高塑性的铝合金板材。
5.本发明的方法按以下步骤进行:
6.1、将铝合金板材进行退火处理,随后空冷或水冷至室温,制成退火板;
7.2、将退火板进行单道次冷轧,根据n种总变形率分别制成不同厚度的n种冷轧板,其中n≥2,n种冷轧板按厚度从大到小排列依次为第1~n冷轧板;或者将两个相同的退火板叠放后进行第一次单道次冷轧,制成1次叠放冷轧板,然后将一次叠放冷轧板放在中间,上下各叠放一块退火板进行第二次单道次冷轧,制成2次叠放冷轧板,以此类推,直至制成n次叠放冷轧板,其中n≥2;其中,从第二次单道次冷轧开始,当进行下一次单道次冷轧时,叠放冷轧板始终处于退火板之间,最终使n次叠放冷轧板的中心层被反复轧制,各层厚度按从中部到两个侧面从小到大梯度排列;
8.3、将第1~n冷轧板分别剪裁制成长宽尺寸与退火板相同的n种冷轧剪裁板;或者将2个n次叠放冷轧板剪裁制成长宽尺寸与退火板相同的2个叠放冷轧剪裁板;
9.4、对冷轧剪裁板或叠放冷轧剪裁板进行表面处理,获得n种表面处理冷轧剪裁板
或2个表面处理叠放冷轧剪裁板;
10.5、将n种表面处理冷轧剪裁板按梯度方式堆叠,构成组合坯,组合坯中各表面处理冷轧剪裁板的厚度由中部向两个侧面按从小到大排列,组合坯中的厚度分布为双向梯度分布;或者将n种表面处理冷轧剪裁板与退火板按梯度方式堆叠,构成组合坯,组合坯中退火板位于两侧,表面处理冷轧剪裁板从中部到两个侧面的厚度从小到大排列,组合坯中的厚度分布为双向梯度分布;或者将2个表面处理叠放冷轧剪裁板堆叠,构成组合坯,各表面处理叠放冷轧剪裁板内部各层从中部到两个侧面厚度按从小到大梯度排列,或者将n种表面处理冷轧剪裁板按梯度方式堆叠,构成组合坯,组合坯中各表面处理冷轧剪裁板的厚度从一个侧面到另一个侧面按从小到大排列,组合坯中的厚度分布为单向梯度分布;或者将n种表面处理冷轧剪裁板与退火板按梯度方式堆叠,构成组合坯,组合坯中退火板位于一侧,厚度最小的表面处理冷轧剪裁板位于另一侧,其余各表面处理冷轧剪裁板的厚度从退火板一侧到另一侧按从大到小排列,组合坯中的厚度分布为单向梯度分布;
11.6、将组合坯用铝钉铆接固定,然后进行成型冷轧,成型冷轧的总压下率为50~80%,制成一级成型冷轧板;将一级成型冷轧板在150~500℃条件下保温30~180min进行热处理,制成高强度高塑性铝合金板材。
12.上述的步骤6中,将两个一级成型冷轧板叠放后,进行成型冷轧,成型冷轧的总压下率为50~80%,制成二级成型冷轧板;将二级成型冷轧板在150~500℃条件下保温30~180min进行热处理,制成高强度高塑性铝合金板材。
13.上述的步骤6中,将两个一级成型冷轧板叠放后,进行成型冷轧,成型冷轧的总压下率为50~80%,制成二级成型冷轧板;重复上述步骤,直至制成n级冷轧板,其中n=3~8;将n级成型冷轧板在150~500℃条件下保温30~180min进行热处理,制成高强度高塑性铝合金板材。
14.上述的步骤1中,退火温度150~450℃,时间30~180min。
15.上述的步骤2中,当制备第1~n冷轧板时,单道次冷轧的压下率15~88%。
16.上述的步骤1、2和5中,退火板选用厚度1~9mm。
17.上述的步骤5中,当组合坯中的厚度分布为双向梯度分布时,与组合坯中心处距离相等的两个表面处理冷轧剪裁板厚度相同。
18.上述的步骤4中,表面处理的步骤为:表面喷砂去除表面氧化膜;,后可选用有机溶剂清洗,最后使表面自然风干。
19.上述的步骤2中,各次单道次冷轧的轧制方向相同。
20.上述的步骤6中,成型冷轧时采用双辊或四辊轧机,轧制时的轧辊转速200~600r/min。
21.上述的步骤5中,当组合坯中有多个表面处理冷轧剪裁板时,相邻两个表面处理冷轧剪裁板中的厚度比按厚板:薄板≥1.2。
22.上述的步骤6中,成型冷轧是在不使用润滑剂的情况下进行的单道次冷轧,以保证结合效果。
23.上述的高强度高塑性铝合金板材的屈服强度为100~160mpa,抗拉强度为100~180mpa,维氏硬度为40~98hv。
24.上述的高强度高塑性铝合金板材的中部晶粒粒径为0.1~15μm;表面的晶粒粒径
为12~30μm。
25.本发明利用梯度纳米材料的原理,采用了相比过去更为方便且新颖的方法,即循环梯度叠轧制备高强度高塑性铝合金板材的方法,通过叠轧的方法将不同厚度的铝合金板结合在一起,对其进行梯度排列,形成了中心部晶粒尺寸小而外表的晶粒尺寸大,沿厚度方向有明显的梯度排布,并能大幅度提高层片厚度细化效率,获得了具有梯度结构的高强度高塑性铝合金板材,满足应用性能的需要。
附图说明
26.图1为本发明实施例1中成型冷轧步骤的轧制方式示意图;
27.图2为本发明实施例1中六级成型冷轧板的微观组织示意图。
具体实施方式
28.本发明实施例中成型冷轧是在无润滑剂的情况下进行的单道次冷轧,以保证结合效果。
29.本发明实施例中进行成型冷轧时,单道次压下率为15~30%。
30.实施例1
31.采用1060铝板,铝板厚度3mm;
32.将铝合金板材进行退火处理,退火温度350℃,时间120min,随后空冷至室温,制成退火板;
33.将退火板进行单道次冷轧,分别制成厚度为2.5mm、1.5mm和0.5mm的第1冷轧板、第二冷轧板和第三冷轧板,变形率分别为16.7%、50%和83.3%;
34.将第1冷轧板、第二冷轧板和第三冷轧板分别剪裁制成侧面尺寸为500mm
×
250mm的第一剪裁板、第二剪裁板和第三剪裁板;
35.对第一剪裁板、第二剪裁板和第三剪裁板进行表面处理,表面喷砂去除表面氧化膜;,后可选用有机溶剂清洗,最后使表面自然风干,获得第一表面处理冷轧剪裁板、第二表面处理冷轧剪裁板和第三表面处理冷轧剪裁板;
36.将第一表面处理冷轧剪裁板、第二表面处理冷轧剪裁板和第三表面处理冷轧剪裁板按梯度方式堆叠,构成组合坯,组合坯中各表面处理冷轧剪裁板的厚度由中部向两个侧面按从小到大排列,组合坯中的厚度分布为双向梯度分布;组合坯的两个侧面为厚度2.5m的第一表面处理冷轧剪裁板,中间为一个厚度0.5mm的第三表面处理冷轧剪裁板,在第三表面处理冷轧剪裁板的两侧各有一个厚度1.5mm的第二表面处理冷轧剪裁板;总共5个表面处理冷轧剪裁板组合成一个组合坯;
37.将组合坯的四角打孔后用铝钉铆接固定,然后进行成型冷轧,成型冷轧的总压下率为53%,制成一级成型冷轧板,厚度4mm;成型冷轧时采用双辊轧机,轧制时的轧辊转速500r/min;成型冷轧方式如图1所示;
38.将两个尺寸相同的一级成型冷轧板叠放,再次进行成型冷轧,总压下率为53%,制成二级成型冷轧板;重复上述的叠放+成型冷轧操作,直至形成六级成型冷轧板,其微观组织如图2所示;
39.将六级成型冷轧板在500℃条件下保温60min进行热处理,制成高强度高塑性铝合
金板材,屈服强度为144mpa,抗拉强度为159mpa,维氏硬度为73hv,中部晶粒粒径为1~8μm;表面的晶粒粒径为16~25μm。
40.实施例2
41.方法同实施例1,不同点在于:
42.(1)采用6061铝合金板,铝板厚度6mm;
43.(2)退火处理温度400℃,时间60min,水冷至室温;
44.(3)将退火板进行单道次冷轧,分别制成厚度为3mm、2mm和1mm的第1冷轧板、第二冷轧板和第三冷轧板,变形率分别为50%、66.7%和83.3%;
45.(4)将第1冷轧板、第二冷轧板和第三冷轧板分别剪裁制成侧面尺寸为400mm
×
250mm的第一剪裁板、第二剪裁板和第三剪裁板;
46.(5)堆叠构成组合坯,组合坯中各表面处理冷轧剪裁板的厚度从一个侧面到另一个侧面按从小到大排列,组合坯中的厚度分布为单向梯度分布;组合坯中厚度3mm的第一表面处理冷轧剪裁板在一个侧面,厚度1mm的第三表面处理冷轧剪裁板在另一个侧面,两者中间为厚度2mm的第二表面处理冷轧剪裁板;总共3个表面处理冷轧剪裁板组合成一个组合坯;
47.(6)成型冷轧的总压下率为60%,一级成型冷轧板厚度2.4mm;轧制时的轧辊转速400r/min;
48.(7)按总压下率60%,重复进行叠放+成型冷轧,直至形成四级成型冷轧板;在堆叠构成组合坯时,厚度最大的表面处理冷轧剪裁板所在侧面的厚侧面,厚度最小的表面处理冷轧剪裁板所在侧面为薄侧面,在各级成型冷轧板的堆叠过程中,厚侧面与薄侧面相连接;
49.(8)将四级成型冷轧板在400℃条件下保温120min进行热处理;高强度高塑性铝合金板材的屈服强度为119mpa,抗拉强度为129mpa,维氏硬度为51hv;高强度高塑性铝合金板材的中部晶粒粒径为0.1~5.2μm;表面的晶粒粒径为10~29μm。
50.实施例3
51.方法同实施例1,不同点在于:
52.(1)采用7085铝合金板,铝板厚度4mm;
53.(2)退火处理温度150℃,时间180min,水冷至室温;
54.(3)将退火板进行单道次冷轧,分别制成厚度为2mm、1mm和0.5mm的第1冷轧板、第二冷轧板和第三冷轧板,变形率分别为50%、75%和87.5%;
55.(4)堆叠构成组合坯,组合坯中各表面处理冷轧剪裁板的厚度从一个侧面到另一个侧面按从小到大排列,组合坯中的厚度分布为单向梯度分布;组合坯中厚度2mm的第一表面处理冷轧剪裁板在一个侧面,厚度0.5mm的第三表面处理冷轧剪裁板在另一个侧面,两者中间为厚度1mm的第二表面处理冷轧剪裁板;总共3个表面处理冷轧剪裁板组合成一个组合坯;
56.(5)成型冷轧的总压下率为57%,一级成型冷轧板厚度1.5mm;轧制时的轧辊转速600r/min;
57.(6)按总压下率57%,重复进行叠放+成型冷轧,直至形成七级成型冷轧板;在堆叠构成组合坯时,厚度最大的表面处理冷轧剪裁板所在侧面的厚侧面,厚度最小的表面处理冷轧剪裁板所在侧面为薄侧面,在各级成型冷轧板的堆叠过程中,厚侧面与薄侧面相连接;
58.(7)将七级成型冷轧板在400℃条件下保温180min进行热处理;高强度高塑性铝合金板材的屈服强度为155mpa,抗拉强度为168mpa,维氏硬度为98hv;高强度高塑性铝合金板材的中部晶粒粒径为1.2~15μm;表面的晶粒粒径为15~30μm。
59.实施例4
60.方法同实施例1,不同点在于:
61.(1)退火板侧面尺寸为500mm
×
250mm;对退火板进行表面处理;
62.(2)将退火板、第一表面处理冷轧剪裁板、第二表面处理冷轧剪裁板和第三表面处理冷轧剪裁板按梯度方式堆叠,构成组合坯;组合坯的两个侧面为退火板,有两个侧面向中部依次为第一表面处理冷轧剪裁板、第二表面处理冷轧剪裁板和第三表面处理冷轧剪裁板;组合坯由2个退火板和5个表面处理冷轧剪裁板构成;
63.(3)成型冷轧的总压下率为80%,制成一级成型冷轧板,厚度2.9mm;
64.(4)按总压下率80%,重复进行叠放+成型冷轧,直至形成三级成型冷轧板;
65.(7)将三级成型冷轧板在350℃条件下保温180min进行热处理;高强度高塑性铝合金板材的屈服强度为124mpa,抗拉强度为172mpa,维氏硬度为95hv;高强度高塑性铝合金板材的中部晶粒粒径为0.8~1.9μm;表面的晶粒粒径为16~28μm。