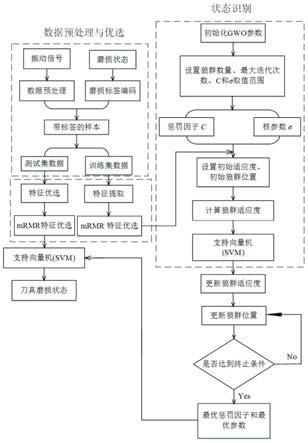
1.本发明属于拉刀磨损状态识别技术领域,具体涉及一种拉刀磨损状态识别模型建立方法。
背景技术:2.拉削是一种高效、高精的一次成形机械加工作业类型,可以完成复杂形状快速切削。被广泛地应用于燃气轮机、汽车制动钳支架和航空发动机轮盘榫槽等关键零部件的加工。拉削的刀具叫拉刀,作为切削加工中的关键部分,拉刀能加工复杂轮廓且具有很高的精度,对其状态识别是确保工件加工精度和机床安全的关键因素。
3.刀具磨损状态监测方法主要分为两类:直接监测法和间接监测法;直接监测法受到的环境干扰较大和所需的成本较高;间接监测法的刀具状态识别方法主要是对刀具磨损相关的信号数据(切削力、振动、声发射等)进行采集并进行分析处理然后采用机器学习(svm、神经网络等)、深度学习等方法预测刀具磨损状态。目前svm方法在刀具状态识别中得到较好使用,但是在提取刀具表面磨损的特征的过程中,会产生较大的冗余和较高的相似性,使得特征矩阵具有较高的维度,这在很大程度上降低了模型的精确度和消耗了计算时长;此外,svm模型的识别精度性能很大程度上依赖于学习算法的参数。
技术实现要素:4.针对现有技术中存在的上述问题,本发明的目的在于提供一种使得提取的特征拥有最小冗余和最大相关性,并提高模型识别精度的拉刀磨损状态识别模型的建立方法。
5.本发明提供如下技术方案:一种拉刀磨损状态识别模型建立方法,其特征在于:包括以下步骤:
6.1)、通过加工过程中的拉刀性能试验,采集刀具有效生命周期过程原始的振动信号和对应的刀具磨损状态,采集原始振动信号过程中,对采集的振动信号进行小波包阈值降噪处理并对刀具磨损状态进行标签编码;
7.2)、将步骤1)中磨损状态标签编码后的振动信号数据随机分为测试集及训练集,分别对测试集及训练集中振动信号进行特征提取,并经过mrmr特征优选,移除相关性高和冗余大的提特征,进行降维处理;
8.3)、建立gwo
‑
svm模型,将步骤2)中经过降维处理的训练集振动信号输入gwo
‑
svm模型中进行训练,保存训练后的模型结构及参数;
9.4)、将步骤2)中经过降维处理的测试集振动信号输入步骤3)中训练好的gwo
‑
svm模型,验证模型的识别精度。
10.所述的一种拉刀磨损状态识别模型建立方法,其特征在于所述步骤1)中,刀具磨损状态包括初期磨损、正常磨损和剧烈磨损三个磨损状态。
11.所述的一种拉刀磨损状态识别模型的建模方法,其特征在于刀具磨损量为0
‑
0.05mm时,记为初期磨损状态,标签为1、刀具磨损量为0.05
‑
0.2mm时,记为正常磨损状态,
标签为2、刀具磨损量为大于0.2
‑
mm时,记为剧烈磨损状态,标签为3。
12.所述的一种拉刀磨损状态识别模型建立方法,其特征在于所述刀具磨损量记录过程如下:记录拉刀刀齿后刀面在粗加工、半精加工及精加工状态下的磨损值,并将三个加工状态下记录的磨损值取平均,该平均值记为拉刀的当前磨损值。
13.所述的一种拉刀磨损状态识别模型建立方法,其特征在于所述步骤1)中,小波包阈值降噪处理的具体过程如下:
14.s1、择小波基函数并确定分解层次,对原始的振动信号进行小波包分解得到小波系数;
15.s2、确定小波包变换阈值估计方法,对小波包分解系数进行阈值量化,得到有效小波系数;
16.s3、利用逆变换可以对有效小波系数进行重构,达到降噪的目的。
17.所述的一种拉刀磨损状态识别模型建立方法,其特征在于所述步骤2)中,测试集及训练集中提取的特征包括时域、频域和时频域特征。
18.所述的一种拉刀磨损状态识别模型建立方法,其特征在于所述时域特征包括均值、均方根、方差、峰差、峭度、峰值因子、脉冲因子和裕度因子八个信号特征;所述频域特征包括重心频率、频率方差和均方频率三个频域信号特征。
19.所述的一种拉刀磨损状态识别模型建立方法,其特征在于所述时频域特征的提取过程如下:
20.通过小波包变换的方法,对采集到的振动信号进行三层小波包分解重构,得到八个不同频段的时序信号,所述时序信号作为时频域特征。
21.所述的一种拉刀磨损状态识别模型建立方法,其特征在于所述步骤3)中,gwo
‑
svm模型的训练过程如下:
22.3.1、设置gwo参数狼群数量和最大迭代次数,将svm的惩罚参数c和核参数作为狼群位置的坐标,随机初始化惩罚参数c和核参数。
23.3.2、利用训练集寻找svm的最优参数,gwo的适应度选择状态分类精度作为指标,并根据适应度对狼群进行位置更新。
24.3.3、狼群经过逐渐缩小搜索空间靠近猎物,计算并更新狼群的适应度,包围猎物并更新位置,使狼群逐渐搜索到全局变量最优或最大迭代次数时,得到最优的惩罚参数c和核参数。
25.3.4、利用最优惩罚参数c和核参数训练svm,保存模型结构和参数。
26.通过采用上述技术,与现有技术相比,本发明的有益效果如下:
27.本发明是一种基于最大相关最小冗余和灰度振动信号特征间接识别的拉削刀具磨损状态识别方法。在拉削加工过程中实时采集拉刀振动信号,通过信号处理技术提取信号时域、频域和时频域特征,建立mrmr
‑
gwo
‑
svm拉削刀磨损状态识别模型;采用最小冗余最大相关方法mrmr进行数据降维,解决高维空间中支持向量机分类困难和参数选择依赖先验知识的问题,采用灰狼优化算法gwo参数寻优,提高支持向量机svm的识别精度;本发明模型能够准确地反映刀具磨损状态,在提高状态识别精度和减少参数寻优时间上具有更好的有效性和可行性。
附图说明
28.图1为本发明模型的拉刀磨损状态识别流程图;
29.图2为本发明实施例最优特征个数与分类精度示意图;
30.图3为本发明实施例中,经mrmr特征优选后前10个最优特征随拉刀磨损的变化趋势示意图,其中,图(a)为x方向频率方差,图(b)为y方向均方根,图(c)为x方向均方根,图(d)为y方向脉冲因子,图(e)为x方向重心频率,图(f)为y方向重心频率,图(g)为x方向小波第二频带分量,图(h)为z方向均方根,图(i)为z方向峭度,图(j)为x方向小波第八频带分量;
31.图4为本发明中,利用测试集评估gwo
‑
svm模型在mrmr特征优选后的特征的拉刀磨损状态分类结果示意图;
32.图5为完备特征下的拉刀磨损状态分类结果示意图;
33.图6为本发明实施例中,gwo
‑
svm模型在mrmr特征优选下的识别结果混淆矩阵图;
34.图7为本发明实施例中,gwo
‑
svm模型在完备特征下的识别结果混淆矩阵图;
35.图8为本发明实施例中,经过mrmr特征优选条件下,gwo
‑
svm模型在分类精度上与pso
‑
svm、ga
‑
svm模型的分类精度性能对比图;
36.图9为本发明实施例中,经过mrmr特征优选条件下,gwo
‑
svm模型在分类精度上与pso
‑
svm、ga
‑
svm模型的寻优时间性能对比图。
具体实施方式
37.为了使本发明的目的、技术方案及优点更加清楚明白,以下结合说明书附图及实施例,对本发明进行进一步详细说明。应当理解,此处所描述的具体实施例仅仅用以解释本发明,并不用于限定本发明。
38.相反,本发明涵盖任何由权利要求定义的在本发明的精髓和范围上做的替代、修改、等效方法以及方案。进一步,为了使公众对本发明有更好的了解,在下文对本发明的细节描述中,详尽描述了一些特定的细节部分。对本领域技术人员来说没有这些细节部分的描述也可以完全理解本发明。
39.实施例:
40.请参阅图1
‑
9,一种拉刀磨损状态识别模型建立方法,具体步骤如下:
41.步骤1、信号采集和处理:
42.本实施例选用lg6516zx
‑
2800高速卧式榫槽拉床、pcb333b30加速度传感器(量程:
±
50g,灵敏度:(
±
10%)100mv/g)、lmsscadasiii
‑
305采集卡(采样频率为3.2khz)、计算机(dell/m90)、超景深显微镜等设备搭建实验平台,采用超景深显微镜测量刀具磨损情况,记录拉刀三个刀齿后刀面(粗、半精、精加工第一个刀齿后刀面)磨损的平均值,并将该磨损均值作为刀具的当前磨损量,对刀具磨损状态进行分类。
43.本实施例中使用的刀具为涂层硬质合金拉刀,工件为某型号飞机涡轮盘,材料为高温镍基粉末合金fh97,所用的切削参数为:主电机功率为51kw,额定拉削力为160kn,进给速度f=4m/min。每次走刀结束,将拉刀从拉床上取下通过显微镜观察后刀面,对其拍照并测量和记录刀具后刀面磨损值。数据采集卡的通信方式为同轴电缆,加速度传感器按照x、y、z三个方向粘附在拉床刀盒上,用于能够实时采集拉刀在加工过程中不同方向的加速度
信号。
44.进行790组拉削加工后,得到拉刀后刀面磨损数据,由于大量的数据不经过处理就输入到模型中去进行预测会消耗大量运算时间,且工业生产现场存在着各种干扰因素,采集到的信号中存在拉刀结构振动、背景振动等干扰信息,影响后续的刀具磨损状态识别精度,所以需要对数据进行预处理。数据预处理主要是对提取的振动信号数据进行小波包阈值降噪,其一般分为三个步骤:1、选择小波基函数并确定分解层次,小波包分解得到小波系数;2、确定小波包变换阈值估计方法,对小波包分解系数进行阈值量化;3、利用逆变换可以对小波包系数进行重构,达到降噪的目的。
45.试验对拉刀磨损状态的划分以后刀面vb区作为刀具磨损测量标准。根据刀具磨损过程并结合试验情况,在后刀面磨损量为0~0.05mm时,该阶段为初期磨损阶段;在后刀面磨损量为0.05~0.2mm时,该阶段为中期磨损阶段;在后刀面磨损量大于0.2mm时,该阶段为剧烈磨损阶段,此时刀具快速磨损,迅速达到失效状态。拉刀拉削工件一次记为一个拉削行程,拉刀磨损状态经历了初期磨损阶段到剧烈磨损阶段的过程,并将初期磨损阶段记为第一类,标签为1,中期磨损阶段记为第二类,标签为2,剧烈磨损阶段记为第三类,标签为3。
46.步骤2、将步骤1)中磨损状态标签编码后的振动信号数据随机分为测试集及训练集,分别对测试集及训练集中振动信号进行特征提取,并经过mrmr特征优选,移除相关性高和冗余大的提特征,进行降维处理。具体过程如下:
47.提取三个方向的时域、频域、时频域,即均值、均方根、方差、峰差、峭度、峰值因子、脉冲因子和裕度因子8个时域信号特征,重心频率、频率方差和均方频率3个频域信号特征,以及采用db9小波包进行3层分解提取的[a
31
,d
31
,a
32
,d
32
,a
33
,a
33
,a
34
,d
34
]8个小波特征。如下表表1所示:
[0048]
表1时域、频域、时频域的统计参数和表达式
[0049][0050][0051]
(续表1)
[0052][0053]
经小波包阈值降噪处理后的拉刀磨损表征信号特征提取,共得到57个特征,其中三个方向振动信号的时域特征24个,频域特征9个、小波包三层分解的小波能量特征24个,并将790组不同磨损状态下的数据样本中的632组作为训练数据,158组作为测试数据。为了避免信息冗余,以减少gwo
‑
svm模型的输入特征,采用mrmr对数据信号特征进行优选。
[0054]
步骤3:建立gwo
‑
svm模型,将步骤2)中经过降维处理的训练集振动信号输入gwo
‑
svm模型中进行训练,保存训练后的模型结构及参数,步骤如下:
[0055]
3.1、设置gwo参数狼群数量和最大迭代次数,将svm的惩罚参数c和核参数作为狼群位置的坐标,随机初始化惩罚参数c和核参数 。
[0056]
3.2、利用训练集寻找svm的最优参数,gwo的适应度选择状态分类精度作为指标,并根据适应度对狼群进行位置更新。
[0057]
3.3、狼群经过逐渐缩小搜索空间靠近猎物,计算并更新狼群的适应度,包围猎物并更新位置,使狼群逐渐搜索到全局变量最优或最大迭代次数时,得到最优的惩罚参数c和核参数。
[0058]
3.4、利用最优惩罚参数c和核参数训练svm,保存模型结构和参数。
[0059]
具体过程如下:
[0060]
刀具磨损的振动信号数据十分复杂,在经时域、频域和时频域57维特征中,一定存在相关特征、无关特征和冗余特征。若不进行特征优选,将表征矩阵直接输入到决策模型中,会导致决策模型诊断精度低、泛化性能差。因此,特征优选是拉刀磨损状态识别不可或缺的一项工作。将特征矩阵输入到mrmr中,查看前20维特征的分类精度如图2所示。
[0061]
由图2可知,经过mrmr计算得前11个最优特征能较好地体现特征与类别之间的相关性,并最小化特征之间的冗余性,达到最好的分类精度。若继续增加特征,存在特征与类别之间相关性变差和特征之间冗余,并不能进一步提升分类精度,甚至会降低分类精度。因此挑选前11个最优特征作为拉刀磨损表征特征,如表2所示。
[0062]
表2最优特征
[0063][0064]
图3展示了经mrmr特征优选后前10个最优特征随拉刀磨损的变化趋势。前10维的特征随着拉刀磨损都呈现逐渐增加的趋势,但x方向频率方差相对于y方向小波第八频带分量的特征值变化趋势更加明显,更能反映拉刀磨损的变化。前5维的特征能较好的展现特征与类别之间的相关性,但存在异常组难以区分。后5维的特征与类别的相关性较弱,没有明显的界限区分拉刀的磨损状态。因此,需要采用状态识别方法建立特征与类别之间的映射关系,从而对拉刀的磨损状态进行准确地识别。
[0065]
按照步骤3.1
‑
步骤3.4的gwo
‑
svm寻优过程,svm利用mrmr特征优选后的训练集、测试集和通过gwo算法寻找到最佳参数c和来识别后刀面的磨损标签,其中特征优选后的训练集识别模型,测试集检验模型的识别精度。
[0066]
本实施例在pythton环境中使用sklearn软件库对刀具磨损状态进行分类,并采用应用广泛且模式识别效果较好的径向基rbf函数作为核svm的核函数。根据试错法和经验法,确定gwo
‑
svm模型的超参数选择范围,如表3所示。
[0067]
表3 gwo
‑
svm模型训练过程的具体参数
[0068][0069]
在训练过程中,为避免模型过拟合,采用5
‑
折交叉验证计算模型训练精度,获得gwo
‑
svm模型在mrmr特征优选后和完备特征下的最优核参数和惩罚参数分别为=0.32、=196.29和=86.04、=254.32。利用测试集评估gwo
‑
svm模型在mrmr特征优选后的特征和完备特征下的拉刀磨损状态分类结果,如图4、5所示。经过mrmr特征优选后的特征,拉刀磨损状态能够更为准确地分类,gwo
‑
svm模型识别准确率提高到了6.33%。
[0070]
图6、7为gwo
‑
svm模型在mrmr特征优选(11维)和完备特征下的识别结果混淆矩阵图。结果表明经过特征优选后gwo
‑
svm模型在三种拉刀磨损状态下识别准确率分别提升1.5%、2.5%、1.8%。由此可得,将拉刀磨损表征信号特征通过mrmr特征优选后,将特征中大量冗余特征和不相关特征剔除,降低了特征空间的维度,有效地提高模型的识别精度。
[0071]
步骤4、mrmr
‑
gwo
‑
svm模型与其他模型性能对比:
[0072]
为了揭示gwo
‑
svm算法寻优能力和识别能力,构建pso
‑
svm和ga
‑
svm模型实现拉刀
磨损状态识别与gwo
‑
svm模型进行对比。三个模型的参数设置如表4所示。
[0073]
表4优化算法中的具体参数
[0074][0075]
采用gwo、pso、ga对svm核函数中的超参数进行寻优,以错误率最小化为目标,采用5折交叉验证,用5次测试结果的平均值作为迭代过程中拉刀磨损状态识别的精度指标。为了比较三种优化算法对svm分类模型的性能,对分类精度和寻优时间两个指标进行研究。从图7、8中可得,对比无特征优选和mrmr特征优选可知,三个模型的分类精度都有所提升,且寻优时间减少。经过mrmr特征优选条件下,gwo
‑
svm模型在分类精度上优于pso
‑
svm和ga
‑
svm模型,且在寻优时间上分别比pso
‑
svm和ga
‑
svm模型减少了54.2%和60.5%。
[0076]
上述结果表明,经过mrmr特征优选后的gwo
‑
svm模型可以精确地识别拉刀磨损状态,分类精度达到96.84%。
[0077]
以上所述仅为本发明的较佳实施例而已,并不用以限制本发明,凡在本发明的精神和原则之内所作的任何修改、等同替换和改进等,均应包含在本发明的保护范围之内。