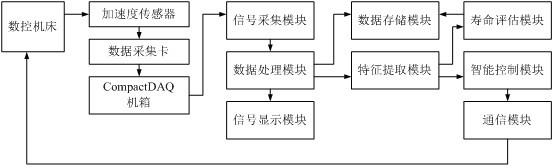
一种基于机床振动信号的刀具状态监测系统及方法
1.技术领域
2.本发明属于数控机床智能控制技术领域,涉及一种基于机床振动信号的刀具状态监测系统及方法。
背景技术:3.切削加工是最常用的机械加工方法,因此切削刀具在加工中的作用显得尤其重要,它的使用寿命对机械产品的生产质量产生直接影响,从而影响生产制造技术水准和经济效益。刀具严重磨损可引起刀具的破坏,刀具的破坏会导致工件报废同时会损伤昂贵的设备,更严重的后果是会影响机床的正常使用及操作者的人身安全。对刀具磨损情况的实时监测有助于提高加工环境的稳定性和工件的质量,保障机床及加工人员安全,同时还能提高企业的生产效率、减低生产成本。因此,发展刀具状态监测技术十分必要。
4.刀具磨损的主要特征是机器伴有异常的振动和噪声,考虑到机床工作环境通常比较嘈杂,因此通过对机床振动信号的监测来判断机床的实际运行状态是最有效的手段。专利号为cn201420471749.x的一种机床振动在线监控系统仅能实现主轴振动的预警功能,功能单一。专利号为cn201320505108.7的一种机床的振动传感监测装置以及专利号为cn201120096755.8的一种机床运行监测系统均是振动采集系统,不具备数据分析且无法与机床进行交互。
技术实现要素:5.为解决上述技术问题,本发明的目的是提供一种基于机床振动信号的刀具状态监测系统及方法,可对机床加工中的振动状态进行实时监控评估刀具磨损情况,并根据振动状态优化机床切削加工参数,达到延长刀具寿命及故障预警的目的。
6.本发明提供一种基于机床振动信号的刀具状态监测系统,包括:上位机控制模块和数据采集模块;所述数据采集模块用于采集数控机床主轴的振动信号并发送给上位机控制模块;上位机控制模块根据振动信号判断刀具磨损情况和使用寿命并优化切削加工参数;所述上位机控制模块通过网线和数控机床控制系统相连,数控机床控制系统根据优化的切削加工参数进行机加工;所述数据采集模块包括:加速度传感器、数据采集卡和compactdaq机箱;加速度传感器用于采集数控机床主轴的振动信号并与数据采集卡相连;数据采集卡通过卡槽与compactdaq机箱相连,数据采集卡对采集的振动信号进行ad转换处理,compactdaq机箱通过usb数据线将ad转换处理后的振动信号发送给上位机控制模块;所述上位机控制模块包括:信号采集模块、数据处理模块、数据存储模块、信号显示模块、特征提取模块、智能控制模块、寿命评估模块和通信模块;所述信号采集模块接收
ad转换处理后的振动信号并发送给数据处理模块,数据处理模块对振动信号进行频域积分获得振动曲线后通过信号显示模块进行显示,并传输到数据存储模块进行记录,数据处理模块同时将振动曲线传输给特征提取模块;所述特征提取模块将振动曲线与标准特征值曲线进行对比判定是否发生故障并更换刀具,将对比结果传输给寿命评估模块和智能控制模块;所述寿命评估模块根据振动磨损数学模型和振动曲线计算刀具磨损情况;所述智能控制模块根据刀具磨损情况优化切削加工参数;所述通信模块与智能控制模块连接,使用opcua协议与数控机床控制系统进行通讯,传输优化后的切削加工参数。
7.在本发明的基于机床振动信号的刀具状态监测系统中:所述上位机控制模块还包括:参数设置模块和连接模块,所述参数设置模块用于进行数据采集参数设置、通讯通道设置;所述连接模块用于进行硬件连接调试、数据采集调试以及上位机控制模块与数控机床控制系统的双向通讯的调试。
8.本发明提供一种基于机床振动信号的刀具状态监测方法,其特征在于,包括:步骤1:采集数控机床主轴的振动信号并对振动信号进行ad转换处理;步骤2:对ad转换处理后的振动信号进行频域积分处理获得振动曲线,将获得的振动曲线进行存储和显示;步骤3:将振动曲线与标准特征值曲线进行对比,判断是否发生故障并更换刀具以及是否处于正常加工状态;标准特征值曲线为两条,一条是新刀振动曲线,用于表征振动信号的最小值;一条是磨损刀具振动曲线,用于表征振动信号的最大值,当振动曲线超过磨损刀具振动曲线时,判定需要换刀;步骤4:根据振动磨损数学模型和振动曲线计算刀具磨损情况,进而评估刀具寿命;步骤5:根据刀具磨损情况,优化切削加工参数。
9.在本发明的基于机床振动信号的刀具状态监测方法中:所述步骤1中通过加速度传感器采集机床主轴的振动信号,即加速度信号。
10.在本发明的基于机床振动信号的刀具状态监测方法中:所述步骤1中每秒采集多个加速度信号,步骤2中经频域积分处理后并取有效数值获得一个振动数据,数控机床工作预定时间后即获得多个振动数据,多个振动数据构成一条振动曲线。
11.在本发明的基于机床振动信号的刀具状态监测方法中:所述步骤4中通过历史振动信号和刀具磨损情况的映射关系建立振动磨损数学模型。
12.在本发明的基于机床振动信号的刀具状态监测方法中:所述步骤5中根据刀具磨损情况优化切削加工参数,包括主轴转速、进给速度和切深。
13.本发明的一种基于机床振动信号的刀具状态监测系统及方法,通过采集数控机床主轴振动信号从时域、频域、幅值等多个角度反映了机床的故障信息。基于振动信号的刀具状态监测系统在加工过程中实时监测机床主轴的振动信号,智能判断刀具磨损情况,并依据刀具磨损情况给出换刀预警,实现刀具运维无人化和预测化,有效避免刀具因过度磨损影响加工精度或更换过勤,浪费资源。通过opcua协议与数控机床控制系统进行通讯,在加工过程中对数控机床切削加工参数进行自适应优化,进而避免机床误操作,提升加工质量,降低人工成本,减少刀具磨损,实现安全生产,同时实现方式比较便捷。
附图说明
14.图1是本发明的一种基于机床振动信号的刀具状态监测系统的框图;图2是本发明的一种基于机床振动信号的刀具状态监测方法的流程图。
具体实施方式
15.如图1所示,本发明一种基于机床振动信号的刀具状态监测系统,包括:上位机控制模块和数据采集模块;所述数据采集模块用于采集数控机床主轴的振动信号并发送给上位机控制模块;上位机控制模块根据振动信号判断刀具磨损情况和使用寿命并优化切削加工参数;所述上位机控制模块通过网线和数控机床控制系统相连,数控机床控制系统根据优化的切削加工参数进行机加工。
16.所述数据采集模块包括:加速度传感器、数据采集卡和compactdaq机箱;加速度传感器用于采集数控机床主轴的振动信号并与数据采集卡相连;数据采集卡通过卡槽与compactdaq机箱相连,数据采集卡对采集的振动信号进行ad转换处理,compactdaq机箱通过usb数据线将ad转换处理后的振动信号发送给上位机控制模块。
17.所述上位机控制模块包括:信号采集模块、数据处理模块、数据存储模块、信号显示模块、特征提取模块、智能控制模块、寿命评估模块和通信模块;所述信号采集模块接收ad转换处理后的振动信号并发送给数据处理模块,数据处理模块对振动信号进行频域积分获得振动曲线后通过信号显示模块进行显示,并传输到数据存储模块进行记录,数据处理模块同时将振动曲线传输给特征提取模块;所述特征提取模块将振动曲线与标准特征值曲线进行对比判定是否发生故障并更换刀具,将对比结果传输给寿命评估模块和智能控制模块;所述寿命评估模块根据振动磨损数学模型和振动曲线计算刀具磨损情况;所述智能控制模块根据刀具磨损情况优化切削加工参数;所述通信模块与智能控制模块连接,使用opcua协议与数控机床控制系统进行通讯,传输优化后的切削加工参数。
18.所述上位机控制模块还包括:参数设置模块和连接模块,所述参数设置模块用于进行数据采集参数设置、通讯通道设置;所述连接模块用于进行硬件连接调试、数据采集调试以及上位机控制模块与数控机床控制系统的双向通讯的调试。
19.具体实施时,compactdaq机箱的型号为ni cdaq-9178,数据采集卡的型号为ni9234,采用b&k的加速度传感器型号为4528 b001。
20.如图2所示,本发明的一种基于机床振动信号的刀具状态监测方法,包括:步骤1:采集数控机床主轴的振动信号并对振动信号进行ad转换处理;具体实施时,通过加速度传感器采集数控机床主轴的振动信号,即加速度信号。
21.步骤2:对ad转换处理后的振动信号进行频域积分处理获得振动曲线,将获得的振动曲线进行存储和显示;具体实施时,每秒采集多个加速度信号,经频域积分处理后并取有效数值获得一个振动数据,数控机床工作预定时间后即获得多个振动数据,多个振动数据构成一条振动曲线。
22.步骤3:将振动曲线与标准特征值曲线进行对比,判断是否需要更换刀具以及是否处于正常加工状态;具体实施时,标准特征值曲线为两条,一条是新刀振动曲线,用于表征振动信号的
最小值;一条是磨损刀具振动曲线,用于表征振动信号的最大值,当振动曲线超过磨损刀具振动曲线时,就判定需要换刀。
23.步骤4:根据振动磨损数学模型和振动曲线计算刀具磨损情况,进而评估刀具寿命;具体实施时,通过历史振动信号和刀具磨损情况的映射关系建立振动磨损数学模型。
24.步骤5:根据刀具磨损情况,优化切削加工参数。
25.具体实施时,根据刀具磨损情况优化切削加工参数,切削加工参数包括主轴转速、进给速度和切深等,随着振动的增大,逐步降低切削参数,采用较保守的切削方案。例如振动速度增加到原来的110%以内时,认为刀具还比较锋利,切削参数不作调整;振动速度增加到110%-120%之间时,认为刀具已有了较明显的磨损,需要适当降低主轴转速、进给速度、切深等,比如降到原来的90%以避免较大的振动损伤刀具;振动速度有效值增加到120%以上时,认为刀具磨损进一步加剧,此时需采用更保守的切削方案,以保证切削时的振动状态比较稳定。参数的具体优化方案需要根据现场加工情况、加工工件材料等的不同并结合切削试验作适应性调整。
26.本发明的监测系统具有以下工作模式:模式一:机床振动状态监测:使用到的模块:数据采集模块及上位机控制模块中的参数设置模块、信号采集模块、数据处理模块、信号显示模块和数据存储模块。
27.连接方式:加速度传感器吸附于主轴附近,通过信号线与数据采集卡相连,数据采集卡通过卡槽与compactdaq机箱相连,compactdaq机箱通过usb数据线与上位机控制模块相连。
28.实施过程:加速度传感器采集主轴的加速度信号,数据采集卡采集加速度信号并进行ad转换处理,经由数据处理模块处理后获得振动曲线由信号显示模块进行显示,并传输入数据存储模块进行记录。模式一用于实时监测机床振动状态。
29.模式二:刀具寿命监测:使用到的模块:数据采集模块及上位机控制模块中的参数设置模块、信号采集模块、数据处理模块、信号显示模块、数据存储模块、特征提取模块、寿命评估模块。
30.连接方式:加速度传感器吸附于主轴附近,通过信号线与数据采集卡相连,数据采集卡通过卡槽与compactdaq机箱相连,compactdaq机箱通过usb数据线与上位机控制模块相连。
31.实施过程:加速度传感器采集主轴的加速度信号,数据采集卡采集加速度信号并进行ad转换处理,经由数据处理模块处理后获得振动曲线,将振动曲线与标准特征值曲线作比对判定是否需要换刀以及是否处于正常加工状态,寿命评估模块中根据振动磨损数学模型和振动曲线计算刀具磨损情况及其预期寿命并显示结果。
32.模式三:刀具状态监测及智能控制:使用到的模块:数据采集模块及上位机控制模块中的参数设置模块、信号采集模块、数据处理模块、信号显示模块、数据存储模块、特征提取模块、智能控制模块和通讯模块。
33.连接方式:加速度传感器吸附于主轴附近,通过信号线与数据采集卡相连,数据采集卡通过卡槽与compactdaq机箱相连,compactdaq机箱通过usb数据线与上位机控制模块相连,上位机控制模块通过网线和数控机床控制系统相连。
34.实施过程:加速度传感器采集主轴的加速度信号,数据采集卡采集加速度信号并进行ad转换处理,数据处理模块进行数据处理后获得振动曲线并传输给特征提取模块,将振动曲线和标准特征值曲线作比对判定是否需要换刀,寿命评估模块中根据振动磨损数学模型和振动曲线计算刀具磨损情况;智能控制模块根据刀具磨损情况,优化切削加工参数,通过opcua协议与数控机床控制系统进行交互,对机床主轴及进给系统进行自适应控制调整,实现对机床加工状态的智能控制。
35.本系统通过opcua协议与数控机床控制系统进行通讯,无需单片机或继电器模组等额外硬件,无需修改plc程序,仅需要一根网线和数控机床控制系统进行连接,同时数控机床控制系统内开通对应的opcua协议即可实现与数控机床控制系统的双向通讯,实现对机床主轴及进给系统的动态控制,操作简单明了、通用性强,学习成本低,研究成果易于向生产的转化。
36.通过加速度传感器采集机床主轴振动信号传入数据采集卡,进行ad转换处理后传入上位机控制模块,上位机控制模块将采集数据与离线学习的标准特征值曲线比对后,做出智能判断,并通过opcua协议向数控机床控制系统发送指令,从而实现对机床切削加工参数的智能优化;同时也可根据振动变化状态,判断刀具的磨损情况。
37.以上所述仅为本发明的较佳实施例,并不用以限制本发明的思想,凡在本发明的精神和原则之内,所作的任何修改、等同替换、改进等,均应包含在本发明的保护范围之内。