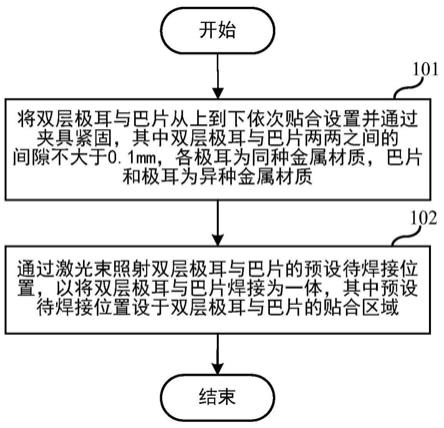
1.本技术涉及焊接技术领域,尤其涉及双层极耳与巴片的激光焊接方法、激光焊接装置及锂电池。
背景技术:2.激光焊接是利用高能量密度的激光束作为热源的一种高效高精密的焊接方法。激光焊接过程属热传导型,即激光辐射加热工件表面,表面热量通过热传导向内部扩散。通过控制激光脉冲的宽度、能量、峰值功率和重复频率等参数,使工件熔化,形成特定的熔池。激光焊接的原理可分为热传导型和深熔焊接。功率密度小于104
‑
105w/cm2时为热传导焊接,此时熔深浅,焊接速度慢。功率密度大于105
‑
107w/cm2时,金属表面受热作用下凹成“匙孔”,形成深熔焊。
3.在锂电池生产领域中,相邻的极耳之间的可靠连接对整个锂电池制造工艺的安全可靠性起到极其关键的作用。一般情况下,相邻的两个极耳通过巴片连接,以实现相邻电芯的串联。传统相邻的两个极耳之间的连接只能是:两个铝极耳分别与铝巴片焊接、两个铜极耳分别与铜巴片焊接。这种对极耳和巴片的材质的限制,使得电池在结构设计方面极其复杂,制造加工难度大,生产成本高。
技术实现要素:4.本技术的目的在于提供一种双层极耳与巴片的激光焊接方法、激光焊接装置及锂电池,本技术实现了双层极耳与异种金属材料的巴片的激光焊接,消除了焊接时对极耳和巴片材质的限制,既保证了焊接质量,提高了企业生产效率,又降低了生产成本。
5.为解决上述技术问题,本技术的第一方面提供了一种双层极耳与巴片的激光焊接方法,包括:将双层极耳与巴片从上到下依次贴合设置并通过夹具紧固,其中所述双层极耳与所述巴片两两之间的间隙不大于0.1mm,各所述极耳为同种金属材质,所述巴片和极耳为异种金属材质;以及通过激光束照射所述双层极耳与所述巴片的预设待焊接位置,以将所述双层极耳与所述巴片焊接为一体,其中所述预设待焊接位置设于所述双层极耳和所述巴片的贴合区域。
6.本技术的第二方面提供了一种双层极耳与巴片的激光焊接装置,包括:光纤激光器;多自由度的机器人手臂,持有所述光纤激光器;控制系统,电性耦接所述光纤激光器及机器人手臂,以控制所述机器人手臂和光纤激光器执行上述的双层极耳与巴片的激光焊接方法。
7.本技术的第三方面提供了一种锂电池,包括:由上述的双层极耳与巴片的焊接方法焊接得到的导电结构。
8.在第一方面的实施例中,所述通过激光束照射所述双层极耳与所述巴片的预设待焊接位置,将所述双层极耳与所述巴片焊接为一体,具体包括:将所述双层极耳与巴片的预设待焊接位置沿纵向分成多段区域;对所述预设待焊接位置的多段区域分别照射不同功率
的激光束,以将所述双层极耳与巴片焊接为一体,其中所述预设待焊接位置设于所述巴片和所述双层极耳的贴合区域。
9.在第一方面的实施例中,通过激光束照射所述双层极耳与所述巴片的预设待焊接位置,以将所述双层极耳与所述巴片焊接为一体之前,还包括:对所述巴片和所述双层极耳的预设待焊接位置进行油污清洗。
10.在第一方面的实施例中,所述激光束为连续波,波长为1064nm,所述激光功率为1400w至1600w,焊接速度为40mm/s至60mm/s,焊接频率为90hz至110hz。
11.在第一方面的实施例中,所述巴片为厚度3mm的铜巴片。
12.在第一方面的实施例中,所述双层极耳为厚度0.4mm的双层铝极耳。
13.在第一方面的实施例中,所述激光束垂直于所述预设待焊接位置的焊接面。
14.在第一方面的实施例中,所述双层极耳与所述巴片两两之间的间隙为0.05mm。
15.本技术实施例相对于现有技术而言,本技术实现了双层极耳与异种金属材料的巴片的激光自动化焊接,既保证了焊接质量,提高了企业生产效率,又降低了生产成本。
附图说明
16.图1显示为本技术第一实施例中双层极耳与巴片的激光焊接方法的流程示意图;
17.图2显示为本技术实施例中双层极耳与巴片贴合的侧视图;
18.图3显示为本技术第二实施例中双层极耳与巴片的激光焊接方法的流程示意图;
19.图4显示为本技术实施例中双层极耳与巴片贴合的俯视图;
20.图5显示为本技术第三实施例中双层极耳与巴片的激光焊接方法的流程示意图。
具体实施方式
21.以下通过特定的具体实例说明本技术的实施方式,本领域技术人员可由本说明书所揭露的内容轻易地了解本技术的其他优点与功效。本技术还可以通过另外不同的具体实施方式加以实施或应用系统,本说明书中的各项细节也可以基于不同观点与应用系统,在没有背离本技术的精神下进行各种修饰或改变。需说明的是,在不冲突的情况下,本技术中的实施例及实施例中的特征可以相互组合。
22.下面以附图为参考,针对本技术的实施例进行详细说明,以便本技术所属技术领域的技术人员能够容易地实施。本技术可以以多种不同形态体现,并不限定于此处说明的实施例。
23.为了明确说明本技术,省略与说明无关的器件,对于通篇说明书中相同或类似的构成要素,赋予了相同的参照符号。
24.在通篇说明书中,当说某器件与另一器件“连接”时,这不仅包括“直接连接”的情形,也包括在其中间把其它元件置于其间而“间接连接”的情形。另外,当说某种器件“包括”某种构成要素时,只要没有特别相反的记载,则并非将其它构成要素排除在外,而是意味着可以还包括其它构成要素。
25.当说某器件在另一器件“之上”时,这可以是直接在另一器件之上,但也可以在其之间伴随着其它器件。当对照地说某器件“直接”在另一器件“之上”时,其之间不伴随其它器件。
26.虽然在一些实例中术语第一、第二等在本文中用来描述各种元件,但是这些元件不应当被这些术语限制。这些术语仅用来将一个元件与另一个元件进行区分。例如,第一接口及第二接口等描述。再者,如同在本文中所使用的,单数形式“一”、“一个”和“该”旨在也包括复数形式,除非上下文中有相反的指示。应当进一步理解,术语“包含”、“包括”表明存在所述的特征、步骤、操作、元件、组件、项目、种类、和/或组,但不排除一个或多个其他特征、步骤、操作、元件、组件、项目、种类、和/或组的存在、出现或添加。此处使用的术语“或”和“和/或”被解释为包括性的,或意味着任一个或任何组合。因此,“a、b或c”或者“a、b和/或c”意味着“以下任一个:a;b;c;a和b;a和c;b和c;a、b和c”。仅当元件、功能、步骤或操作的组合在某些方式下内在地互相排斥时,才会出现该定义的例外。
27.此处使用的专业术语只用于言及特定实施例,并非意在限定本技术。此处使用的单数形态,只要语句未明确表示出与之相反的意义,那么还包括复数形态。在说明书中使用的“包括”的意义是把特定特性、区域、整数、步骤、作业、要素及/或成份具体化,并非排除其它特性、区域、整数、步骤、作业、要素及/或成份的存在或附加。
28.表示“下”、“上”等相对空间的术语可以为了更容易地说明在附图中图示的一器件相对于另一器件的关系而使用。这种术语是指,不仅是在附图中所指的意义,还包括使用中的装置的其它意义或作业。例如,如果翻转附图中的装置,曾说明为在其它器件“下”的某器件则说明为在其它器件“上”。因此,所谓“下”的示例性术语,全部包括上与下方。装置可以旋转90
°
或其它角度,代表相对空间的术语也据此来解释。
29.虽然未不同地定义,但包括此处使用的技术术语及科学术语,所有术语均具有与本技术所属技术领域的技术人员一般理解的意义相同的意义。普通使用的字典中定义的术语追加解释为具有与相关技术文献和当前提示的内容相符的意义,只要未进行定义,不得过度解释为理想的或非常公式性的意义。
30.图1展示了本技术第一实施例中双层极耳与巴片的激光焊接方法的流程示意图。本技术实施例的激光焊接方法包括步骤101和步骤102。
31.步骤101中,将双层极耳与巴片从上到下依次贴合设置并通过夹具紧固,其中双层极耳与巴片两两之间间隙不大于0.1mm,各极耳为同种金属材质,巴片和极耳为异种金属材质。
32.锂电池结构中双层极耳与巴片通过激光焊接的方式实现连接。具体地,先将双层极耳和巴片依次放置在自动夹具中,从下至上的顺序依次是如图2中所示的巴片10和双层极耳20(第一极耳21和第二极耳22),以此顺序使得巴片10和各极耳间互相贴合并夹紧,并且使得第一极耳21、第二极耳22与巴片10两两之间间隙不大于0.1mm,例如可以是0.05mm、0.06mm、0.08mm或0.1mm,较小的间隙利于提高焊接效果。在本优选实施例中,极耳的材料优选为型号1060纯铝,厚度为0.4mm,巴片优选为型号t2状态紫铜,且表面镀镍,厚度为2mm及以上,例如可以是3mm,下料方式采用线切割的方法成型,保证每个切割面平整无毛刺,以减小巴片与极耳之间的间隙,提高焊接效果。但可理解,各个极耳和巴片的材料和厚度均不局限于上述的型号,此处仅为举例说明。
33.步骤102中,通过激光束照射双层极耳与巴片的预设待焊接位置,以将双层极耳与巴片焊接为一体,其中预设待焊接位置设于双层极耳与巴片的贴合区域。
34.本实施例的激光焊接方法采用光纤激光器为热源,激光束通过光纤激光器产生。
光纤激光焊接是一种高效、污染少的新型高附加值的焊接方式,可以在增强工业自动化能力的同时,也减少了对环境的污染,属于环境友好型的高科技加工方法。具体地,首先将光纤激光焊接头的位置调整到预设待焊接位置的正面位置,整个过程中激光束与预设待焊接位置的角度保持垂直,以保证激光能量最有效地被转化。其中预设待焊接位置在优选实施例中为缝状,且设于双层极耳与巴片的贴合区域内。在焊接时焊接方向从焊缝的左侧开始至右侧结束,焊缝由光纤激光焊接头一次性持续工作完成。
35.以上光纤激光焊接方法的工艺参数为:光纤激光为连续波,波长为1064nm,焊接激光功率1400w
‑
1600w,焊接速度为40mm/s
‑
60mm/s,焊接频率为90hz
‑
110hz。通过选用不同的激光功率进行焊接,获取如表一中所示的不同的激光功率对应的不同熔深。
36.表一 焊缝的不同工艺参数
[0037][0038]
表二 焊缝的最佳工艺参数
[0039][0040]
需要说明的是,通常在焊接过程中需要向焊接位置输送保护气体,以保护焊缝不被氧化。而通过本技术中焊接参数获取的熔深并非深熔,采用上述焊接速度和频率参数,在无保护气的情况下焊接时焊缝不会被氧化,可实现无保护气体形式下的焊接。
[0041]
熔深如果太小会降低焊接质量,导致在外力下焊接位脱落,熔深如果太大也会容易导致焊穿的风险,当拉力测试达到35n以上时焊接达到设计要求,可知表二中双层极耳与巴片在适中的焊接功率下可达到较佳的拉力水平,而且热影响区很小,组织致密,强度符合设计要求。本实施例的双层极耳与巴片的激光焊接方法,与传统焊接方法相比,降低了异种金属焊接时产生的脆性相问题,实现了双层极耳与异种金属材料的巴片的激光焊接,既保证了焊接质量,提高了企业生产效率,有降低了生产成本。
[0042]
本技术的第二实施例涉及一种双层极耳与巴片的激光焊接方法。第二实施例与第一实施例大致相同,主要区别之处在于:在第二实施例中,为达到更好的焊接效果,焊接起始功率、稳定功率、终止功率在焊接过程中发生变化。第二实施例中,如图3所示,步骤102包括子步骤1021和子步骤1022。
[0043]
子步骤1021中,将双层极耳与巴片的预设待焊接位置沿纵向分成多段区域。
[0044]
如图4所示,巴片10和双层极耳20的预设待焊接位置30设于巴片10和双层极耳20的重叠区域内。进行焊接时,激光束与预设待焊接位置的角度保持垂直,在焊接时焊接方向从焊缝的左侧开始至右侧结束,预设待焊接位置沿纵向可分成多段区域,然后再进行焊接操作。具体地,例如可以将预设待焊接位置沿纵向分成起始段、中间段和终止段。在本优选
实施例中,预设待焊接位置沿纵向长度为35mm,可将35mm沿纵向分为起始段0mm
‑
4mm、中间段4mm
‑
32mm和终止段33mm
‑
35mm。但可理解,预设待焊接位置不局限于上述的三段,即起始段、中间段和终止段,也可以是其他数量分段,另外各段也不局限于上述的长度。
[0045]
子步骤1022中,对预设待焊接位置的多段区域分别照射不同功率的激光束,以将双层极耳与巴片焊接为一体,其中预设待焊接位置设于双层极耳与巴片的贴合区域。
[0046]
对子步骤1021的预设待焊接位置的多段区域进行多变功率输出的焊接,以此建立稳定的熔深。具体地,熔深如果太小会降低焊接质量,导致在外力下焊接位脱落,熔深如果太大也会容易导致焊穿的风险。在预设待焊接位置起始段上,金属本身需要进行预热,为了在金属表面形成“匙孔”,需施加一个起始焊接功率,待金属预热并在起始段上建立“匙孔”后,可稍微降低焊接功率,达到一个稳定的热量输出,以对预设待焊接位置的中间段进行焊接,从而获取一个稳定的熔深。焊接到终止段时,可根据此刻熔深情况增加或减少焊接功率,完成终止段的收尾焊接。通过多变焊接功率输出的焊接可达到一个更精准的焊接效果,从而建立一个稳定的熔深,以将双层极耳与巴片焊接为一体的导电结构,达到相应的拉力要求,同时在中间段降低焊接功率,也降低了焊接能量消耗。
[0047]
本技术的第三实施例涉及一种双层极耳与巴片的激光焊接方法。第三实施例与第二实施例大致相同,主要区别之处在于:在本技术第三实施例中,如图5所示,步骤101和步骤102之间还包括步骤1011:对双层极耳与巴片的预设待焊接位置进行油污清洗。具体地说,预设待焊接位置如果存在油污等,在进行焊接时会对激光产生反射,对焊接质量会产生不良影响,通常会对预设待焊接位置提前进行清洗。例如在焊接前将焊缝周围半径50mm内的油污采用酒精清洗干净,这样可以减少其对激光的反射,增加工件对光的吸收率,增加熔深,保证焊接质量
[0048]
本技术的第四实施例涉及一种双层极耳与巴片的激光焊接装置,该焊接装置包括光纤激光器;多自由度的机器人手臂,机器人手臂持有光纤激光器;该装置还包括控制系统,控制系统电性耦接光纤激光器及机器人手臂,以控制机器人手臂和光纤激光器执行上述实施例的双层极耳与巴片的激光焊接方法。该激光焊接装置的光纤激光器安装于机器人手臂,从而使得光纤激光器能够自由移动和旋转,实现自动化控制,提高了焊接效率和焊接精度,同时降低了生产成本。
[0049]
本技术的第五实施例涉及一种锂电池,该锂电池包括由上述实施例的双层极耳与巴片的焊接方法焊接得到的导电结构。由上述焊接方法焊接得到的导电结构的焊接质量较高,成本较低。
[0050]
上述实施例仅例示性说明本技术的原理及其功效,而非用于限制本技术。任何熟悉此技术的人士皆可在不违背本技术的精神及范畴下,对上述实施例进行修饰或改变。因此,举凡所属技术领域中具有通常知识者在未脱离本技术所揭示的精神与技术思想下所完成的一切等效修饰或改变,仍应由本技术的权利要求所涵盖。