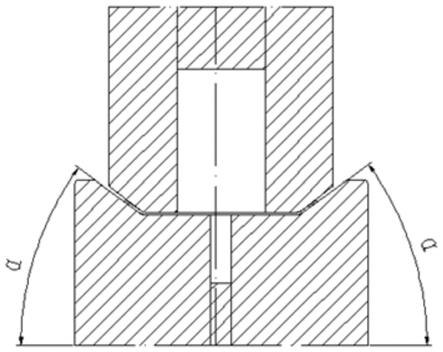
1.本发明涉及冷弯成型技术领域,尤其是涉及一种直角梯形断面钢管的成型方法。
背景技术:2.随着客车车架的不断优化,直角梯形管逐步替代冷弯方矩管拼焊应用于客车车窗框架部位。直角梯形管的生产在国内却为空白,可以肯定的是诸如此类异形断面冷弯产品通过“板料先成圆管,圆管再成异形管”的方法能制造出合格的产品,但该成型工艺需要专用模具,成本投入较大。因此开发一种采用通用性较高的模具成型直角梯形管的方法可以大量节省成本。
3.冷弯型钢产品中方矩管产品约占80%~90%,方矩管产品为断面对称型产品,成型工艺较为成熟。待开发的直角梯形管断面非对称,如果采用“板料先成圆管,圆管再成异形管”的方法进行制造势必会增加模具的投入成本,若采用方矩管成型的直接成型工艺,可以预料到板料变形过程中变形程度不均匀会造成产品出现弯曲、扭转或尺寸无法达标等缺陷。
技术实现要素:4.本发明涉及到的直角梯形管成型方法能有效解决上述两种成型方法带来的不利影响,充分考虑材料各部位变形的均匀性,设计各个成型道次的成型角度,最大程度降低产品成型过程中出现变形等缺陷。经生产实际验证具备批量生产的条件。
5.本发明所采用的技术方案是:
6.一种直角梯形断面钢管的成型方法,具体包括如下步骤:
7.(1)初成型阶段-采用10架次平辊,7架次立辊将板料辊弯成未焊合的断面完成初成型:
8.将原料板带依次通过第一架次平辊、第一架次立辊、第二架次平辊、第二架次立辊、第三架次平辊、第三架次立辊、第四架次平辊、第四架次立辊、第五架次平辊、第五架次立辊、第六架次平辊、第六架次立辊、第七架次平辊、第七架次立辊、第八架次平辊、第九架次平辊、第十架次平辊各架次配置的孔型,将板带经横向弯曲变形成为直角梯形的断面,完成初成型;
9.(2)挤压焊接、外毛刺清除阶段:
10.板料通过初成型形成具有形状的断面后,再经过挤压辊模具,配合高频焊接工艺完成挤压焊接,形成直缝焊管;
11.(3)精成型阶段:
12.通过前述2个步骤形成直缝焊管后,通过5架次标准辊精整将产品尺寸控制在技术要求范围内,完成成型;
13.其中,步骤(1)的具体要求如下:
14.一弯成型:平辊1-3架次成型梯形管上底,根据均匀变形的原则,将上底两边弯角
部位成型角度α按照架次顺序分别设计为22
°
、45
°
、68
°
,上底两边弯角部位成型角度对称;
15.二弯成型:平辊4-7架次成型梯形管腰部,成型角度β按4-7架次顺序分别设计为16
°
、32
°
、48
°
、64
°
,两腰部弯角处成型角度对称;
16.一弯成型和二弯成型均采用平辊和立辊交替方式进行,在各架次平辊结束后,分别利用第1-7架次立辊对板料横向约束,避免偏心,立辊成型角度ω按1-7架次顺序依次设计为33
°
、56
°
、8
°
、24
°
、40
°
、56
°
、72
°
;
17.封闭辊成型:平辊8-10架次对整体形状进行控制,腰部直角边成型角度λ按架次顺序依次设计为80
°
、80
°
、86
°
,腰部斜边成型角度μ按架次顺序分别设计为82
°
、90
°
、97
°
,直角焊接小边成型角度σ按架次顺序分别设计为80
°
、80
°
、86
°
,钝角焊接小边成型角度τ按架次顺序分别设计为74
°
、74
°
、77
°
,确保产品进入下一阶段的挤压焊接能满足工艺参数,顺利完成焊接。
18.进一步的,所述步骤(2)具体操作为:
19.采用四辊挤压的方式对初成型后的板料断面进行挤压,以板-板对接的方式对上底中间的焊合处进行挤压,在高频感应电流的作用下完成焊接,在毛刺刀片的作用下,梯形管焊接外毛刺在高温状态下被清除,梯形管内部毛刺予以保留。
20.进一步的,所述步骤(3)具体操作为:
21.采用5架次四辊对产品断面进行精整,每架次四辊均配置有与梯形管断面形状相匹配的孔型,精整过程中使用相对两辊间的间隙逐架次均匀递减的方法对断面各边长进行控制,确保产品通过所有架次后外观尺寸满足技术要求。
22.本发明上述技术方案的有益效果如下:
23.开发了一套直角梯形断面钢管的成型方法,在现有传统方矩管冷弯成型工艺的基础上,开发一套直角梯形管的冷弯成型方法,仅需补充350kg模具(轧辊),占全套轧辊重量的10%,即可完成直角梯形管的成型。通过此低成本投入、高效益产出的生产工艺制造的直角梯形管各项技术参数断面边长、两边夹角、圆弧部位半径和产品平面度、弯曲度、扭转度等均满足《gb/t 6728-2017结构用冷弯空心型钢》标准要求,并且具备批量化生产的能力。
附图说明
24.图1为平辊第1、2、3架次梯形管上底成型示意图,每架次所用的平辊模具均包括有一个下辊、一个上辊;
25.图2为平辊第4、5、6、7架次梯形管腰部成型示意图,每架次所用的平辊模具均包括有一个下辊、一个上辊;
26.图3为平辊8、9、10架次封闭辊成型示意图,每架次所用的平辊模具均包括有上辊、下辊、左侧辊、右侧辊各一个;
27.图4为立辊1、2、3、4、5、6、7架次成型示意图,每架次所用的立辊模具均包括左侧立辊、右侧立辊各一个;
28.图5为挤压辊成型示意图,所用模具包括两个上辊和两个下辊;
29.图6为标准辊精整成型示意图,每架次所用模具均包括上辊、下辊、左侧辊和右侧辊各一个;
30.图7为直角梯形管产品横断面示意图;
31.其中,α-平辊1-3架次梯形上底两边弯角部位成型角度;β-平辊4-7架次成型角度;ω-立辊成型角度;λ-腰部直角边成型角度;μ-腰部斜边成型角度;σ-直角焊接小边成型角度;τ-钝角焊接小边成型角度。
具体实施方式
32.为更好地理解本发明,以下将结合附图和具体实施例对本发明的技术方案进行详细的说明。
33.一种直角梯形断面钢管的成型方法,包括如下步骤:
34.(1)根据梯形管产品断面形状尺寸确定横截面积,再综合考虑梯形管上底的内外毛刺量计算该产品的生产用料板带规格,本实施例中使用厚度2.0mm低合金钢板带;
35.(2)在成型阶段,先采用10架次平辊,7架次立辊将板料辊弯成未焊合的断面完成初成型:
36.将符合要求的原料板带依次通过第一架次平辊、第一架次立辊、第二架次平辊、第二架次立辊、第三架次平辊、第三架次立辊、第四架次平辊、第四架次立辊、第五架次平辊、第五架次立辊、第六架次平辊、第六架次立辊、第七架次平辊、第七架次立辊、第八架次平辊、第九架次平辊、第十架次平辊各架次配置的孔型,将板带经横向弯曲变形成为直角梯形的断面,完成初成型;
37.(3)板料通过初成型形成具有形状的断面后,再经过挤压辊模具,配合高频焊接工艺完成挤压焊接,形成直缝焊管,具体为:
38.采用四辊挤压的方式对初成型后的板料断面进行挤压,以板-板对接的方式对上底中间的焊合处进行挤压,在高频感应电流的作用下完成焊接。在毛刺刀片的作用下,梯形管焊接外毛刺在高温状态下被清除,梯形管内部毛刺予以保留。
39.(4)通过前述3个步骤形成直缝焊管后,通过5架次标准辊精整将产品尺寸控制在技术要求范围内,完成成型,具体为:
40.如图5所示,采用5架次四辊对产品断面进行精整,每架次四辊均配置有与梯形管断面形状相匹配的孔型,为确保梯形的各边长符合要求,精整过程中使用相对两辊间的间隙逐架次均匀递减的方法对断面各边长进行控制,确保产品通过所有架次后外观尺寸满足技术要求。
41.其中,步骤(2)的具体要求如下:
42.一弯成型:如图1所示,平辊1-3架次成型梯形管上底,根据均匀变形的原则,将上底两边弯角部位成型角度α按照架次顺序分别设计为22
°
、45
°
、68
°
,上底两边弯角部位成型角度对称;
43.二弯成型:如图2所示,平辊4-7架次成型梯形管腰部,成型角度β按4-7架次顺序分别设计为16
°
、32
°
、48
°
、64
°
,两腰部弯角处成型角度对称;
44.一弯成型和二弯成型均采用平辊和立辊交替方式进行,在各架次平辊结束后分别利用第1-7架次立辊对板料横向约束,避免偏心,如图4所示,立辊成型角度ω按1-7架次顺序依次设计为33
°
、56
°
、8
°
、24
°
、40
°
、56
°
、72
°
;
45.封闭辊成型:如图3所示,平辊8-10架次对整体形状进行控制,腰部直角边成型角度λ按架次顺序依次设计为80
°
、80
°
、86
°
,腰部斜边成型角度μ按架次顺序分别设计为82
°
、
90
°
、97
°
,直角焊接小边成型角度σ按架次顺序分别设计为80
°
、80
°
、86
°
,钝角焊接小边成型角度τ按架次顺序分别设计为74
°
、74
°
、77
°
,确保产品进入下一阶段的挤压焊接能满足工艺参数,顺利完成焊接。
46.本实施例中通过以上方法所制得直角梯形管50
×
50
×
40
×
2.0(2.0为厚度)各项技术参数如下:断面边长(上底40.22mm、下底50.10mm、高50.12mm)、两边夹角(梯形两个直角分别为90.2
°
、90.0
°
)、圆弧部位半径(四个圆弧半径均为4mm)和产品平面度(最大值为0.1mm)、弯曲度(长度10000mm的产品弯曲度2mm)、扭转度(长度10000mm的产品扭转度2mm),以上各参数均满足《gb/t 6728-2017结构用冷弯空心型钢》标准的相关要求,即断面边长(上底40mm
±
0.5mm、下底50mm
±
0.5mm、高50mm
±
0.5mm)、两边夹角(梯形两个直角90
°±
1.5
°
)、圆弧部位半径(3mm≤r≤5mm)和产品平面度(≤边长的0.6%)、弯曲度(长度方向上每米不应大于2mm,总弯曲度不应大于总长度的0.15%)、扭转度(≤2mm+l
×
0.5
‰
,l为长度,单位为mm)。
47.本发明的方法所制备的直角梯形管可以替代方矩管使用,同时其成型方法只需要在原有方矩管成型模具基础上,补充占全套轧辊重量的10%模具(一般为350kg轧辊),通过改变各架次成型角度,即可完成直角梯形管的成型。