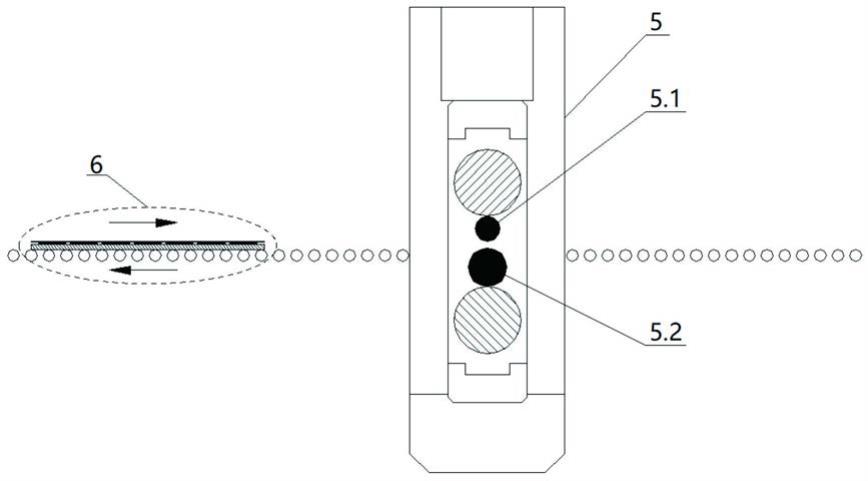
一种单块式tc4钛合金板材连续冷轧生产方法
技术领域
1.本发明涉及钛及钛合金生产技术领域,具体涉及一种单块式tc4钛合金板材连续冷轧生产方法。
背景技术:2.钛及钛合金板材是钛加工材的主要产品,2020年国内钛加工材产量不足10万吨,其中钛板材的产量超过了5万吨,占比约55%。钛板材具有轻质、高强、耐腐蚀和高温力学性能好的优点,因而广泛应用在国防工业、航空航天、石油化工、制盐制碱、船舶制造、海滨电站及医疗体育等行业。
3.tc4钛合金的合金成份是ti-6al-4v,具有显著的高强度、抗高温蠕变等优点,是所有钛合金中应用最为广泛的品种之一。但由于tc4存在强度高、加工难度大的问题,尤其是薄板产品普遍存在板形和机械性能各向异性的缺陷,因而其生产成品率低,导致销售价格居高不下;以海绵钛价格每吨7万元计,宽度1000mm,厚度0.5mm的中高端品质tc4薄板的销售价格超过了每吨30万元,使得tc4合金板材的大规模推广应用受到一定限制,尤其是体现在民品应用领域。
4.因而,提高tc4钛合金板材尤其是宽幅薄板的生产效率、成品率、板形质量和降低机械性能的各向异性,进而降低产品的生产成本和销售价格已成为钛合金板材加工行业亟待解决的技术难题之一。
5.目前国内外tc4钛合金板材所采用的生产工艺及连续轧制生产工艺的研发状况如下所述:一、很多企业为了降低投资,多借用钢铁等轧制生产线进行代料加工,但由于设备的专业化程度低,导致产品的性能和质量不稳定,尤其是产品的均匀性和一致性程度差。最为重要的是,宽幅tc4板材产品的板形质量和各向异性在目前钢铁行业所配置的轧机上生产时基本处于不受控状态,导致最终产品的性能及质量根本无法满足实际应用的要求。
6.二、采用传统的“二人转”式板材冷轧机进行人工辅助单块式法生产,其单块式、间断性的冷轧生产方式不仅存在连续化程度低、生产效率低的问题,同时在轧制过程中存在冷轧机频繁咬料、抛料、频繁升降速问题,都进一步恶化了tc4板材轧制过程的变形条件,还有现有的传统对称式冷轧变形方法还难以彻底解决产品各向异性技术难题。有统计数据证明,传统单块式法生产工艺冷轧的tc4板材综合成品率只有50%,但其能源消耗吨产品用电量却超过了1万千瓦时。另外,利用传统块片生产工艺冷轧的tc4钛合金板材产品的头尾、横向尺寸精度和板形控制难度大,最终成品需进行切边,导致切废和工艺废品居高不下。
7.三、tc4钛合金板材连续冷轧生产工艺的研制目前也遇到无法逾越的技术瓶颈,由于tc4钛合金特殊的晶格类型,因而难以实现像铝板带、铜板带以及纯钛ta1、ta2、ta3板带的卷式工艺进行高效生产。目前,国内外tc4钛合金板材以带式法生产工艺的开发均未成功,有个别企业试制成卷,但因产品的各向异性、强度、韧性等原因不能满足市场要求。另外,带式法连续轧制生产工艺从根源上为全纵向轧制,无法解决tc4板材产品的各向异性问
题。所以,现有卷式工艺及带式工艺生产技术均不适合tc4钛合金板材的连续生产。
技术实现要素:8.为了克服背景技术中的不足,本发明公开了一种单块式tc4钛合金板材连续冷轧生产方法,钛合金板在轧制过程中,配合使用有轧制基板,若干块钛合金板以设定间距设置在轧制基板上构成轧制复合体,然后通过可逆冷轧机进行往复多道次连续轧制,从而将现有的人工辅助tc4钛合金板材单块式轧制转变为恒辊缝状态下的稳速、稳态、连续化轧制,极大提高了tc4钛合金板材的生产效率;另外通过在轧制基板上设置导流沉槽来限制tc4钛合金板材在轧制过程中的流动方向,实现轧制过程tc4钛合金板材的纵向导流或横向导流的控制,通过可逆冷轧机交替对tc4钛合金板材进行纵向导流和横向导流往复多道次连续轧制,最终得到具有各向同性的高强度、高韧性、高板形质量的tc4钛合金板材;另外,tc4钛合金板材在冷轧变形过程中,因受到导流沉槽控制,使tc4钛合金板材产品的头尾、横向尺寸精度均得到良好控制,最终成品无需再进行切边,因此极大降低了切废和工艺废品,使tc4钛合金板材的生产成本得以大幅下降。
9.为了实现所述发明目的,本发明采用如下技术方案:一种单块式tc4钛合金板材连续冷轧生产方法,钛合金板在轧制过程中,配合使用有轧制基板,若干块钛合金板以设定间距设置在轧制基板上构成轧制复合体,然后通过可逆冷轧机进行往复多道次连续轧制;以轧制复合体的形式对单块tc4钛合金板材进行连续轧制时,仅在轧制复合体头部进入工作辊和轧制复合体尾部脱离工作辊时才会经历升降速,而若干块tc4钛合金板材在实际轧制过程中均无升降速的过程,使单块轧制过程转变为参数稳定可控的恒辊缝状态下的稳速、稳态、连续化轧制,tc4钛合金板材在轧制过程的变形条件始终稳定可控,因此有利于最终轧制成品的质量控制;在轧制基板配合下对tc4钛合金板材进行轧制时,为确保tc4钛合金板材在轧制过程中的变形可控性及轧制基板的使用寿命,轧制基板的材料选取应保证其材质屈服强度大于需轧制的钛合金板的屈服强度。
10.进一步的,钛合金板在轧制过程中,需经过粗轧、精轧、板形矫正三个过程,最终得到所需厚度尺寸的tc4钛合金板材,在以上三个轧制过程中,需配合使用不同的轧制基板,因此轧制基板又包括了粗轧基板、精轧基板、矫正基板,钛合金板在轧制过程中,以设定间距设置在粗轧基板、精轧基板或矫正基板上,通过可逆冷轧机依序进行往复多道次粗轧、精轧、矫正连续轧制;在粗轧、精轧、板形矫正三个轧制过程中,轧制率及实际轧制变形参数均不相同,通常粗轧单道次冷轧压下率为25%,轧制最大变形参数最大,因此所需轧制力也最大,为确保粗轧基板在轧制过程中不致发生结构破坏,其设计有较大的厚度,以初始厚度为2毫米的tc4钛合金板材为例,粗轧基板厚度为30毫米;通常精轧过程中实际单道次冷轧压下率为15%,轧制变形参数相对较小,因此所需轧制力也相对较小,精轧基板设计厚度为20毫米,保证精轧基板在轧制过程中不致发生结构破坏;在板形矫正轧制过程中,实际单道次冷轧压下率为最小,矫正基板设计厚度为5毫米即可在轧制过程中其结构不致发生破坏。
11.进一步的,粗轧基板包括粗轧纵向导流基板和粗轧横向导流基板,粗轧纵向导流基板和粗轧横向导流基板是在粗轧基板上设定间距设置轧纵向导流槽或横向导流槽而形成,纵向导流槽或横向导流槽为在轧制基板上表面设置的具有一定深度、长度和宽度的凹槽;对于纵向导流槽,其长度大于需轧制的钛合金板的长度,其宽度基本与需轧制的钛合金
板的宽度相等;对于横向导流槽,其长度基本等于需轧制的钛合金板的长度,其宽度大于需轧制的钛合金板的宽度;粗轧基板的纵向导流槽或横向导流槽的底部,可以设计成平面、凸面或凹面,但对于粗轧基板,其通常设计为凹面,使钛合金板材在粗轧过程中,板材边沿材料容易向纵向导流槽或横向导流槽内侧流动,以改善轧制过程中钛合金板材边沿出现的飞边问题,同时钛合金板材轧制过程上下板面的非对称变形,还会形成搓轧效应,有利于降低轧制后的各向异性;钛合金板在粗轧过程中,设置在粗轧纵向导流基板或粗轧横向导流基板的纵向导流槽或横向导流槽中,用于控制tc4钛合金板材在粗轧过程中材料的变形流动方向,通过可逆冷轧机依序进行纵向导流粗轧和横向导流粗轧往复多道次轧制,或通过可逆冷轧机交替进行纵向导流粗轧和横向导流粗轧往复多道次连续轧制,改善常规轧制时tc4钛合金板材金属轧制流动状态以纵向为主所导致的各向异性技术难题。
12.进一步的,精轧基板包括精轧纵向导流基板和精轧横向导流基板,精轧纵向导流基板和精轧横向导流基板和粗轧纵向导流基板和粗轧横向导流基板一样,是在精轧基板上以设定间距设置轧纵向导流槽或横向导流槽而形成;精轧基板的纵向导流槽或横向导流槽的底部,同样可以设计成平面、凸面或凹面,但对于精轧基板,其通常设计为凸面,以改善轧制过程中钛合金板材中间的受力,避免精轧后出现板材中间厚、边沿薄的板形问题;钛合金板在精轧过程中,设置在精轧纵向导流基板或精轧横向导流基板的纵向导流槽或横向导流槽中,用于控制tc4钛合金板材在精轧过程中材料的变形流动方向,通过可逆冷轧机依序进行纵向导流精轧和横向导流精轧往复多道次轧制,或通过可逆冷轧机交替进行纵向导流精轧和横向导流精轧往复多道次连续轧制,在tc4钛合金板材连续轧制变薄的过程中,同时消除材料流动变形所导致的各向异性问题。
13.进一步的,矫正基板包括纵向矫正基板和横向矫正基板,纵向矫正基板和横向矫正基板是在矫正基板上板面以设定间距设置纵向矫正槽或横向矫正槽而形成,纵向矫正槽或横向矫正槽与纵向导流槽或横向导流槽的不同之处在于两点:一、矫正基板的纵向导流槽或横向导流槽的深度、长度和宽度与tc4钛合金板材成品的厚度、长度和宽度尺寸基本相等;二、矫正基板的纵向矫正槽或横向矫正槽的底部为阵列设置的柱状凸形面或球形面;钛合金板在矫正轧制过程中,通过可逆冷轧机依序进行纵向矫正和横向矫正往复多道次矫正轧制,或通过可逆冷轧机交替进行纵向矫正和横向矫正往复多道次连续矫正轧制,在矫正轧制中,由于矫正基板的厚度较薄,矫正轧制实现对tc4钛合金板材轧制过程的下工作辊与矫正基板之间实际存在柔性可控的接触变形区,使tc4钛合金板材沿阵列设置的柱状凸形面或球形面使tc4钛合金板材发生局部微变形,从而达到对成品板形的矫正控制和进一步消除成品的各向异性问题;tc4钛合金板材在矫正轧制中,板材的上下两面均需进行矫正轧制;必要时,如果对tc4钛合金板材成品表面质量要求极高时,还需对板材的上下两面或其中一面做表面整形处理,以便消除矫正轧制在板材成品表面留下的矫正痕;如无特殊表面质量需求时,轧制后tc4钛合金板材成品表面的阵列矫正纹具有特殊的外观效果,可作为外观件直接使用。
14.通常情况下,在钛合金板在粗轧、精轧、矫正轧制工序之间,需进行退火处理,以消除粗轧、精轧后钛合金板材中出现的应力,同时有利于后续工序的加工。
15.进一步的,在某些情况下对tc4钛合金板材成品质量要求不是太高的应用场景下,粗轧基板、精轧基板、矫正基板可以直接做成为平板状,以减小粗轧基板、精轧基板、矫正基
板的加工费用,降低tc4钛合金板材的加工成本;若干块钛合金板以设定间距设置在粗轧基板、精轧基板、矫正基板上板面进行连续轧制,在轧制过程中,通过改变tc4钛合金板材在粗轧基板、精轧基板、矫正基板的放置方向,改变tc4钛合金板材在轧制过程中的变形流动方向,从而达到消除成品各向异性的目的。
16.进一步的,钛合金板在轧制过程中,钛合金板上表面覆盖有柔性覆板,通过柔性覆板将钛合金板与上工作辊隔离,达到改善轧制过程中材料流动性和延长上工作辊的使用寿命,同时通过选择不同材质的柔性覆板及厚度,增加了轧制过程工艺参数调整范围,以适应不同轧制工艺的需求。
17.进一步的,钛合金板在轧制过程中中,钛合金板下表面与轧制基板之间、钛合金板上表面与柔性覆板之间设置有轧制工艺介质;轧制工艺介质为矿物油、乳化液、石墨或玻璃粉中的一种,或为矿物油、乳化液、石墨或玻璃粉中的两种的混合物;设置轧制工艺介质的目的是减小轧制过程中,钛合金板下表面与轧制基板之间、钛合金板上表面与柔性覆板之间的摩擦力,实现界面润滑或相对滑动搓轧控制,提高tc4钛合金板材表面质量和尺寸精度,同时控制tc4钛合金板材和轧制基板之间的结合力,避免轧制过程破坏工艺介质层,使轧制后的tc4钛合金板材易于脱离轧制基板,达到改善轧制过程中材料流动性和延长轧制基板的使用寿命。
18.进一步的,可逆冷轧机的上工作辊、下工作辊之间设置有直径差,下工作辊直径大于上工作辊直径;上工作辊、下工作辊之间的直径差范围为0.2%-10%;在粗轧过程中,上工作辊、下工作辊之间的直径差通常采用10%,以提高下工作辊对轧制基板的支撑刚性;在精轧过程中,上工作辊、下工作辊之间的直径差通常采用5%,在保证精轧质量的前提下,尽可能提高下工作辊对轧制基板的支撑刚性;在矫正轧制过程中,上工作辊、下工作辊之间的直径差通常采用0.2%,因矫正轧制过程上工作辊、下工作辊受力较小,尽可能减小上工作辊、下工作辊的直径差,同时配合较薄的矫正基板,实现tc4钛合金板材轧制过程的下工作辊与矫正基板之间存在柔性可控的接触变形区,保证钛合金板材成品的机械性能及外观质量。
19.由于采用如上所述的技术方案,本发明具有如下有益效果:本发明公开的一种单块式tc4钛合金板材连续冷轧生产方法,钛合金板在轧制过程中,配合使用有轧制基板,若干块钛合金板以设定间距设置在轧制基板上构成轧制复合体,然后通过可逆冷轧机进行往复多道次连续轧制,从而将现有的人工辅助tc4钛合金板材单块式轧制转变为恒辊缝状态下的稳速、稳态、连续化轧制,极大提高了tc4钛合金板材的生产效率;另外通过在轧制基板上设置导流沉槽来限制tc4钛合金板材在轧制过程中的流动方向,实现轧制过程tc4钛合金板材的纵向导流或横向导流的控制,通过可逆冷轧机交替对tc4钛合金板材进行纵向导流和横向导流往复多道次连续轧制,最终得到具有各向同性的高强度、高韧性、高板形质量的tc4钛合金板材;另外,tc4钛合金板材在冷轧变形过程中,因受到导流沉槽控制,使tc4钛合金板材产品的头尾、横向尺寸精度均得到良好控制,最终成品无需再进行切边,因此极大降低了切废和工艺废品,使tc4钛合金板材的生产成本得以大幅下降。
附图说明
20.图1为单块式tc4钛合金板材连续冷轧生产方法原理示意图;图2为钛合金板在轧制基板设置形式示意图;
图3为轧制复合体结构示意图;图4为导流沉槽结构示意图一;图5为导流沉槽结构示意图二;图6为导流沉槽结构示意图三;图7为钛合金板在平板结构的轧制基板上的设置示意图;图8为钛合金板在平面状导流沉槽上的设置状况示意图;图9为钛合金板在凸面状导流沉槽上的设置状况示意图;图10为钛合金板在凹面状导流沉槽上的设置状况示意图。
21.图中:1、轧制基板;1.1、导流沉槽;2、钛合金板;3、轧制工艺介质;4、柔性覆板;5、可逆冷轧机;5.1、上工作辊;5.2、下工作辊;6、轧制复合体。
具体实施方式
22.通过下面的实施例可以详细的解释本发明,公开本发明的目的旨在保护本发明范围内的一切技术改进。
23.以下以原始尺寸规格为2
×
1125
×
1500mm毫米,成品尺寸规格为0.5
×
1500
×
3000mm毫米的tc4钛合金板材轧制生产为例,具体说明单块式tc4钛合金板材连续冷轧生产方法:钛合金板2在轧制生产过程中,需经过粗轧、精轧、矫正轧制三道工序;粗轧配合使用粗轧纵向导流基板和粗轧横向导流基板,粗轧纵向导流基板和粗轧横向导流基板的尺寸为30
×
2000
×
20000mm,材料选用模具钢,经热处理及表面处理及表面处理保证强度及表面硬度;粗轧纵向导流基板上设置有五个粗轧纵向导流沉槽,粗轧横向导流基板上设置有五个粗轧横向导流沉槽,纵向导流沉槽和横向导流沉槽深度均为1.0毫米,底面凹度均为0.05毫米;五块钛合金板2设置在粗轧纵向导流基板的粗轧纵向导流沉槽中,首先进行两次纵向导流粗轧,然后再将钛合金板2设置在粗轧纵向导流基板的精轧纵向导流沉槽中,进行两次横向导流粗轧;粗轧过程中,tc4板材上表面设置有厚度为0.5毫米、材质为pvc的柔性覆板4,钛合金板2上下面均涂抹有5号轧制工艺润滑油;轧机选用四辊可逆冷轧机,轧机上工作辊直径比下工作辊直径小10%,单道次冷轧压下率控制在20%-30%,轧制速度控制在0.2-0.5m/s;精轧配合使用精轧纵向导流基板和精轧横向导流基板,精轧纵向导流基板和粗轧横向导流基板的尺寸为20
×
2200
×
40000mm,材料选用模具钢,经热处理及表面处理保证强度及表面硬度;精轧纵向导流基板上设置有五个精轧纵向导流沉槽,精轧横向导流基板上设置有五个精轧横向导流沉槽,纵向导流沉槽和横向导流沉槽深度均为0.5毫米,底面凸度均为0.05毫米;粗轧后的钛合金板2设置在精轧纵向导流基板的粗轧纵向导流沉槽中,首先进行两次纵向导流精轧,然后再将钛合金板2设置在精轧纵向导流基板的精轧纵向导流沉槽中,进行两次横向导流精轧;精轧过程中,tc4板材上表面设置有厚度为0.3毫米、材质为pvc的柔性覆板4,钛合金板2上下面均涂抹有5号轧制工艺润滑油;轧机选用四辊可逆冷轧机,轧机上工作辊直径比下工作辊直径小5%,单道次冷轧压下率控制在15%-20%,轧制速度控制在0.5-1.0m/s;矫正轧制配合使用纵向矫正基板和横向矫正基板,纵向矫正基板和横向矫正基板
的尺寸为5.0
×
2200
×
40000mm,材料选用模具钢,经热处理及表面处理保证强度及表面硬度;纵向矫正基板上设置有五个纵向矫正沉槽,横向矫正基板上设置有五个横向矫正沉槽,纵向矫正沉槽和横向矫正沉槽深度均为0.5毫米,底面阵列设置有凸度均为0.02毫米柱状凸形面;精轧后的钛合金板2设置在纵向矫正基板的纵向矫正沉槽中,首先进行一次纵向纵向矫正轧制,然后再将钛合金板2设置在横向矫正基板的横向矫正沉槽中,进行一次横向矫正轧制;将钛合金板2翻转上下面,重复上述矫正轧制过程;矫正轧制过程中,钛合金板2上下面均涂抹有5号轧制工艺润滑油;轧机选用四辊可逆冷轧机,轧机上工作辊直径比下工作辊直径小1.5%,单道次冷轧压下率均控制在2.0%,轧制速度控制在1.5m/s;矫正轧制完成后,将tc4钛合金板材定尺寸剪切为0.5
×
1500
×
3000mm的成品板材。
24.本发明未详述部分为现有技术。