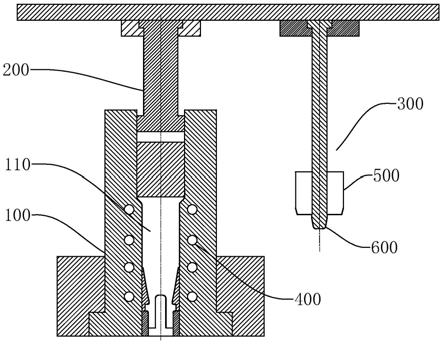
1.本技术涉及发动机风扇轴技术领域,尤其是涉及一种双盲孔风扇轴一体化双向挤压近净成形工艺。
背景技术:2.航空涡扇发动机风扇轴在工作时承受巨大的扭矩载荷,将涡轮功率传递给风扇,带动大尺寸风扇转动并产生推力,现航空涡扇发动机的风扇轴设计发展较快,传统发动机风扇轴设计多为渐变型鼓筒形结构,如cfm56系列发动机等;最新发展为收口型瓶形结构,此类风扇轴具有内径不等径,内外变截面,外壁端口有凸台,内壁中部有凸台等特点。
3.在此之前,风扇轴类锻件通常采用组合模锻的工艺方式成形,此类组合模锻工艺采用实心锻造,分别进行杆部自由拔长工序+模锻成形头部,工艺简单,设备要求低,易于操作,但存在锻件锻造变形量较小,应变分布不均匀,多火次加热存在局部空烧,组织均匀性较差,锻件加工割断了变形组织流线,材料利用率低等问题。
4.近年来,不断有优化工艺方案试图解决分体式模锻存在的问题,公开号为cn103350180a的发明专利《c25马氏体时效钢风扇轴的锻造成形方法》采用组合模锻的工艺成形,存在材料利用率低,各部位应变不均匀;公开号为cn 105057529a的发明专利《变截面空心轴锻件挤压成型方法》以及公开号为cn 106862471a的发明专利《一种空心挤压c250合金钢长轴类锻件的成型方法》中,针对鼓筒形风扇轴结构锻件设计,设计了圆孔的坯料,锻件采用正向挤压成型,其特点是界面差小,锻件大头端的变形量较小。
技术实现要素:5.为了提高风扇轴各部位变形量及整体变形均匀性,本技术提供了一种双盲孔风扇轴一体化双向挤压近净成形工艺。
6.本技术提供的一种双盲孔梭形风扇轴的锻造模具,采用如下的技术方案:双盲孔风扇轴一体化双向挤压近净成形工艺,包括坯料一火次加热后利用模具正向挤压形成第一盲孔和反向挤压形成第二盲孔的步骤。
7.通过采用上述技术方案:一火次加热、两工步分别采用正向挤压和反向挤压双向组合挤压整体成形。该风扇轴锻件成形技术整体一火加热,变形充分均匀,成形后锻件具有组织均匀精细,流线完整随形,内外表面近净成形等特点,可显著提高风扇轴锻件整体组织均匀一致性,同时提高风扇轴零件转动疲劳性能。
8.可选的,所述模具包括下模、与下模配合的压模和上模,第一盲孔由压模和下模配合正向挤压形成,第二盲孔由下模和上模配合反向挤压形成,其中下模中设置有加热组件,上模为带有辅针器的挤压杆结构,所述下模的底部设有向上的第一盲孔成型杆。
9.通过采用上述技术方案:将坯料加热至特定温度并涂覆润滑介质,第一工步坯料在下模腔内由压模正向挤压形成锻件第一盲孔,第二工步更换为上模,上模下移过程中反挤压坯料形成锻件第二盲孔,通过在下模内设有加热组件,可以使得下模的模腔内保持一
定的温度,在挤压坯料的过程中更容易使得坯料均匀变形。
10.可选的,具体包括以下步骤:s1、将棒材加工成挤压坯料,加热至挤压温度并适当冲温;同时完成模具的预热和组装固定;s2、坯料出炉滚涂润滑介质后转移至下模的模腔内;s3、压模与下模合模,压模向下移动,坯料在下模内受正向挤压向下变形流动,坯料充满下模的模腔,完成第一工步正向挤压,成形锻件第一盲孔和凸台;s4、压模复位,将压模更换为上模,上模和下模再次合模,上模向下移动,坯料在下模腔内受反向挤压反向变形流动,完成第二工步反挤压,成形锻件第二盲孔。
11.通过采用上述技术方案:工艺流程简单,采用两次正反组合挤压成形,可实现复杂截面空腔型风扇轴类锻件一火整体结构的近净成型,成形锻件为双盲孔结构,成形工艺具有双向组合挤压、单一火次整体加热、一体化空心整体成形的特点,锻件整体变形充分均匀,金属流变连续随形,组织致密,表面质量好,大幅度提高锻件整体的流线完整性、应力均匀性和组织性能一致性,材料利用率高,降低生产成本。
12.可选的,所述坯料预先放入预热炉内预热,然后在表面喷涂防氧化剂,采用电炉加热至1000-1200
°
,冲温5-10
°
。
13.通过采用上述技术方案:可以防止坯料氧化,加热和冲温后的坯料更容易挤压变形。
14.可选的,所述下模通过加热组件预热,使得下模的模腔内温度在200-350
°
之间,所述压模和上模均在预热炉内预热至300-350
°
,压模、上模和下模内均涂覆润滑剂。
15.通过采用上述技术方案:通过预热和在坯料表面涂覆润滑剂,可以使得坯料更容易挤压变形,对坯料的内部金属结构损伤下,提高了应力均匀性。
16.可选的,所述压模向下模合模的过程中,以18-22mm/s速度完成正向挤压,在更换完上模后,上模成为带有辅针器的挤压杆结构,上模移动并合模,以18-22mm/s速度完成反向挤压。
17.通过采用上述技术方案:通过上述两个步骤,可以能够较为快速的在坯料的底端形成第一盲孔,在坯料的上端形成第二盲孔。
18.可选的,还包括将坯料由下模向上顶出后将风扇轴锻件进行固溶热处理,机械加工去除表面余量的步骤。
19.通过采用上述技术方案:使得锻件的表面更为光滑。
20.可选的,所述挤压杆结构为分段的分体式结构,所述辅针器滑动套设在挤压杆上。
21.通过采用上述技术方案:随上模的不断下压,逐段去除辅针器,以保证挤压杆承力均匀。
22.综上所述,本技术包括以下至少一种有益技术效果:单一火次整体加热、一体化空心整体成形的特点,锻件整体变形充分均匀,金属流变连续随形,组织致密,表面质量好,大幅度提高锻件整体的流线完整性、应力均匀性和组织性能一致性,材料利用率高,降低生产成本。
附图说明
23.图1是本技术实施例的压模与下模一状态配合图。
24.图2是本技术实施例的压模与下模另一状态配合图。
25.图3是本技术实施例的上模与下模的一状态配合图。
26.图4是本技术实施例的上模与下模的另一状态配合图。
27.图5是本技术实施例的上模脱模后的结构示意图。
28.图6是本技术实施例的锻件取出结构示意图。
29.附图标记说明,100、下模;110、模腔;200、压模;300、上模;400、加热组件;500、辅针器;600、挤压杆。
具体实施方式
30.以下结合附图1-6对本技术作进一步详细说明。
31.本技术实施例公开了一种双盲孔风扇轴一体化双向挤压近净成形工艺。
32.参照图1和图2,双盲孔风扇轴一体化双向挤压近净成形工艺包括坯料一火次加热后利用模具正向挤压形成第一盲孔和反向挤压形成第二盲孔的步骤。一火次加热、两工步分别采用正向挤压和反向挤压双向组合挤压整体成形,该风扇轴锻件成形技术整体一火加热,变形充分均匀,成形后锻件具有组织均匀精细,流线完整随形,内外表面近净成形等特点,可显著提高风扇轴锻件整体组织均匀一致性,同时提高风扇轴零件转动疲劳性能。
33.参照图3和图4,本实施例中的模具包括下模100、与下模100配合的压模200和上模300,下模100的内部设有中空的模腔110,所述下模100的底部设有向上的第一盲孔成型杆;第一盲孔由压模200和下模100配合正向挤压形成,第二盲孔由下模100和上模300配合反向挤压形成,其中下模100中设置有加热组件400,上模300为带有辅针器500的挤压杆600结构。通过在下模100内设有加热组件400,可以使得下模100的模腔110内保持一定的温度。将坯料加热至特定温度并涂覆玻璃润滑剂,第一工步棒坯在下模100腔内由压模200正向挤压形成锻件第一盲孔,第二工步更换上模300,上模300下移过程中反挤压坯料形成锻件第二盲孔。
34.本实施例中,具体包括以下步骤:s1、将棒材加工成挤压坯料,加热至挤压温度并适当冲温;同时完成模具的预热和组装固定;具体的,坯料预先放入预热炉内预热,然后在表面喷涂防氧化剂,采用电炉加热至1000-1200
°
,冲温5-10
°
。可以防止坯料氧化,加热和冲温后的坯料更容易挤压变形。下模100通过加热组件400预热,使得下模100的模腔110内温度在200-350
°
之间,所述压模200和上模300均在预热炉内预热至300-350
°
,压模200、上模300和下模100内均涂覆润滑剂。通过预热和在坯料表面涂覆润滑剂,可以使得坯料更容易挤压变形,对坯料的内部金属结构损伤下,提高了应力均匀性。
35.s2、坯料出炉滚涂润滑介质后转移至下模100的模腔110内;具体的,坯料出炉后在操作台进行表面滚涂玻璃润滑剂,机械手在30s内快速、准确的将坯料转移至下模100的模腔110内。
36.s3、压模200与下模100合模,压模200向下移动,坯料在下模100内受正向挤压向下变形流动,坯料充满下模100的模腔110,完成第一工步正向挤压,成形锻件第一盲孔和凸
台;所述挤压杆600结构为分段的分体式结构,辅针器500滑动套设在挤压杆600上。随上模300的不断下压,逐段去除辅针器500,以保证挤压杆600承力均匀。
37.s4、压模200复位,将压模200更换为上模300,上模300和下模100再次合模,上模300向下移动,坯料在下模100腔内受反向挤压反向变形流动,完成第二工步反挤压,成形锻件第二盲孔;其中,压模200向下模100合模的过程中,以18-22mm/s速度完成正向挤压,在更换完上模300后,上模300成为带有辅针器500的挤压杆600结构,上模300移动并合模,以18-22mm/s速度完成反向挤压。通过上述两个步骤,可以能够较为快速的在坯料的底端形成第一盲孔,在坯料的上端形成第二盲孔。
38.参照图5和图6,步骤s5、上模300再次复位,通过工具上顶将风扇轴锻件移出下模100并转移。
39.本实施例还包括将顶出后将风扇轴锻件进行固溶热处理,机械加工去除表面余量的步骤。使得锻件的表面更为光滑。
40.上述工艺流程简单,采用两次正反组合挤压成形,可实现复杂截面空腔型风扇轴类锻件一火整体结构的近净成型,成形锻件为双盲孔结构,成形工艺具有双向组合挤压、单一火次整体加热、一体化空心整体成形的特点,锻件整体变形充分均匀,金属流变连续随形,组织致密,表面质量好,大幅度提高锻件整体的流线完整性、应力均匀性和组织性能一致性,材料利用率高,降低生产成本。
41.以上均为本技术的较佳实施例,并非依此限制本技术的保护范围,故:凡依本技术的结构、形状、原理所做的等效变化,均应涵盖于本技术的保护范围之内。