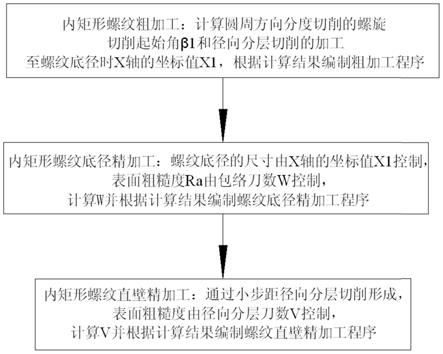
1.本发明涉及燃气轮机单向离合器螺旋花键加工领域,尤其涉及一种多头大槽宽大螺旋角高精度内矩形螺纹的加工方法。
背景技术:2.某型燃气轮机有一启动电机离合器,内含一种特殊的内矩形螺纹结构,其螺纹大径d1≤φ20mm,螺纹小径d3≤φ17mm,螺纹头数n≥4,槽宽弦长k≥5mm,槽距l≤15,螺旋角α≥40
°
,表面粗糙度≤ra1.6μm。
3.这种结构的螺纹:槽宽大,采用成形车刀加工,刀具难以承受巨大的切削力及冲击力,产生振刀、崩刀,且圆弧底径成形困难;螺旋角大,齿数较少,难以在插齿机上按插斜齿轮的方式加工;孔径小,无法在加工中心上采用动力头铣削。总之,难以用常规方法实现小孔径多头大槽宽大螺旋角高精度内矩形螺纹这一特征,同时为保障其传动平稳性,槽宽精度及表面粗糙度要求高,控制难度大。
技术实现要素:4.本发明要解决的技术问题是克服现有技术的不足,提供一种解决了大槽宽大螺旋角高精度内矩形螺纹缺乏适用的加工方法、精度控制困难等问题的多头大槽宽大螺旋角高精度内矩形螺纹的加工方法。
5.为解决上述技术问题,本发明采用以下技术方案:
6.一种多头大槽宽大螺旋角高精度内矩形螺纹的加工方法,包括以下步骤:
7.s1、内矩形螺纹粗加工:包括圆周方向分度切削以及径向分层切削,计算圆周方向分度切削的螺旋切削起始角β1和径向分层切削的加工至纹底径时x轴的坐标值x1,
8.β1和x1的计算公式为,
[0009][0010][0011][0012]
其中,d1为内矩形螺纹大径,s为螺纹导程,k为内矩形螺纹槽宽弦长,p为螺纹车刀刃宽,r为螺纹车刀刀尖半径,α为内矩形螺纹底径处螺旋角,
[0013]
基于g32螺纹切削指令,根据计算结果编制粗加工程序;
[0014]
s2、内矩形螺纹底径精加工:螺纹底径通过螺纹车刀刀刃两端刀尖圆角包络形成,螺纹底径的尺寸由x轴的坐标值x1控制,表面粗糙度ra由包络刀数w控制,w的计算公式为,
[0015][0016]
其中,γ为校正系数,
[0017]
基于g32螺纹切削指令,根据计算结果编制螺纹底径精加工程序;
[0018]
s3、内矩形螺纹直壁精加工:通过小步距径向分层切削形成,表面粗糙度由径向分层刀数v控制,v的计算公式为,
[0019][0020]
其中,d3为内矩形螺纹小径,δ为校正系数,
[0021]
基于g32螺纹切削指令,根据计算结果编制螺纹直壁精加工程序。
[0022]
作为上述方案的进一步改进:步骤s1中,粗加工程序包括子程序和主程序,子程序为圆周分度,对单个螺旋槽,如第一刀螺纹切削起始角q1=q,则最后一刀螺纹切削起始角q2=q+1000(β
1-2),其中2为槽宽余量,单位为
°
;步距按螺纹车刀最大切宽设置;主程序为径向分层,最后一刀x轴坐标值为x1-0.2,其中0.2为圆弧底径余量,单位为mm;切削参数以调质后的中碳合金钢为例,步距按0.07~0.18mm设置,切削速度范围为2~4m/min。
[0023]
作为上述方案的进一步改进:在步骤s2中,螺纹底径精加工程序为圆周分度,对单个螺旋槽,x轴坐标值为x1,如第一刀螺纹切削起始角q1=q,则最后一刀螺纹切削起始角q2=q+1000β1,步距按β1/w设置。
[0024]
作为上述方案的进一步改进:在步骤s3中,槽宽尺寸精度通过补偿后螺纹切削起始角范围β1+δβ控制,由于螺纹车刀存在刀尖圆角,螺纹切削起始角q值范围按β1加工时,槽宽尺寸实测值偏小,叠加机床及刀具误差,生产过程中首件调试时,需调整精加工内矩形螺纹直壁程序中螺纹切削起始角q值范围,调整量为δβ,δβ的计算公式为,
[0025][0026]
其中,δk—内矩形螺纹槽宽弦长余量。
[0027]
作为上述方案的进一步改进:在步骤s1中,采用专用内矩形螺纹车刀,在刚性足和轴向运动速度≥2m/min的数控车床上进行车削加工,并以螺纹车刀主切削刃刃宽中点为刀具零点进行对刀。
[0028]
与现有技术相比,本发明的优点在于:
[0029]
本发明的多头大槽宽大螺旋角高精度内矩形螺纹的加工方法,通过对高精度内矩形螺纹空间结构进行分析,针对大槽宽、大螺旋角、圆弧底径、短距多头内矩形螺纹加工,制定了技术方案,具体为,根据内矩形螺纹参数以及刀具参数,精确计算得到螺纹切削起始角范围以及精加工刀路数,用于编制初始车削程序;通过设定螺纹切削起始角范围及径向分层梯度,控制螺纹的槽宽尺寸及表面粗糙度;通过设定精加工螺纹切削起点x坐标及圆周分层梯度,包络出螺纹的圆弧底径,控制螺纹的圆弧底径尺寸及其表面粗糙度,首次采用数控车床和螺纹车刀,解决了大槽宽大螺旋角高精度内矩形螺纹缺乏适用的加工方法、精度控制困难等问题。
附图说明
[0030]
图1是本发明的多头大槽宽大螺旋角高精度内矩形螺纹的加工方法的流程示意图。
[0031]
图2是本发明的内矩形螺纹的剖面示意图(图中a表示内矩形螺纹)。
[0032]
图3是本发明的内矩形螺纹的轴向示意图(图中a表示内矩形螺纹)。
[0033]
图4是本发明中内矩形螺纹粗加工的刀具轨迹示意图。
[0034]
图5是本发明中内矩形螺纹底径精加工的刀具轨迹示意图。
[0035]
图6是本发明中内矩形螺纹直壁精加工的刀具轨迹示意图。
具体实施方式
[0036]
以下结合说明书附图和具体实施例对本发明作进一步详细说明。
[0037]
图1所示,本发明的多头大槽宽大螺旋角高精度内矩形螺纹的加工方法,包括以下步骤:
[0038]
s1、内矩形螺纹粗加工:包括圆周方向分度切削以及径向分层切削,计算圆周方向分度切削的螺旋切削起始角β1和径向分层切削的加工至螺纹底径时x轴的坐标值x1,
[0039]
β1和x1的计算公式为,
[0040][0041][0042][0043]
其中,d1为内矩形螺纹大径,s为螺纹导程,k为内矩形螺纹槽宽弦长,p为螺纹车刀刃宽,r为螺纹车刀刀尖半径,α为内矩形螺纹底径处螺旋角,
[0044]
基于g32螺纹切削指令,根据计算结果编制粗加工程序;
[0045]
s2、内矩形螺纹底径精加工:螺纹底径通过螺纹车刀刀刃两端刀尖圆角包络形成,螺纹底径的尺寸由x轴的坐标值x1控制,表面粗糙度ra由包络刀数w控制,w的计算公式为,
[0046][0047]
其中,γ为校正系数,
[0048]
基于g32螺纹切削指令,根据计算结果编制螺纹底径精加工程序;
[0049]
s3、内矩形螺纹直壁精加工:通过小步距径向分层切削形成,表面粗糙度由径向分层刀数v控制,v的计算公式为,
[0050][0051]
其中,d3为内矩形螺纹小径,δ为校正系数,
[0052]
基于g32螺纹切削指令,根据计算结果编制内矩形螺纹直壁精加工程序。
[0053]
本发明的多头大槽宽大螺旋角高精度内矩形螺纹的加工方法,通过对高精度内矩形螺纹空间结构进行分析,针对大槽宽、大螺旋角、圆弧底径、短距多头内矩形螺纹加工,制定了技术方案,具体为,根据内矩形螺纹参数以及刀具参数,精确计算得到螺纹切削起始角范围以及精加工刀路数,用于编制初始车削程序;通过设定螺纹切削起始角范围及径向分层梯度,控制螺纹的槽宽尺寸及表面粗糙度;通过设定精加工螺纹切削起点x坐标及圆周分层梯度,包络出螺纹的圆弧底径,控制螺纹的圆弧底径尺寸及其表面粗糙度,首次采用数控车床和螺纹车刀,解决了大槽宽大螺旋角高精度内矩形螺纹缺乏适用的加工方法、精度控制困难等问题。本发明为类似的大槽宽大螺旋角高精度内矩形螺纹加工提供了技术参考。
[0054]
本实施例中,步骤s1中的内矩形螺纹粗加工,主要包括圆周方向分度切削以及径向分层切削。零件采用专用内矩形螺纹车刀,在刚性足和轴向运动速度合适(≥2m/min)的数控车床上进行车削加工,并以螺纹车刀主切削刃刃宽中点为刀具零点进行对刀。单个行程运动包括车刀沿工件轴向的进给运动以及工件主轴的圆周运动(与轴向进给轴联动),各行程圆周方向分度通过调整切削起始角实现,径向分层通过x轴坐标偏移实现,如图4所示,f实线为内矩形螺纹小径,e实线为内矩形螺纹轮廓,虚线为刀具轮廓。
[0055]
步骤s1中的公式推导过程如下:
[0056]
为实现上述运动,需确定螺纹切削起始角范围β1(单位:度)以及加工成品螺纹底径时x轴坐标值x1(单位:mm)。
[0057]
α(单位:度)为内矩形螺纹底径处螺旋角,采用下式计算:
[0058][0059]
式中:d1为内矩形螺纹大径,s为螺纹导程。
[0060]
β(单位:度)为圆弧上某一弦长c对应的圆心角,采用下式计算:
[0061][0062]
式中:d为圆弧直径(通用公式中举例用的圆弧)。
[0063]
由式(1)和式(2)可得,内矩形螺纹横截面上零件圆周分度角度范围即螺纹切削起始角范围计算方法:
[0064][0065]
式中:k为内矩形螺纹槽宽弦长,p为螺纹车刀刃宽。
[0066]
由于螺纹底径由螺纹车刀刀刃两端刀尖轨迹包络形成,加工成品螺纹底径时x轴坐标值x1必然小于内矩形螺纹大径d1,叠加螺纹车刀刀尖半径r影响。车刀刀尖圆弧与主切削刃切点可近似为刀尖圆弧与实际包络轮廓的切点,按勾股定理,其计算方法:
[0067][0068]
基于fanuc系统螺纹切削指令g32(指令格式:g32 x_z_f_j_k_q_;),编制粗加工程序。其中子程序为圆周分度,对单个螺旋槽,如第一刀螺纹切削起始角q1=q,则最后一刀螺纹切削起始角q2=q+1000(β
1-2),其中2
°
为槽宽余量,步距按螺纹车刀最大切宽设置;主程序为径向分层,最后一刀x轴坐标值为x1-0.2,其中0.2mm为螺纹底径余量,切削参数以调质后的中碳合金钢为例,步距按0.07~0.18mm设置,切削速度范围为2~4m/min。
[0069]
本实施例中,步骤s2中,螺纹底径通过螺纹车刀刀刃两端刀尖圆角包络形成,底径尺寸由x1控制,表面粗糙度由精加工螺纹底径时包络刀数w控制。
[0070]
步骤s2中的公式推导过程如下:
[0071]
表面粗糙度ra可近似为相邻步距在零件表面上残料的残余高度,在步距较小的情况下,圆弧上弧长可近似为弦长,则按弦长计算方法,步距t(单位:mm)计算公式:
[0072][0073]
已知螺纹切削起始角范围β1对应的弧长,刀数w等于螺纹底径实际切削弧长(πd1β1/360,根据圆心角算弧长)除以步距t,则精加工螺纹底径时包络刀数w计算方法:
[0074][0075]
式中:γ为校正系数,属于经验参数,一般情况下为0.5。
[0076]
基于螺纹切削指令g32(指令格式:g32 x_z_f_j_k_q_;),编制螺纹底径精加工程序。程序为圆周分度,对单个螺旋槽,x轴坐标值为x1,如第一刀螺纹切削起始角q1=q,则最后一刀螺纹切削起始角q2=q+1000(β
1-2),步距按β1/w设置,如图5所示,j实线为内矩形螺纹小径,h实线为内矩形螺纹轮廓,虚线为刀具轮廓。
[0077]
本实施例中,步骤s3中,内矩形螺纹直壁通过小步距径向分层切削形成,槽宽尺寸精度通过补偿后螺纹切削起始角范围β1+δβ控制,表面粗糙度由精加工内矩形螺纹直壁径向分层刀数v控制。
[0078]
步骤s3中的公式推导过程如下:
[0079]
由于螺纹车刀存在刀尖圆角,螺纹切削起始角q值范围按β1加工时,槽宽尺寸实测值偏小,叠加机床及刀具误差,生产过程中首件调试时,需调整精加工内矩形螺纹直壁程序中螺纹切削起始角q值范围,调整量为δβ,由式(3)可推导出其计算方法:
[0080][0081]
式中:δk—内矩形螺纹槽宽弦长余量。
[0082]
与式(5)和式(6)同理可得精加工内矩形螺纹直壁径向分层刀数v计算方法:
[0083][0084]
式中:d3为内矩形螺纹小径,δ为校正系数,属于经验参数,一般情况下为0.6。
[0085]
基于螺纹切削指令g32(指令格式:g32 x_z_f_j_k_q_;),编制内矩形螺纹直壁精加工程序。其中子程序为圆周方向加工两刀,对单个螺旋槽,如第一刀螺纹切削起始角q1=q,则第二刀螺纹切削起始角q2=q+1000(β1+δβ);主程序为径向分层,最后一刀x轴坐标值为x1-0.05,步距按(d
1-d3)/2v设置,如图6所示,n实线为内矩形螺纹小径,m实线为内矩形螺纹轮廓,虚线为刀具轮廓。
[0086]
具体实施案例:
[0087]
某型燃气轮机启动电机离合器中一种特殊的内矩形螺纹加工方法,包括以下步骤:
[0088]
1)根据内矩形螺纹导程s=62.2mm、大径d1=φ20.3mm,槽宽弦长k=5.5mm、螺纹车刀刃宽p=2mm、刀尖半径r=0.3mm,计算确定:
[0089]
螺纹切削起始角范围β1=29.62
°
;
[0090]
加工成品圆弧底径时x轴坐标值x1=20.294mm。
[0091]
基于g32螺纹切削指令,根据上述步骤计算结果编制粗加工程序(限于篇幅,仅展示片段,其余为重复语句段):
[0092]
子程序:
[0093][0094]
主程序:
[0095][0096]
2)螺纹底径主要通过螺纹车刀两刀尖圆角包络形成,经计算确定:
[0097]
精加工圆弧底径时包络刀数w=43。
[0098]
基于g32螺纹切削指令,根据上述步骤计算结果编制圆弧底径精加工程序(限于篇幅,仅展示片段,其余为重复语句段):
[0099][0100]
3)内矩形螺纹直壁通过小步距径向分层切削形成,经计算确定:精加工内矩形螺纹直壁时径向分层刀数v=13。
[0101]
基于g32螺纹切削指令,根据上述步骤计算结果编制内矩形螺纹直壁精加工程序(限于篇幅,仅展示片段,其余为重复语句段):
[0102]
子程序:
[0103][0104]
主程序:
[0105][0106]
4)选择具有或兼容fanuc系统的数控车床进行车削,首件调试螺纹切削起始角调整量δβ=0.58
°
,槽宽尺寸合格,表面粗糙度实测为ra1.108μm(垂直加工纹路方向)、ra0.637μm(轴线方向),满足设计图规定要求。
[0107]
以上所述,仅是本发明的较佳实施例而已,并非对本发明作任何形式上的限制。虽然本发明已以较佳实施例揭示如上,然而并非用以限定本发明。任何熟悉本领域的技术人员,在不脱离本发明的精神实质和技术方案的情况下,都可利用上述揭示的方法和技术内容对本发明技术方案做出许多可能的变动和修饰,或修改为等同变化的等效实施例。因此,凡是未脱离本发明技术方案的内容,依据本发明的技术实质对以上实施例所做的任何简单修改、等同替换、等效变化及修饰,均仍属于本发明技术方案保护的范围内。