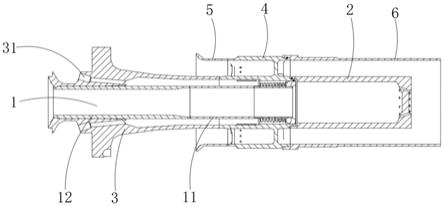
1.本发明涉及零部件制造方法技术领域,尤其涉及一种燃气轮机燃烧室喷嘴的制造方法。
背景技术:2.随着世界范围内对环境保护问题的日益重视和天然气资源的进一步开发利用,燃气轮机及其联合循环技术在电力生产领域中占据了越来越重要的地位。
3.燃气轮机燃烧室喷嘴是燃气轮机组件中非常重要的一部分,出于功能上的需求,燃气轮机燃烧室喷嘴的结构较为复杂,在制造流程上只能是分别制造好各零部件后,再把各零部件组合才能得到成品。燃气轮机燃烧室喷嘴的零部件一般包括波纹管、安装在波纹管前端的扩散头、套接在波纹管的法兰和旋流器、套接在法兰与旋流器的交界处的气流环、和连接在旋流器的前端的燃烧器管,上述零部件之间需要采用焊接的方式相互连接,出于使用场景的需要,焊接缝隙不能有漏洞,出于装配需求,零部件与零部件之间的装配精度要求也很高,上述因素使得燃气轮机燃烧室喷嘴的加工难度大,工艺复杂。同时,燃气轮机燃烧室喷嘴的零部件一般由耐高温的哈氏合金等难熔金属材料制成,传统工艺采用氩弧焊工艺进行焊接,这导致焊接收缩量大、变形大,难以控制零部件的焊接尺寸,使得最终成品不良率高,效率低。
技术实现要素:4.本发明的目的在于提供一种燃气轮机燃烧室喷嘴的制造方法,旨在解决燃气轮机燃烧室喷嘴制造时不良率高、效率低的问题。
5.为了达到上述的目的,本发明提供了一种燃气轮机燃烧室喷嘴的制造方法,燃气轮机燃烧室喷嘴包括波纹管、安装在波纹管前端的扩散头、套接在波纹管的后部的法兰和前部的旋流器、连接在旋流器后端的气流环和连接在旋流器的前端的燃烧器管,波纹管包括本体和连接在本体的后端的延长管,波纹管与扩散头所组成的通道为扩散系统,法兰、波纹管、旋流器、气流环、燃烧器管之间所组成的通道为油气预混合系统,其包括以下步骤:步骤1、对本体与延长管进行预固定,之后转移到真空室中进行电子束焊接得到波纹管,在延长管与本体之间形成焊缝;步骤2、把旋流器套在波纹管并在该两者之间设置钎焊焊环后进行预固定,把扩散头的后端套在旋流器的前端的内环并在该两者之间设置钎焊焊环后进行预固定,把燃烧器管套在旋流器的前端的外环并在该两者之间设置钎焊焊环后进行预固定;步骤3、把步骤2中装配好的整体竖立放入真空炉中,抽真空后升温到1060-1070℃,在旋流器与波纹管之间形成焊缝,在旋流器与扩散头之间形成焊缝,在旋流器与燃烧器管之间形成焊缝,完成钎焊,得到钎焊组件;步骤4、先把气流环套进钎焊组件,之后对法兰进行加热使其膨胀,把波纹管套进膨胀后的法兰中;步骤5、对法兰与旋流器进行预固定,之后转移到真空室中进行电子束焊接,在法兰与旋流器之间形成焊缝;步骤6、对扩散系统和油气预混合系统进行压力测试;步骤7、对扩散系统和油气预混合系统进行空气流量测试;步骤8、
对气流环与旋流器进行预固定,之后转移到真空室中进行电子束焊接,在气流环与旋流器之间形成焊缝;步骤9、焊接法兰与延长管;步骤10、夹持旋流器的外圆,对法兰端面进行精车;步骤11、采用x光检测所有焊缝。
6.进一步地,在步骤1和/或步骤5和/或步骤8中,在进行电子束焊接前,采用点焊的方式对待焊接零部件进行预固定,且保证零部件间的间隙不超过0.05mm;电子束焊接前抽真空至5*10-4
torr以下。
7.进一步地,在步骤1中,进行两道电子束焊接,第一道的加速电压为50kv,束流为22ma,聚焦电流为聚焦后电流值-4ma,零部件转速为10r/min,缓变时上升为30ms,缓变时下降为50ms,第二道的加速电压为50kv,束流为10ma,聚焦电流为聚焦后电流值-15ma,零部件转速为10r/min,缓变时上升为30ms,缓变时下降为50ms;在步骤5中,进行三道电子束焊接,第一道的加速电压为50kv,束流为9ma,聚焦电流为聚焦后电流值+0ma,零部件转速为6.3r/min,缓变时上升为30ms,缓变时下降为50ms,第二道的加速电压为50kv,束流为32ma,聚焦电流为聚焦后电流值-4ma,零部件转速为6.3r/min,缓变时上升为30ms,缓变时下降为50ms,第三道的加速电压为50kv,束流为10ma,聚焦电流为聚焦后电流值-15ma,零部件转速为6.3r/min,缓变时上升为30ms,缓变时下降为50ms;在步骤8中,进行两道电子束焊接,第一道的加速电压为50kv,束流为22ma,聚焦电流为聚焦后电流值+2ma,零部件转速为3.9r/min,缓变时上升为30ms,缓变时下降为50ms,第二道的加速电压为50kv,束流为10ma,聚焦电流为聚焦后电流值-10ma,零部件转速为3.9r/min,缓变时上升为30ms,缓变时下降为50ms。
8.进一步地,在步骤2中,在波纹管前端的外周面设置第一环槽,把钎焊焊环放入第一环槽内,把旋流器套在波纹管并覆盖第一环槽,采用点焊的方式对旋流器与波纹管进行预固定;在旋流器的前端的内环外周面设置第二环槽,把钎焊焊环放入第二环槽内,扩散头后端加工形成阶梯结构,把扩散头的后端套在旋流器的前端的内环外周面并覆盖第二环槽,采用点焊的方式对旋流器与扩散头进行预固定;在旋流器的前端的外环外周面设置第三环槽,燃烧器管后端加工形成阶梯结构,把燃烧器管套在旋流器的前端的外环外周面并覆盖第三环槽,采用点焊的方式对旋流器与燃烧器管进行预固定。
9.进一步地,钎焊焊环的材料为ams4786。
10.进一步地,在步骤3中,抽真空至5*10-4
torr以下,之后按照9-13℃/min的速率升温到520-545℃,保温7-12min,再按照9-13℃/min的速率升温到910-940℃,保温60-65min,再按照9-13℃/min的速率升温到1060-1070℃,保温30-35min,再降温到840-850℃,充入氩气,再冷却至120-125℃,之后释放真空至常压。
11.进一步地,每次形成焊缝后,先目视检查焊缝析出是否正常,再使用荧光渗透法检测焊缝质量。
12.进一步地,在步骤6中,对扩散系统进行压力测试的方法为,封住扩散头端部的气孔,向波纹管通入氮气,把压力升至50psi后放入水中保压30s以上,看是否有气体渗出;对油气预混合进行压力测试的方法为,封住旋流器与法兰之间的开口和燃烧器管与扩散头之间的开口,从法兰上的斜孔通入氮气,把压力升至50psi后放入水中保压30s以上,看是否有气体渗出。
13.进一步地,在步骤7中,如检测到空气流量不足,则采用铰刀对系统内的气孔进行
铰大。
14.进一步地,进行步骤3时,一次往真空炉中放入多组装配好的整体;在进行步骤1和/或步骤5和/或步骤8时,设置多轴联动的支架,支架上安装多组待焊接零部件,在一次抽真空中对待焊接零部件进行逐个焊接。
15.本发明所提供的一种燃气轮机燃烧室喷嘴的制造方法,相比于现有技术,其采用电子束焊接、真空钎焊焊接以及过盈装配等工艺的配合,对不同零部件之间的焊接及定位选用不同的方式来进行,能够提高生产效率和焊接精度,同时,采用电子束焊接和真空钎焊焊接替代了传统的氩弧焊接后,能够避免零部件收缩量大、变形大和不同材料的零部件间焊接时膨胀尺寸不一的问题,提高了良率。
附图说明
16.图1是燃气轮机燃烧室喷嘴的剖视图;
17.图2是步骤1的示意图;
18.图3是步骤2的示意图;
19.图4是步骤4的示意图;
20.图5是步骤6的示意图。
21.【附图标记说明】
22.1-波纹管、11-本体、12-延长管;
23.2-扩散头;
24.3-法兰、31-法兰斜孔;
25.4-旋流器;
26.5-气流环;
27.6-燃烧器管;
28.7-气孔;
29.8-开口;
30.9-钎焊焊环。
具体实施方式
31.以下结合具体实施例对本发明作详细说明。
32.如图1所示,燃气轮机燃烧室喷嘴包括波纹管1、安装在波纹管1前端的扩散头2、套接在波纹管1的后部的法兰3和前部的旋流器4、连接在旋流器4后端的气流环5和连接在旋流器4的前端的燃烧器管6,波纹管1包括本体11和连接在本体11的后端的延长管12。
33.本发明提供了一种燃气轮机燃烧室喷嘴的制造方法,其包括以下步骤:
34.步骤1、如图2所示,先对本体11与延长管12进行预固定,之后转移到真空室中进行电子束焊接得到波纹管1,在延长管12与本体11之间形成焊缝。优选地,焊接前使用超声波对待焊接部件进行清洗,采用点焊的方式对待焊接零部件进行预固定,且保证零部件间的间隙不超过0.05mm,电子束焊接前抽真空至5*10-4
torr以下。然后进行两道电子束焊接,第一道的加速电压为50kv,束流为22ma,聚焦电流为聚焦后电流值-4ma,零部件转速为10r/min,缓变时上升为30ms,缓变时下降为50ms,第二道的加速电压为50kv,束流为10ma,聚焦
电流为聚焦后电流值-15ma,零部件转速为10r/min,缓变时上升为30ms,缓变时下降为50ms。焊接完后释放真空至常压,对焊接成品进行目视检测和荧光渗透法检测。
35.步骤2、把旋流器4套在波纹管1并在该两者之间设置钎焊焊环9后进行预固定,把扩散头2的后端套在旋流器4的前端的内环并在该两者之间设置钎焊焊环9后进行预固定,把燃烧器管6套在旋流器4的前端的外环并在该两者之间设置钎焊焊环9后进行预固定。优选地,如图3所示,在波纹管1前端的外周面设置第一环槽,把钎焊焊环9放入第一环槽内,把旋流器4套在波纹管1并覆盖第一环槽,采用点焊的方式对旋流器4与波纹管1进行预固定;在旋流器4的前端的内环外周面设置第二环槽,把钎焊焊环9放入第二环槽内,扩散头2后端加工形成阶梯结构,把扩散头2的后端套在旋流器4的前端的内环外周面并覆盖第二环槽,采用点焊的方式对旋流器4与扩散头2进行预固定;在旋流器4的前端的外环外周面设置第三环槽,燃烧器管6后端加工形成阶梯结构,把燃烧器管6套在旋流器4的前端的外环外周面并覆盖第三环槽,采用点焊的方式对旋流器4与燃烧器管6进行预固定。进一步优选地,钎焊焊环9的材料为ams4786。ams4786为金基钎料,易于保存,且保存期不受限制。采用焊环的形式容易装配且焊接均匀性好,适配本方法的使用场景。
36.步骤3、把步骤2中装配好的整体竖立放入真空炉中,抽真空至5*10-4
torr以下,之后按照9-13℃/min的速率升温到520-545℃,保温7-12min,再按照9-13℃/min的速率升温到910-940℃,保温60-65min,再按照9-13℃/min的速率升温到1060-1070℃,保温30-35min,再降温到840-850℃,充入氩气,再冷却至120-125℃,之后释放真空至常压。之后先目视检查焊缝析出是否正常,再使用荧光渗透法检测焊缝质量。
37.步骤4、如图4所示,先把气流环5套进钎焊组件,之后对法兰3进行加热到340-360℃,并保温50-70min,使其膨胀,之后,佩戴耐高温手套,使用胀紧式装配工装装进延长管12内并拉动延长管12,把波纹管1套进膨胀后的法兰3中,直到延长管12的端面紧贴在法兰3内孔端面。
38.步骤5、对法兰3与旋流器4进行预固定,之后转移到真空室中进行电子束焊接,在法兰3与旋流器4之间形成焊缝。优选地,焊接前使用酒精或无尘纸对待焊接部件进行清洗,采用点焊的方式对待焊接零部件进行预固定,且保证零部件间的间隙不超过0.05mm,电子束焊接前抽真空至5*10-4
torr以下。然后进行三道电子束焊接,第一道的加速电压为50kv,束流为9ma,聚焦电流为聚焦后电流值+0ma,零部件转速为6.3r/min,缓变时上升为30ms,缓变时下降为50ms,第二道的加速电压为50kv,束流为32ma,聚焦电流为聚焦后电流值-4ma,零部件转速为6.3r/min,缓变时上升为30ms,缓变时下降为50ms,第三道的加速电压为50kv,束流为10ma,聚焦电流为聚焦后电流值-15ma,零部件转速为6.3r/min,缓变时上升为30ms,缓变时下降为50ms。焊接完后释放真空至常压,对焊接成品进行目视检测和荧光渗透法检测。
39.步骤6、对扩散系统和油气预混合系统进行压力测试。扩散系统即波纹管1与扩散头2所组成的通道,油气预混合系统即法兰3、波纹管1、旋流器4、气流环5、燃烧器管6之间所组成的通道。如图5所示,优选地,对扩散系统进行压力测试的方法为,封住扩散头2端部的气孔7,向波纹管1通入氮气,把压力升至50psi后放入水中保压30s以上,看是否有气体渗出。对油气预混合进行压力测试的方法为,封住旋流器4与法兰3之间的开口8和燃烧器管6与扩散头2之间的开口8,从法兰斜孔31通入氮气,把压力升至50psi后放入水中保压30s以
上,看是否有气体渗出。
40.步骤7、对扩散系统和油气预混合系统进行空气流量测试。如检测到空气流量不足,则采用铰刀对系统内的气孔7进行铰大。在预制带气孔7的零部件时,把气孔7稍微做小,方便后续进行铰大。
41.步骤8、对气流环5与旋流器4进行预固定,之后转移到真空室中进行电子束焊接,在气流环5与旋流器4之间形成焊缝。气流环5与旋流器4之间的焊接放在两款测试之后,主要是因为一旦气流环5提前焊接好了,会阻碍气体渗出的观察,也会阻碍铰刀对气孔7铰大的施工,为此,本方案中把气流环5的焊接调后了。优选地,焊接前使用酒精或无尘纸对待焊接部件进行清洗,采用点焊的方式对待焊接零部件进行预固定,且保证零部件间的间隙不超过0.05mm,电子束焊接前抽真空至5*10-4
torr以下。然后,进行两道电子束焊接,第一道的加速电压为50kv,束流为22ma,聚焦电流为聚焦后电流值+2ma,零部件转速为3.9r/min,缓变时上升为30ms,缓变时下降为50ms,第二道的加速电压为50kv,束流为10ma,聚焦电流为聚焦后电流值-10ma,零部件转速为3.9r/min,缓变时上升为30ms,缓变时下降为50ms。焊接完后释放真空至常压,对焊接成品进行目视检测和荧光渗透法检测。
42.步骤9、焊接法兰3与延长管12。此处采用氩弧焊焊接即可,可提高效率,焊接完后对焊接成品进行目视检测和荧光渗透法检测。
43.步骤10、夹持旋流器4的外圆,对法兰3端面进行精车。
44.步骤11、采用x光检测所有焊缝。检测出在各类测试、装配和机加工后可能出现的焊缝损伤,保证最终成品的质量。
45.优选地,进行步骤3时,一次往真空炉中放入多组装配好的整体;在进行步骤1和/或步骤5和/或步骤8时,设置多轴联动的支架,支架上安装多组待焊接零部件,在一次抽真空中对待焊接零部件进行逐个焊接。通过上述的设置,本方案在步骤3和步骤1、5、8中均可同时对多个零部件进行焊接,由于这些步骤中都需要进行抽真空处理,而抽真空所花费的时间较长,为此,本方案设置在这些步骤中同时处理多个零部件,可以减少批量生产时抽真空所花费的时间,提高生产效率。
46.优选地,目视检测包括检查是否有焊接缺陷,例如焊接弧坑、咬边、气孔、填充不饱满等缺陷,还要检查焊缝余高尺寸是否满足要求,角焊缝还要检查焊角尺寸是否满足规范要求。荧光渗透法检测包括检查焊缝表面有无裂纹等缺陷。
47.结合上述的步骤设置,本方法相对于现有技术存在以下优势:
48.1、燃气轮机燃烧室喷嘴由哈氏合金、镍基合金等难熔金属组成,使用电子束焊接工艺可以焊接这类难熔金属,焊缝成型好;电子束焊接时束流功率密度极高,焊接速度快,焊缝的深宽比大,因而零部件的变形极小,焊缝的热影响区很窄,焊接后零部件的收缩量很少;电子束焊接是在真空室中进行的,排除了大气中有害气体对熔融金属的影响,因此,熔融金属成分纯净,提高了焊缝质量;电子束焊接速度快,通过改造工装夹具,实现了一次焊接多组零部件,大大提高了生产效率;
49.2、采用本方法所提供的钎焊焊环作为钎焊材料,其熔点比母材的熔点低,施工性能好,母材的材质变化和结构的变形都比较小,从而保证产品的高制造精度;燃气轮机燃烧室喷嘴由包含不锈钢、哈氏合金、镍基合金等材料的零部件组成,使用钎焊工艺能够很好保证这些异种材料之间良好的连接性能;同时,采用钎焊工艺可以在步骤3中一次批量焊接多
组零部件,焊接效率高。
50.采用传统的方法制造燃气轮机燃烧室喷嘴时,不良率为3%-5%,采用本发明所提供的燃气轮机燃烧室喷嘴的制造方法后,经统计,不良率降至低于1%。
51.综上,该种燃气轮机燃烧室喷嘴的制造方法不良率低,且生产效率高。
52.在不冲突的情况下,上述的实施例及实施例中的特征可以相互组合。
53.最后应当说明的是,以上实施例仅用以说明本发明的技术方案,而非对本发明保护范围的限制,尽管参照较佳实施例对本发明作了详细地说明,本领域的普通技术人员应当理解,可以对本发明的技术方案进行修改或者等同替换,而不脱离本发明技术方案的实质和范围。