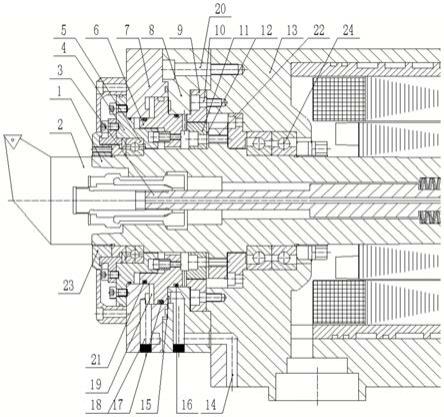
1.本发明属于机械制造机床技术领域,具体地说,涉及一种数控摆头车铣复合主轴。
背景技术:2.作为机械加工领域中两种最基本的加工成型手段,车削和铣削的工作原理截然不同。车削为工件旋转、车刀在平面内做直线或曲线移动的切削加工,而铣削为刀具旋转(作主运动)、工件移动(作进给运动)或固定的切削加工。
3.鉴于车削和铣削的区别,可实现复合加工的数控加工中心一般价格高昂,而且目前市面上所存在的摆头车铣复合主轴普遍存在刹车不牢靠、刚性不高、震动大等问题,这不仅会使支撑摆头车铣复合主轴的轴承丧失其刚性,大幅缩短其使用周期甚至直接报废,从而增加生产及使用成本,而且会降低摆头车铣复合主轴的工作精度,为生产加工带来许多的不便。
技术实现要素:4.本发明所要解决的技术问题在于:针对因现有市场摆头车铣复合主轴普遍存在的刹车不稳、刚性不高、震动大所导致的轴承使用寿命大幅缩短的问题,提供了一种新型摆头车铣复合主轴,具有震动小、刚性高、加工精度高、轴承使用寿命长、成本低的特点。
5.为解决上述技术问题,本发明采用以下技术方案:
6.一种数控摆头车铣复合机床刹车主轴,包括主轴、穿过主轴内孔的拉杆、主轴制动锁紧机构,所述主轴制动锁紧机构由第一刹车缸、第二刹车缸、活塞锁紧齿盘、固定齿盘、旋转齿盘组成;所述第二刹车缸、所述固定齿盘与壳体固定连接,所述旋转齿盘与主轴固定连接并可随主轴旋转,所述活塞锁紧齿盘的一端面与第一刹车缸形成第一油腔,另一端面与第二刹车缸构成第二油腔,通过控制两个油腔的压力进而控制活塞锁紧齿盘与固定齿盘、旋转齿盘的分离和啮合,以实现车削与铣削功能。
7.作为进一步的技术方案,所述活塞锁紧齿盘将锁紧齿与活塞做成整体。
8.作为进一步的技术方案,所述第二刹车缸的端面开有油槽,该油槽与活塞锁紧齿盘的端面共同构成第二油腔。
9.作为进一步的技术方案,所述活塞锁紧齿盘突出部分的外圆槽安装有o型垫圈,与刹车缸内止口紧配合,将第一油腔和第二油腔分开成两个独立的油腔。
10.作为进一步的技术方案,所述固定齿盘开有螺纹孔,与壳体固定连接。
11.作为进一步的技术方案,所述的固定齿盘与旋转齿盘为间隙配合。
12.作为进一步的技术方案,所述旋转齿盘与主轴突出法兰固定连接。
13.作为进一步的技术方案,所述固定齿盘齿面与旋转齿盘的齿面平齐。
14.作为进一步的技术方案,所述活塞锁紧齿盘的齿面可同时和固定齿盘齿面、旋转齿盘齿面啮合。
15.作为进一步的技术方案,所述主轴前端装有辅助支撑轴承,通过锁紧螺母将辅助
支撑轴承锁紧在与第一刹车缸固定的辅助支撑座内。
16.与现有技术相比,本发明的有益效果是:
17.本发明通过控制第一油腔、第二油腔的油压,当第一油腔的压力大于第二油腔的压力时,使得锁紧刹车盘可以同时与固定齿盘、旋转齿盘啮合,在圆周方向上具有足够防止轴旋转的力矩,保证了刹车的可靠性,实现车削;当第一油腔的压力小于第二油腔的压力时,活塞锁紧齿盘向左移动,活塞锁紧齿盘与固定齿盘和旋转齿盘脱离啮合,旋转齿盘跟随主轴1同时旋转,主轴前端刀具更换为铣刀,刀具与主轴保持同步高速旋转,此时为铣削工作状态。同时且将活塞与锁紧齿做成整体,减小了刹车装置的安装空间,减小主轴的整体体积,降低成本。本发明刹车可靠,使用寿命长、精度高、具有较好的经济适用性。主轴前端另加辅助轴承进行支撑,从而避免了刹车过程的震动,也加强了主轴的刚性,既保证了工件的加工精度与光洁度,也提高了刀具的使用寿命,
附图说明
18.图1为本发明的整体结构示意图;
19.图2为本发明的活塞锁紧齿盘示意图;
20.图中:1、主轴;2、刀柄;3、拉杆;4、前支撑座;5、第一支承轴承;6、活塞锁紧齿盘;6-1活塞;6-2锁紧齿,7、第一刹车缸;8、第二刹车缸;9、固定齿盘;10、螺钉;11、旋转齿盘;12、齿高调整垫;13、壳体;14、第二进油口;15、第二油腔;16、第一o型垫圈;17、第二o型垫圈;18、第一进油口;19、第一油腔;20、螺钉;21、第三o型垫圈;22、螺钉;23、锁紧螺母;24、第二支撑轴承。
具体实施方式
21.为了便于理解本发明,下面将参照附图对数控摆头车铣复合主轴进行更全面的描述。附图中给出了数控摆头车铣复合主轴的优选实施例。但是,数控摆头车铣复合主轴可以通过各种不同的形式来实现,并不限于本文所描述的实施例。相反的,提供这些实施例的目的是使对数控摆头车铣复合主轴的公开内容展示的更加透彻全面。
22.需要说明的是,当元件被称为“固定于”另一个元件,它可以直接在另一个元件上或者也可以存在居中的元件。当一个元件被认为是“连接”另一个元件,它可以是直接连接到另一个元件或者可能同时存在居中元件。相反,当元件被称作“直接在”另一元件“上”时,不存在中间元件。本文说使用的疏于“垂直的”、“水平的”、“左”、“右”以及类似的表述只是为了说明的目的。
23.除非另有定义,本发明所使用的所有的技术和科学术语与属于本发明的技术领域的技术人员通常理解的含义相同。本文中在数控摆头车铣复合主轴的说明书中所使用的术语只是为了描述具体的实施例的目的,不是旨在限制本发明。本文所使用的术语“及/或”包括一个或多个相关的所列项目的任意的和所有的组合。
24.正如背景技术部分所描述的,本实施例公开了一种数控摆头车铣复合机床刹车主轴,包括主轴、穿过主轴内孔的拉杆、主轴制动锁紧机构,所述主轴制动锁紧机构由第一刹车缸、第二刹车缸、活塞锁紧齿盘、固定齿盘、旋转齿盘组成;所述第二刹车缸、所述固定齿盘与壳体固定连接,所述旋转齿盘与主轴固定连接并可随主轴旋转,所述活塞锁紧齿盘的
一端面与第一刹车缸形成第一油腔,另一端面与第二刹车缸构成第二油腔,通过控制两个油腔的压力进而控制活塞锁紧齿盘与固定齿盘、旋转齿盘的分离和啮合,以实现车削与铣削功能。本发明还可安装在工作台上,扩大工艺范围,且结构紧凑,整体安装空间小,刹车牢靠,振动小,刚度大,提高了加工精度与使用寿命,具有良好的经济适用性。
25.实施例1
26.请结合参阅图1,数控摆头车铣复合主轴具有主轴1、刀柄2、拉杆3、前支撑座4、支承轴承5、活塞锁紧齿盘6、第一刹车缸7、第二刹车缸8、固定齿盘9、螺钉10、旋转齿盘11、齿高调整垫12、壳体13、第一o型垫圈16、第二o型垫圈17、螺钉20、第三o型垫圈21、螺钉22、锁紧螺母23、支撑轴承24等关键零部件。
27.主轴1作为本发明的工作元件,用来带动铣刀旋转工作或连接车刀进行车削,在本实施例中,主轴内孔装有拉杆3,由拉杆3将车刀柄拉紧在主轴前端锥孔内;锁紧螺母23与主轴前端的螺纹构成螺纹副将支撑轴承5固定在主轴前端。第一刹车缸7与第二刹车缸8由止口配合用螺钉固定连接;旋转齿盘11与齿高调整垫12通过螺钉22固定在主轴1法兰位置上,旋转齿盘11可随着主轴1进行旋转,即旋转齿盘11连接在主轴1法兰上与主轴1保持相同的运动状态。
28.进一步的,本实施例中的固定齿盘9设置在旋转齿盘11的外圈,且固定齿盘9通过螺钉10固定在壳体13上,即固定齿盘9连接在壳体上与壳体保持静止运动状态,且固定齿盘9、旋转齿盘11的齿面位于同一平面上,可以同时与活塞锁紧齿盘6进行啮合。
29.进一步的,第二刹车缸8通过螺钉20固定在壳体13上,且以图1所示的方位为例,本实施例中第二刹车缸8左端面开有油槽,第二刹车缸8的右端面与壳体13、固定齿盘9贴合。
30.进一步的,前支撑座安装在第一刹车缸7上,前支撑座4和主轴1之间装有第一支撑轴承5,第一支撑轴承5作为辅助轴承,承担了刹车时的部分轴向力,减小了第二支撑轴承24承受的轴向力。锁紧螺母23与主轴1前端的螺纹构成螺纹副,将第一支撑轴承5固定在前支撑座4内,从而避免了刹车过程的震动,也加强了主轴的刚性,既保证了工件的加工精度与光洁度,也提高了刀具的使用寿命。
31.进一步,本实施例中的活塞锁紧齿盘6是将锁紧齿与活塞作为整体,如图2所示,包括活塞6-1和锁紧齿6-2,两者一体成型,通过一体成型减小了锁紧机构的体积,节省了安装空间,实现对旋转齿盘的锁紧;锁紧齿盘放置于第一刹车缸7与第二刹车缸8之间,在活塞锁紧齿盘6右端面紧靠第二刹车缸8,第二刹车缸8左端面开有油槽,与活塞锁紧齿盘右端面构成第二油腔15,活塞锁紧齿盘6的左端面与第一刹车缸7形成第一油腔19;活塞锁紧齿盘6突出部分的外圆槽安装有第二o型垫圈17,与第一刹车缸7内止口紧配合,将第一油腔19和第二油腔15分开成两个独立的油腔。
32.进一步,活塞锁紧齿盘6的突出部分两端外圆的凹槽内安装第一o型垫圈16、第三o型垫圈21,与两个刹车缸内孔过盈紧配合,阻止两油腔的油向外部泄漏。
33.进一步的,在壳体13上设有第二进油口14,第二进油口14通过设置在壳体13内的油道和设置在第二刹车缸8的油道与第二油腔15连通;在第一刹车缸17上设有第一进油口18,第一进油口18通过设置在第一刹车缸17内的油道与第一油腔19连通。
34.本实施例公开的装置,其工作原理如下:
35.液压油通过第二进油口14进入第二油腔15,通过第一进油口18进入第一油腔19,
通过调节第一油腔和第二油腔的压力大小,控制活塞锁紧齿盘6的左右移动。当第一油腔19的压力大于第二油腔15的压力时,活塞锁紧齿盘6向右移动,同时与固定齿盘9和旋转齿盘11啮合。在圆周方向上产生足够防止主轴1旋转的力矩,主轴静止,此时为车削工作状态。当第一油腔19的压力小于第二油腔15的压力时,活塞锁紧齿盘6向左移动,活塞锁紧齿盘6与固定齿盘9和旋转齿盘11脱离啮合,旋转齿盘11跟随主轴1同时旋转,主轴前端刀具更换为铣刀,刀具与主轴保持同步高速旋转,此时为铣削工作状态。
36.以上所述仅为本发明的优选实施例而已,并不用于限制本发明,对于本领域的技术人员来说,本发明可以有各种更改和变化。凡在本发明的精神和原则之内,所作的任何修改、等同替换、改进等,均应包含在本发明的保护范围之内。