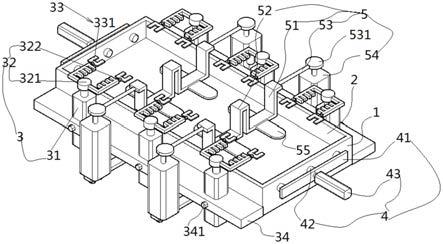
1.本实用新型涉及电池外壳焊接加工装置,尤其涉及的是一种电池壳体生产装置。
背景技术:2.随着新能源的发展,电池供能提供动力逐渐应用到新能源汽车上,用于电池外壳提供动力。
3.由于新能源汽车供给电力动力较大,因此,组成动力电池数量较多,因此,安装动力电池的安装壳体的体积较大。在动力电池安装壳体加工过程中,经常由于操作人员误操作导致工件壳体变形,具体时,工件壳体上的容纳电池模块的容纳槽受到不均匀作用力时容易变形,变形后无法轻易的复位。
4.造成上述技术缺陷的实质原因在于:现有技术中并未公开一种工装夹具装置,能够将壳体工件在加工过程中充分支撑定位,避免变形。
技术实现要素:5.本实用新型所要解决的技术问题在于提供了一种电池壳体生产装置。
6.本实用新型是通过以下技术方案解决上述技术问题的:
7.一种电池壳体生产装置,包括加工夹具台,所述加工夹具台的顶部开设有限位槽;
8.所述加工夹具台上装配连接有若干个左右间隔设置的壳体支持部件,所述壳体支持部件均包括多段u形支持杆,所述多段u形支持杆包括若干个前后间隔设置的u形部,所述u形部的开口朝上设置;
9.所述u形部之间通过若干个前后间隔设置的连接部一体成型;
10.所述多段u形支持杆的前后两端均固定连接有连杆,所述连杆的端部固定连接有端座盘体,所述端座盘体的底部装配连接有气缸。
11.优选地,所述加工夹具台前后两侧均装配连接有相互配合的定位夹持部件;
12.所述定位夹持部件包括固定连接在加工夹具台侧壁上的安装台板,所述安装台板上装配连接有若干个左、右间隔设置的定位气缸,所述定位气缸的活塞杆顶部固定连接有u形定位件,所述u形定位件包括固定连接在定位气缸活塞杆上的u形杆,所述u形杆的内侧壁上固定连接有若干个前、后间隔设置的定位端头杆;
13.所述定位气缸的缸筒装配连接在安装台板上。
14.优选地,所述u形部的底部均固定连接有两个左右对称设置的定位板。
15.优选地,位于前后部位所述气缸的缸筒底部之间装配连接有连桥板,所述连桥板的顶部通过若干个前后间隔设置的连接柱固定连接在加工夹具台的底部。
16.优选地,所述定位气缸的活塞杆顶部固定连接有端座,所述u形杆固定连接在端座上,所述u形杆贯穿所述端座。
17.优选地,所述安装台板上开设有若干个左右间隔设置的装配通孔,所述定位气缸的缸筒装配连接在装配通孔内,所述安装台板上螺纹连接有定位螺栓,所述定位螺栓螺纹
连接在定位气缸的缸筒。
18.优选地,所述u形杆的左右端部均装配连接有端部定位部件;
19.端部定位部件均包括螺纹连接在u形杆上的螺杆,所述螺杆的端部螺纹连接有u形按压杆。
20.优选地,所述u形按压杆上固定连接有螺纹筒,所述螺纹筒螺纹连接在螺杆上。
21.优选地,所述加工夹具台的左右两端均装配连接有工件端部挤压定位部件。
22.优选地,所述工件端部挤压定位部件均包括端头条板,所述端头条板的内侧壁上固定连接有若干个定位柱,所述定位柱贯穿所述加工夹具台并位于限位槽内,所述端头条板的外侧壁固定连接有推动气缸。
23.本实用新型相比现有技术具有以下优点:
24.本实用新型公开一种电池壳体生产装置,通过设计加工夹具台,加工夹具台的顶部开设有限位槽;加工夹具台上装配连接有若干个左右间隔设置的壳体支持部件,所述壳体支持部件均包括多段u形支持杆,所述多段u形支持杆包括若干个前后间隔设置的u形部,所述u形部的开口朝上设置;u形部之间通过若干个前后间隔设置的连接部一体成型;多段u形支持杆的前后两端均固定连接有连杆,所述连杆的端部固定连接有端座盘体,所述端座盘体的底部装配连接有气缸,实现将电池壳体工件进行支撑加工。
25.采用上述装置部件设计不仅实现充分将装配电池的大体积壳体工件进行支撑,避免加工过程中工件变形,切上述装置部件设计能够定位夹持工件,且上述装置部件设计操作方便,能够快速、高效、稳定的将工件定位焊接,提高了工件的加工焊接效率。
附图说明
26.图1是本实用新型实施例的整体结构示意图;
27.图2是本实用新型实施例中u形定位件的结构示意图;
28.图3是本实用新型实施例中壳体支持部件的结构示意图;
29.图4是本实用新型实施例中图1中另一种视角下的结构示意图;
30.图5是本实用新型实施例图1中的俯视图。
具体实施方式
31.下面对本实用新型的实施例作详细说明,本实施例在以本实用新型技术方案为前提下进行实施,给出了详细的实施方式和具体的操作过程,但本实用新型的保护范围不限于下述的实施例。
32.如图1
‑
5所示,一种电池壳体生产装置,包括加工夹具台1,所述加工夹具台1的顶部开设有限位槽2;加工的壳体工件放置在限位槽2中。
33.在加工壳体过程中,为了避免壳体工件(壳体工件为矩形,工件上具有若干个容纳电池快的容纳槽,容纳槽由壳体工件上若干个垂直板形成,壳体工件上具有壳体工件槽,通过若干个垂直板形成容纳槽,加工中,容纳槽容易变形)在加工过程中变形,上述加工夹具台上1装配连接有若干个左、右间隔设置的壳体支持部件5,所述壳体支持部件5均包括多段u形支持杆,所述多段u形支持杆包括若干个前后间隔设置的u形部51,所述u形部51的开口朝上设置。
34.上述u形部51之间通过若干个前后间隔设置的连接部52一体成型。上述多段u形支持杆的前后两端均固定连接有连杆53,所述连杆53的端部固定连接有端座盘体531,所述端座盘体531的底部装配连接有气缸54。
35.将壳体工件放置到限位槽2中,此时,打开气缸54,气缸54驱动壳体支持部件5下降,由于壳体支持部件5下降后,壳体支持部件5上的u形部51下降并支持在壳体工件内的容纳槽内,此时,在u形部51的支撑下(u形部51支撑在壳体工件上构成容纳槽的垂直板侧壁上),工件不容易变形。
36.上述位于前后部位所述气缸54的缸筒底部之间装配连接有连桥板56,所述连桥板56的顶部通过若干个前、后间隔设置的连接柱561固定连接在加工夹具台的底部。
37.实际工作过程中,为了在支撑过程中,定位壳体工件,上述u形部51的底部均固定连接有两个左、右对称设置的定位板55,通过定位板55实现定位壳体。
38.由于壳体工件的体积较大,实际工作中,为了充分定位住工件,便于加工,上述加工夹具台1前后两侧均装配连接有相互配合的定位夹持部件3(定位夹持部件3与上述壳体支持部件5交错设置)。
39.定位夹持部件3的具体结构如下:
40.所述定位夹持部件3包括固定连接在加工夹具台1侧壁上的安装台板34(下述定位气缸31的缸筒装配连接在安装台板34上,具体是,安装台板34上开设有若干个左右间隔设置的装配通孔,所述定位气缸31的缸筒装配连接在装配通孔内,所述安装台板34上螺纹连接有定位螺栓341,所述定位螺栓341螺纹连接在定位气缸31的缸筒)。
41.上述安装台板34上装配连接有若干个左、右间隔设置的定位气缸31,所述定位气缸31的活塞杆顶部固定连接有u形定位件32,所述u形定位件32包括固定连接在定位气缸31活塞杆上的u形杆,所述u形杆的内侧壁上固定连接有若干个前、后间隔设置的定位端头杆322。
42.具体时,定位气缸31的活塞杆顶部固定连接有端座321,所述u形杆固定连接在端座321上,所述u形杆贯穿所述端座321。
43.当工件放置到限位槽2中,此时,打开所有定位气缸31至定位气缸31驱动u形定位件32定位在工件的侧边部位,在u形定位件32上u形杆以及定位端头杆322的多个定位位点定位下,体积较大的工件能够充分定位。
44.实际工作过程中,由于壳体工件的尺寸大小有差距,为了针对尺寸小的工件充分定位,上述u形杆的左右端部均装配连接有端部定位部件33。
45.端部定位部件33的具体结构如下:
46.端部定位部件33均包括螺纹连接在u形杆上的螺杆333(u形杆上开设与螺杆333适配的螺纹槽),所述螺杆333的端部螺纹连接有u形按压杆331。u形按压杆331上固定连接有螺纹筒332,所述螺纹筒332螺纹连接在螺杆333上。
47.通过上述设计实现延长定位位置,进而方便将尺寸小的工件能够定位到,具体是,需要定位尺寸小的工件时,将u形杆螺纹连接到螺杆333上,实现通过u形杆将工件定位。
48.上述加工夹具台1的左右两端均装配连接有工件端部挤压定位部件4。工件端部挤压定位部件4均包括端头条板41,所述端头条板41的内侧壁上固定连接有若干个定位柱42,所述定位柱42贯穿所述加工夹具台1并位于限位槽2内,所述端头条板41的外侧壁固定连接
有推动气缸43。
49.同时,按照现有常规方式,推动气缸43的缸筒装配连接有u形安装板(图中未画出),所述u形安装板的左右两端固定连接在加工夹具台1的侧壁上。
50.工件放置到限位槽2内,尤其是尺寸小的工件,为了实现将工件的左右两侧挤压定位,打开推动气缸43,推动气缸43驱动端头条板41,进而端头条板41推动定位柱42将工件挤压定位在壳体工件上。
51.采用上述装置部件设计不仅实现充分将装配电池的大体积壳体工件进行支撑,避免加工过程中工件变形,切上述装置部件设计能够定位夹持工件,且上述装置部件设计操作方便,能够快速、高效、稳定的将工件定位焊接,提高了工件的加工焊接效率。
52.以上所述仅为本实用新型的较佳实施例而已,并不用以限制本实用新型,凡在本实用新型的精神和原则之内所作的任何修改、等同替换和改进等,均应包含在本实用新型的保护范围之内。