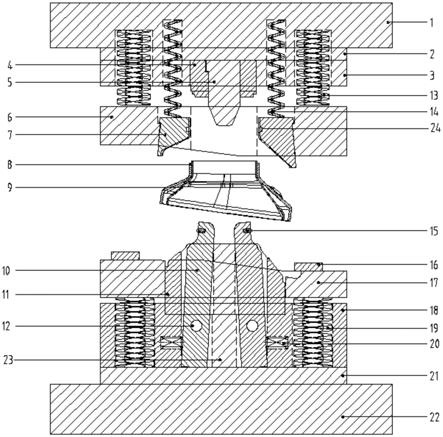
1.本实用新型涉及模具技术领域,具体地说是一种汽车排气端锥类零件的点铆接模具。
背景技术:2.随着汽车工业的高速发展,汽车模具制造行业竞争也日趋激烈,相应的需要降低生产制造成本,提高工作效率,提升产品质量,持续改进冲压及模具工艺。
3.常见的排气端锥类零件是以焊接工艺为主,为满足焊接要求往往需要建立焊接工艺生产线,实际生产中需要占用过多的机床、人工等中间环节。
4.因此,设计一种汽车排气端锥类零件的点铆接模具,不需要焊接也可以把汽车排气类端锥相互紧配,降低生产成本,提高工作效率。
技术实现要素:5.本实用新型为克服现有技术的不足,设计一种汽车排气端锥类零件的点铆接模具,充分利用机床力,有效替代了常规的焊接工艺,节约了大量的焊接成本,并且点铆接完成后可以自动脱料,复位,节省了人力物力,提高了工作效率。
6.为实现上述目的,设计一种汽车排气端锥类零件的点铆接模具,包括上模、下模,上模下方设有下模,其特征在于:所述的上模包括上模座、上垫板、上夹板、驱动冲头、上脱板、成型块,上模座下端连接上垫板上端,上垫板下端连接上夹板上端,上夹板下方设有上脱板,位于上夹板中心设有第一型腔,第一型腔内设有驱动冲头,位于上脱板中心设有第二型腔,第二型腔内的左右两侧分别设有成型块,成型块内侧设有凹槽,所述的下模包括下模座、下垫板、下模板、下脱板、成型旋转块、第一限位块、定位块,所述的下模座上端连接下垫板下端,下垫板上端连接下模板下端,下模板上端设有下脱板,位于下模板内中心设有第三型腔,第三型腔内的左右两侧分别转动连接成型旋转块,成型旋转块上部外端设有凸点冲头,成型旋转块下部外侧设有侧推弹簧一端,侧推弹簧另一端位于下模板内,左右两侧成型旋转块之间设有第一限位块,位于下脱板中心设有第四型腔,第四型腔内的左右两侧分别设有定位块。
7.所述的驱动冲头与第一型腔内壁之间设有夹板镶件。
8.所述的驱动冲头上端抵接上垫板下端面,驱动冲头下端与左右两侧的成型旋转块接触或者分离。
9.所述的上脱板上端连接上脱料弹簧一端,上脱料弹簧另一端分别贯穿上夹板、上脱板、上模座下端,并位于上模座内。
10.所述的成型块上端连接浮块弹簧的一端,浮块弹簧的另一端分别贯穿上夹板、上脱板、上模座下端,并位于上模座内。
11.所述的成型旋转块下端抵接下垫板上端,成型旋转块下部通过旋转轴与下模板转动连接,成型旋转块上部位于下模板上方。
12.所述的下脱板上端设有第二限位块。
13.所述的下脱板下端连接下脱料弹簧的一端,下脱料弹簧的另一端贯穿下模板并抵接下垫板上端。
14.所述的凹槽的形状、位置与凸点冲头的形状、位置相配合。
15.本实用新型同现有技术相比,充分利用机床力,有效替代了常规的焊接工艺,节约了大量的焊接成本,并且点铆接完成后可以自动脱料,复位,节省了人力物力,提高了工作效率。
附图说明
16.图1为本实用新型上模与下模开模时的结构示意图。
17.图2为本实用新型外端锥、内端锥固定在上模、下模之间的结构示意图。
18.图3为本实用新型上模与下模闭模时的结构示意图。
19.图4为本实用新型外端锥的结构示意图。
20.图5为本实用新型外端锥的俯视图。
21.图6为本实用新型内端锥的结构示意图。
22.图7为本实用新型内端锥的俯视图。
23.图8为本实用新型内端锥、外端锥点铆接后的结构示意图。
24.图9为本实用新型内端锥、外端锥点铆接后的俯视图。
25.参见图1至图9,其中,1是上模座,2是上垫板,3是上夹板,4是夹板镶件,5是驱动冲头,6是上脱板,7是成型块,8是外端锥,9是内端锥,10是成型旋转块,11是定位块,12是旋转轴,13是上脱料弹簧,14是浮块弹簧,15是凸点冲头,16是第二限位块,17是下脱板,18是下模板,19是下脱料弹簧,20是侧推弹簧,21是下垫板,22是下模座,23是第一限位块,24是凹槽。
具体实施方式
26.下面根据附图对本实用新型做进一步的说明。
27.如图1至图3所示,上模包括上模座1、上垫板2、上夹板3、驱动冲头5、上脱板6、成型块7,上模座1下端连接上垫板2上端,上垫板2下端连接上夹板3上端,上夹板3下方设有上脱板6,位于上夹板3中心设有第一型腔,第一型腔内设有驱动冲头5,位于上脱板6中心设有第二型腔,第二型腔内的左右两侧分别设有成型块7,成型块7内侧设有凹槽24,所述的下模包括下模座、下垫板、下模板、下脱板、成型旋转块、第一限位块、定位块,所述的下模座22上端连接下垫板21下端,下垫板21上端连接下模板18下端,下模板18上端设有下脱板17,位于下模板18内中心设有第三型腔,第三型腔内的左右两侧分别转动连接成型旋转块10,成型旋转块10上部外端设有凸点冲头15,成型旋转块10下部外侧设有侧推弹簧20一端,侧推弹簧20另一端位于下模板18内,左右两侧成型旋转块10之间设有第一限位块23,位于下脱板17中心设有第四型腔,第四型腔内的左右两侧分别设有定位块11。
28.驱动冲头5与第一型腔内壁之间设有夹板镶件4。
29.驱动冲头5上端抵接上垫板2下端面,驱动冲头5下端与左右两侧的成型旋转块10接触或者分离。
30.上脱板6上端连接上脱料弹簧13一端,上脱料弹簧13另一端分别贯穿上夹板3、上脱板6、上模座1下端,并位于上模座1内。
31.成型块7上端连接浮块弹簧14的一端,浮块弹簧14的另一端分别贯穿上夹板3、上脱板6、上模座1下端,并位于上模座1内。
32.成型旋转块10下端抵接下垫板21上端,成型旋转块10下部通过旋转轴12与下模板18转动连接,成型旋转块10上部位于下模板18上方。
33.下脱板17上端设有第二限位块16。
34.下脱板17下端连接下脱料弹簧19的一端,下脱料弹簧19的另一端贯穿下模板18并抵接下垫板21上端。
35.凹槽24的形状、位置与凸点冲头15的形状、位置相配合。
36.夹板镶件4起到固定驱动冲头5的作用。
37.成型块7、定位块11、上脱板6、下脱板17的结构与内端锥9、外端锥8的结构相配合。
38.外端锥8的结构如图4
‑
5所示,内端锥9的结构如图6
‑
7所示,外端锥8与内端锥9点铆接的位置根据需求确定。并且凸点冲头15的位置、凹槽24的位置与外端锥8与内端锥9点铆接的位置相配合。
39.上模在机床的作用力下完成下压。
40.如图1至图3所示,本实用新型的外端锥8与内端锥9点铆接时,包括如下步骤:
41.s1,装配外端锥8与内端锥9,并将装配好的外端锥8与内端锥9定位在定位块11上;
42.s2,上模下压,下压过程中,上脱板6内的成型块7接触到外端锥8与内端锥9时受阻力回推,成型块7的脱料行程,即浮块弹簧14的脱料行程量;
43.s3,上模继续下压,上脱板6抵接第二限位块16,并在第二限位块16的回推力下回推,上脱板6的脱料行程,即上脱料弹簧13的脱料行程量;
44.s4,上模继续下压至上模与下模完全闭合,左右两侧成型块7抵接外端锥8与内端锥9上部,上脱板6下端抵接第二限位块16,驱动冲头5下端穿过外端锥8与内端锥9中心并且插入左右两侧成型旋转块10之间,左右两侧成型旋转块10旋转轴12旋转,将侧推弹簧20拉出,同时凸点冲头15抵接内端锥9后在驱动冲头5、成型块7的侧向压力进行点铆接;
45.s5,点铆接完成后,上模上行,下脱板17和第二限位块16在下脱料弹簧19的浮升状态下恢复自由状态,成型旋转块10在侧推弹簧20的侧推力下复位,成型块通过浮块弹簧14完成脱料,上脱板6通过上脱料弹簧13完成脱料;
46.s6,取下点铆接完成的外端锥8与内端锥9。
47.具体使用时,可以根据所需的点铆接形状及大小,控制凸点冲头15、成型块7、凹槽24的形状、尺寸。
48.本实用新型充分利用机床力,有效替代了常规的焊接工艺,节约了大量的焊接成本,并且点铆接完成后可以自动脱料,复位,节省了人力物力,提高了工作效率。