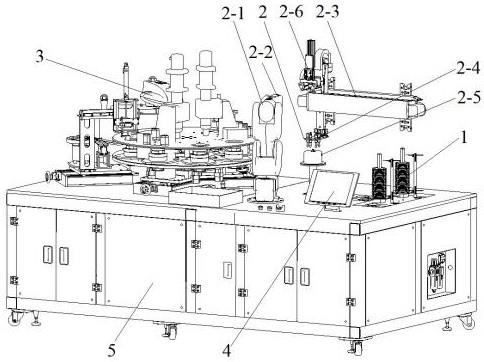
1.本实用新型属于离合器专用设备技术领域,具体涉及一种离合器配重板的旋铆自动装配机。
背景技术:2.在摩托车离合器生产过程中,配重板是离合器的组成部分,目前配重板的旋铆装配均为人工完成,由于产量较大,而且工人一直重复旋铆工艺的上下料工作,浪费大量人力物力,并且由于工人疏忽,容易出错。所以,设计一种自动化设备,代替人工,完成配重板的旋铆工艺。
技术实现要素:3.本实用新型的目的在于克服上述现有技术的不足,提供了一种离合器配重板的旋铆自动装配机,克服了现有技术中存在的问题。
4.为了解决技术问题,本实用新型的技术方案是:一种离合器配重板的旋铆自动装配机,包括上料台、自动上料装置、转盘装配装置、工控机和底部支撑台,所述上料台、自动上料装置、转盘装配装置、工控机均设置于底部支撑台上端面,上料台设置于底部支撑台上端面一侧,转盘装配装置设置于底部支撑台上端面另一侧,自动上料装置设置于上料台和转盘装配装置之间的位置,自动上料装置将上料台盛放的工件抓取移动至转盘装配装置,所述上料台、自动上料装置和转盘装配装置分别与工控机电连接。
5.优选的,所述上料台包括上料伺服电缸、上料气缸、托盘机构、平移气缸、插齿和安装板,所述上料伺服电缸设置于底部支撑台的台面下方,上料伺服电缸上端连接上料气缸,其中上料伺服电缸与上料气缸垂直设置,上料气缸上端设置有插齿,所述平移气缸设置于底部支撑台的台面上端面,平移气缸上端固定连接安装板,所述安装板上设置有两组托盘机构,平移气缸带动两组托盘机构左右移动至上料气缸位置,插齿在上料气缸的带动下移动至托盘机构底部,将托盘机构盛放的工件,接着在上料伺服电缸的带动下使托盘机构升降,所述上料伺服电缸、上料气缸、托盘机构和平移气缸分别与工控机电连接。
6.优选的,所述托盘机构包括托盘、导向立杆、传感器,所述导向立杆竖直固定于安装板上端面,其中托盘中心穿过导向立杆套装于导向立杆上,工件穿过导向立杆放置于托盘内,所述传感器通过固定杆设置于导向立杆一侧,用于检测工件的高度,传感器与工控机电连接。
7.优选的,所述自动上料装置包括机器人、机器人夹具、xy桁架移栽机构、抓手组件、定位台和视觉系统,机器人、xy桁架移栽机构和定位台分别固定于底部支撑台的台面上端面,xy桁架移栽机构一端靠近上料台,xy桁架移栽机构另一端靠近转盘装配装置,机器人靠近转盘装配装置设置,定位台设置于xy桁架移栽机构和机器人之间,并且视觉系统设置于定位台正上方,所述xy桁架移栽机构上设置有抓手组件,抓手组件沿xy桁架移栽机构移动将上料台盛放的工件抓取移动至定位台上,所述机器人安装有机器人夹具,机器人夹具将
定位台上的工件抓取移动至转盘装配装置,所述机器人、机器人夹具、xy桁架移栽机构、抓手组件和视觉系统分别与工控机电连接。
8.优选的,所述视觉系统为摄像头。
9.优选的,所述转盘装配装置包括上层固定圆盘、下层旋转转盘、第一气动机构、第一旋铆机、转运机器人、第二旋铆机、第二振动上料机,其中上层固定圆盘、第一气动机构、第一旋铆机、转运机器人、第二旋铆机和第二振动上料机分别固定于底部支撑台的台面上端面,下层旋转转盘同轴设置于上层固定圆盘正下方,下层旋转转盘通过其中心下侧布置的电机绕中心轴旋转,所述第一气动机构、第一旋铆机、转运机器人、第二旋铆机和第二振动上料机均匀设置于上层固定圆盘和下层旋转转盘周边位置。
10.优选的,所述上层固定圆盘上设置有八个圆形工位,其中第一气动机构设置于12点钟圆形工位一侧的底部支撑台的台面上端面,第一气动机构一侧设置有第一振动上料机,第一旋铆机设置于1点钟圆形工位一侧的底部支撑台的台面上端面,其中3点钟圆形工位为自动上料装置上料空位,5点钟圆形工位为下料空位,第二旋铆机设置于6点钟圆形工位一侧的底部支撑台的台面上端面,第二振动上料机设置于7点钟圆形工位一侧的底部支撑台的台面上端面,转运机器人设置于9点钟和11点钟圆形工位之间一侧的底部支撑台的台面上端面。
11.优选的,所述下层旋转转盘上设置有八个旋转工位,八个旋转工位每次旋转一个分度位置均停止在上层固定圆盘上的八个圆形工位同心位置,八个所述旋转工位上分别设置有自转组件,自转组件上安装有工件模具,所述八个旋转工位分两组,每组四个,两组旋转工位分别间隔布置,并且两组旋转工位上安装的工件模具不同,同组旋转工位上安装的工件模具相同;所述自转组件通过步进电机带动绕旋转工位的中心轴旋转,下层旋转转盘带动八个自转组件公转,每个自转组件由步进电机带动绕旋转工位的中心轴自转。
12.优选的,所述第二振动上料机一侧设置有第二气动机构,所述1点钟圆形工位和6点钟圆形工位的上层固定圆盘上设置有固定组件。
13.相对于现有技术,本实用新型的优点在于:
14.(1)本实用新型旋铆自动装配机包括上料台、自动上料装置、转盘装配装置、工控机,工控机控制自动上料装置将上料台盛放的工件抓取移动至转盘装配装置,进行装配的各个工序,本实用新型自动设备可大幅减少人工成本,并大大提高了生产效率,提高了自动化程度,一个工人可同时兼顾多台设备;
15.(2)本实用新型转盘装配装置为满足使用两种不同工件模具,将下层旋转转盘的八工位分为两组,每组90
°
均布,在同一转盘上的两组工件模具,在同一转动下完成两组工艺,两组之间设置转运机器人;下层旋转转盘的电机公转每次90
°
,各个自转组件自转,互不影响,在振动上料机的配合下使两组铆钉在工件模具上分别呈圆周分布;
16.(3)本实用新型将中心旋转结构分为上层固定圆盘和下层旋转转盘,下层旋转转盘用于工件在不同工位之间的转移,上层固定圆盘用于针对每个位置的工艺布置相应的工艺设备满足使用,实现“上下层的固定与转动”;
17.(4)本实用新型将旋铆的各个工艺集成于一台设备上,设备集成化程度高、自动化程度高,生产效率高。
上端面,平移气缸1
‑
6上端固定连接安装板1
‑
8,所述安装板1
‑
8上设置有两组托盘机构,平移气缸1
‑
6带动两组托盘机构左右移动至上料气缸1
‑
2位置,插齿1
‑
7在上料气缸1
‑
2的带动下移动至托盘机构底部,接着在上料伺服电缸1
‑
1的带动下使托盘机构盛放的工件升降,所述上料伺服电缸1
‑
1、上料气缸1
‑
2、托盘机构和平移气缸1
‑
6分别与工控机4电连接。
36.如图3~4所示,优选的,所述托盘机构包括托盘1
‑
3、导向立杆1
‑
4、传感器1
‑
5,所述导向立杆1
‑
4竖直固定于安装板1
‑
8上端面,其中托盘1
‑
3中心穿过导向立杆1
‑
4套装于导向立杆1
‑
4上,工件穿过导向立杆1
‑
4放置于托盘1
‑
3内,所述传感器1
‑
5通过固定杆设置于导向立杆1
‑
4一侧,用于检测工件的高度,传感器1
‑
5与工控机4电连接。
37.所述上料伺服电缸1
‑
1布置于台面5
‑
1下方,用于顶升托盘1
‑
3至指定高度;上料气缸1
‑
2安装在上料伺服电缸1
‑
1上,上料气缸1
‑
2上设有插齿1
‑
7,需要上料伺服电缸1
‑
1顶升托盘1
‑
3时,上料气缸1
‑
2将插齿1
‑
7推入托盘1
‑
3下方,即可使托盘1
‑
3升降;托盘1
‑
3、导向立杆1
‑
4均安装在平移气缸1
‑
6上,平移气缸1
‑
6可实现安装在其上面的两套托盘机构平移位置,以满足托盘1
‑
3可移动至上料伺服电缸1
‑
1正上方;托盘1
‑
3用于盛放工件,并在其中心设有导向孔,保证其在垂直方向升降,导向立杆1
‑
4用于上料伺服电缸1
‑
1完成工件托盘的垂直移动导向作用。
38.实施例3
39.如图1所示,优选的,所述自动上料装置2包括机器人2
‑
1、机器人夹具2
‑
2、xy桁架移栽机构2
‑
3、抓手组件2
‑
4、定位台2
‑
5和视觉系统2
‑
6,机器人2
‑
1、xy桁架移栽机构2
‑
3和定位台2
‑
5分别固定于底部支撑台5的台面5
‑
1上端面,xy桁架移栽机构2
‑
3一端靠近上料台1,xy桁架移栽机构2
‑
3另一端靠近转盘装配装置3,机器人2
‑
1靠近转盘装配装置3设置,定位台2
‑
5设置于xy桁架移栽机构2
‑
3和机器人2
‑
1之间,并且视觉系统2
‑
6设置于定位台2
‑
5正上方,所述xy桁架移栽机构2
‑
3上设置有抓手组件2
‑
4,抓手组件2
‑
4沿xy桁架移栽机构2
‑
3移动将上料台1盛放的工件抓取移动至定位台2
‑
5上,所述机器人2
‑
1安装有机器人夹具2
‑
2,机器人夹具2
‑
2将定位台2
‑
5上的工件抓取移动至转盘装配装置3,所述机器人2
‑
1、机器人夹具2
‑
2、xy桁架移栽机构2
‑
3、抓手组件2
‑
4和视觉系统2
‑
6分别与工控机4电连接。
40.优选的,所述视觉系统2
‑
6为摄像头。
41.所述视觉系统为摄像头以及配套的算法系统,用于识别不同规格的工件,以便后续将工件由机器人安装在模具内。
42.所述xy桁架移栽机构2
‑
3为现有装置,可以直接购买。
43.所述抓手组件2
‑
4是由多组真空吸盘固定于支架上,由该吸盘吸取工件并移动。
44.此外,为降低成本,xy桁架移栽机构2
‑
3可采用气动机构完成,机器人2
‑
1同时也可由移栽机构完成操作。视觉系统不仅可以设置于定位正上方,也可以安装与机器人夹具2
‑
2上。此外,去除视觉系统,由定位模具替代。不过这种方式,虽然降低成本,同时也降低设备柔性化,须对每种工件设置不同的定位模具。
45.实施例4
46.如图2、5所示,优选的,所述转盘装配装置3包括上层固定圆盘3
‑
1、下层旋转转盘3
‑
2、第一气动机构3
‑
3、第一振动上料机3
‑
11、第一旋铆机3
‑
4、转运机器人3
‑
5、第二旋铆机3
‑
6和第二振动上料机3
‑
7,第二第二气动机构3
‑
8,其中上层固定圆盘3
‑
1、第一气动机构3
‑
3、第一振动上料机3
‑
11、第一旋铆机3
‑
4、转运机器人3
‑
5、第二旋铆机3
‑
6、第二振动上料机
3
‑
7和第二第二气动机构3
‑
8分别固定于底部支撑台5的台面5
‑
1上端面,下层旋转转盘3
‑
2同轴设置于上层固定圆盘3
‑
1正下方,下层旋转转盘3
‑
2通过其中心下侧布置的电机绕中心轴旋转,所述第一气动机构3
‑
3、第一振动上料机3
‑
11、第一旋铆机3
‑
4、转运机器人3
‑
5、第二旋铆机3
‑
6、第二振动上料机3
‑
7和第二第二气动机构3
‑
8均匀设置于上层固定圆盘3
‑
1和下层旋转转盘3
‑
2周边位置。
47.如图2、5所示,优选的,所述上层固定圆盘3
‑
1上设置有八个圆形工位,第一气动机构3
‑
3设置于12点钟圆形工位一侧的底部支撑台5的台面5
‑
1上端面,第一气动机构3
‑
3一侧设置有第一振动上料机3
‑
11,第一旋铆机3
‑
4设置于1点钟圆形工位一侧的底部支撑台5的台面5
‑
1上端面,其中3点钟圆形工位为自动上料装置2的上料空位,5点钟圆形工位为下料空位,第二旋铆机3
‑
6设置于6点钟圆形工位一侧的底部支撑台5的台面5
‑
1上端面,第二振动上料机3
‑
7设置于7点钟圆形工位一侧的底部支撑台5的台面5
‑
1上端面,转运机器人3
‑
5设置于9点钟和11点钟圆形工位之间一侧的底部支撑台5的台面5
‑
1上端面。
48.实施例5
49.如图2、5所示,优选的,所述下层旋转转盘3
‑
2上设置有八个旋转工位,八个旋转工位每次旋转一个分度位置均对应停止在上层固定圆盘3
‑
1上的八个圆形工位同心位置,八个所述旋转工位上分别设置有自转组件3
‑
10,自转组件3
‑
10上安装有工件模具,所述八个旋转工位分两组,每组四个,两组旋转工位分别间隔布置,并且两组旋转工位上安装的工件模具不同,同组旋转工位上安装的工件模具相同;所述自转组件3
‑
10通过步进电机带动绕旋转工位的中心轴旋转,下层旋转转盘3
‑
2带动八个自转组件3
‑
10公转,每个自转组件3
‑
10由步进电机带动绕旋转工位的中心轴自转。
50.如图5所示,优选的,所述第二振动上料机3
‑
7一侧设置有第二气动机构3
‑
8,所述1点钟圆形工位和6点钟圆形工位的上层固定圆盘3
‑
1上设置有固定组件3
‑
9。
51.由于在旋铆的工艺位置需要额外增加固定组件随同布置,将固定组件3
‑
9固定于上层固定圆盘3
‑
1上,节省成本,下层旋转转盘3
‑
2为公转与自转使用的转盘。
52.所述第二气动机构3
‑
8是类似于xy桁架移栽机构2
‑
3的装置,区别在于该机构使用气缸配合导向装置将较大的铆钉送到位置,例如滑块导轨,分别执行了x轴向运动和z轴升降运动。
53.所述自转组件3
‑
10用于带动工件模具旋转,从而实现工件的旋铆铆钉动作,自转组件3
‑
10属于现有组件,所述工件模具上设置有三个铆钉孔,并且以圆形三等分位置分布,每个铆钉孔由振动上料机送上一个铆钉,所以每旋铆一个铆钉后,就需要该工件模具旋转一定角度后,再旋铆下一个。
54.所述自转组件3
‑
10包括伺服电机、同步带和同步带轮,伺服电机驱动同步带,同步带连接同步带轮,同步带轮直连安装工件的工件模具,以完成旋转动作。
55.所述下层旋转转盘3
‑
2和自转组件3
‑
10满足“内外圈公转与自转”,即满足八工位旋转,内圈公转即下层旋转转盘3
‑
2的电机公转每次90
°
,外圈自转即自转组件3
‑
10旋转并配合振动上料机将旋铆的3颗铆钉呈圆周分布在工件模具上,所以每个外圈工位的工件模具均设有自转组件3
‑
10,完成每个工位的操作。
56.所述第一气动机构3
‑
3通过第一振动上料机3
‑
11用于输送小的铆钉,因此使用气动上料机配合单气缸实现升降运动即可,第二振动上料机3
‑
7一般用于输送大的铆钉,因此
需要第二气动机构3
‑
8进行配合双气缸实现升降和平移运动。
57.实施例6
58.优选的,一种如上任一项所述的离合器配重板的旋铆自动装配机的装配方法,包括以下步骤:
59.步骤1:将工件放置于上料台1上;
60.步骤2:利用工控机4控制自动上料装置2将工件抓取至转盘装配装置3;
61.步骤3:通过转盘装配装置3完成工件装配的各个工序。
62.本实用新型的工作原理及装配过程如下:
63.本实用新型包括上料台1、自动上料装置2、转盘装配装置3、工控机4和底部支撑台5,上料台1设置于底部支撑台5上端面一侧,转盘装配装置3设置于底部支撑台5上端面另一侧,自动上料装置2设置于上料台1和转盘装配装置3之间的位置,工控机4控制自动上料装置2将上料台1盛放的工件抓取移动至转盘装配装置3,上料台1将离合器的配重板由人工首先放置在上料台1的托盘1
‑
3上,将转盘装配装置3上自转组件3
‑
10上的工件模具换成对应的工件模具,即可启动设备,由上料伺服电缸1
‑
1将配重板移动至自动上料的指定高度位置(传感器1
‑
5检测的位置),自动上料装置2将上料台1输送的工件抓取并通过视觉系统2
‑
6重新定位后,放置于转盘装配装置3上,由转盘装配装置3各个工位完成铆钉的上料与铆固,在八工位最后一个工位,完成工件的下料,下料位置放有物料托盘或者可以使用皮带线等传出工件,形成生产线。
64.如图3、4所示,上料台1设有两组托盘机构,一用一备的方式使用,由平移气缸1
‑
6完成哪组托盘机构由上料伺服电缸1
‑
1升降,其中一组托盘机构停止到位后,上料气缸1
‑
2伸出插齿1
‑
7,插齿1
‑
7移动至托盘1
‑
3正下方,上料伺服电缸1
‑
1抬升完成托盘1
‑
3提升动作,工件置于穿过导向立杆1
‑
4放置在托盘1
‑
3上,工件升高由传感器1
‑
5探测高度,每当抓手组件2
‑
4取走一件工件后,托盘1
‑
3升降一件工件的厚度,保证最上层工件一直保持在最高位置。
65.如图1所示,由抓手组件2
‑
4将工件从上料台1抓取后,抓手组件2
‑
4沿xy桁架移栽机构移动至定位台2
‑
5正上方,放置于定位台2
‑
5上,定位台2
‑
5装有固定装置,可以将工件固定于其上,视觉系统2
‑
6对工件完成外形和旋铆孔位置的识别形成数据信息,数据信息传递给机器人2
‑
1后,由机器人夹具2
‑
2确定抓取角度和位置,再实施抓取,并将抓取后的工件,按照旋铆孔的位置装配于转盘装配装置3的工件模具上。
66.如图2、5所示,机器人夹具2
‑
2将工件放置于3点钟圆形工位布置于下层旋转转盘3
‑
2上的自转组件3
‑
10的工件模具上,此时自转组件3
‑
10的工件模具上已经放置完成铆钉,机器人2
‑
1将工件对准该工件模具上的三个铆钉完成放置动作(说明:已经完成放置的铆钉,是在12点钟位置由第一气动机构3
‑
3通过第一振动上料机3
‑
11将铆钉送入自转组件3
‑
10上工件模具上的销孔,该销孔在圆周上共有两组,第一气动机构3
‑
3每送入一个铆钉,自转组件3
‑
10上工件模具旋转一定角度,将下一个销孔转至第一气动机构3
‑
3送料位置,接着机器人夹具2
‑
2将工件放置于3点钟圆形工位的操作运行),接着下层旋转转盘3
‑
2公转90
°
,工件转动到6点钟圆形工位,由第二旋铆机3
‑
6将三个铆钉固定于工件上,完成第一个工艺;
67.第二个工艺是将另一种铆钉以上述同样的方式固定于工件上,区别在于铆钉的规格,分布的圆周直径不同。因此需要换另一种工件模具利用上述同样工艺完成。因此,在6点
钟位置第一个旋铆的工件,通过下层旋转转盘3
‑
2旋转至9点钟位置后,由转运机器人3
‑
5将9点钟位置的工件取出,装在10点钟位置的工件模具上(说明:10点钟位置的工件模具上已经完成放置的铆钉,是在7点钟位置由第二振动上料机3
‑
7配合第二气动机构3
‑
8,将铆钉送入自转组件3
‑
10上工件模具上的销孔);接着下层旋转转盘3
‑
2公转90
°
,工件转动到1点钟圆形工位,由第一旋铆机3
‑
4和固定组件3
‑
9将三个铆钉固定于工件上,最终完成该工件两种铆钉的固定,接着下层旋转转盘3
‑
2公转90
°
,转动至5点钟位置,再由机器人2
‑
1抓取后下料。
68.本实用新型旋铆自动装配机包括上料台、自动上料装置、转盘装配装置、工控机,工控机控制自动上料装置将上料台盛放的工件抓取移动至转盘装配装置,进行装配的各个工序,本实用新型自动设备可大幅减少人工成本,并大大提高了生产效率,提高了自动化程度,一个工人可同时兼顾多台设备。
69.本实用新型转盘装配装置为满足使用两种不同工件模具,将下层旋转转盘的八工位分为两组,每组90
°
均布,在同一转盘上的两组工件模具,在同一转动下完成两组工艺,两组之间设置转运机器人;下层旋转转盘的电机公转每次90
°
,各个自转组件3
‑
10自转,互不影响,在振动上料机的配合下使两组各三颗铆钉在工件模具上呈圆周分布。
70.本实用新型将中心旋转结构分为上层固定圆盘和下层旋转转盘,下层旋转转盘用于工件在不同工位之间的转移,上层固定圆盘用于针对每个位置的工艺布置相应的工艺设备满足使用,实现“上下层的固定与转动”。
71.本实用新型将旋铆的各个工艺集成于一台设备上,设备集成化程度高、自动化程度高,生产效率高。
72.上面对本实用新型优选实施方式作了详细说明,但是本实用新型不限于上述实施方式,在本领域普通技术人员所具备的知识范围内,还可以在不脱离本实用新型宗旨的前提下做出各种变化。
73.不脱离本实用新型的构思和范围可以做出许多其他改变和改型。应当理解,本实用新型不限于特定的实施方式,本实用新型的范围由所附权利要求限定。