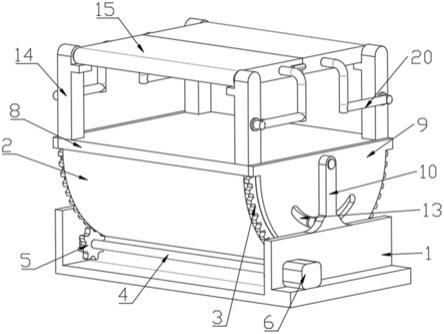
1.本实用新型涉及焊接装置技术领域,具体为一种铝合金车身激光焊接装置。
背景技术:2.激光焊接作为一种在汽车车身焊接过程中经常被选用的焊接工艺,和其他传统焊接工艺相比焊接质量更高、焊接速度更快,产生的夹渣和焊接缺陷更少,随着全自动生产线的推广和普及,人们对车身焊接的工艺标准要求越来越高。
3.传统的焊接过程中一般是通过固定夹具对车身固定,然后进行焊接,然而固定夹具在使用时会有焊接死角,需要将车身进行多次翻转进行夹持焊接,操作较为不便,并且会出现滑落情况,有一定的安全隐患。
4.基于此,本实用新型设计了一种铝合金车身激光焊接装置,以解决上述问题。
技术实现要素:5.为解决上述问题,本实用新型提供如下技术方案:
6.一种铝合金车身激光焊接装置,包括底座,其特征在于:所述底座上设有支撑座,所述支撑座的两侧设有齿环,所述齿环与支撑座固定连接,所述底座上设有与底座转动连接的旋转杆,所述旋转杆上固定连接有与支撑座上的齿环啮合的齿轮,所述旋转杆的一端与正反电机的输出端固定连接,所述底座的两侧设有与支撑座配合的限位机构,所述支撑座上固定连接有支撑板。
7.作为本实用新型的进一步方案,所述限位机构包括固定板、转动杆、连接柱和连接板,所述固定板固定连接在齿环的两侧,所述转动杆的一端与固定板转动连接,另一端与底座固定连接,所述转动杆的一端与连接柱固定连接,所述连接柱的另一端与连接板固定连接。工作时,正反电机带动旋转杆旋转,旋转杆上的齿轮随之带动支撑座上的齿环进行旋转,随之支撑座在底座转动连接,便于支撑座进行转动,对支撑座上的车身上焊接死角进行焊接,操作简单。
8.作为本实用新型的进一步方案,所述固定板上设有与连接柱相适配的弧形槽。工作时,可以避免支撑座转动幅度过大而导致齿轮脱位的现象。
9.作为本实用新型的进一步方案,所述支撑座的上端设有支撑板,所述支撑板上设有四个支撑腿,两个横向所述支撑腿之间设有旋转板,所述旋转板通过连接杆与支撑腿转动连接。工作时,将旋转板在两个支撑腿内的连接杆上向内翻转,压住车身,通过支撑腿内侧的凸块可以将旋转板限位。
10.作为本实用新型的进一步方案,一个所述旋转板内设有弹簧槽,所述弹簧槽内设弹簧,所述弹簧的一端与弹簧槽的内壁固定连接,另一端与固定块固定连接,另一个所述旋转板内设有与固定块相适配的固定槽。工作时,旋转板向内旋转后,固定块随之向弹簧槽内移动,压缩弹簧,当两个旋转板紧贴与支撑腿凸块位置时,弹簧槽与固定槽相对,弹簧恢复形变,固定块随之向固定槽内移动,对两个旋转板进行固定,便于对焊接时的车身进行固
定。
11.作为本实用新型的进一步方案,所述支撑腿的外侧设有横杆,所述横杆的一端与支撑腿转动连接,另一端与旋转板固定连接。工作时,避免对车身焊接时出现滑落的现象。
12.有益效果
13.与现有技术相比,本实用新型的有益效果是:
14.1.通过正反电机、旋转杆、齿轮、齿条、底座和支撑座等结构的配合使用,通过正反电机带动旋转杆旋转,旋转杆上固定的齿轮随之带动与其啮合的齿环进行旋转,支撑座随之通过转动杆在底座上转动,便于对支撑座上需要焊接的车身的死角进行焊接,操作方便。
15.2.通过旋转板、支撑腿、弹簧、固定块和横杆之间的配合使用,旋转板向内旋转后,固定块随之向弹簧槽内移动,压缩弹簧,当两个旋转板紧贴与支撑腿凸块位置时,弹簧槽与固定槽相对,弹簧恢复形变,固定块随之向固定槽内移动,对两个旋转板进行固定,便于对焊接时的车身进行固定,设置横杆,能避免对车身焊接时出现滑落的现象。
附图说明
16.为了更清楚地说明本实用新型实施例的技术方案,下面将对实施例描述所需要使用的附图作简单地介绍,显而易见地,下面描述中的附图仅仅是本实用新型的一些实施例,对于本领域普通技术人员来讲,在不付出创造性劳动的前提下,还可以根据这些附图获得其他的附图。
17.图1为本实用新型总体结构示意图;
18.图2为本实用新型限位机构结构示意图;
19.图3为本实用新型旋转板与支撑腿剖视示意图;
20.图4为本实用新型图3的a处放大示意图;
21.图5为本实用新型固定块与瘫痪配合示意图。
22.附图中,各标号所代表的部件列表如下:
[0023]1‑
底座,2
‑
支撑座,3
‑
齿环,4
‑
旋转杆,5
‑
齿轮,6
‑
正反电机,7
‑
限位机构,8
‑
支撑板,9
‑
固定板,10
‑
转动杆,11
‑
连接柱,12
‑
连接板,13
‑
弧形槽,14
‑
支撑腿,15
‑
旋转板,16
‑
弹簧槽,17
‑
弹簧,18
‑
固定块,19
‑
固定槽,20
‑
横杆。
具体实施方式
[0024]
下面将结合本实用新型实施例中的附图,对本实用新型实施例中的技术方案进行清楚、完整地描述。
[0025]
请参阅图1
‑
4,本实用新型提供一种技术方案:
[0026]
一种铝合金车身激光焊接装置,包括底座1,其特征在于:底座1上设有支撑座2,支撑座2的两侧设有齿环3,齿环3与支撑座2固定连接,底座1上设有与底座1转动连接的旋转杆4,旋转杆4上固定连接有与支撑座2上的齿环3啮合的齿轮5,旋转杆4的一端与正反电机6的输出端固定连接,底座1的两侧设有与支撑座2配合的限位机构7,支撑座2上固定连接有支撑板8。
[0027]
作为本实用新型的进一步方案,限位机构7包括固定板9、转动杆10、连接柱11和连接板12,固定板9固定连接在齿环3的两侧,转动杆10的一端与固定板9转动连接,另一端与
底座1固定连接,转动杆10的一端与连接柱11固定连接,连接柱11的另一端与连接板12固定连接。工作时,正反电机6带动旋转杆4旋转,旋转杆4上的齿轮5随之带动支撑座2上的齿环3进行旋转,随之支撑座2在底座1转动连接,便于支撑座2进行转动,对支撑座2上的车身上焊接死角进行焊接,操作简单。
[0028]
作为本实用新型的进一步方案,固定板9上设有与连接柱11相适配的弧形槽13。工作时,可以避免支撑座2转动幅度过大而导致齿轮5脱位的现象。
[0029]
作为本实用新型的进一步方案,支撑座2的上端设有支撑板8,支撑板8上设有四个支撑腿14,两个横向支撑腿14之间设有旋转板15,旋转板15通过连接杆与支撑腿14转动连接。工作时,将旋转板15在两个支撑腿14内的连接杆上向内翻转,压住车身,通过支撑腿14内侧的凸块可以将旋转板15限位。
[0030]
作为本实用新型的进一步方案,一个旋转板15内设有弹簧槽16,弹簧槽16内设弹簧17,弹簧17的一端与弹簧槽16的内壁固定连接,另一端与固定块18固定连接,另一个旋转板15内设有与固定块18相适配的固定槽19。工作时,旋转板15向内旋转后,固定块18随之向弹簧槽16内移动,压缩弹簧17,当两个旋转板15紧贴与支撑腿14凸块位置时,弹簧槽16与固定槽19相对,弹簧17恢复形变,固定块18随之向固定槽19内移动,对两个旋转板15进行固定,便于对焊接时的车身进行固定。
[0031]
作为本实用新型的进一步方案,支撑腿14的外侧设有横杆20,横杆20的一端与支撑腿14转动连接,另一端与旋转板15固定连接。工作时,避免对车身焊接时出现滑落的现象。
[0032]
本实施例的一个具体应用为:
[0033]
使用本实用新型时,首先,需要对车身进固定焊接时,旋转板15向内旋转后,固定块18随之向弹簧槽16内移动,压缩弹簧17,当两个旋转板15紧贴与支撑腿14凸块位置时,弹簧槽16与固定槽19相对,弹簧17恢复形变,固定块18随之向固定槽19内移动,对两个旋转板15进行固定,需要对车身死角进行焊接时,启动正反电机6,正反电机6带动旋转杆4旋转,旋转杆4上的齿轮5随之带动支撑座2上的齿环3进行旋转,随之支撑座2通过转动杆10在底座1转动。本实用新型便于对支撑座2上需要焊接的车身的死角进行焊接,操作方便,同时也便于对焊接时的车身进行固定,避免对车身焊接时出现滑落的现象。
[0034]
优选实施例并没有详尽叙述所有的细节,也不限制该实用新型仅为的具体实施方式。