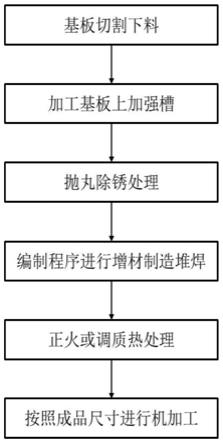
1.本发明涉及一种能够快速加工零件的复合增材方法,适用于需要投入模具且生产周期长、批量小的零件,属于增材制造和工程机械技术领域。
背景技术:2.增材制造技术作为20世纪一项重大制造方法创新,受到很多国家的高度重视,它包含了数字建模、机械加工和材料学等前沿技术,通过将材料逐层堆焊成实体零件,节省了模具投入和材料消耗,缩短了新产品和小批量产品的制造周期,经过多年的发展,增材制造技术已经取得了很大的进步,逐步形成了采用电弧熔丝的高速增材制造工艺,但增材制造的效率仍然较低,需要进一步的提升。
3.对如图1所示的轴承座等厚度较大的零件,由于厚度太厚,无法采用钢板下料后加工成型,需要采用铸造成型,主要流程为模具制作、混砂、造型、制芯、配模、熔炼、浇注、清理等工序。采用铸造模具投入大,且铸造周期长,约60天,无法适应新产品、小批量产品的生产周期需求,若采用增材制造,整个零件堆焊周期约15天,虽然与铸造周期相比有明显的缩短,但与钢板下料后加工成型相比仍存在周期长的缺陷。
技术实现要素:4.针对上述现有技术存在的问题,本发明提供一种能够快速加工零件的复合增材方法,具有快速实现增材制造零件的效果,零件整体强度能够达到铸造水平。
5.为了实现上述目的,本发明采用的一种能够快速加工零件的复合增材方法,包括以下步骤:
6.s1、根据待加工零件的特性选择相同材质的钢板或型材作为基板,基板上开有加强槽;
7.s2、在基板上采用增材堆焊,增材制造材料采用和基板相同或相近材质的焊丝或3d打印粉末。
8.作为改进,所述基板进行机加工和抛丸处理,基板厚度t1≥30mm。
9.作为改进,所述加强槽深度h=5~10mm,宽度b1=10~20mm,加强槽间隔c1=30~50mm。
10.作为改进,所述增材制造时每层厚度t2=1~3mm,每道焊缝宽度b2=3~10mm,每层搭接量c2=2~5mm,每层接头位置错位a=15~90
°
。
11.作为改进,增材堆焊时的保护气采用ar气和co2的混合气,其中ar气体积比≥80%,或采用纯ar气,或采用纯he气。
12.作为改进,所述保护气的流量为20~25l/min。
13.作为改进,堆焊参数如下:堆焊电流为150~280a,堆焊速度为100~500mm/min,送丝速度为300~2000mm/min。
14.作为改进,在每层堆焊时,单双层堆焊顺序相反。
15.作为改进,根据零件材料和力学性能要求进行热处理。
16.作为改进,采用正火热处理时硬度控制在170~220hb;采用调质热处理时硬度控制在240~300hb。
17.最后,本发明还提供了一种采用所述复合增材方法得到的具有复合增材结构的零件。
18.与现有技术相比,本发明提供一种能够快速加工零件的复合增材方法,形成了增材制造的新思路、新方法,包括采用钢板制造的基体和采用与基板相同或相近材质的焊丝(粉末)进行堆焊,形成增材制造的零件,针对零件的不同,基板的重量占比不一,部分占比超过50%,基板重量的占比越大,增材制造的周期越短。
附图说明
19.图1为现有轴承座结构示意图;
20.图2为实施例1中基板及加强槽结构示意图;
21.图3为本发明的增材制造结构示意图;
22.图4为本发明的整体增材制造成品示意图;
23.图5为本发明的加强槽尺寸示意图;
24.图6为本发明的增材制造流程图。
具体实施方式
25.为使本发明的目的、技术方案和优点更加清楚明了,下面对本发明进行进一步详细说明。但是应该理解,此处所描述的具体实施例仅仅用以解释本发明,并不用于限制本发明的范围。
26.除非另有定义,本文所使用的所有的技术术语和科学术语与属于本发明的技术领域的技术人员通常理解的含义相同,本文中在本发明的说明书中所使用的术语只是为了描述具体的实施例的目的,不是旨在于限制本发明。
27.一种能够快速加工零件的复合增材方法,包括以下步骤:
28.步骤一、根据零件特性选择相同材质的钢板或型材作为基板,采用火焰、等离子或激光切割机进行下料,为防止堆焊过程中出现变形,一般基板2的厚度t1≥30mm,若采用火焰切割机下料,切割氧压力0.45~0.6mpa,预热时间70~110s,切割速度150~240mm/min,切割圆弧下调范围为30~50mm/min,保证切割时不失圆,外圆、内孔和端面的加工余量单边留3~5mm;
29.步骤二、采用车床、铣床或镗床机加工设备,根据零件受力情况进行基板加强槽预加工,加强槽3的深度h=5~10mm,宽度b1=10~20mm,加强槽间隔c1=30~50mm;
30.步骤三、采用抛丸机或打磨机等设备,对加工后的基板进行抛丸除锈,除锈等级达到sa2.5,粗糙度50~150μm;
31.步骤四、进行堆焊程序编制,设定堆焊参数,采用机器人进行堆焊,堆焊参数如下:堆焊电流为150~280a,堆焊速度为100~500mm/min,送丝速度为300~2000mm/min;
32.选择焊丝作为增材制造材料,也可以选择3d打印粉末作为增材制造材料,堆焊层间温度控制在50~200℃,如层间间隔时间较长温度降至常温,需要将表面进行打磨处理;
33.为了防止接头集中在同一位置影响增材制造零件强度,增材制造每层厚度t2=1~3mm,每道焊缝宽度b2=3~10mm,每层搭接量c2=2~5mm,每层接头位置错位a=15~90
°
;另外,为了保证焊缝内部无气孔等缺陷,增材堆焊时的保护气采用ar气和co2的混合气,其中ar气体积比≥80%,或采用纯ar气,或采用纯he气,所述保护气的流量为20~25l/min;
34.需要注意的是:在每层堆焊时,单双层堆焊顺序相反,单层从外侧向内侧堆焊,双层从内侧向外侧堆焊;
35.步骤五、进行正火或调质等热处理,热处理前表面应清洁,不允许有裂纹及影响热处理质量的氧化皮、疏松、渣孔等缺陷,热处理硬度参照零件技术要求,正火硬度在170~220hb,加热温度830~850℃,保温时间180~240min,调质硬度在240~300hb,加热温度850~870℃,保温时间120~150min,出炉淬火,回火加热温度530~570℃,保温时间150~180min,布氏硬度每处测1~3点,取其算术平均值;
36.步骤六、根据增材制造零件形状和图纸加工要求,采用车床、铣床、镗床、钻床等设备进行机械加工。
37.实施例1
38.如图1-图6所示,一种能够快速加工零件的复合增材方法,本实施例以图1所示的轴承座为例,可以将轴承座的下部采用钢板下料,经过加工形成如图2所示的基板2,基板2上设有加强槽3,通过增材制造形成如图3所示的增材结构1,将基板2与增材结构1成型组合,形成如图4所示的轴承座成品;
39.具体包括以下步骤:
40.步骤一、采用火焰切割机进行下料,基板2的厚度t1接近80mm,采用火焰切割机下料的切割氧压力0.5mpa,预热时间90s,切割速度180mm/min,切割圆弧下调范围为40mm/min,保证切割时不失圆,外圆、内孔和端面的加工余量单边留4mm;
41.步骤二、采用车床进行基板加强槽预加工,加强槽3的深度h=8mm,宽度b1=15mm,加强槽间隔c1=40mm;
42.步骤三、采用抛丸机进行抛丸除锈,除锈等级达到sa2.5,粗糙度80~90μm;
43.步骤四、进行堆焊程序编制,设定堆焊参数,采用机器人进行堆焊,堆焊参数如下:堆焊电流为180a,堆焊速度为300mm/min,送丝速度为1500mm/min;
44.选择焊丝作为增材制造材料,堆焊层间温度控制在160℃,如层间间隔时间较长温度降至常温,需要将表面进行打磨处理;同时,增材制造每层厚度t2=2mm,每道焊缝宽度b2=5mm,每层搭接量c2=3mm,每层接头位置错位a=60
°
;为了保证焊缝内部无气孔等缺陷,增材堆焊时的保护气采用纯ar气,流量为20~25l/min;
45.步骤五、进行正火热处理,热处理前表面应清洁,不允许有裂纹及影响热处理质量的氧化皮、疏松、渣孔等缺陷,热处理硬度参照零件技术要求,正火硬度在170~220hb,加热温度840℃,保温时间200min,出炉淬火,回火加热温度550℃,保温时间160min,布氏硬度每处测3点,取其算术平均值,经测定符合要求;
46.步骤六、根据增材制造零件形状和图纸加工要求,进行机械加工。
47.本发明将钢板通过切割机进行下料,用机加工设备进行基板加强槽预加工,在堆焊前进行抛丸除锈,提供了除锈等级标准、堆焊参数标准、热处理标准等,通过基板和增材
制造组合,可以大幅减少增材制造时间,为生产制造过程提供了技术支持。
48.实施例2
49.常规工程机械球墨铸铁铸件主要采用qt450或qt500,其力学性能标准及采用本发明的复合增材方法得到的零件,检测对比如下表1、表2所示:
50.表1常规铸件与本发明增材制造的零件的力学性能对比
[0051][0052]
经过万能力学性能试验机检测,增材制造零件抗拉强度达到qt450或qt500标准,伸长率优于qt450或qt500标准;
[0053]
表2常规铸件与本发明增材制造的零件的缺陷对比
[0054]
对比零件内部缺陷qt450或qt500铸件二级(5mm以下)本发明增材制造零件一级(2mm以下)
[0055]
经过超声波探伤仪检测,增材制造零件内部缺陷等级优于铸件内部缺陷等级。
[0056]
以上所述仅为本发明的较佳实施例而已,并不用以限制本发明,凡在本发明的精神和原则之内所作的任何修改、等同替换或改进等,均应包含在本发明的保护范围之内。