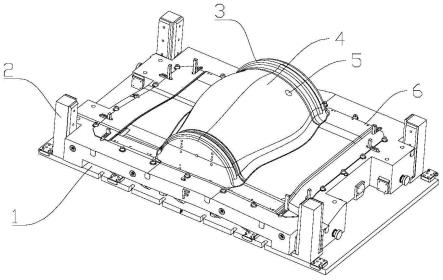
1.本发明涉及飞机零件制造领域,更具体的是飞机发动机机罩制造领域。
背景技术:2.在飞机制造领域,发动机机罩,对飞机而言是指位于飞机尾部,使机体外表面光滑以减小飞行阻力的流线整形构件。又称“机尾整流罩”,为飞机尾部维形整流的结构,对于机身内安装喷气发动机的机尾罩,除了有维形整流作用外,还有引射尾喷管气流来提高推力的作用。发动机机罩由于处在飞机的高温区和尾部,易损坏,为便于更换,常采用与机身部分固定、部分可拆卸的连接型式。其结构一般由内外蒙皮和隔框组成。
3.现有制造发动机机罩的方法为三段式成型再铆接,具体为:先将发动机机罩分段式成型,再将每段的机罩部件进行修剪,最后分别铆接各段机罩部件,得到成品的发动机机罩。
4.现有发动机机罩的生产方法经历多次成型及多次修剪,最后还需进行分别铆接,加工工序繁多,多次铆接及修剪等工艺容易影响机罩的强度等性能,且多段部件经铆接后,机罩的重量过重,使得飞机的重量增加,飞机的安全性随之降低,使得此种生产工艺局限性较大,使用范围较小。
技术实现要素:5.本发明的目的在于:本技术拟采用一次冲压成型的方式生产机罩,解决现有发动机机罩因采用分段铆接造成工序繁多、重量增加以及一次冲压成型过程中带来的在机罩两侧产生褶皱的问题,本发明为了实现上述目的具体采用以下技术方案:
6.一种飞机发动机机罩的生产方法,包括如下步骤:
7.步骤1、将板料置于发动机罩整体成型模内,进行拉延;
8.步骤2、对拉延后所得的粗品进行修边;
9.步骤3、对修边后的粗品进行翻边处理;
10.发动机罩整体成型模包括上模和下模,所述下模的顶面安装有成型鞍,所述成型鞍的轮廓与发动机罩的外形轮廓一致,所述上模的顶面开有与所述成型鞍的轮廓一致的成型凹腔,所述成型鞍的顶面两端还均设有多个成型凸楞,所述成型凹腔内开有与成型凸楞对应的多个成型凹槽。
11.根据生产需求选择合适材质及规格的板料,并将所选的板料放置在发动机罩整体成型模上,将板料在发动机罩整体成型模内成型,成型结束后,将粗品裁剪去边缘多余的部分进行修边,再将粗品进行翻边处理,得到成品的发动机机罩;由于飞机发动机机罩中部较深,板料在压料面流动容易产生冷作硬化,修边后应力释放易形成波浪,同时拉延时板料在成型凸楞上流动亦产生冷作硬化,后续翻边形成表面扭曲不平;因此通过设置对应的成型凹槽及成型凸楞,增大板料在模内的阻力,使得拉延时不走料,避免了两端的成型凸楞之间出现出现波浪、起皱及表面扭曲的问题,成型后将成型凸楞以外的部分修边,使得成品的质
量优良,显著提升了拉延件的尺寸精度和外观质量;通过使用发动机罩整体成型模将板料一次性成型,使得生产工艺被大大缩短,仅包括一次拉延、一次修边及一次翻边,工艺简单,且避免了常规工艺的三段式成型再铆接所带来的缺陷,解决了现有生产工艺所制造的机罩重量过重使得飞机安全性低,以及拉延过程中机罩两侧产生褶皱的问题。
12.优选的,所述拉延使用的油压机吨位为1600t。
13.优选的,所述拉延为多次压制,所述多次压制的次数至少为1次。在拉延过程中,根据所使用的料板的具体材质改变压制的次数,例如拉延dc01冷轧钢板的压制次数为2次,而拉延2024-o的铝合金板料时,拉延压制次数设定为9次,以满足不同板料材质成型的条件。
14.优选的,所述拉延所使用的拉延油为蓖麻油、猪油或菜籽油。
15.优选的,所述下模包括下模板,所述下模板的顶面安装有所述成型鞍,所述上模包括上模板,所述上模板的顶面开有所述成型凹腔。
16.优选的,所述成型鞍上开有定位凹槽,所述成型凹腔内设有与定位凹槽对应的定位凸起。
17.优选的,所述上模板的底面安装有行程缩短机构。
18.优选的,所述行程缩短机构包括安装在上模板底面的多个延长板,所述延长板位于竖直方向,多个所述延长板的下端连接有同一连接板。
19.优选的,所述下模板上还均匀的安装有多个导向杆,多个所述导向杆位于竖直方向。
20.优选的,所述下模上还安装有定位块。
21.本发明的有益效果如下:
22.1.本发明涉及的一种飞机发动机机罩的生产方法,通过使用发动机罩整体成型模将板料一次性成型,使得生产工艺被大大缩短,仅包括一次拉延、一次修边及一次翻边,且避免了常规工艺的三段式成型再铆接所带来的工序繁多、重量增加、安全性低的问题,工艺简单,无铆接,机罩重量减小,飞机重量减小,安全性提高。
23.2.本发明涉及的一种飞机发动机机罩的生产方法,所使用的发动机罩整体成型模上设置对应的成型凹槽及成型凸楞,增大了板料在模具内的阻力,使得两端的成型凸楞之间的板料被拉紧,使得拉延时板料不走料,避免了两端的成型凸楞之间出现出现波浪、起皱及表面扭曲的问题,成型后将成型凸楞以外的部分修边,使得成品的质量优良,显著提升了拉延件的尺寸精度和外观质量。
24.3.本发明涉及的一种飞机发动机机罩的生产方法,所述凸模的成型区域设有定位凸起,所述凹模上设置有与所述定位凸起对应的定位凹槽。在拉延过程中,定位凸起与定位凹槽对应,使得拉延时,料板不易滑移。
附图说明
25.图1是一种飞机发动机机罩的生产方法的发动机罩整体成型模的下模的结构图;
26.图2是一种飞机发动机机罩的生产方法的发动机罩整体成型模的上模的结构图;
27.图3是常规三段式方法所制造的发动机机罩的结构图;
28.图4是本发明所涉及的生产方法的成品图;
29.图5是厚度的粗测定的区域选择图;
30.图6是试验4对比组的成品的表面扭曲情况;
31.图7是试验4实验组的成品的表面扭曲情况。
32.附图标注:1-下模板,2-导向杆,3-成型凸楞,4-成型鞍,5-定位凹槽,6-定位块,7-延长板,8-连接板,9-上模板,10-成型凹槽,11-成型凹腔,12-定位凸起。
具体实施方式
33.为使本发明实施例的目的、技术方案和优点更加清楚,下面将结合本发明实施例中的附图,对本发明实施例中的技术方案进行清楚、完整地描述,显然,所描述的实施例是本发明一部分实施例,而不是全部的实施例。通常在此处附图中描述和示出的本发明实施例的组件可以以各种不同的配置来布置和设计。
34.实施例1
35.一种飞机发动机机罩的生产方法,包括如下步骤:
36.步骤1、将板料置于发动机罩整体成型模内,进行拉延;
37.步骤2、对拉延后所得的粗品进行修边;
38.步骤3、对修边后的粗品进行翻边处理;
39.发动机罩整体成型模包括上模和下模,所述下模的顶面安装有成型鞍4,所述成型鞍4的轮廓与发动机罩的外形轮廓一致,所述上模的顶面开有与所述成型鞍4的轮廓一致的成型凹腔11,所述成型鞍4的顶面两端还均设有多个成型凸楞3,所述成型凹腔11内开有与成型凸楞3对应的多个成型凹槽10。
40.根据生产需求选择合适材质及规格的板料,并将所选的板料放置在发动机罩整体成型模上,将板料在发动机罩整体成型模内成型,成型结束后,将粗品裁剪去边缘多余的部分进行修边,再将粗品进行翻边处理,得到成品的发动机机罩;由于飞机发动机机罩中部较深,板料在压料面流动容易产生冷作硬化,修边后应力释放易形成波浪,同时拉延时板料在成型凸楞3上流动亦产生冷作硬化,后续翻边形成表面扭曲不平;因此通过设置对应的成型凹槽10及成型凸楞3,增大板料在模内的阻力,使得拉延时不走料,避免了两端的成型凸楞3之间出现出现波浪、起皱及表面扭曲的问题,成型后将成型凸楞3以外的部分修边,使得成品的质量优良,显著提升了拉延件的尺寸精度和外观质量;通过使用发动机罩整体成型模将板料一次性成型,使得生产工艺被大大缩短,仅包括一次拉延、一次修边及一次翻边,工艺简单,且避免了常规工艺的三段式成型(参见图4,将机罩分为a、b、c三段,进行拉延成型,再分别进行修剪整形,最后铆接在一起。)再铆接所带来的缺陷,解决了现有生产工艺所制造的机罩重量过重使得飞机安全性低,以及拉延过程中机罩两侧产生褶皱的问题。
41.实施例2
42.正如背景技术中所介绍的现有技术对发动机罩的制造是由三段件板材分别成型后再铆接起来,这样存在的主要问题是发动机罩的整体性不佳,而且加工工序较多,为此本实施例提供了一种发动机罩整体成型模,如图1-图2所示,包括上模和下模,下模包括下模板1,下模板1的顶面安装有成型鞍4,成型鞍4的轮廓与发动机罩的外形轮廓一致,上模包括上模板9,上模板9的顶面开有成型凹腔11,成型凹腔11的形状与成型鞍4的轮廓一致。
43.优选的,下模板1上还均匀的安装有多个导向杆2,多个导向杆2位于竖直方向,下模上还安装有定位块6,当上模向下模移动时,下模上的导向杆2可以对上模的移动起到导
向的作用,定位块6可以对上模起到定位的作用,从而可以使上模和下模贴合得更准确,进而可以使该模具冲压出来的发动机罩的质量更好。
44.工作原理:通过该成型模生产发动机罩时,通过常规的冲压动力装置带动上模向下模移动,将发动机罩板材冲压在成型鞍4上,由于成型鞍4的轮廓与发动机罩的外形轮廓一致,因此冲压后可以使发动机罩板材一次冲压为发动机罩,这样就不需要将三段件板材分别成型后再连接起来,从而减少了将三段件板材铆接的工序;由于是一体成型,因此发动机罩的整体性和质量更好,同时发动机罩的质量也更轻,进一步可以使飞机的机身也更轻,从而有助于实现飞机机身的轻量化。
45.还有可以转移发动机罩上褶皱的更优选结构:成型鞍4的顶面两端还均设有多个成型凸楞3,成型凹腔11内开有与成型凸楞3对应的多个成型凹槽10。
46.若直接对发动机罩进行一次冲压成型,由于发动机罩板材的变形回弹,会在成型后的发动机罩的中间局部位置有回弹起皱的现象,这样会影响到发动机罩的外观和质量;为此采用本实施例中的技术方案,其中成型凸楞3具有控制材料流量的作用,当上模和下模冲压结合在一起时,成型凸楞3和成型凹槽10会给发动机罩一定的作用力,在该作用力的作用下可以将原本应该在发动机罩中间产生的褶皱转移到发动机罩的边沿附近部位,然后通过常规的方式再将发动机罩的边沿附近处的褶皱切除,这样可以减少发动机罩上的褶皱,从而使生产出来的发动机罩的外观和质量更好。
47.更加便于切除发动机罩上褶皱的优选结构为:成型鞍4上开有定位凹槽5,成型凹腔11内设有与定位凹槽5对应的定位凸起12。
48.还可以将发动机罩上的褶皱转移到发动机罩的边沿附近,这样就可以将边沿附近的褶皱直接切除掉,切除褶皱的时候需要将发动机罩安装在另外的工位,为了让成型后的发动机罩在切割褶皱时更加便于定位,为此给出了本实施例中的技术方案;当冲压发动机罩时,定位凸起12会进入定位凹槽5内,定位凸起12和定位凹槽5的搭配,可以在发动机罩上成型出一个凹陷槽,在切割发动机罩上的褶皱时,利用这个凹陷槽可以起到定位作用,从而可以更加便于切除发动机罩上的褶皱。
49.可以减少带动上模移动的冲压动力装置行程的优选结构为:上模板9的底面安装有行程缩短机构,行程缩短机构包括安装在上模板9底面的多个延长板7,延长板7位于竖直方向,多个延长板7的下端连接有同一连接板8。
50.带动上模移动的冲压动力装置需要具有一定的行程才能使上模到达下模处,并完成对发动机罩板材的冲压,但是在一定的空间条件、冲压动力装置的具体要求下,对冲压动力装置的行程有一定的要求,总之适当减少冲压动力装置的行程更好,为此提出了本实施例中的技术方案;多个延长板7间是空的,这样不但可以增加上模的厚度,而且不至于使上模的重力过大,由于增加了上模的厚度,冲压动力装置伸出更短的行程就可以使上模到达下模处,并完成对发动机罩的冲压,因此可以根据实际情况设置延长板7的长度,以此来改变上模的厚度,最终来调整冲压动力装置的行程,从而可以使冲压动力装置更容易带动上模向下模进行冲压。
51.实施例3
52.在实施例1的基础上,选择的料板为dc01冷轧钢板。生产步骤如下:
53.步骤1、将冷轧钢板料置于发动机罩整体成型模内。
54.步骤2、开启油压机进行压制,所述油压机的顶杆行程为550~600mm,所述油压机的液垫压力为12~16mpa,所述油压机的保压时间为20s。
55.步骤3、对拉延后所得的粗品进行修边:将成型凸楞外沿的部分修剪掉。
56.步骤4、对修边后的粗品进行翻边处理,将粗品放置在翻边模具内进行翻边(翻边模具为本领域常规设置。);最终制得冷轧钢材质的飞机发动机机罩。
57.实施例4
58.在实施例1的基础上,选择的料板为2024-o的铝合金板料,由于铝合金硬度及强度较高,成形性能较低,因此将拉延压制次数设定为9次。生产步骤如下:
59.步骤1、将铝合金板料置于发动机罩整体成型模内。
60.步骤2、开启油压机进行九个阶段的压制,第一阶段油压机的液垫压力为12mpa,顶杆行程为600mm;第二阶段油压机的液垫压力为12mpa,顶杆行程为450mm,;第三阶段油压机的液垫压力为12mpa,顶杆行程为400mm;第四阶段油压机的液垫压力为12mpa,顶杆行程为350mm;第五阶段油压机的液垫压力为12mpa,顶杆行程为300mm;第六阶段油压机的液垫压力为15mpa,顶杆行程为250mm;第七阶段油压机的液垫压力为15mpa,顶杆行程为200mm;第八阶段油压机的液垫压力为15mpa,顶杆行程为150mm;第九阶段油压机的液垫压力为15mpa,顶杆行程为100mm,每个阶段的油压机保压时间均为20s。
61.步骤3、对拉延后所得的粗品进行修边:将成型凸楞外沿的部分修剪掉。
62.步骤4、对修边后的粗品进行翻边处理,将粗品放置在翻边模具内进行翻边;最终制得铝合金材质的飞机发动机机罩。
63.实施例5
64.在实施例1的基础上,选择的料板为ly12m的硬铝合金板料的,由于硬铝合金硬度及强度较高,成形性能较低,因此将拉延压制次数设定为9次。
65.步骤1、将硬铝合金板料置于发动机罩整体成型模内;
66.步骤2、开启油压机进行压制,压制分为九个阶段,第一阶段至第五阶段油压机的液垫压力均为8.5mpa,第六阶段至第九阶段油压机的液垫压力为7.5mpa,第一阶段油压机的顶杆行程为600mm,第二阶段油压机的顶杆行程为450mm,第三阶段油压机的顶杆行程为400mm,第四阶段油压机的顶杆行程为350mm,第五阶段油压机的顶杆行程为300mm,第六阶段油压机的顶杆行程为250mm,第七阶段油压机的顶杆行程为200mm,第八阶段油压机的顶杆行程为150mm,第九阶段油压机的顶杆行程为100mm,每个阶段油压机的保压时间均为20s。
67.步骤3、对拉延后所得的粗品进行修边:将成型凸楞外沿的部分修剪掉。
68.步骤4、对修边后的粗品进行翻边处理,将粗品放置在翻边模具内进行翻边;最终制得硬铝合金材质的飞机发动机机罩。
69.性能试验
70.对实施例3-5所涉及的一种飞机发动机机罩的生产方法所制得的发动机机罩进行性能试验。
71.1.厚度的粗测定
72.1.1试验设计
73.参见图5,试验设置a、b、c、d,4个区域组,随机选取实施例4所得的成品机罩8件分
别测定每件成品机罩的四处区域的机罩厚度,得出平均值。
74.1.2参数指标及检测方法
75.发动机机罩的生产质检标准规定的机罩厚度标准值为1.8mm,测定仪器选用:tessonics测厚仪(型号为ttg1),料板的初始厚度为2.3mm。
76.1.3试验结果及分析
77.表1成品机罩的厚度的粗测定
[0078][0079]
参照表1可以看出,所选的机罩1-8的四处区域组的厚度平均值均大于机罩厚度标准值1.8mm,均满足质检标准。
[0080]
2.平均减薄率的计算
[0081]
参照表1的数据,根据减薄率公式:厚度平均值
÷
料板初始厚度
×
100%=平均减薄率,计算本工艺流程所涉及的生产方法的机罩的平均减薄率,结果见下表2。
[0082]
2.1计算结果及分析
[0083]
表2成品机罩的平均减薄率
[0084]
区域abcd平均值平均减薄率(%)9.112.110010.4
[0085]
参照表2的数据,本发明所涉及的工艺流程所生产的机罩的4处区域的平均减薄率的均值为10.4%,均小于质检标准所述的12.8%的减薄率,符合质检标准,性能优良。
[0086]
3.产品表面扭曲情况的分析
[0087]
3.1试验设计
[0088]
对本发明所涉及的工艺流程所生产的机罩进行产品表面扭曲情况的分析。设计两组试验,皆选取的2024-o的铝合金板料,实验组为根据实施例4所涉及的工艺流程制造的成品机罩1件,并记录产品的表面的扭曲情况,产品情况参见图6;对比组现有常用的三段成型工艺,制造成品机罩1件,并记录产品外周的扭曲情况,产品情况参见图7。
[0089]
3.2结果及分析
[0090]
参照图7,可见使用现有常用的三段成型工艺所制造成品机罩的表面有明显的起皱现象,而参见图6,使用本发明所涉及的工艺流程所生产的机罩表面光滑无起皱现象。
[0091]
与常规工艺的对比分析
[0092]
参见图3,常规工艺的三段式成型,将机罩分为a、b、c三段,进行拉延成型,再分别进行修剪整形,最后铆接在一起。而本发明参见图4所示,将整个机罩一次性成型。
[0093]
在实际的生产中,采用常规的三段式成型,需要多开2副成型模具,工装开发费用约为261万,而采用本发明所涉及的生产方法,节约了成本,工装开发费用约为164万,总计
节约97万。
[0094]
综上所述,本发明通过使用发动机罩整体成型模将板料一次性成型,使得生产工艺被大大缩短,避免了常规工艺的三段式成型再铆接所带来的缺陷,所生产的成品性能优良、表面光滑无起皱现象。