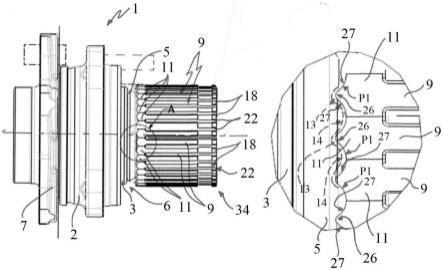
1.本发明涉及用于通过塑性变形在轮毂的内圈上形成前齿部(front toothing)的方法。本发明还涉及用于实现根据本发明的方法的相关设备。
2.特别地,本发明适用于轮毂,在该轮毂中,内圈形成转轴(/主轴/心轴)(spindle),转轴设置有带凸缘的第一端部(/第一凸缘端部)和与第一端部相对的第二端部,第二端部包括镦粗(upset)轴环(/轴圈/套圈)(collar),镦粗轴环被构造为通过压印和随后的塑性变形来接纳与形成车辆的传动系统的一部分的等速接头(/等速万向节)(constant velocity joint)机械连接并从该等速接头接收驱动传动所需的前齿部。
背景技术:3.在前述类型的轮毂中,所述前齿部的目的是将轮毂的内圈与等速接头(/等速万向节)(constant-velocity joint)的外圈的对应前齿部头对头地联接在一起,以确保扭矩从等速接头传递至轮毂的内圈,该轮毂的内圈通过其带凸缘的端部承载(/支撑)车辆的车轮。在us-a-4893960中描述了这种类型的联接(coupling),其还教导了如何在轮毂的内圈上形成前齿部(front toothing)。特别地,在形成镦粗轴环的同时,借助于工具使用所谓的“摆辗成形(/摆辗成型)(orbital forming)”方法形成前齿部,该工具包括:截头圆锥形元件,执行使轴环镦粗;以及前带齿管状元件(frontally toothed tubular element),在轴向上可滑动地安装在截头圆锥形元件的外侧,并将齿压印在仍在变形的轴环上。在径向上位于带齿管状元件外侧的元件控制轴环在径向上朝向外侧的变形,该元件可形成同一工具的一部分或者形成单独的第二工具。
4.诸如us-a-4893960中描述的成形方法需要使用相对复杂的工具,并且特别是不能确保形成具有高度均匀的齿轮廓的特征的齿,考虑到必须传递的扭矩越来越高,高度均匀的齿轮廓的特征是绝对必要的。
5.ep2551034b1基本上克服了该问题,在ep2551034b1中,齿部借助于多个滑动刀(/刮板)(sliding knives)形成,多个滑动刀在支撑件上配置成环,在角度上彼此间隔开,以允许直接安装在已经组装的轮毂的内圈上。
6.利用根据ep2551034b1的方法,可以使用明显更简单且成本更低的工具来获得前齿部的高度均匀性的尺寸。然而,不总是实现齿的正确成形,特别是关于齿的尖端(/齿尖)(tips)或脊部(ridges)的形状(往往是平坦的)。
7.这意味着,一方面,无法总是可以提供必须传递的越来越高的扭矩,另一方面,在轮毂与等速接头的组装期间,可能会发生不正确的齿对齿安装,这意味着两个组件的齿在联接期间不正确地啮合(mesh)在一起。在使用期间,当齿由于操作扭矩而最终卡扣接合到正确位置时,用于将两个组件锁定在一起的中央螺母或螺丝立即(immediately)失去在组装期间施加的紧固力,并且在轮毂和等速接头的两组接合齿之间也可能会形成少量的前游隙(front play),所述游隙不会阻止扭矩的传递,但会导致沿着轮轴(axle)的噪声,这是由于每当传递较高扭矩时,齿从正确接合位置跳出。
8.最后,在经受(/遇到)这种状况的车辆中,齿也可能逐渐磨损,最终在2wd(两轮驱动)车辆的情况下完全失去(/损失)牵引力(traction),或者在awd车辆(具有不是始终接合的四个驱动轮)的情况下仅部分失去牵引力。
9.在这两种情况下,如果驾驶员没有检测到沿着轮轴的动力损失,则这可能会随着时间的推移导致齿轮的逐渐劣化,这是因为,由于没有牵引力的轮轴仍然产生似乎合理的abs信号,因此车辆的控制单元不会及时检测到异常状况。
技术实现要素:10.因此,本发明的目的是提供用于通过塑性变形在轮毂的内圈上形成前齿部的方法和相关设备,其是现有技术的方法和设备的替代方案,并且特别地,其不仅能够确保齿的较大的尺寸精度以及在所述齿的轮廓的尺寸和几何形状方面的高度均匀性,而且特别是能够避免通过摆辗成形(/摆辗)(orbital forming)获得的前齿部中的齿的尖端或脊部变平。
11.本发明的目的还是提供用于通过塑性变形在轮毂的内圈上形成前齿部的方法和相关设备,其能够避免由于在成形操作期间由工具在内圈上施加的力而对轮毂的内圈和/或其他组件的任何可能的损坏。
12.因此,基于本发明,提供了如所附权利要求中所限定的用于通过塑性变形在轮毂的内圈上形成前齿部的方法和相关设备。
附图说明
13.从下面参照附图提供的本发明的实施方式的两个非限制性示例的描述中,本发明的其他特性特征和优点将变得清楚,在附图中:
14.图1以示意性形式示出了使用相关设备执行的根据本发明的方法的第一步骤的正视图,其中,示出了其一系列第一组件,且在旁边示出了其较大比例的细节“a”;
15.图2以示意性形式示出了与如图1所示的根据本发明的方法的第一步骤相同但使用相关设备的可型变型来执行的第一步骤的正视图,其中,示出了其一系列第一组件,且在旁边示出了其较大比例的细节“a”;
16.图3以示意性形式示出了使用相关设备执行的根据本发明的方法的第二步骤,其中,示出了一系列第二组件,且在旁边示出了其较大比例的细节“a”;以及
17.图4以示意性形式示出了图1至图3中所示的步骤的材料执行的细节。
具体实施方式
18.参照图1和图3,在这些图中,1表示轮毂整体,轮毂本身是已知的,并且为了简化图示而仅以示意性形式示出并仅示出外部,所述轮毂包括外圈2和内圈3,外圈2用于在使用期间以已知的方式紧固到车辆的悬架立柱(未示出)。外圈2和内圈3借助于两列滚动体(例如,球)(已知,并且为了简化图示而未示出)可旋转地连接在一起,两列滚动体在径向上插入圈2与圈3之间并且接合在形成于圈2和圈3中的特定环形滚道(/轨道)(tracks)(也已知,并且为了简化图示而未示出)内侧。
19.内圈3可以在使用期间以已知的方式借助于前齿部(front toothing)(图3)与等速接头(/等速万向节)(constant velocity joint)(已知,并且为了简化图示而未示出)可
操作地相关联,该前齿部以将看到的方式在对内圈3的第一端部6镦锻(upset)的环形轴环(annular collar)5上获得。内圈3还设置有已知凸缘7,凸缘7用于将车辆车轮安装在端部6的相对侧。
20.内圈3、外圈2和环形轴环5彼此同轴,具有与整个轮毂(/车轮轮毂)1的总体对称轴线重合的共用对称轴线a。
21.由于这种布局,镦粗的轴环5以已知的方式通过摆辗成形(/轨道成形)(orbital forming)获得,摆辗成形是在末端(/终端)6上执行的塑性变形操作,以借助于具有进动运动(/旋进运动)(precession movement)的旋转工具(已知,并且为了简化图示而未示出)将预定的径向轮廓赋予环形轴环5。
22.镦粗的环形轴环5设置有前齿部4,该前齿部4形成在端部6的前面(/正面)(front face)上,端部6的正面被配置为基本上垂直于轮毂1的对称轴线a,通常特别是内圈3的对称轴线a。
23.前齿部4包括多个径向齿8(图3),径向齿8形成为环形配置并且在轮毂1的内圈3的端部6上具有恒定节距,特别是在镦粗的环形轴环5上具有恒定节距,镦粗的环形轴环5在先前的步骤或操作期间已经预先形成在端部6上(已知,并且为了简化图示而未示出)。
24.在该准备操作或步骤之后,使用在总体结构方面与ep2551034b1(ep2551034b1的内容根据需要被包含(/并入)于此)中描述的设备完全类似的设备,根据本发明,通过由图1和图3中示意性地示出的两个步骤组成的方法获得前齿部4。
25.特别地,以与ep2551034b1中的方式完全相同的方式,根据本发明的方法包括用于使环形轴环5塑性变形的至少一个操作,其中,在轴向上引导多个刀(/刮板)(knives)10(图3)平行于轴线a可滑动,并且将多个刀10在轴向上且顺序地压印(impress)在环形轴环5上,多个刀10被配置成环,绕着环形轴环5的对称轴线a对称。
26.然而,根据本发明,使用刀10的步骤不是通过塑性变形形成前齿部4的方法所设想的唯一塑性变形步骤,而是在对于图3的塑性变形步骤的特征准备步骤之前的步骤,其在图1中示意性地示出。
27.为了执行图1中所示的该第一步骤,根据本发明,使用与可用于执行图3的步骤的设备完全类似的设备。总体上,用于执行图1和图3的步骤的设备在它们的总体结构方面彼此完全类似,并且与ep2551034b1中描述的设备完全类似,仅具有与现有技术不同的一些具体结构细节(如将看到的)。
28.因此,根据本发明,用于通过塑性变形形成前齿部4的方法包括第一步骤(图1),在该第一步骤中,将多个第一刀9在轴向上且可滑动地压印在环形轴环5上,多个第一刀9朝向环形轴环5设置有对应的第一成形端部11,第一成形端部11具有预定的第一周向轮廓p1。
29.第一周向轮廓p1被构造为反向(/相反地)(in reverse)再现(/复制/翻印)(reproduce)要获得的前齿部4的径向齿8的尖端或脊部12(图3)的至少一部分,以在环形轴环5上形成以环形配置的凹部(/印记/压痕)(imprints)13和凸部(/浮雕/浮凸)(reliefs)14(在图1中仅示意性地且不按比例地以虚线示出)的交替。
30.凹部13和凸部14在径向上配置成环,并且凸部14通过凹部13在周向上以恒定节距彼此间隔开。
31.此外,根据本发明,轮廓p1被构造为使得压印之后的径向凸部14具有与要获得的
径向齿8的尖端或脊部12的轮廓精确地或至少基本上对应的圆形周向轮廓,并且因此具有圆形轮廓。
32.根据本发明,用于通过塑性变形形成前齿部4的方法包括随后的第二步骤(图3),在该第二步骤中,将多个第二刀10在轴向上且顺序地压印在环形轴环5上,多个第二刀10朝向环形轴环5设置有对应的第二成形端部15,第二成形端部15具有预定的第二周向轮廓p2。
33.预定的第二周向轮廓p2被构造为完全或部分地反向再现要获得的前齿部4的径向齿8的对应的相对侧面(flanks)16(图3)的轮廓。
34.在该第二步骤期间,将第二刀10压印于在上述第一步骤期间已经在轴环5上形成的径向凹部13内部,直到在环形轴环5上形成要获得的所有前齿部4。
35.根据本发明的基本方面,在第一步骤期间,如图1中清楚地示出的,将第一刀9的第一成形端部11引导为以此周向接触、基本上没有游隙方式抵靠环形轴环5。
36.为此目的,第一刀9成形为在周向上比它们对应的第一成形端部11薄,以允许将其安装在与ep2551034b1的设备类似的设备上。此外,刀9均包括按压头(pressing head)18,按压头18配置在相应的第一成形端部11的相对侧,并且被构造为单独地接收轴向压缩力,该轴向压缩力适于将刀9的成形端部或“尖端”11推压抵靠轴环5,以在轴环5上形成凹部13。
37.根据本发明的一个方面,如在图4中的示意性细节中更清楚地示出的,头18还被组装成在彼此之间保持小的周向间隙200,并且为了在允许刀9容易地组装的同时获得对刀9的最佳引导,优选将头18头对头地抵靠相应的第三刀19(与刀9同轴地安装)安装。
38.刀19具有按压头180,按压头180配置在刀9的相对侧并且被配置为基本上彼此接触,即具有大致为零或在任何情况下都非常小的周向间隙。按压头180被构造为各自单独地与具有相同的摆辗成形头32(已知,并且在图4中仅示意性地且以虚线示出)配合(/协作),摆辗成形头32具有进动旋转运动(precession rotating movement)。
39.因此,按压头32在使用期间选择性地并且借助于插入的刀19将刀9推压抵靠轴环5,以形成凹部13,并且因此,通过借助于刀9从凹部13“移位”的金属材料形成凸部14。
40.组合以上内容并且根据本发明的另一基本方面,在第二步骤期间,将第二刀10(图3)的第二成形端部15引导为抵靠环形轴环5,第二成形端部15在周向上彼此间隔开,使得在每个第二成形端部15与刀10的紧邻所述每个第二成形端部15的第二成形端部15之间存在预定周向间隙20(参见图3右侧的较大比例细节)。
41.该预定周向间隙20被设置为与在第一步骤结束时获得的径向凸部14的周向延伸部基本上相同,使得当刀10压印抵靠轴环5时,刀10不影响(至少不直接影响)凸部14,因此在刀10形成齿8的侧面16的同时,凸部14保持基本不变并且逐渐形成,一旦完成侧面16,则齿8的尖端或脊部12形成。
42.为此目的,每个第二刀10包括按压头21,按压头21配置在相应的第二成形端部15的相对侧,并且被构造为在周向上与第二刀10的紧邻其的相应成形端部15无游隙地接触配合。
43.反之亦然,如上所述并且如图4中示意性地示出的,刀9的按压头18被配置并且被操作,从而在它们之间保持预定的周向间隙200。
44.第二刀10的按压头21还被构造为单独地和选择性地与推动元件配合,在这种情况下,推动元件直接由已知的具有进动旋转运动的摆辗成形头23形成,摆辗成形头23与用于
刀9的摆辗成形头32类似或相同。
45.根据本发明的一个方面,第二刀10的第二成形端部15的第二周向轮廓p2被构造为使得每个第二成形端部15具有圆形的尖端或脊部24,尖端或脊部24反向再现要获得的前齿部4的两个紧邻径向齿8的对应的相对侧面16的周向轮廓以及要获得的前齿部的各个凹面(concavity)或凹陷(depression)25的周向轮廓,凹面或凹陷25存在于前齿部4的每对两个紧邻的径向齿8之间。
46.根据本发明的另一方面,第一刀9的第一成形端部11的第一周向轮廓p1以鸥形翼(gull wings)的方式成形。
47.特别地,每个第一成形端部11包括圆形的尖端或脊部26,尖端或脊部26被构造为在环形轴环5上形成径向凹部13之一。
48.每个第一成形端部11还包括一对相对的弯曲凹形侧面27。根据本发明的一个方面,两个相邻第一成形端部11中的每一个的相对的凹形侧面27被构造为一起再现要获得的前齿部4的径向齿8的尖端或脊部12的最终的基本上或精确的圆形轮廓。
49.现在参照图2,其以示意性形式示出了根据本发明的方法的图1所示的第一步骤的可行变型。为了简化图示,使用相同的附图标记指示与已经描述的细节类似或相同的细节。
50.根据该变型(已经描述的所有其余部分保持完全相同),代替第一刀9,使用第一刀90来执行本发明的方法的第一步骤,所述刀90与刀9的不同之处仅在于:刀90具有第一成形端部29,第一成形端部29具有与刀9的第一成形端部11的形状不同的形状。
51.特别地,刀90的第一成形端部29具有第一周向轮廓p3,该第一周向轮廓p3由形成在每个第一刀90内部的凹面30以及每个第一刀90的朝向凹面30成圆形的一对周向相对侧面31界定。
52.每个第一刀90的相对侧面31被配置为在周向上与紧邻其的另外两个第一刀90的相应的相对侧面31接触。
53.每个第一刀90的相对侧面31也成形为,使得彼此相邻的两个第一刀90的每对相对侧面31被构造为在环形轴环5上形成所述径向凹部13之一。
54.反之亦然,形成在每个第一刀90内部的凹面(concavity)30被构造为再现(reproduce)要获得的前齿部4的径向齿8的尖端或脊部12的最终圆形轮廓。
55.图1和图2中所示的根据本发明的方法的第一步骤的两个实施方式之间的主要差异在于刀9和90的不同形状,刀9和90具有相关联的成形端部11和29,使得要获得的齿部4的齿8的尖端或脊部12可以在第一步骤结束时已经形成,但是在图1的实施方式的情况下,通过借助于一对相邻的刀9来实现每个尖端或脊部12,或者在图2的实施方式的情况下,通过借助于每个单个刀90来实现每个尖端或脊部12。
56.从到此为止提供的描述中,最后清楚的是,本发明也适用于设备33(图4)(在图1或图2和图3中仅部分地示出),以在轮毂1的内圈3上形成包括多个径向齿8的前齿部4,其中,内圈3在其第一端部6处设置有具有预定径向轮廓的环形轴环5,设备33包括多个刀9或90和10,多个刀9或90和10被配置成环,绕着环形轴环5的对称轴线a对称,并且借助于与ep2551034b1中描述的机器设计完全类似的机器设计在轴向上被引导为平行于对称轴线a可滑动,其中,刀9或90被构造为借助于摆辗成形头32在轴向上且顺序地压印在环形轴环5上,且刀19配置在刀9或90与摆辗成形头32之间;并且,其中,刀10被构造为借助于摆辗成形
头23(摆辗成形头23也可以由相同的摆辗成形头32代替)在轴向上且顺序地压印在环形轴环5上。
57.根据本发明,该设备33以组合的方式包括:
58.第一组34或34b(图1和图2)的第一刀9或90,分别具有第一成形端部11或29,第一成形端部11或29具有与要获得的前齿部4的齿8的对应尖端或脊部12的周向轮廓反向相对应的第一周向轮廓p1或p3,第一刀9或90被构造为在其第一成形端部11或29的一侧压印抵靠环形轴环5,以在环形轴环5上形成多个圆形径向凸部14和多个径向凹部13,多个圆形径向凸部14构成要获得的前齿部4的径向齿8的所有尖端或脊部12,多个径向凹部13、将径向凸部14在周向上彼此分开;以及
59.第二组35(图3)的第二刀10,具有第二成形端部15,第二成形端部15具有与要获得的前齿部4的径向齿8的对应的相对侧面16的周向轮廓的至少一部分反向相对应的第二周向轮廓p2。
60.然而,第二刀10被构造为:在第一刀9或90之后在其第二成形端部15的一侧压印抵靠环形轴环5并且压印抵靠在径向凹部13内部,以在环形轴环5上形成要获得的所有前齿部4。
61.组35的第二刀10的可以替换刀9(或90)组装在单个摆辗成形机器或设备上,或者优选永久地组装在与前述设备基本上相同的第二摆辗成形设备33c(图3)上,除了不存在刀19(不再需要)并且存在替换刀9(或90)的刀10以及用于可滑动地支撑它们的系统(考虑到它们的不同功能)之外。
62.事实上,除了存在两个单独组34、34b和35的成形刀9(或90)之外,设备33(和33c,未以限制性方式示出)具有以下基本特征:第一刀9、90的第一成形端部11、29被配置为在周向上彼此接触,基本上没有游隙;而第二刀10的第二成形端部15被配置为在周向上彼此间隔开,使得每个第二成形端部15与紧邻其的第二成形端部15之间存在预定的周向间隙20。
63.此外,组34(或34b)中的第一刀9(或90)在周向上比它们对应的第一成形端部11(或29)薄,以确定周向间隙200的存在。
64.最终,第一刀9(或90)和第二刀10两者各自包括按压头18、21,按压头18、21配置在相应的第一成形端部11或29或者第二成形端部15的相对侧,第一刀9、90的按压头18被配置为具有周向游隙并且被构造为各自单独地借助于刀19间接与摆辗成形头32配合,第二刀10的按压头21被配置为彼此周向接触并且被构造为各自单独地直接与摆辗成形头23配合。
65.基本上,根据现有技术,齿的最终形状在凹口工艺(/压凹工艺)(indentation process)期间限定,该工艺需要相当大的力,然而,为了避免损坏轴承,必须限制该力,因为它实际上施加在单个点处(每个齿单独形成)。冲突需求之间的这种折衷创建了齿的模型,但每个齿的尖端几乎是平坦的。为了产生正确的圆形尖端,将需要额外的力,存在损坏设备和/或轮毂的风险。
66.相反,根据本发明,成形工艺被分成两个步骤。在第一步骤中,仅执行将形成齿的顶部的成圆形(rounding):在该步骤期间,基本上创建(/产生)由凹部13和凸部14形成的齿的“外形(outline)”,其中,由凸部14限定的“齿”的总深度会相当小。
67.代替,在第二步骤中,执行凹部13的显著变形,从而创建齿8的其余部分,且更多的注意力集中在齿8的侧面16的形成以及齿8的由凹面或凹陷25限定的“根部”上。以这种方
式,由设备33传递到轮毂1的载荷在两个步骤之间被均等地分配。
68.如图1和图2所示,可以使用在第一成形端部11或29的设计和形状方面不同的设备33来执行第一步骤(创建齿8的尖端或脊部12的圆形形式)。每对相邻刀(9或90)之间的分界线可以位于齿8的顶部上(图1),或者位于底部处(凹陷25的最大深度处)(图2)。刀的形状也可以根据期望的结果而不同(在齿8的顶部12处和在凹陷25的中间的底部处,都可以具有小半径或大半径)。
69.由于分成两个步骤,最终,可以以较低的轴向力操作刀9、90和10,从而节省能量并且避免损坏工具和/或轮毂的风险。
70.因此,实现了所有目的。