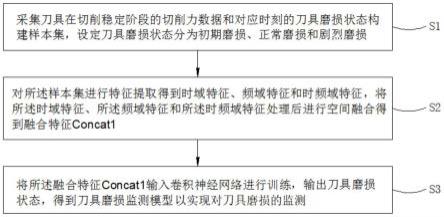
1.本发明属于铣削加工刀具磨损监测技术领域,尤其涉及一种基于多特征空间卷积神经网络的刀具磨损监测方法。
背景技术:2.随着国家航空航天、航母和兵器工业的发展,对产品零部件的材料性能有了更严格的要求,出现了各种高硬度、高强度、高韧性的工程材料(如超高强度钢、钛合金、高温合金等)。采用铣削工艺加工上述材料,存在着刀具急剧磨损的问题。磨损的刀具不仅增大切削力,而且会降低加工表面质量,进而影响零部件的服役性能。因此,对铣削过程的刀具磨损状态进行监测具有重要意义。
3.刀具磨损状态辨识实际上属于模式识别的范畴,是一个提取故障特征进行映射表征的过程,即设计一个非线性分类器,将特征空间映射到目标空间。常用的非线性分类器有高斯过程回归、bp神经网络和支持向量积。由于一维卷积神经网络具有时移不变性,近些年已被广泛应用于处理诸如切削力、振动等时序信号。
4.现有的刀具磨损监测技术虽然有了一定程度的发展,但在实际生产工况中仍然存在漏报、误报、实时性差等问题。因此有必要提出更有效的、能够满足实际加工需要的刀具磨损监测方法。
技术实现要素:5.针对现有技术存在的不足及改进需求,本发明提供了一种基于多特征空间卷积神经网络的刀具磨损监测方法。其目的在于有效地监测铣削加工中的刀具磨损状态,为刀具寿命评估及换刀提供参考。
6.本发明通过以下技术方案来实现上述目的:
7.一种基于多特征空间卷积神经网络的刀具磨损监测方法,包括以下步骤:
8.s1:采集刀具在切削稳定阶段的切削力数据和对应时刻的刀具磨损状态构建样本集,设定刀具磨损状态分为初期磨损、正常磨损和剧烈磨损;
9.s2:对所述样本集进行特征提取得到时域特征、频域特征和时频域特征,将所述时域特征、所述频域特征和所述时频域特征处理后进行空间融合得到融合特征concat1;
10.s3:将所述融合特征concat1输入卷积神经网络进行训练,输出刀具磨损状态,得到刀具磨损监测模型。
11.作为本发明的进一步优化方案,所述s1中使用测力仪实时采集切削稳定阶段的切削力数据,采用移动滑窗法对所述切削力数据进行划分,并与刀具磨损状进行对应,进而构建样本集。
12.作为本发明的进一步优化方案,所述s2中得到融合特征concat1的具体步骤如下:
13.s201:对所述样本集采用离散小波变换进行去噪处理,得到时域特征;对所述时域特征进行快速傅立叶变换得到频域特征;将所述时域特征经过小波变换得到的小波系数作
为时频域特征;
14.s202:分别将所述时域特征、所述频域特征和所述时频域特征与大小为5
×
5的卷积核进行卷积操作得到卷积特征c1、卷积特征c2和卷积特征c3;
15.s203:分别将所述卷积特征c1、所述卷积特征c2和所述卷积特征c3与尺寸为3
×
3的池化核进行池化处理得到池化特征p1、池化特征p2和池化特征p3,池化步长为3;
16.s204:将所述池化特征p1、所述池化特征p2和所述池化特征p3进行拼接融合得到大小为165
×
96的所述融合特征concat1。
17.作为本发明的进一步优化方案,所述s201中对所述样本集采用离散小波变换进行去噪处理,离散小波变换所使用的小波基函数为daubechies小波,其尺度函数φ(x)和小波函数ψ(x)可表示如下:
18.φ(x)=∑
kak
φ(2x-k)
19.ψ(x)=∑
kbk
φ(2x-k)
20.式中,k为平移量,ak和bk分别为尺度函数和小波函数的系数。
21.作为本发明的进一步优化方案,所述s3中的卷积神经网络采用inception架构。
22.作为本发明的进一步优化方案,所述s3的具体步骤如下:
23.s301:将所述融合特征concat1与大小为1
×
1的卷积核进行卷积操作得到大小为165
×
32的卷积特征c4;将所述融合特征concat1进行无尺寸变化池化操作得到大小为165
×
96的池化特征p4,将所述池化特征p4与大小为1
×
1的卷积核进行卷积操作得到大小为165
×
32的卷积特征c5;将所述融合特征concat1与大小为1
×
1的卷积核进行卷积操作得到大小为165
×
48的卷积特征c6,将所述卷积特征c6与大小为3
×
3的卷积核进行卷积操作得到大小为165
×
64的卷积特征c7;将所述融合特征concat1与大小为1
×
1的卷积核进行卷积操作得到大小为165
×
16的卷积特征c8,将所述卷积特征c8与大小为5
×
5的卷积核进行卷积操作得到大小为165
×
16的卷积特征c9;
24.s302:将所述卷积特征c4、所述卷积特征c5、所述卷积特征c7和所述卷积特征c9进行拼接融合得到大小为165
×
144的融合特征concat2;
25.s303:将所述融合特征concat2与大小为5
×
5的卷积核进行卷积操作得到大小为161
×
32的卷积特征c10;
26.s304:将所述卷积特征c10进行池化操作,池化核尺寸为3
×
3、池化步长为3,得到大小为53
×
32的池化特征p5;
27.s305:将所述池化特征p5与大小为5
×
5的卷积核进行卷积操作得到大小为49
×
32的卷积特征c11;
28.s306:将所述卷积特征c11进行全局池化操作得到尺寸为32的池化特征p6;
29.s307:将所述池化特征p6与全连接层相连,通过softmax分类器获得分类结果,并将误差反向传播,得到训练完成的刀具磨损监测模型。
30.作为本发明的进一步优化方案,所述卷积操作均为一维卷积,卷积层运算如下:
[0031][0032]
式中,a
l-1
为第l-1层特征矩阵,k
l
为第l层卷积核,卷积核仅沿时间轴进行移动进行一维卷积操作,b
l
为第l层偏置向量,g为relu激活函数。
[0033]
作为本发明的进一步优化方案,所述s307中softmax分类器的交叉熵损失函数如
下所示:
[0034]
loss=-∑iyilogf(zi)
[0035][0036]
式中,yi为当前样本的真实标签,zi为全连接层的输出结点值,f为softmax函数。
[0037]
本发明的有益效果在于:
[0038]
本发明改善了人工提取特征与单特征空间在表征能力上的不足,实现了对多特征空间的自适应提取与融合;此外,卷积网络采用inception架构,在提高模型宽度的同时可减少模型的训练参数,不仅提高了模型的表征能力,而且降低了过拟合的风险。本发明具有适用性强、监测精度高等优点,可准确地辨识刀具磨损状态,满足实际加工中的需要。
附图说明
[0039]
图1是本发明的方法流程框图;
[0040]
图2是本发明的方法具体流程框图;
[0041]
图3(a)-(c)分别为刀具初期磨损、正常磨损和剧烈磨损时期的三向切削力样本数据;
[0042]
图4(a)-(c)分别为刀具初期磨损、正常磨损和剧烈磨损的显微照片;
[0043]
图5为inception卷积神经网络架构。
具体实施方式
[0044]
下面结合附图对本技术作进一步详细描述,有必要在此指出的是,以下具体实施方式只用于对本技术进行进一步的说明,不能理解为对本技术保护范围的限制,该领域的技术人员可以根据上述申请内容对本技术作出一些非本质的改进和调整。
[0045]
实施例1
[0046]
如图1-5所示,一种基于多特征空间卷积神经网络的刀具磨损监测方法,包括以下步骤:
[0047]
(1)开展刀具磨损试验,使用测力仪实时采集三向切削力信号,并且每间隔一定的切削长度观测刀具磨损状态。取出切削稳定阶段的切削力数据,采用移动滑窗法划分数据集,进而构建样本集(如图3所示);其中,采样频率为10k,样本集大小为7680
×
500
×
3;
[0048]
(2)根据步骤(1)刀具磨损试验观测的刀具磨损状态(如图4所示)对样本集贴标签,包括初期磨损、正常磨损和剧烈磨损3类;
[0049]
(3)针对步骤(1)构建的样本集,在时域空间下,采用离散小波变换(dwt)对信号进行去噪处理;进一步,将去噪后的时域信号进行快速傅立叶变换(fft)得到频域信号;另外,将时域信号经过小波变换(wt)得到的小波系数作为时频域信号;在模型训练前,为保证样本数据在一个较小的范围内,将上述时域、频域和时频域信号分别进行归一化处理;
[0050]
其中,离散小波变换所使用的小波基函数为daubechies小波,其尺度函数φ(x)和小波函数ψ(x)可表示如下:
[0051]
φ(x)=∑
kak
φ(2x-k)
[0052]
ψ(x)=∑
kbk
φ(2x-k)
[0053]
式中,k为平移量,ak和bk分别为尺度函数和小波函数的系数。
[0054]
(4)将步骤(3)特征处理后获得的特征作为卷积神经网络的输入进行训练,输出为过程(2)中贴好的标签;其中,卷积神经网络采用如图5所示的inception架构,训练过程具体包括:
[0055]
(4.1)将时域信号与大小为5
×
5的卷积核进行卷积操作,得到496
×
32的卷积特征c1;随后进行池化操作,池化核尺寸为3
×
3、池化步长为3,得到165
×
32的池化特征p1;对于频域信号和时频域信号,进行同样的卷积和池化操作后,分别得到池化特征p2和p3;
[0056]
本发明所述卷积操作均为一维卷积,卷积层运算可表示如下:
[0057][0058]
式中,a
l-1
为第l-1层特征矩阵,k
l
为第l层卷积核,两者进行一维卷积操作,即卷积核仅沿时间轴进行移动;此外,b
l
为第l层偏置向量,g为relu激活函数。
[0059]
(4.2)将池化特征p1、p2、p3沿最后一个维度进行拼接融合,得到融合特征concat1,大小为165
×
96;
[0060]
(4.3)将融合特征concat1与大小为1
×
1的卷积核进行卷积操作,得到165
×
32的卷积特征c4;
[0061]
(4.4)将融合特征concat1进行无尺寸变化池化操作,得到165
×
96的池化特征p4,进一步与大小为1
×
1的卷积核进行卷积操作,得到165
×
32的卷积特征c5;
[0062]
(4.5)将融合特征concat1与大小为1
×
1的卷积核进行卷积操作,得到165
×
48的卷积特征c6,进一步与大小为3
×
3的卷积核进行卷积操作,得到165
×
64的卷积特征c7;
[0063]
(4.6)将融合特征concat1与大小为1
×
1的卷积核进行卷积操作,得到165
×
16的卷积特征c8,进一步与大小为5
×
5的卷积核进行卷积操作,得到165
×
16的卷积特征c9;
[0064]
(4.7)将卷积特征c4、c5、c7、c9沿最后一个维度进行拼接融合,得到大小为165
×
144的融合特征concat2;
[0065]
(4.8)将融合特征concat2与大小为5
×
5的卷积核进行卷积操作,得到161
×
32的卷积特征c10;随后进行池化操作,池化核尺寸为3
×
3、池化步长为3,得到53
×
32的池化特征p5;
[0066]
(4.9)将池化特征p5与大小为5
×
5的卷积核进行卷积操作,得到49
×
32的卷积特征c11,进一步进行全局池化操作,得到尺寸为32的池化特征p6;
[0067]
(4.10)将池化特征p6与全连接层相连,通过softmax分类器获得分类结果,并将误差反向传播。
[0068]
其中,softmax交叉熵损失函数可表示如下:
[0069]
loss=-∑iyilogf(zi)
[0070][0071]
式中,i和j代表某种类别,yi为当前样本的真实标签,zi为全连接层的输出结点值,f为softmax函数。
[0072]
本发明采用自建的刀具磨损数据集,包括三向切削力数据和刀具磨损状态标签。故障分类的训练样本为5376,测试样本为2304。经过参数优选,测试精度达到99.87%以上,
能较好满足实际加工中的刀具磨损监测需求。
[0073]
以上所述实施例仅表达了本发明的一种实施方式,其描述较为具体和详细,但并不能因此而理解为对本发明专利范围的限制。应当指出的是,对于本领域的普通技术人员来说,在不脱离本发明构思的前提下,还可以做出若干变形和改进,这些都属于本发明的保护范围。