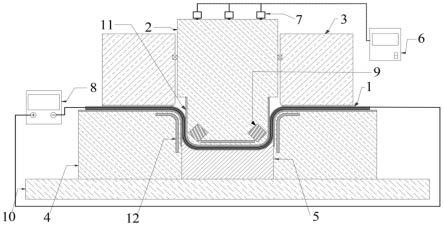
1.本发明涉及纤维金属层板的成形加工领域,更具体地说,涉及一种电磁超声辅助纤维金属层板冲压变形方法。
背景技术:2.纤维金属层板是一种由高强度金属薄板与纤维预浸料相互交替铺层,经一定固化工艺成型后得到的超混杂结构材料,与单一金属板材相比,具有轻质、高强、良好的导电性、优良的抗冲击和损伤容限性能、良好的阻燃性能及耐腐蚀性能等优点,因而在航空航天、军工武器、高速运载工具等领域具有广阔的应用前景。在上述领域中,纤维金属层板弯曲件常常作为桁架材料,因为其应用的工况往往极端苛刻,且需求量大,不仅对其可靠性有极高要求,同时也需要高效率的生产工艺方法。
3.纤维金属层板弯曲件作为在航空航天、军工武器、高速运载等领域的重要构件,其成形质量直接决定了构件的服役寿命,甚至进一步关乎上述领域的运载安全。现有的复杂异形纤维金属复合层板件往往是通过选用很薄的金属层板分步冲压后,在金属板间分步铺设纤维材料,最后进行固化的工艺来制造的。这种铺层方法易因树脂流动性强,而导致纤维树脂层厚度不均,界面结合效果差,且固化过程时间长,制造工序复杂,生产效率低下。
4.现有的冲压工艺成形纤维金属层板构件,主要是围绕特定的纤维金属层板圆桶件结构的成形,一般成形的层数较少,成形极限低,且易出现破裂、褶皱、树脂基体断裂、金属与纤维树脂分层等缺陷,成形质量差、精度差,无法可靠的应用在高精尖领域。
技术实现要素:5.本发明要解决的技术问题在于,提供一种电磁超声辅助纤维金属层板冲压变形方法,该方法纤维间树脂分布均匀、厚度一致性好,层间界面结合效果优良,显著提升了生产效率,提高了可成形层数及成形极限,破裂、褶皱及树脂基体断裂等成形缺陷明显减少,大幅降低了金属层板开裂率及界面脱层率,并较好地控制了回弹,极大提升了成形质量和精度。
6.本发明解决其技术问题所采用的技术方案是:构造一种电磁超声辅助纤维金属层板冲压变形方法,包括以下步骤:
7.s1、将金属薄板与纤维预浸料相互交替铺层,作为纤维金属层板预制料;
8.s2、将纤维金属层板预制料放置在软模容框上,上压边下压固定预制料;
9.s3、将纤维金属层板预制料两端通过夹具与脉冲电流发生器的正负两电极分别相连;
10.s4、凸模下行,同时,通过脉冲电流发生器给纤维金属层板预制料施加脉冲电流作用,并通过在励磁线圈中通入交变电流,形成脉冲磁场,作用于纤维金属层板预制料,进行电磁耦合辅助处理;
11.辅助电脉冲处理过程包括:常温下,对纤维金属层板预制料金属层施加电脉冲作
用,电脉冲有效电流密度为2
×
107a/m2~8
×
107a/m2,单个电脉冲作用时间为10~100ms,每施加完一次电脉冲作用后间歇30~200ms;
12.辅助磁脉冲处理过程包括:在励磁线圈内通入电压为2~3kv的电流,单次通电时长为1~2ms,每次通电后间隔0.4~1s,通电次数为2~5次,从而实现磁脉冲处理;
13.s5、待凸模下行至目标成形位置时,停止凸模进给和电磁耦合处理,凸模保持停留在目标位置;
14.s6、通过超声振动探头,对变形后的纤维金属层板预制料施加超声振动,保障金属层与纤维层间的结合效果;
15.s7、所述步骤s6中的超声振动施加完毕,对纤维金属层板预制料进行加热固化处理;
16.s8、固化完成后,停止加热,退回凸模,取出成形纤维金属层板。
17.按上述方案,所述凸模、软模容框及压边与纤维金属层板预制料的接触面采用活性金属钎焊法设置氮化硅陶瓷绝缘层,金属模及钎料采用ag-cu-ti+mo。
18.按上述方案,所述步骤s7中采用在压边与凸模中设置加热电阻的方式对其进行加热。
19.按上述方案,所述步骤s7中的加热过程分为两段,首先加热到较低温度,使树脂达到凝胶状态,之后进一步加热到预固化温度。
20.按上述方案,施加的超声振动由超声波发生装置产生,通过超声振动探头由凸模向纤维金属层板预制料传导,振动频率为15~25khz,振动压力为0.2~0.8mpa,振动幅值为30~80μm,振动持续时间为4~10s。
21.按上述方案,通过向纤维金属层板预制料弯角部位施加磁脉冲,在电磁力驱使下,使得弯角部位圆角半径逐渐减小并贴膜,能有效控制回弹,同时利于材料的均匀流动,使得弯角部位的应变分布更均匀。
22.按上述方案,通过向纤维金属层板预制料金属层施加电脉冲,可以利用电致塑性效应,通过热效应和电子风力,使得金属层的抗形变应力的下降和塑性的提高,从而减少甚至避免破裂和褶皱的发生。
23.按上述方案,所述超声振动能够促进胶液在纤维与金属层之间的流动,使其分布均匀,从而减少纤维层内部的孔隙等缺陷,同时提升层间的界面结合效果。
24.按上述方案,软模可以提供法向压应力,提高构件成形性,在解决纤维金属层板变形时的塑性差、应变梯度大问题时起到明显作用,从而提高成形质量。
25.按上述方案,所述步骤s4中,电脉冲的波形为方波
26.本发明具体原理如下:
27.首先,本发明采用高强度金属薄板与纤维预浸料相互交替铺层,不需固化,以该预制料作为冲压对象,保障在冲压过程中金属层间相互关系良好,同时使树脂分布及流动更均匀,利于形成厚度均匀良好的纤维金属层板件。
28.其次,本发明采用合理的电磁耦合脉冲工艺对冲压变形中的预制料进行处理,加入脉冲电流辅助时,金属材料会在内部焦耳热和电子风力的作用下,在材料中引起再结晶、相变现象,从而实现电致塑性,可以有效提高金属层的塑性成型能力;加入脉冲磁场辅助,可以通过降低活化能来增加金属材料内部位错运动的可能性,同时通过磁致伸缩诱发的磁
振动为位错运动提供能量,使得位错分布均匀化,从而降低金属层内部的残余应力,有效控制回弹;从而使得冲压变形中金属层不易发生破坏,避免成形后的弯曲件过度回弹。
29.第三,超声振动辅助能够在纤维树脂层内产生冲击波,使树脂高速喷向附着面,从而增强层间的界面结合效果,减少纤维层内孔隙等缺陷,增强层间界面结合效果。
30.最后,本发明采用根据成形目标设计的实心橡胶软模作为下模,软模可以提供法向压应力,提高构件成形性,在解决层板复杂深腔构件变形时产生的塑性差、应变梯度大问题时起到明显作用。
31.实施本发明的电磁超声辅助纤维金属层板冲压变形方法,具有以下有益效果:
32.本发明综合利用力场、电场、磁场、热场多能场协同辅助纤维金属层板冲压变形,相比于传统纤维金属层板弯曲件成形工艺,采用预制料作为冲压对象,使得多层金属层能一次冲压,层间相对关系有保障,树脂分布及流动更均匀;冲压过程中对预制料同步施加电脉冲和磁脉冲,从而调控金属层的塑性及内部应力,大大降低金属层破裂、褶皱的发生,并较好的控制了回弹;对变形完成的预制料作用超声,能够在树脂纤维层内产生冲击波,使树脂高速喷向附着面,从而确保粘结界面紧密,减少纤维层内部的孔隙等缺陷,增强层间界面结合效果;保持凸模冲压停止位置并保温保压固化纤维金属层板,可以保障层板的成形效果。本发明显著提升了生产效率,大幅降低了金属层板开裂率及界面脱层率,并较好地控制了回弹。
附图说明
33.下面将结合附图及实施例对本发明作进一步说明,附图中:
34.图1为凸模进给到目标位置后的纤维金属层板冲压示意简图;
35.1-纤维金属层板、2-凸模;3-压边、4-下模容框、5-下模、6-超声发生器、7-超声振动探头、8-脉冲电流发生器、9-励磁线圈、10-垫板、11-氮化硅陶瓷绝缘层、12-加热电阻。
具体实施方式
36.为了对本发明的技术特征、目的和效果有更加清楚的理解,现对照附图详细说明本发明的具体实施方式。
37.如图1所示,在本发明的电磁超声辅助纤维金属层板冲压变形方法所采用的设备包括纤维金属层板1、凸模2;压边3、下模容框4、下模5、超声发生器6、超声振动探头7、脉冲电流发生器8、励磁线圈9、垫板10、氮化硅陶瓷导热绝缘层11、加热电阻12。
38.本发明电磁超声辅助纤维金属层板冲压变形方法,包括以下步骤:
39.(1)将高强度金属薄板与纤维预浸料相互交替铺层,作为纤维金属层板预制料;
40.(2)将纤维金属层板预制料放置在下模上,精确定位后,上压边下压固定预制料;
41.(3)将纤维金属层板预制料两端通过夹具与脉冲电流发生器的正负两电极分别相连;
42.(4)凸模下行,同时,通过脉冲电流发生器给纤维金属层板预制料施加脉冲电流作用,并通过在励磁线圈中通入交变电流,形成脉冲磁场,作用于纤维金属层板预制料,进行电磁耦合辅助处理;
43.辅助电脉冲处理过程包括:常温下,对纤维金属层板预制料金属层施加电脉冲作
用,电脉冲有效电流密度为20~80a/mm2,单个电脉冲作用时间为10~100ms,每施加完一次电脉冲作用后间歇30~200ms;
44.辅助磁脉冲处理过程包括:在励磁线圈内通入电压为2~3kv的电流,单次通电时长为1~2ms,每次通电后间隔0.4~1s,通电次数为2~5次,从而实现磁脉冲处理;
45.(5)待凸模下行至目标成形位置时,停止凸模进给和电磁耦合处理,凸模保持停留在目标位置;
46.(6)通过超声振动探头,对变形后的纤维金属层板预制料施加超声振动,保障金属层与纤维层间的结合效果;
47.(7)待所述步骤(6)中的超声振动施加完毕后,对纤维金属层板预制料进行加热固化处理;
48.(8)固化完成后,停止加热,退回凸模,取出成形纤维金属层板。
49.优选的,所述步骤(2)中,预制料固定后,连接预制料与脉冲电流发生器的线端夹具应该保证与预制料中的每层金属板均有良好接触。
50.优选的,所述在凸模、软模容框及压边中应在与预制料的接触面设置氮化硅陶瓷绝缘层。
51.优选的,设置氮化硅陶瓷绝缘层时,采用活性金属钎焊法,金属模及钎料采用ag-cu-ti+mo。
52.优选的,所述步骤(8)中采用在容框与凸模中放置加热电阻对其进行加热。
53.优选的,所述电磁超声辅助纤维金属层板冲压变形方法中下模采用橡胶软模,通过软模提供作用于预制料的法向压应力,提高构件成形性。
54.优选的,所述施加的超声振动能够减少纤维层内部的孔隙等缺陷,同时提升层间的界面结合效果。
55.优选的,所述施加的电脉冲,可以利用电致塑性效应,通过热效应和电子风力,使得金属层的抗形变应力的下降和塑性的提高,从而减少甚至避免破裂和褶皱的发生。
56.优选的,所述施加的电磁脉冲,可以使得弯角部位圆角在电磁力驱使下半径逐渐减小并贴膜,能有效控制回弹,同时利于材料的均匀流动,使得弯角部位的应变分布更均匀。
57.优选的,所述超声振动能够促进胶液在纤维与金属层之间的流动,使其分布均匀,从而提高界面结合质量,降低分层的可能。
58.按上述技术方案,步骤(4)中,所述电脉冲的波形设置为方波。
59.本发明首先应批量制备多层结构的纤维金属层板预制料,其中金属层层数优选为2~5层,进一步优选为2~4层;金属层厚度优选为0.1~1mm每层,进一步优选为0.1~0.5mm每层;纤维树脂层层数优选为1~4层,进一步优选为1~3层;纤维树脂层厚度优选为0.1~1mm每层,进一步优选为0.1~0.5mm每层。
60.在本发明中,金属层材料优选为不锈钢、铝合金或钛合金;
61.在本发明中,纤维层材料优选为玻璃纤维预浸布或碳纤维预浸布;预浸布中胶粘剂优选为环氧树脂类或聚酰亚胺类胶粘剂。
62.在本发明中,将层板放置在容框上时,在层板上表面中心做十字标记,凸模中心也相应进行十字标记,通过标记将纤维金属层板预制料定位准确,上下压边固定完毕后,将其
两端通过夹具与脉冲电流发生器的正负两电极分别相连,夹具连接应当保障与每层金属都有良好接触。
63.在本发明中,在凸模、软模框及压边与纤维金属层板预制料的接触面设置氮化硅陶瓷绝缘层,厚度优选为1~5mm,进一步优选为3~4mm。氮化硅陶瓷的硬度大,强度高,热膨胀系数小,摩擦系数小,导热率高。采用氮化硅陶瓷作为绝缘层,可在保证层板中脉冲电流作用良好的同时,保障下述步骤中的加热层板过程导热良好,且不因热膨胀过大而影响最终加工成形精度。
64.在本发明中,所述的下模具是根据成形目标设计的实心橡胶软模,软模可以提供法向压应力,提高构件成形性,在解决层板复杂深腔构件变形时产生的塑性差、应变梯度大问题时起到明显作用。
65.本发明优选在冲压过程中,层板塑性变形时,向其周围施加适当的超声振动,能够保障金属层与树脂间的结合效果,有效降低纤维树脂中的孔隙率,提升界面结合效果。同时,也可以促进金属层外层的表面成形质量和强度。
66.在本发明中,采用恒定速度冲压,冲压速度优选为5~30mm/s,进一步优选为5~20mm/s。
67.实施例1
68.本发明实施例1以玻璃纤维-不锈钢层板弯曲件的制造方法为例,提供一种电磁超声辅助纤维金属层板冲压变形方法,具体包括以下步骤:
69.s1、纤维金属层板预制料的准备:纤维层采用ewr600无碱玻纤预浸布,金属层采用0.4mm厚国标0cr13al牌号铁素体不锈钢板。首先采用磷酸阳极氧化法对不锈钢层进行表面处理,构造粗糙表面;按3层不锈钢层+2层玻璃纤维层的结构铺设纤维金属层板预制料,其中纤维层按0
°
/90
°
铺层进行正交铺设,预浸料中胶粘剂为成分为环氧树脂的j-272中温固化胶,铺设厚度为0.4mm;对预制料上表面进行十字标记,通过标记定位后压边固定妥当,将其两端通过夹具与脉冲电流发生器的正负两电极分别相连,夹具连接应当保障与每层金属都有良好接触;
70.s2、电磁耦合辅助冲压:冲压开始,冲压恒定速度为7mm/s,冲压持续时长为10s,同时,通过脉冲电流发生器向纤维金属层板预制料施加脉冲电流作用,电脉冲设置为有效电流密度为15.6a/mm2,单个电脉冲作用时间为100ms,每施加完一次电脉冲作用后间歇100ms;在冲压进行5s后,通过在励磁线圈中通入电压为3.2kv的电流,单次通电时长为2ms,每次通电后间隔1s,通电次数为5次,从而形成脉冲磁场,实现磁脉冲处理,作用于纤维金属层板预制料,进行电磁耦合辅助处理;
71.s3、超声振动界面结合强化:凸模下行至目标成形位置时,停止凸模进给和电磁耦合处理,由超声发生装置产生超声,通过超声振动探头由凸模向纤维金属层板预制料传导,超声波振动装置型号为me-1800,振动频率为10khz,振动压力为1.2mpa,振动幅值为60μm,超声作用持续时间为12s;
72.s4、加热固化成形:保持凸模位置不变,停止超声后,通过加热电阻对纤维金属层板预制料进行加热及保温;整个加热固化成形过程分四个温度阶段进行。第一阶段为预热阶段,将预制料温度升至70℃,持续保温15min;第二阶段为中温固化阶段,将预制料温度继续升至125℃,持续保温50min;第三阶段为高温固化阶段,升温至180℃,持续保温180min;
第四阶段为冷却阶段,固化结束后,停止加热,仍保持凸模位置不变,使层板自然冷却到室温,随后退出凸模,取出纤维金属层板弯曲件。
73.对按本实施例1方法和传统成形制造方法各获得的20件纤维金属层板弯曲件的成形效率和平均缺陷情况进行比较,具体对比结果如表1所示:
74.表1
[0075][0076][0077]
由表1可见:相比于传统纤维金属层板弯曲件成形制造工艺,本实施例1的技术方法明显缩短了玻璃纤维-不锈钢层板弯曲件单件成形时间,从而证明了本发明方法能有效提升生产效率,并且破裂率、成形缺陷数、回弹角度均显著下降,证实了本发明方法能显著提高成形质量。
[0078]
实施例2
[0079]
本发明实施例2以玻璃纤维-铝合金层板弯曲件的制造方法为例,提供一种电磁超声辅助纤维金属层板冲压变形方法,具体包括以下步骤:
[0080]
s1、纤维金属层板预制料的准备:其中金属层选用0.3mm厚5052-o铝合金板材,铺设前预先采用磷酸阳极氧化法进行表面处理,构造粗糙表面,增大其比表面积;纤维层选用ewr400e无碱玻璃纤维预浸方格布按0
°
/90
°
正交铺设0.4mm;层板结构为3层铝合金层+2层玻璃纤维层,铺设纤维金属层板预制料;其中,预浸料中胶粘剂为成分为环氧树脂的j-272中温固化胶;对预制料上表面进行十字标记,通过标记定位后压边固定妥当,将其两端通过夹具与脉冲电流发生器的正负两电极分别相连,夹具连接应当保障与每层金属都有良好接触;
[0081]
s2、电磁耦合辅助冲压:冲压开始,冲压恒定速度为12mm/s,冲压持续时长为5s,同时,通过脉冲电流发生器给纤维金属层板预制料施加脉冲电流作用,电脉冲设置为有效电流密度为16.8a/mm2,单个电脉冲作用时间为100ms,每施加完一次电脉冲作用后间歇100ms;并通过在励磁线圈中通入电压为2.5kv的电流,单次通电时长为2ms,每次通电后间隔1s,通电次数为4次,从而实现磁脉冲处理,形成脉冲磁场,作用于纤维金属层板预制料,进行电磁耦合辅助处理;
[0082]
s3、超声振动界面结合强化:凸模下行至目标成形位置时,停止凸模进给和电磁耦合处理,由超声发生装置产生超声,通过超声振动探头由凸模向纤维金属层板预制料传导,超声波振动装置型号为台湾明和me-1800,振动频率为10khz,振动压力为0.8mpa,振动幅值为52μm,超声作用持续时间为15s;
[0083]
s4、加热固化成形:保持凸模位置不变,停止超声后,通过加热电阻对纤维金属层板预制料进行加热及保温;整个加热固化成形过程分四个温度阶段进行。第一阶段为预热阶段,将预制料温度升至70℃,持续保温20min;第二阶段为中温固化阶段,将预制料温度继续升至125℃,持续保温60min;第三阶段为高温固化阶段,升温至180℃,持续保温210min;第四阶段为冷却阶段,固化结束后,停止加热,仍保持凸模位置不变,使层板自然冷却到室
温,随后退出凸模,取出纤维金属层板弯曲件。
[0084]
对按本实施例2方法和传统成形制造方法各获得的20件玻璃纤维-铝合金层板弯曲件的成形效率和缺陷情况进行比较,具体对比结果如表2所示:
[0085]
表2
[0086][0087]
从表2可以看出:相比于传统纤维金属层板弯曲件成形制造工艺,本实施例2的技术方法明显缩短了玻璃纤维-铝合金层板弯曲件单件成形时间,从而证明了本发明方法能有效提升生产效率,并且破裂率、成形缺陷数、回弹角度均显著下降,证实了本发明方法能显著提高成形质量。
[0088]
实施例3
[0089]
本发明实施例3以碳纤维-钛合金层板弯曲件的成形为例,提供一种电磁超声辅助纤维金属层板冲压变形方法,具体包括以下步骤:
[0090]
s1、纤维金属层板预制料的准备:其中金属层选用0.4mm厚ta7钛合金板材,铺设前预先采用natesi阳极氧化法处理钛合金板材,获得高氧化膜孔洞密度的粗糙表面;纤维层选用日本三菱tr50s-12k碳纤维预浸布按0
°
/90
°
正交铺设0.4mm;层板结构为3层钛合金层+2层碳纤维层,铺设纤维金属层板预制料;其中,预浸料中胶粘剂为kh-308型pmr聚酰亚胺;十字标记预制料上表面,定位后将压边固定妥当,将预制料被压边固定的两端通过夹具与脉冲电流发生器的正负两电极分别相连,夹具连接应当保障与预制料间的良好接触;
[0091]
s2、电磁耦合辅助冲压:冲压开始,冲压恒定速度为5mm/s,冲压持续时长为12s,同时,通过脉冲电流发生器给纤维金属层板预制料施加脉冲电流作用,电脉冲设置为有效电流密度为25.6a/mm2,单个电脉冲作用时间为100ms,每施加完一次电脉冲作用后间歇150ms;冲压进行10s后,并通过在励磁线圈中通入电压为3kv的电流,单次通电时长为2ms,每次通电后间隔1s,通电次数为2次,从而实现磁脉冲处理,形成脉冲磁场,作用于纤维金属层板预制料,进行电磁耦合辅助处理;
[0092]
s3、超声振动界面结合强化:凸模下行至目标成形位置时,停止凸模进给和电磁耦合处理,由超声发生装置产生超声,通过超声振动探头由凸模向纤维金属层板预制料传导,超声波振动装置型号为me-1800,振动频率为15khz,振动压力为0.4mpa,振动幅值为56μm,超声作用持续时间为8s;
[0093]
s4、加热固化成形:保持凸模位置不变,停止超声后,通过加热电阻对纤维金属层板预制料进行加热及保温;整个加热固化成形过程分四个阶段进行。第一阶段为阶梯预热阶段,首先将预制料温度升温至80℃,持续保温60min,然后继续升温至120℃,持续保温60min,之后进一步升温至160℃,再持续保温60min,最后,将预制料升温至200℃,持续保温60min,阶梯预热结束;第二阶段为中温固化阶段,将预制料温度继续升至280℃,持续保温30min;第三阶段为高温固化阶段,将预制料最终升温至320℃,持续保温120min;第四阶段为冷却阶段,固化结束后,停止加热,仍保持凸模位置不变,使层板自然冷却到室温,随后退
出凸模,取出纤维金属层板弯曲件。
[0094]
对按本实施例3方法和传统成形制造方法各获得的20件碳纤维-钛合金层板弯曲件的成形效率和平均缺陷情况进行比较,具体对比结果如表3所示:
[0095]
表3
[0096][0097]
从表3可以看出:相比于传统纤维金属层板弯曲件成形制造工艺,本实施例3的技术方法明显缩短了碳纤维-钛合金层板弯曲件单件成形时间,从而证明了本发明方法能有效提升生产效率,并且破裂率、成形缺陷数、回弹角度均显著下降,证实了本发明方法能显著提高成形质量。
[0098]
上面结合附图对本发明的实施例进行了描述,但是本发明并不局限于上述的具体实施方式,上述的具体实施方式仅仅是示意性的,而不是限制性的,本领域的普通技术人员在本发明的启示下,在不脱离本发明宗旨和权利要求所保护的范围情况下,还可做出很多形式,这些均属于本发明的保护之内。