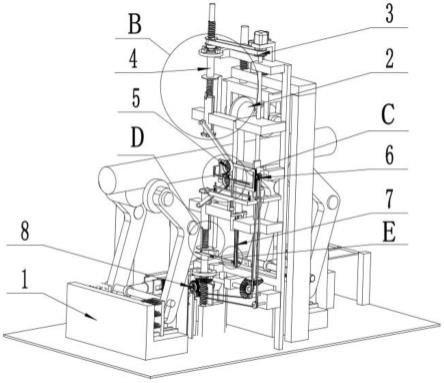
1.本发明涉及金属管材轧制设备技术领域,特别涉及一种用于中间耳轴液压缸的调整装置。
背景技术:2.目前,在无缝钢管轧制生产线中,轧机是无缝钢管的主要延伸变形设备。在连轧管机孔型构成中,轧辊为钢管的外变形孔型,芯棒在钢管内部形成内变形工具(孔型),内外孔型一起组成无缝钢管轧制孔型,从而可以轧制出壁厚尺寸一定的无缝钢管。为了轧制出壁厚均匀的无缝钢管,轧辊孔型中心和芯棒中心都要求和轧制中心线精确重合,上下左右控制在
±
2mm内,否则有可能导致芯棒插偏将毛管顶飞,造成较大设备事故,危及人身安全;另一方面芯棒中心偏移,插棒时会将芯棒表面石墨润滑剂擦掉,造成钢管内表面缺陷,保证芯棒在轧制中心线上的主要机构是由中间耳轴液压缸控制的芯棒升降托辊,由于升降托辊机构动作频繁,转动部件容易磨损,导致芯棒中心容易偏移,所以在工作中需要对芯棒轴心进行测量与调整。
3.现有技术中,公开号为cn203565472u的中国实用新型专利公开了一种用于管材轧制的芯棒支撑装置,包括芯棒支撑架壳体,所述芯棒支撑架壳体的底端设置与轧制中心线交错垂直的水平导向导轨;还包括与水平导向轨道滑动配合的固定导轨和倾斜固定设置的伸缩式压紧机构,所述伸缩式压紧机构在伸出状态下压紧在芯棒支撑架壳体的顶端侧部;在伸缩式压紧机构的倾斜压力作用下,所述水平导向导轨向下压靠在固定导轨上、并与固定导轨滑动配合。该现有技术用于管材轧制的芯棒支撑装置,由于芯棒支撑架壳体能从轧机牌坊的侧部进出,换辊操作更为方便;同时芯棒支撑架壳体在轧机牌坊中由伸缩式压紧机构实现自动压紧固定,自动化程度高。
4.但是现有技术仍存在液压缸耳座为不可调的技术问题,多个升降托辊机构在动作时因磨损不一致,导致升降托辊高低不一致,造成芯棒中心偏移,可调横梁不能完全弥补升降托辊高低差,同类机组普遍存在这一问题。也有的改进方式是:液压缸耳座两侧增加4个调节螺杆装置,并将液压缸耳座固定螺栓孔改为槽孔,便于耳座前后调节,虽然可以实现液压缸前后调节达到芯棒升降托辊支撑芯棒至中心线的目的,但存在以下缺陷:芯棒在前进或后退过程中会冲击升降托辊,传递至液压缸耳座,使调节螺杆受力大,多次冲击后容易脱焊与松动,稳定性差;调节螺杆只能安装于部件下方,受力面积小,受空间限制,调节时不方便,特别是靠支座端调节螺杆调整更困难,调节用时长,且紧固困难;耳座固定螺栓孔需要开槽孔,螺栓固定后易松动,导致升降托辊失稳,芯棒轧制中心线难以保证。所以急需一种用于中间耳轴液压缸的调整装置。
技术实现要素:5.针对上述技术问题,本发明采用的技术方案为:一种用于中间耳轴液压缸的调整装置,包括定位机构、位差机构,还包括支撑机构、补偿机构,所述支撑机构包括底板、升降
组件,底板上对称设置有两组液压缸,一组液压缸对应一组升降组件,液压缸的活动端转动安装在升降组件底部,芯棒放置在升降组件上;底板上设置有第四支架、第五支架,定位机构共有两组,两组定位机构对称安装在第四支架上,两组定位机构在第四支架上相向移动或相背运动,所述定位机构包括t型架、定位块,t型架上设置有横杆,横杆纵向滑动安装在底板的第五支架上,定位块纵向滑动安装在横杆上,定位块和t型架之间固定有定位弹簧;位差机构纵向滑动安装在第五支架上,所述位差机构包括位差框、两组叶轮,位差框纵向滑动安装第五支架上,位差框上横向滑动安装有位差杆,位差杆上对称设置有两组叶轮罩,叶轮转动安装在叶轮罩上,一组叶轮对应一组定位机构,第一组定位机构和位差框上设置有卡位机构,第一组定位弹簧压缩时,第二组定位机构驱动位差框向下滑动;第四支架上设置有传动机构,补偿机构设置在底板上的第七支架上,所述补偿机构包括补偿丝杆、补偿液压缸,补偿丝杆底部设置有活塞,补偿丝杆底部滑动安装在补偿液压缸内部,位差机构通过传动机构驱动补偿丝杆在补偿液压缸内部滑动,第六支架上设置有四组调节机构,两组调节机构对应一组液压缸,补偿机构通过调节机构驱动液压缸在第六支架上滑动。
6.进一步的,所述第四支架上设置有驱动机构,所述驱动机构包括空心带轮、空心蜗轮,第四支架上对称设置有两组圆盘架,空心蜗轮转动安装在第一组圆盘架上,空心带轮转动安装在第二组圆盘架上,空心蜗轮和空心带轮内部设置有螺纹,空心带轮与空心蜗轮之间设置有驱动组件。驱动组件驱动空心带轮和空心蜗轮同时转动。
7.进一步的,所述定位机构还包括定位丝杆、连杆,定位丝杆分别转动安装在圆盘架上,第一组定位丝杆转动安装在空心蜗轮内部,第二组定位丝杆转动安装在空心带轮内部,定位丝杆底部转动安装在t型架上,定位块上设置有定位销,连杆第一端转动安装在定位销上,连杆第二端转动安装在叶轮上。空心带轮和空心蜗轮转动时,带动两组定位丝杆同时转动,使两组定位丝杆相向移动或反向移动,定位丝杆带动t型架在第五支架上滑动,定位丝杆带动定位块移动,定位块驱动连杆摆动,连杆驱动叶轮转动,同时驱动位差杆在位差框上横向滑动,直至第一组定位块与芯棒接触时,第一组定位弹簧压缩,第一组横杆在第一组定位块和第五支架上滑动。
8.进一步的,所述卡位机构包括摆杆、弧槽杆,第一组定位块上固定安装有驱动杆,驱动杆滑动安装在第一组t型架上,驱动杆底部设置有斜面体,摆杆两端分别设置有楔体、凸柱,摆杆中部滑动安装有滑块,滑块转动安装在t型架的圆柱销上,滑块与摆杆之间设置有连接弹簧,弧槽杆滑动安装在位差框上,凸柱与弧槽杆上的凹槽咬合,弧槽杆上设置有弹簧杆,弹簧杆上设置有卡位组件,弹簧杆两端与第五支架之间设置有卡位弹簧。第一组定位块与芯棒接触时,第一组定位弹簧压缩,第一组定位块静止,第一组t型架继续向上滑动,第一组t型架带动摆杆向上移动,在斜面体与卡位组件的作用下,驱动杆推动摆杆在滑块上向弧槽杆滑动,连接弹簧伸长,直至卡位组件与弧槽杆上的凹槽咬合,t型架带动摆杆继续向上移动,摆杆推动弧槽杆向上移动,卡位弹簧拉伸。
9.进一步的,所述卡位组件包括压缩弹簧、卡位板,压缩弹簧第一端固定安装在弹簧杆上,压缩弹簧第二端固定安装有连接板,卡位板横向滑动安装在连接板上,卡位板纵向滑动安装在叶轮罩上,卡位板与叶轮上的凹槽咬合。弧槽杆带动卡位组件向上移动,直至弧槽杆固定机构与第二组叶轮上的凹槽咬合,第二组叶轮停止转动。
10.进一步的,所述传动机构包括传动齿轮、传动组件,传动齿轮转动安装在第八支架
上,传动组件包括传动轮、连接轮,传动轮共有三组,第一组传动轮和第二组传动轮转动安装在第四支架上,第三组传动轮与传动齿轮固定安装,连接轮转动安装在第四支架上,三组传动轮与连接轮上设置有传动带。第一组传动轮转动时,通过传动带带动连接轮和第三组传动轮转动,第三组传动轮转动时带动传动齿轮转动。
11.进一步的,所述补偿机构还包括补偿齿轮,补偿齿轮转动安装在第七支架上,传动齿轮与补偿齿轮啮合,补偿齿轮内部设置有凸起弧体,位差框上设置有齿条,第四支架上转动安装有位差齿轮,位差齿轮与齿条啮合,第一组传动轮与位差齿轮固定安装。第二组叶轮停止转动后,第二组定位块继续向下移动,带动第二组连杆向下移动,则第二组连杆通过第二组叶轮推动位差杆向下移动,同时第一组连杆通过第一组叶轮推动位差杆向齿条的方向移动,叶轮罩带动叶轮和卡位板同向移动,连接弹簧驱动机构在连接板上滑动,压缩弹簧压缩;位差杆带动位差框向下移动,齿条驱动位差齿轮转动,位差齿轮带动第一组传动轮转动,传动齿轮转动时带动补偿齿轮转动。
12.进一步的,所述补偿机构还包括补偿组件、圆筒,补偿组件共有三组,三组补偿组件均匀的滑动安装在圆筒上,圆筒转动安装在第七支架上,所述补偿组件包括螺纹块、凸杆,凸杆第一端滑动安装在凸起弧体上,螺纹块固定安装在凸杆第二端,圆筒与螺纹块之间设置有补偿弹簧,补偿弹簧第一端固定安装在圆筒上,补偿弹簧第二端固定安装在螺纹块上,补偿丝杆设置在三组螺纹块内部,螺纹块上的螺纹与补偿丝杆啮合。补偿齿轮转动时,凸杆在凸起弧体上滑动,通过凸起弧体驱动三组螺纹块向补偿丝杆滑动,补偿弹簧伸长,直至螺纹块上的螺纹与补偿丝杆啮合,圆筒继续转动,带动补偿组件转动,补偿组件带动圆筒转动,补偿组件驱动补偿丝杆向补偿液压缸内部移动。
13.进一步的,所述调节机构包括调节液压缸、液压缸架,调节液压缸固定安装在第六支架上,调节液压缸与补偿液压缸底部之间连接有液体管,液压缸架滑动安装在第六支架上,液压缸架固定安装在调节液压缸的活动端,液压缸固定安装在液压缸架上,液压缸架的弹簧架下方滑动安装有锯齿条,锯齿条与弹簧架之间设置有自锁弹簧,第六支架上固定安装有锯齿块,锯齿块与锯齿条上的齿咬合。补偿丝杆向补偿液压缸内部移动时,推动补偿液压缸内部的液体向调节液压缸流动,调节液压缸内部的液体增多,调节液压缸的活动端推动液压缸架向升降组件方向滑动,液压缸架带动液压缸单向移动,滑动过程中,锯齿条在弹簧架上滑动,自锁弹簧发生形变,防止锯齿条反向滑动,从而防止液压缸架带动液压缸反向滑动。
14.进一步的,所述升降组件包括升降杆、中间耳轴,升降杆有两组,升降杆中部转动安装在底板的第二支架上,两组升降杆第一端转动安装有托辊,中间耳轴滑动安装在两组升降杆第二端,中间耳轴转动安装在液压缸的输出端。液压缸架带动液压缸单向移动,升降杆绕第二支架转动,使升降杆带动托辊向上移动,从而使芯棒的中心线向上移动。
15.本发明与现有技术相比的有益效果是:(1)本发明设置的两组定位机构,可以对轧制中心向下偏移的距离进行测量;(2)本发明设置的卡位机构,卡位机构辅助定位机构将轧制中心向下偏移的距离反应在位差机构上;(3)本发明设置的位差机构和传动机构,位差机构通过传动机构将纵向的偏移距离转换成横向的偏移距离;(4)本发明设置的补偿机构,将偏移距离分别传递到两组调节机构上,分别对两组液压缸进行调节,补偿托辊磨损导致的轧制中心向下偏移;(5)本发明设置的调节机构,利用锯齿条和锯齿块的咬合,防止液压缸
反向滑动,保证轧制中心的稳定。
附图说明
16.图1为本发明整体结构的示意图。
17.图2为本发明第一视角的示意图。
18.图3为本发明第二视角的示意图。
19.图4为图3的a部分的局部放大图。
20.图5为图1的b部分的局部放大图。
21.图6为图1的c部分的局部放大图。
22.图7为图1的d部分的局部放大图。
23.图8为图1的e部分的局部放大图。
24.图9为图2的f部分的局部放大图。
25.图10图2的g部分的局部放大图。
26.图11为图2的h部分的局部放大图。
27.图12为图3的i部分的局部放大图。
28.图13为图3的j部分的局部放大图。
29.图14为图3的k部分的局部放大图。
30.图15为图2的l部分的局部放大图。
31.图16为图7的m部分的局部放大图。
32.图17为图6的n部分的局部放大图。
33.图18为本发明补偿机构的示意图。
34.附图标记:1-支撑机构;11-底板;12-稳定组件;13-升降组件;14-液压缸;111-第一支架;112-第二支架;113-第三支架;114-第四支架;115-第五支架;116-第六支架;117-第七支架;118-第八支架;121-稳定板;122-稳定弹簧;131-升降杆;132-托辊;133-中间耳轴;1141-圆盘架;1131-电机架;1132-齿轮架;2-固定机构;21-固定电机;22-固定齿轮;23-空心齿轮;24-固定丝杆;25-u型架;26-固定辊;3-驱动机构;31-驱动电机;32-驱动组件;33-空心带轮;34-空心蜗轮;321-带轮;322-皮带;323-主动锥齿轮;324-从动锥齿轮;325-蜗杆;4-定位机构;41-定位丝杆;42-t型架;43-定位弹簧;44-定位块;45-连杆;441-定位销;421-横杆;422-圆柱销;5-位差机构;51-位差框;52-位差杆;53-叶轮;54-齿条;55-位差齿轮;521-叶轮罩;6-传动机构;61-传动齿轮;62-传动组件;621-传动轮;622-连接轮;623-传动带;7-卡位机构;71-驱动杆;72-摆杆;73-连接弹簧;74-弧槽杆;75-卡位弹簧;76-滑块;77-卡位组件;711-斜面体;721-楔体;722-凸柱;741-弹簧杆;771-压缩弹簧;772-连接板;773-卡位板;8-补偿机构;81-补偿齿轮;82-补偿组件;83-补偿丝杆;84-圆筒;85-补偿液压缸;811-凸起弧体;821-螺纹块;822-补偿弹簧;823-凸杆;9-调节机构;91-调节液压缸;92-液压缸架;93-自锁弹簧;94-锯齿条;95-锯齿块;921-弹簧架;10-液体管。
具体实施方式
35.下面结合附图并通过具体实施方式来进一步说明本发明的技术方案。
36.其中,附图仅用于示例性说明,表示的仅是示意图,而非实物图,不能理解为对本
专利的限制;为了更好地说明本发明的实施例,附图某些部件会有省略、放大或缩小,并不代表实际产品的尺寸;对本领域技术人员来说,附图中某些公知结构及其说明可能省略是可以理解的。
37.实施例:如图1、图2、图3、图4、图5、图6、图7、图8、图9、图10、图11、图12、图13、图14、图15、图16、图17、图18所示的一种用于中间耳轴液压缸的调整装置,包括定位机构4、位差机构5,还包括支撑机构1、补偿机构8,所述支撑机构1包括底板11、升降组件13,底板11上对称设置有两组液压缸14,一组液压缸14对应一组升降组件13,液压缸14的活动端转动安装在升降组件13底部,芯棒放置在升降组件13上;底板11上设置有第四支架114、第五支架115,定位机构4共有两组,两组定位机构4对称安装在第四支架114上,两组定位机构4在第四支架114上相向移动或相背运动,所述定位机构4包括t型架42、定位块44,t型架42上设置有横杆421,横杆421纵向滑动安装在底板11的第五支架115上,定位块44纵向滑动安装在横杆421上,定位块44和t型架42之间固定有定位弹簧43;位差机构5纵向滑动安装在第五支架115上,所述位差机构5包括位差框51、两组叶轮53,位差框51纵向滑动安装第五支架115上,位差框51上横向滑动安装有位差杆52,位差杆52上对称设置有两组叶轮罩521,叶轮53转动安装在叶轮罩521上,一组叶轮53对应一组定位机构4,第一组定位机构4和位差框51上设置有卡位机构7,第一组定位弹簧43压缩时,第二组定位机构4驱动位差框51向下滑动;第四支架114上设置有传动机构6,补偿机构8设置在底板11上的第七支架117上,所述补偿机构8包括补偿丝杆83、补偿液压缸85,补偿丝杆83底部设置有活塞,补偿丝杆83底部滑动安装在补偿液压缸85内部,位差机构5通过传动机构6驱动补偿丝杆83在补偿液压缸85内部滑动,第六支架116上设置有四组调节机构9,两组调节机构9对应一组液压缸14,补偿机构8通过调节机构9驱动液压缸14在第六支架116上滑动。
38.如图2、图3、图9、图11、图13、图14所示,支撑机构1,底板11上设置有第一支架111、第二支架112、第三支架113、第四支架114、第五支架115、第六支架116、第七支架117、第八支架118,第一支架111共有两组,稳定组件12分别设置在第一支架111上,稳定组件12包括稳定板121、稳定弹簧122,稳定板121滑动安装在第一支架111上,稳定弹簧122设置在稳定板121和第一支架111侧面之间,稳定弹簧122第一端固定安装在第一支架111侧面,稳定弹簧122第二端固定安装在稳定板121上;液压缸14共有两组,两组液压缸14分别滑动安装在第六支架116上,液压缸14活动端的移动方向相同,升降组件13共有两组,一组升降组件13分别对应一组液压缸14和一组稳定组件12,升降组件13包括升降杆131、托辊132、中间耳轴133,每组升降组件13包括两组升降杆131,两组升降杆131中部对称转动安装在第二支架112上,托辊132转动安装在两组升降杆131第一端,中间耳轴133滑动安装在两组升降杆131第二端,中间耳轴133转动安装在液压缸14的输出端。液压缸14单向移动时,升降杆131绕第二支架112转动,使升降杆131带动托辊132向上移动,从而使芯棒的中心线向上移动,稳定组件12限制升降杆131的摆动,使131的摆动更加稳定。
39.如图2、图4所示,固定机构2,固定机构2设置在第三支架113上,第三支架113上设置有电机架1131、齿轮架1132,固定电机21固定安装在电机架1131上,固定齿轮22固定安装在固定电机21的输出轴上,固定电机21带动固定齿轮22转动,空心齿轮23共有两组,空心齿轮23对称设置在固定齿轮22两边,空心齿轮23转动安装在齿轮架1132上,空心齿轮23与固定齿轮22啮合,固定齿轮22转动时带动空心齿轮23转动,固定丝杆24共有两组,两组固定丝
杆24滑动安装在空心齿轮23内部,固定丝杆24转动安装在第三支架113上,第三支架113与固定丝杆24接触处设置有螺纹,空心齿轮23转动时带动固定丝杆24转动,固定丝杆24转动时在第三支架113上移动,固定丝杆24底部均转动安装在u型架25上,固定丝杆24在第三支架113上移动时,带动u型架25移动,固定辊26转动安装在u型架25底部,固定丝杆24带动u型架25向下移动时,固定辊26辅助固定芯棒。
40.如图1、图2、图10、图12、图15所示,驱动机构3设置在第四支架114上,第四支架114上对称设置有两组圆盘架1141,驱动电机31固定安装在第四支架114上,空心蜗轮34转动安装在第一组圆盘架1141上,空心带轮33转动安装在第二组圆盘架1141上,空心蜗轮34和空心带轮33内部设置有螺纹,驱动组件32设置在空心带轮33和空心蜗轮34之间,驱动组件32包括带轮321、皮带322、主动锥齿轮323、从动锥齿轮324、蜗杆325,带轮321转动安装在第四支架114上,带轮321固定安装在驱动电机31的输出轴上,驱动电机31带动带轮321转动,皮带322设置在空心带轮33和带轮321上,带轮321通过皮带322带动空心带轮33转动;主动锥齿轮323转动安装在第四支架114上,主动锥齿轮323与带轮321固定安装,带轮321转动时带动主动锥齿轮323转动,从动锥齿轮324转动安装在第四支架114下方,从动锥齿轮324与主动锥齿轮323啮合,主动锥齿轮323转动时带动从动锥齿轮324转动,蜗杆325转动安装在第四支架114下方,蜗杆325与从动锥齿轮324固定安装,从动锥齿轮324转动时带动蜗杆325转动,蜗杆325与空心蜗轮34啮合,蜗杆325转动时带动空心蜗轮34转动。
41.如图5、图6所示,定位机构4共有两组,两组定位机构4对称滑动安装在圆盘架1141上,两组定位丝杆41分别转动安装在圆盘架1141上,第一组定位丝杆41转动安装在空心蜗轮34内部,第二组定位丝杆41转动安装在空心带轮33内部,空心带轮33和空心蜗轮34转动时,带动两组定位丝杆41同时转动,使两组定位丝杆41相向移动或相背运动;定位丝杆41底部转动安装在t型架42上,两组t型架42对称安装,t型架42上设置有横杆421,横杆421纵向滑动安装在第五支架115上,定位丝杆41带动t型架42在第五支架115上滑动,定位块44纵向滑动安装在横杆421上,定位弹簧43设置在定位块44和t型架42之间,定位弹簧43第一端固定安装在t型架42上,定位弹簧43第二端固定安装在定位块44上,定位丝杆41通过定位弹簧43带动定位块44移动;定位块44上设置有定位销441,连杆45第一端转动安装在定位销441上,连杆45第二端转动安装在叶轮53上,定位块44驱动连杆45摆动。
42.如图6、图9、图12所示,位差机构5纵向滑动安装在第五支架115上,位差框51纵向滑动安装第五支架115上,位差杆52横向滑动安装在位差框51上,位差杆52上对称设置有两组叶轮罩521,叶轮53共有两组,位差机构5分别驱动机构3转动安装在叶轮罩521上,连杆45驱动叶轮53转动,同时驱动位差杆52在位差框51上横向滑动,一组叶轮53对应一组定位机构4,齿条54固定安装在位差框51上,位差齿轮55转动安装在第四支架114上,位差齿轮55与齿条54啮合,位差杆52带动位差框51向下移动,位差框51带动齿条54向下移动,驱动位差齿轮55转动,位差机构5通过传动机构6驱动补偿丝杆83在补偿液压缸85内部滑动。
43.如图2、图7、图6、图8、图9、图16所示,卡位机构7设置在第一组定位机构4和位差框51上,驱动杆71固定安装在第一组定位块44上,驱动杆71滑动安装在第一组t型架42上,驱动杆71底部设置有斜面体711,摆杆72两端分别设置有楔体721、凸柱722,滑块76滑动安装在摆杆72中部,滑块76转动安装在t型架42的圆柱销422上,第一组定位块44与芯棒接触时,第一组定位弹簧43压缩,第一组定位块44静止,第一组t型架42继续向上滑动,第一组t型架
42带动摆杆72向上移动,在斜面体711与楔体721的作用下,驱动杆71推动摆杆72在滑块76上向弧槽杆74滑动,连接弹簧73设置在滑块76与摆杆72之间,连接弹簧73第一端固定安装在摆杆72上,连接弹簧73第二端固定安装在滑块76上,摆杆72向弧槽杆74滑动,连接弹簧73伸长,弧槽杆74滑动安装在位差框51上,直至凸柱722与弧槽杆74上的凹槽咬合,t型架42带动摆杆72继续向上移动,摆杆72推动弧槽杆74向上移动;弧槽杆74上设置有弹簧杆741,卡位弹簧75共有两组,卡位弹簧75设置在弹簧杆741两端与第五支架115之间,卡位弹簧75第一端固定安装在第五支架115上,卡位弹簧75第二端固定安装在弹簧杆741上,弧槽杆74带动弹簧杆741和卡位组件77向上移动,卡位弹簧75拉伸。
44.如图6、图7、图17所示,卡位组件77设置在弹簧杆741上,卡位组件77包括压缩弹簧771、连接板772、卡位板773,压缩弹簧771第一端固定安装在弹簧杆741上,连接板772固定安装在压缩弹簧771第二端,卡位板773横向滑动安装在连接板772上,卡位板773纵向滑动安装在叶轮罩521上,弧槽杆74带动卡位组件77向上移动,直至卡位板773与叶轮53上的凹槽咬合,第二组叶轮53停止转动;第二组定位机构4继续向下移动,第二组定位块44继续向下移动,带动第二组连杆45向下移动,第二组连杆45通过第二组叶轮53推动位差杆52向下移动,位差杆52带动位差框51向下移动;同时第一组连杆45通过第一组叶轮53推动位差杆52向齿条54的方向移动,叶轮罩521带动叶轮53和卡位板773同向移动,连接弹簧73驱动机构3在连接板772上滑动,压缩弹簧771压缩;位差杆52带动位差框51向下移动,齿条驱动位差齿轮55转动。
45.如图9、图10、图11、所示,传动机构6设置在叶轮53与补偿齿轮81之间,传动机构6转动安装在第四支架114和第八支架118上,传动齿轮61转动安装在第八支架118上,传动组件62包括传动轮621、连接轮622、传动带623,传动轮621共有三组,第一组传动轮621和第二组传动轮621转动安装在第四支架114上,第一组传动轮621与位差齿轮55固定安装,位差齿轮55带动第一组传动轮621转动;第三组传动轮621与传动齿轮61固定安装,连接轮622转动安装在第四支架114上,传动带623设置在三组传动轮621与连接轮622上,第一组传动轮621转动时,通过传动带623带动连接轮622和第三组传动轮621转动,第三组传动轮621转动时带动传动齿轮61转动。
46.如图11、图12、图18所示,补偿机构8设置在第七支架117和第八支架118上,补偿齿轮81转动安装在第七支架117上,传动齿轮61与补偿齿轮81啮合,传动齿轮61转动时带动补偿齿轮81转动,补偿齿轮81内部设置有凸起弧体811,圆筒84转动安装在第七支架117上,补偿组件82共有三组,三组补偿组件82均匀的滑动安装在圆筒84上,补偿组件82包括螺纹块821、凸杆823,凸杆823第一端滑动安装在凸起弧体811上,螺纹块821固定安装在凸杆823第二端,补偿弹簧822设置在圆筒84与螺纹块821之间,补偿弹簧822第一端固定安装在圆筒84上,补偿弹簧822第二端固定安装在螺纹块821上,补偿齿轮81转动时,凸杆823在凸起弧体811上滑动,通过凸起弧体811驱动三组螺纹块821向补偿丝杆83滑动,补偿丝杆83设置在三组螺纹块821内部,螺纹块821上的螺纹与补偿丝杆83啮合,补偿弹簧822处于不受力状态时,螺纹块821上的螺纹与补偿丝杆83断开啮合;三组螺纹块821向补偿丝杆83滑动时,补偿弹簧822伸长,直至螺纹块821上的螺纹与补偿丝杆83啮合,圆筒84继续转动,带动补偿组件82转动,补偿组件82带动圆筒84转动,补偿丝杆83底部设置有活塞,补偿丝杆83底部滑动安装在补偿液压缸85内部,补偿组件82驱动补偿丝杆83向补偿液压缸85内部移动。
47.如图3、图12、图14所示,调节机构9共有四组,两组调节机构9对应一组液压缸14,调节机构9设置在第六支架116上,调节液压缸91固定安装在第六支架116上,液体管10连接调节液压缸91底部与补偿液压缸85底部,液压缸架92滑动安装在第六支架116上,液压缸架92固定安装在调节液压缸91的活动端,补偿丝杆83向补偿液压缸85内部移动时,推动补偿液压缸85内部的液体向调节液压缸91流动,调节液压缸91内部的液体增多,调节液压缸91的活动端推动液压缸架92向升降组件13方向滑动,液压缸14固定安装在液压缸架92上,液压缸架92带动液压缸14移动,液压缸架92的弹簧架921下方滑动安装有锯齿条94,锯齿条94与弹簧架921之间设置有自锁弹簧93,锯齿块95固定安装在第六支架116上,锯齿块95与锯齿条94上的齿咬合,滑动过程中,锯齿条94在弹簧架921上滑动,自锁弹簧93发生形变,防止锯齿条94反向滑动,从而使液压缸架92带动液压缸14单向滑动。
48.工作原理:升降组件13在使用过程中,托辊132有磨损,使导致托辊132上的芯棒中心容易向下偏移,则需要调整液压缸14的位置,使托辊132摆动,从而使托辊132向上移动,使芯棒中心尽可能与轧制中心线重合。
49.将需要轧制的芯棒放置在两个托辊132上,使用前,补偿弹簧822处于不受力状态,螺纹块821上的螺纹与补偿丝杆83断开啮合;启动驱动电机31,驱动电机31带动带轮321转动,带轮321通过皮带322带动空心带轮33转动,同时,带轮321带动主动锥齿轮323转动,主动锥齿轮323转动时带动从动锥齿轮324转动,从动锥齿轮324转动时带动蜗杆325转动,蜗杆325转动时带动空心蜗轮34转动;空心带轮33和空心蜗轮34同时转动,带动两组定位丝杆41同时转动,使两组定位丝杆41相向移动;定位丝杆41带动t型架42在第五支架115上滑动,定位丝杆41通过定位弹簧43带动定位块44移动,定位块44驱动连杆45摆动,一组叶轮53对应一组定位机构4,连杆45驱动叶轮53转动,同时驱动位差杆52在位差框51上横向滑动。
50.因为芯棒中心容易向下偏移,则下方的定位块44最先接触芯棒,即第一组定位块44与芯棒接触,此时第二组定位块44未与芯棒接触,空心带轮33和空心蜗轮34继续转动,带动第二组定位块44继续向下移动,芯棒限制第一组定位块44的移动,第一组定位块44静止,则第一组定位弹簧43压缩,第一组t型架42继续向上滑动,第一组t型架42带动摆杆72向上移动,在斜面体711与楔体721的作用下,驱动杆71推动摆杆72在滑块76上向弧槽杆74滑动,连接弹簧73伸长,直至凸柱722与弧槽杆74上的凹槽咬合,t型架42继续向上移动,t型架42带动摆杆72继续向上移动,摆杆72推动弧槽杆74向上移动;弧槽杆74带动弹簧杆741和弧槽杆74固定机构2向上移动,卡位弹簧75拉伸,直至弧槽杆74固定机构2与第二组叶轮53上的凹槽咬合,第二组叶轮53停止转动。
51.第二组叶轮53停止转动时,第二组定位机构4继续向下移动,第二组定位块44继续向下移动,带动第二组连杆45向下移动,则第二组连杆45通过第一组叶轮53推动位差杆52向下移动,位差杆52带动位差框51向下移动;同时第一组连杆45通过第一组叶轮53推动位差杆52向齿条54的方向移动,叶轮罩521带动叶轮53和卡位板773同向移动,连接弹簧73驱动机构3在连接板772上滑动,压缩弹簧771压缩;位差框51向下移动时,齿条54驱动位差齿轮55转动。
52.位差齿轮55带动第一组传动轮621转动,第一组传动轮621转动时,通过传动带623带动连接轮622和第三组传动轮621转动,第三组传动轮621转动时带动传动齿轮61转动,传动齿轮61转动时带动补偿齿轮81转动,补偿齿轮81转动时,凸杆823在凸起弧体811上滑动,
通过凸起弧体811驱动三组螺纹块821向补偿丝杆83滑动,三组螺纹块821向补偿丝杆83滑动时,补偿弹簧822伸长,直至螺纹块821上的螺纹与补偿丝杆83啮合,圆筒84继续转动,带动补偿组件82转动,补偿组件82带动圆筒84转动,补偿组件82驱动补偿丝杆83向补偿液压缸85内部移动。
53.补偿丝杆83向补偿液压缸85内部移动时,推动补偿液压缸85内部的液体通过液体管10向调节液压缸91流动,调节液压缸91内部的液体增多,调节液压缸91的活动端推动液压缸架92向升降组件13方向滑动,液压缸架92带动液压缸14移动,滑动过程中,液压缸14通过中间耳轴133推动升降杆131摆动,使托辊132升高,直至第二组定位块44与芯棒接触,此时芯棒中心与轧制中心线重合;使驱动电机31反向转动,使两组定位机构4恢复初始位置,在定位弹簧43、连接弹簧73、压缩弹簧771的辅助作用下,各个机构恢复初始位置,在凸起弧体811反向转动时,断开螺纹块821与补偿丝杆83的啮合,补偿丝杆83静止不动。
54.锯齿条94在弹簧架921上滑动,自锁弹簧93发生形变,防止锯齿条94反向滑动,从而使液压缸架92带动液压缸14单向滑动。液压缸14通过中间耳轴133推动升降杆131摆动过程中,稳定板121在第一支架111上滑动,稳定弹簧122压缩,使升降杆131的摆动更加稳定。
55.芯棒中心与轧制中心线重合后,启动固定电机21,固定电机21带动固定齿轮22转动,固定齿轮22转动时带动空心齿轮23转动,空心齿轮23转动时带动固定丝杆24转动,固定丝杆24在第三支架113上移动时,带动u型架25移动,固定丝杆24带动u型架25向下移动时,固定辊26辅助固定芯棒,对芯棒进行轧制。
56.当液压缸架92移动到极限时,则托辊132的磨损达到极限,需要对托辊132进行更换,工作人员将液压缸架92和液压缸14恢复到初始位置即可。
57.本发明不局限上述具体实施方式,所属技术领域的技术人员从上述构思出发,不经过创造性的劳动,做出的种种变换,均落在本发明的保护范围之内。