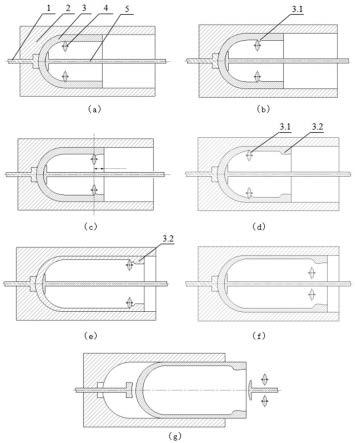
1.本发明属于旋压成形技术领域,具体涉及一种无缝金属气瓶内胆的成形工艺。
背景技术:2.金属气瓶内胆要求瓶体薄,从而减轻重量,而封头和瓶口处的壁厚要求较厚,这是因为在封头的弧形段处应力大,所以需要加厚,瓶口处为了强化螺纹的强度,故也需要加厚。传统的制作方式多是瓶体与瓶口、封头处焊接而成,焊接接头的性能不好保证,所以亟待寻求整体加工方式。
技术实现要素:3.为了克服现有技术的不足,解决焊接成形金属气瓶内胆性能不稳定的技术问题,本发明提供一种无缝金属气瓶内胆的成形工艺。
4.为实现上述目的,本发明是根据以下技术方案实现的:一种无缝金属气瓶内胆的成形工艺,包括以下步骤:s1、冲裁成形:根据无缝金属气瓶内胆的尺寸要求在板坯上冲裁成形,制得坯料;s2、冲压成形:根据无缝金属气瓶内胆的筒径及深度,将步骤s1制得的坯料在冲压模具中冲压成形,制得封底的筒形坯料;s3、内旋压成形:旋压成形模具包括:外推模:外推模包括外推杆和外推模压头,外推模压头与外推杆固定连接,外推模压头的工作面设置为内凹球面;外模:外模的心部沿长度方向设置成形腔体,成形腔体的底部设置为半球面,半球面的心部设置凹槽,凹槽的底部设置通孔;所述外推杆贯穿通孔,并且外推模压头的内凹球面与成形腔体的底部设的半球面共面;内推模:所述内推模包括内推杆和内推模压头,内推模压头与内推杆固定连接,内推模压头的工作面设置为外凸球面;s3-1、将外推模插入成形腔体底部的通孔中,将步骤s2制得的筒形坯料插入成形腔体中,使用内推模沿筒形坯料的轴线方向将筒形坯料推送至成形腔体的底部, 直至外推模压头完全回收至凹槽中,筒形坯料位置固定,此时外推模压头压紧筒形坯料的外壁,内推模压头压紧筒形坯料的内壁;s3-2、把内旋压压头由筒形坯料的瓶口伸入筒形坯料的底部,并调整至初始旋压位置;内旋压压头可为多个旋轮,其作为整体可绕筒形坯料的内壁转动、沿筒形坯料的轴线方向移动,亦可径向调节减薄量;s3-3、启动内旋压压头,内旋压压头绕自身轴线方向转动,与此同时内旋压压头沿筒形坯料的径向向外移动,内旋压压头压紧筒形坯料的内壁做三维螺旋运动;内旋压压头与筒形坯料内壁相互挤压,致使筒形坯料与内旋压压头接触部分产生塑性变形;
s3-4、由于旋压工艺的特点,会使筒形坯料的壁厚减薄且长度拉长,而且旋压工艺会使瓶体内壁的金属在内旋压压头进给方向上产生金属堆积区。在距离筒形坯料瓶口预定位置处停止旋压,将内旋压产生的金属堆积区保留在筒形坯料的瓶口位置处;s3-5、内旋压压头重复上述步骤s3-2至s3-4,每道次压下量为10~20%,总压下量为40~80%,对筒形坯料的内壁进行内旋压加工,直至筒形坯料的壁厚减薄到成品壁厚,成品壁厚为0.2~6mm;每道次产生的金属堆积区在筒形坯料瓶口位置处累积,形成金属堆积垛;s4、使内旋压压头沿筒形坯料的径向向内收拢,从筒形坯料体内抽出内旋压压头,外推模推动内旋压完成的筒形坯料与外模脱离,完成筒形坯料脱料;内旋压成形过程中,设计内旋压加工止于距离筒形坯料瓶口一定位置处和多道次旋压加工,达到减少筒形坯料壁厚的作用,从而减轻重量。而且由于瓶口有金属堆积垛的存在,渐进的增加了瓶口处的壁厚,和随后的外部收口旋压相配合,使弧形封头段和瓶口再次增厚,利于后续瓶口车削内螺纹的加工,增加了螺纹强度,且使筒形坯料内壁光滑、尺寸精度高;s5、外旋压收口:采用外旋压压头对步骤s4取出的筒形坯料进行无芯模的缩径旋压加工,制得无缝金属气瓶内胆毛坯;s6、车削螺纹:在无缝金属气瓶内胆毛坯的瓶口位置处车削内螺纹,制得无缝金属气瓶内胆。
5.进一步地,若干所述内旋压压头沿筒形坯料的内壁等角度布置。
6.进一步地,所述内旋压压头为旋轮或者滚珠。
7.与现有技术相比本发明的有益效果为:本发明提供的一种无缝金属气瓶内胆的成形工艺,实现了内胆瓶体薄、弧形封头和瓶口段的壁厚厚,得到了总体质量轻、封头弧形段的应力小、瓶口内螺纹强度高、一体成形的无缝金属气瓶内胆,且瓶体内部表面加工质量光滑、尺寸精度高,达到提高产品质量的目的。
附图说明
8.图1为本发明的冲裁成形工序流程图;图2为本发明的冲压成形工序流程图;图3为旋压成形模具主视剖视结构示意图;图4为内旋压工艺实施过程流程图;图5为外旋压封口工艺流程图;图6为采用本发明所述工艺制得的成品示意图。
9.图中,1为外推模,2为外模,3为筒形坯料,3.1为金属堆积区,3.2为金属堆积垛,4为内旋压压头,5为内推模,6为外旋压压头。
具体实施方式
10.以下实施例用于说明本发明,但不用来限制本发明的范围。若未特别指明,实施例均按照常规实验条件。另外,对于本领域技术人员而言,在不偏离本发明的实质和范围的前提下,对这些实施方案中的物料成分和用量进行的各种修改或改进,均属于本发明要求保
护的范围。
11.实施例1一种无缝金属气瓶内胆的成形工艺,包括以下步骤:s1、冲裁成形:根据无缝金属气瓶内胆的尺寸要求在板坯上冲裁成形,制得坯料;本实施例1中,板坯的材质为30crmoa,板坯厚度为10mm,冲裁成形后坯料为圆形,坯料的尺寸为φ278.5mm,如图1所示;s2、冲压成形:根据无缝金属气瓶内胆的筒径及深度,将步骤s1制得的坯料在冲压模具中冲压成形,制得封底的筒形坯料;本实施例1中冲压成形工艺参数为:压下速度2mm/s;冲压外模具内径50mm;冲压内模具外径30mm,冲压成形后制成的筒形坯料的直径为50mm,深度为100mm,如图2所示;s3、内旋压成形:旋压成形模具包括:外推模1:外推模1包括外推杆和外推模压头,外推模压头与外推杆固定连接,外推模压头的工作面设置为内凹球面;外模2:外模2的心部沿长度方向设置成形腔体,成形腔体的底部设置为半球面,半球面的心部设置凹槽,凹槽的底部设置通孔;所述外推杆贯穿通孔,并且外推模压头的内凹球面与成形腔体的底部设的半球面共面;内推模5:所述内推模5包括内推杆和内推模压头,内推模压头与内推杆固定连接,内推模压头的工作面设置为外凸球面;s3-1、将外推模1插入成形腔体底部的通孔中,将步骤s2制得的筒形坯料插入成形腔体中,使用内推模5沿筒形坯料3的轴线方向将筒形坯料3推送至成形腔体的底部, 直至外推模压头完全回收至凹槽中,筒形坯料3位置固定,此时外推模压头压紧筒形坯料3的外壁,内推模压头压紧筒形坯料3的内壁;s3-2、把内旋压压头4由筒形坯料3的瓶口伸入筒形坯料3的底部,并调整至初始旋压位置,内旋压压头4沿筒形坯料3的内壁等角度布置三个,内旋压压头4为旋轮;s3-3、启动内旋压压头4,内旋压压头4绕自身轴线方向转动,与此同时内旋压压头4沿筒形坯料3的径向向外移动,内旋压压头4压紧筒形坯料3的内壁做三维螺旋运动,如图4(a)~ (b)所示;s3-4、在距离筒形坯料3瓶口预定位置处停止旋压,将内旋压产生的金属堆积区3.1保留在筒形坯料3的瓶口位置处,如图4(c)所示;s3-5、内旋压压头4重复上述步骤s3-2至s3-4,每道次压下量为10%,总压下量为40%,对筒形坯料3的内壁进行内旋压加工,直至筒形坯料3的壁厚减薄到成品壁厚,成品壁厚为6mm;每道次产生的金属堆积区3.1在筒形坯料3瓶口位置处累积,形成金属堆积垛3.2,如图4(d)~ (e)所示;s4、使内旋压压头4沿筒形坯料3的径向向内收拢,从筒形坯料3体内抽出内旋压压头4,外推模1推动内旋压完成的筒形坯料3与外模2脱离,完成筒形坯料3脱料,如图4(f)~ (g)所示;s5、外旋压收口:采用外旋压压头6对步骤s4取出的筒形坯料3进行无芯模的缩径旋压加工,制得无缝金属气瓶内胆毛坯;在本实施例1中,无缝金属气瓶内胆毛坯底面的壁
厚为10mm,侧壁壁厚为6mm,瓶口位置处金属堆积垛3.2的厚度为12mm,金属堆积垛3.2内侧边缘与瓶口端面的距离为23mm;s6、车削螺纹:在无缝金属气瓶内胆毛坯的瓶口位置处车削内螺纹,制得无缝金属气瓶内胆。
12.实施例2一种无缝金属气瓶内胆的成形工艺,包括以下步骤:s1、冲裁成形:根据无缝金属气瓶内胆的尺寸要求在板坯上冲裁成形,制得坯料;本实施例2中,板坯的材质为34crmo4m1,板坯厚度为12mm,冲裁成形后坯料为圆形,坯料的尺寸为φ285mm;s2、冲压成形:根据无缝金属气瓶内胆的筒径及深度,将步骤s1制得的坯料在冲压模具中冲压成形,制得封底的筒形坯料;本实施例2中冲压成形工艺参数为:压下速度2mm/s;冲压外模具内径54mm;冲压内模具外径30mm,冲压成形后制成的筒形坯料的直径为54mm,深度为100mm;s3、内旋压(旋压成形模具与实施例1相同):s3-1、将外推模1插入成形腔体底部的通孔中,将步骤s2制得的筒形坯料插入成形腔体中,使用内推模5沿筒形坯料3的轴线方向将筒形坯料3推送至成形腔体的底部, 直至外推模压头完全回收至凹槽中,筒形坯料3位置固定,此时外推模压头压紧筒形坯料3的外壁,内推模压头压紧筒形坯料3的内壁;s3-2、把内旋压压头4由筒形坯料3的瓶口伸入筒形坯料3的底部,并调整至初始旋压位置,内旋压压头4沿筒形坯料3的内壁等角度布置三个,内旋压压头4为旋轮;s3-3、启动内旋压压头4,内旋压压头4绕自身轴线方向转动,与此同时内旋压压头4沿筒形坯料3的径向向外移动,内旋压压头4压紧筒形坯料3的内壁做三维螺旋运动;s3-4、在距离筒形坯料3瓶口预定位置处停止旋压,将内旋压产生的金属堆积区3.1保留在筒形坯料3的瓶口位置处;s3-5、内旋压压头4重复上述步骤s3-2至s3-4,每道次压下量为10%,总压下量为50%,对筒形坯料3的内壁进行内旋压加工,直至筒形坯料3的壁厚减薄到成品壁厚,成品壁厚为6mm;每道次产生的金属堆积区3.1在筒形坯料3瓶口位置处累积,形成金属堆积垛3.2;s4、使内旋压压头4沿筒形坯料3的径向向内收拢,从筒形坯料3体内抽出内旋压压头4,外推模1推动内旋压完成的筒形坯料3与外模2脱离,完成筒形坯料3脱料;s5、外旋压收口:采用外旋压压头6对步骤s4取出的筒形坯料3进行无芯模的缩径旋压加工,制得无缝金属气瓶内胆毛坯;在本实施例中,无缝金属气瓶内胆毛坯底面的壁厚为12mm,侧壁壁厚为6mm,瓶口位置处金属堆积垛3.2的厚度为14mm,金属堆积垛3.2内侧边缘与瓶口端面的距离为23mm;s6、车削螺纹:在无缝金属气瓶内胆毛坯的瓶口位置处车削内螺纹,制得无缝金属气瓶内胆。
13.实施例3一种无缝金属气瓶内胆的成形工艺,包括以下步骤:s1、冲裁成形:根据无缝金属气瓶内胆的尺寸要求在板坯上冲裁成形,制得坯料;本实施例3中,板坯的材质为34crmo4m1,板坯厚度为20mm,冲裁成形后坯料为圆形,坯料的
尺寸为φ480mm;s2、冲压成形:根据无缝金属气瓶内胆的筒径及深度,将步骤s1制得的坯料在冲压模具中冲压成形,制得封底的筒形坯料;本实施例3中冲压成形工艺参数为:压下速度2mm/s;冲压外模具内径140mm;冲压内模具外径100mm,冲压成形后制成的筒形坯料的直径为140mm,深度为130mm;s3、内旋压(旋压成形模具与实施例1相同):s3-1、将外推模1插入成形腔体底部的通孔中,将步骤s2制得的筒形坯料插入成形腔体中,使用内推模5沿筒形坯料3的轴线方向将筒形坯料3推送至成形腔体的底部, 直至外推模压头完全回收至凹槽中,筒形坯料3位置固定,此时外推模压头压紧筒形坯料3的外壁,内推模压头压紧筒形坯料3的内壁;s3-2、把内旋压压头4由筒形坯料3的瓶口伸入筒形坯料3的底部,并调整至初始旋压位置,内旋压压头4沿筒形坯料3的内壁等角度布置三个,内旋压压头4为旋轮;s3-3、启动内旋压压头4,内旋压压头4绕自身轴线方向转动,与此同时内旋压压头4沿筒形坯料3的径向向外移动,内旋压压头4压紧筒形坯料3的内壁做三维螺旋运动;s3-4、在距离筒形坯料3瓶口预定位置处停止旋压,将内旋压产生的金属堆积区3.1保留在筒形坯料3的瓶口位置处;s3-5、内旋压压头4重复上述步骤s3-2至s3-4,每道次压下量为20%,总压下量为80%,对筒形坯料3的内壁进行内旋压加工,直至筒形坯料3的壁厚减薄到成品壁厚,成品壁厚为4mm;每道次产生的金属堆积区3.1在筒形坯料3瓶口位置处累积,形成金属堆积垛3.2;s4、使内旋压压头4沿筒形坯料3的径向向内收拢,从筒形坯料3体内抽出内旋压压头4,外推模1推动内旋压完成的筒形坯料3与外模2脱离,完成筒形坯料3脱料;s5、外旋压收口:采用外旋压压头6对步骤s4取出的筒形坯料3进行无芯模的缩径旋压加工,制得无缝金属气瓶内胆毛坯;在本实施例中,无缝金属气瓶内胆毛坯底面的壁厚为20mm,侧壁壁厚为4mm,瓶口位置处金属堆积垛3.2的厚度为24mm,金属堆积垛3.2内侧边缘与瓶口端面的距离为30mm;s6、车削螺纹:在无缝金属气瓶内胆毛坯的瓶口位置处车削内螺纹,制得无缝金属气瓶内胆。
14.以上所述,仅为本发明的具体实施方式,但本发明的保护范围并不局限于此,任何熟悉技术领域的技术人员在本发明揭露的技术范围内,可轻易想到的变化或替换,都应涵盖在本发明的保护范围之内。因此,本发明的保护范围应以所述权利要求的保护范围为准。