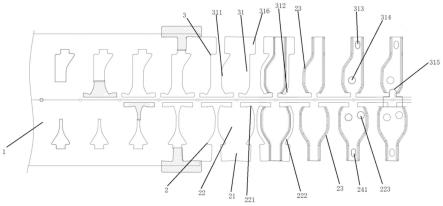
1.本发明涉及汽车扶手支架侧板加工领域。
背景技术:2.汽车扶手支架起到了有效的支撑作用,利用而汽车扶手支架在进行安装时,通常需要通过一些固定侧板来将扶手支架的支撑部分安装到汽车上,进而能进行方便的使用,而侧板上需要设置多个卡槽以及通孔来配合扶手支架进行安装,因此在侧板生产时,不仅需要快速的进行生产加工,而且还要保证生产的侧板具有准确的精度,进而保证能更好的将扶手支架安装到汽车上。
技术实现要素:3.发明目的:为了克服现有技术中存在的不足,本发明提供一种汽车扶手支架侧板及其加工工艺能有效的快速的加工出符合要求的扶手支架侧板结构。
4.技术方案:为实现上述目的,本发明的技术方案如下:
5.一种汽车扶手支架侧板,包括料板,在料板持续运动通过连续模具的过程中,连续模具通过设定的冲压工序依次对料板进行冲压剪裁加工,最终得到支架连接板和支架配合板;同时在整块的料板上部位置加工支架连接板以及在料板下部位置加工支架配合板;先是在相邻的待加工的支架连接板之间位置进行冲孔切边加工,同时在相邻的待加工的支架配合板之间位置进行冲孔切边加工,使相邻的支架连接板和支架配合板边缘断开各自成型;然后再进行翻边冲孔加工,最后在支架连接板和支架配合板之间连接的位置进行切断加工,形成独立开的成型的支架连接板和支架配合板。
6.进一步的,所述支架连接板包括矩型板和曲边板;所述曲边板两侧中部外凸设置;所述曲边板一端两侧边缘设置凸起;所述曲边板另一端边缘渐进变窄,为窄边端;所述窄边端固设矩型板,且所述矩型板长度大于窄边端宽度。
7.进一步的,通过连续模具对曲边板两侧进行翻边加工,形成内翻边。
8.进一步的,所述矩型板两端向内翻边方向翻折平行,形成卡槽;所述内翻边与卡槽侧边连贯设置;所述卡槽槽底中部贯穿开设有贯通孔;所述贯通孔呈椭圆形。
9.进一步的,所述曲边板底部贯穿开设有连通孔;若干所述连通孔横向错开设置。
10.进一步的,所述支架配合板包括直板;所述直板一侧边由中部向底部渐进增宽,为外凸边;所述直板底部及外凸边底部设置有缺口。
11.进一步的,所述直板两侧以及外凸边翻边加工,形成内翻边。
12.进一步的,所述直板顶部中部贯穿开设有椭圆孔;所述直板底部中部靠近外凸边位置贯穿开设有圆孔;所述直板底端中部开设有半圆槽;竖向上所述半圆槽间距于圆孔错开设置。
13.进一步的,所述直板顶部两侧平行对称固设有侧板,且所述侧板垂直于直板设置;对称的所述侧板之间形成卡槽。
14.进一步的,加工工艺方法为:第一工序:冲孔,通过连续模具在整块的料板两侧上进行冲孔加工,并且加工位置处于相邻的支架连接板之间以及相邻的支架配合板之间;
15.第二工序:切边,对料板中部靠近支架连接板冲孔位置进行切边;
16.第三工序,切边,对料板中部靠近支架配合板冲孔位置进行切边,并且料板中部连续设置;
17.第四工序:切边,对料板一侧支架连接板冲孔位置进行切边,促使相邻的支架连接板之间断开,初步形成支架连接板;
18.第五工序:切边,对料板另一侧支架配合板冲孔位置进行切边,促使相邻的支架配合板之间断开,初步形成支架配合板;
19.第六工序:空步,采用空步将上一工序与下一工序分隔开;
20.第七工序:翻边,通过连续模具对初步形成的支架连接板和支架配合板进行翻边加工,使之形成半壳体状;形成内翻边以及卡槽;
21.第八工序:空步,采用空步将翻边工序与下一工序分隔开;
22.第九工序:冲孔,对支架连接板和支架配合板相互靠近以及相互远离的位置进行冲孔;得到连通孔和贯通孔;
23.第十工序:切断,将支架连接板和支架配合板连接的位置切断开,从而形成独立的支架连接板和支架配合板。
24.有益效果:本发明能快速的加工出符合安装在扶手支架上的侧板,节省材料;包括但不限于以下有益效果:
25.1)通过在同一料板上同时加工出扶手支架两端的侧板,能同时进行多个步骤的加工,进而提高生产效率,并且在同一料板上冲裁加工,能减少废料的产生,起到节省材料的效果;
26.2)通过形成的内翻边半包围扶手支架设置,能增加侧板与扶手支架的连接面积,进而保证通常侧板安装后的扶手支架能更稳固,避免安装后容易发生晃动;同时能起到保护扶手之间的作用。
附图说明
27.附图1为支架连接板结构图;
28.附图2为之间配合板结构图;
29.附图3为加工工序流程图;
30.附图4为直板结构图;
31.附图5为曲边板结构图。
具体实施方式
32.下面结合附图对本发明作更进一步的说明。
33.如附图1-5:一种汽车扶手支架侧板,包括料板1,在料板1持续运动通过连续模具的过程中,连续模具通过设定的冲压工序依次对料板1进行冲压剪裁加工,最终得到支架连接板2和支架配合板3;同时在整块的料板1上部位置加工支架连接板2以及在料板1下部位置加工支架配合板3;先是在相邻的待加工的支架连接板2之间位置进行冲孔切边加工,同
时在相邻的待加工的支架配合板3之间位置进行冲孔切边加工,使相邻的支架连接板2和支架配合板3边缘断开各自成型;然后再进行翻边冲孔加工,最后在支架连接板2和支架配合板3之间连接的位置进行切断加工,形成独立开的成型的支架连接板2和支架配合板3。通过在同一料板上同时加工出扶手支架两端的侧板,能同时进行多个步骤的加工,进而提高生产效率,并且在同一料板上冲裁加工,能减少废料的产生,起到节省材料的效果。
34.所述支架连接板2包括矩型板21和曲边板22;所述曲边板22两侧中部外凸设置;所述曲边板22一端两侧边缘设置凸起221;所述曲边板22另一端边缘渐进变窄,为窄边端222;所述窄边端222固设矩型板21,且所述矩型板21长度大于窄边端222宽度。通过连续模具对曲边板22两侧进行翻边加工,形成内翻边23。通过形成的内翻边半包围扶手支架设置,能增加侧板与扶手支架的连接面积,进而保证通常侧板安装后的扶手支架能更稳固,避免安装后容易发生晃动;同时能起到保护扶手之间的作用。
35.所述矩型板21两端向内翻边23方向翻折平行,形成卡槽24;所述内翻边23与卡槽24侧边连贯设置;所述卡槽24槽底中部贯穿开设有贯通孔241;所述贯通孔241呈椭圆形。在扶手支架与侧板先进行安装时,卡槽能相应卡住扶手之间的两端,进而增加安装的稳固性;而贯穿贯通孔的杆件能将扶手支架固定稳固;保证安装后方便的使用。
36.所述曲边板22底部贯穿开设有连通孔223;若干所述连通孔223横向错开设置;便于通过连通孔与连接杆配合安装,保证安装后的稳固性,提高使用效果。
37.所述支架配合板3包括直板31;所述直板31一侧边由中部向底部渐进增宽,为外凸边311;所述直板31底部及外凸边311底部设置有缺口312;利于通过翻边加工在支板和外凸边位置加工出翻边,进而能更好的将扶手支架更稳固的安装到汽车上。
38.所述直板31两侧以及外凸边311翻边加工,形成内翻边23;便于对扶手支架进行卡紧,避免安装后扶手之间容易晃动。
39.所述直板31顶部中部贯穿开设有椭圆孔313;所述直板31底部中部靠近外凸边311位置贯穿开设有圆孔314;所述直板31底端中部开设有半圆槽315;竖向上所述半圆槽315间距于圆孔314错开设置。通过圆孔和半圆槽的设置,能便于连杆将侧板连接在一起,然后对扶手支架进行稳固,方便的安装到汽车上。
40.所述直板31顶部两侧平行对称固设有侧板316,且所述侧板316垂直于直板31设置;对称的所述侧板316之间形成卡槽24;同样通过卡槽对扶手支架进行卡紧,进而能保证扶手支架安装后具有较好的稳定性,进而能方便的进行使用。通过特定的加工工艺将整块的料板进行剪切以及冲压加工,形成所需的侧板结构,并且矩型板和曲边板同时加工,最后再将连接在一起的矩型板和曲边板切开,进而形成所需的矩型板和曲边板,通过这样同时异步加工的方式能同时进行多个工序的加工,进而快速的加工出所需的侧板,而多个不同的侧板同时加工完成,满足生产需求,并且减少了料板材料的浪费。
41.加工工艺方法为:第一工序:冲孔,通过连续模具在整块的料板1两侧上进行冲孔加工,并且加工位置处于相邻的支架连接板2之间以及相邻的支架配合板3之间;通过冲孔加工,能将加工位置多余的废料切除。
42.第二工序:切边,对料板1中部靠近支架连接板2冲孔位置进行切边;
43.第三工序,切边,对料板1中部靠近支架配合板3冲孔位置进行切边,并且料板1中部连续设置;
44.第四工序:切边,对料板1一侧支架连接板2冲孔位置进行切边,促使相邻的支架连接板2之间断开,初步形成支架连接板2;
45.第五工序:切边,对料板1另一侧支架配合板3冲孔位置进行切边,促使相邻的支架配合板3之间断开,初步形成支架配合板3;通过多工序的切边将加工件位置周边的废料切除,进而能加工出所需生产的侧板,同时避免材料浪费。
46.第六工序:空步,采用空步将上一工序与下一工序分隔开;避免相邻工序造成相互影响,容易产生误差。
47.第七工序:翻边,通过连续模具对初步形成的支架连接板2和支架配合板3进行翻边加工,使之形成半壳体状;形成内翻边23以及卡槽24;利于稳固扶手支架。
48.第八工序:空步,采用空步将翻边工序与下一工序分隔开;避免相邻工序造成相互影响,容易产生误差。
49.第九工序:冲孔,对支架连接板2和支架配合板3相互靠近以及相互远离的位置进行冲孔;得到连通孔223和贯通孔241;方便安装。
50.第十工序:切断,将支架连接板2和支架配合板3连接的位置切断开,从而形成独立的支架连接板2和支架配合板3;进而能快速的加工出符合要求的多规格的侧板,提高了生产效率,同时能节省材料,避免多余的浪费。
51.以上仅为本发明的优选的实施例,并不用以限制本发明,相对于本技术领域的普通技术人员来说,在不违背本发明上述原理和精神的情况下,还能对本发明做出若干改进和修改,这些改进和修改也同样视为本发明的保护范围。